Iron Clad:AMERICAN Cast Iron Pipe Company Grows by Doing Things ‘The Right Way’
January 21, 2014
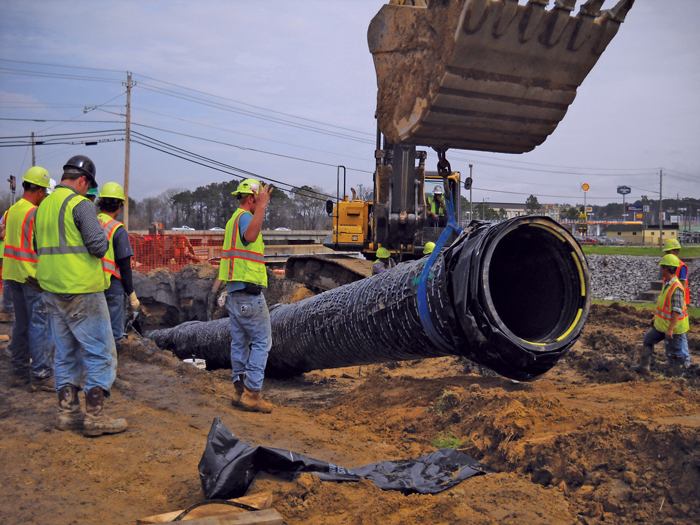
Based on the Golden Rule of treating others the way that you want to be treated, AMERICAN Cast Iron Pipe Company has grown into a company with annual sales of more than $1 billion.
Within that business are five sales divisions, three of which manufacture pipe that are used in trenchless applications from water and sewer systems to gas and oil pipelines. AMERICAN’s Ductile Iron Pipe, SpiralWeld Pipe and Steel Pipe divisions serve those needs.
Ductile Iron Pipe, the leading division in trenchless installations, traces its roots to the 1905 founding of AMERICAN in Birmingham, Ala., then a manufacturer of gray cast iron pipe.
John J. Eagan, the company’s first president, would go on to be its sole proprietor and help guide AMERICAN through an age where strife between management and labor was commonplace.
“Mr. Eagan believed a company run in accordance with the teachings of the Christian faith could prosper for the benefit of all — customers, employees and society,” Carpenter said.
Thus began the company’s Golden Rule philosophy that remains at the center of its corporate values and guides how it does business.
Rounding out the AMERICAN portfolio are AMERICAN Flow Control and ACIPCO International Sales divisions. From ductile iron pipe and spiral-welded steel pipe to hydrants and valves for the waterworks industry, to electric-resistance-welded (ERW) steel pipe for the oil and natural gas industries, AMERICAN products deliver water, transport wastewater to keep communities safe and sanitary, help fight fires, and transport the energy that heats homes and powers our mobile society.
Making all of this work are approximately 3,000 people, about 2,000 at its headquarters and plant facilities in Birmingham and about 1,000 at its subsidiary plants across the United States in Alabama, Oklahoma, South Carolina, Texas and Minnesota. In November, AMERICAN announced that it has plans to build a spiral-welded steel pipe plant in Flint, Mich., in the storied Buick City complex.
Following its ‘The Right Way’ motto and thanks to a diversified portfolio of products, AMERICAN was able to weather the economic downturn and a decrease in need for smaller diameter ductile pipe associated with the housing industry crash.
Getting into Trenchless
All of this success can be traced to its focus on the development of iron pipe — it is in the name after all — and AMERICAN’s history as a company runs parallel to the growth of the nation’s utility infrastructure.
Much of that is 100 years or older and is gray iron pipe. According to the Ductile Iron Pipe Research Association (DIPRA), there are 622 gas and water utilities in North America that are members of the Cast Iron Pipe Century Club and 23 in the Cast Iron Pipe Sesquicentury Club.
“The first documented use of iron pipe has been traced back to 1455. It, like many other products, has improved over the years as new technology has been introduced. These improvements include linings, joints, casting controls and metallurgy. Iron pipe is one of the few pressure pipes that has a service history exceeding 100 years. These critical lines have existed for that long with little or no investment in repairs, a testament to the product’s resilience,” said Carpenter, a ductile iron patriot working to increase the use of ductile iron and steel pipe in needed water infrastructure replacement and upgrades.
“AMERICAN was the first ductile iron pipe producer to see the potential in the trenchless market. For the longest time, we were on our own promoting trenchless applications within the industry,” Carpenter said.
“We are active in the North American Society of Trenchless Technology (NASTT) and other local chapters and support specification developments through ASCE and other associations,” Carpenter said. “In addition, we have submitted and presented numerous papers on HDD and trenchless technology. The primary reason we have a presence today is because of these efforts.”
AMERICAN, credited with co-development of ductile iron, began producing ductile iron pipe in the late 1940s and produced its last piece of gray iron pipe in 1978. It was not until the 1940s and early 1950s with the advent of asbestos cement and plastics that utilities started to turn to the less expensive alternatives to iron pipe.
“If people look at the long-term operation of a pipeline, iron is a very clear choice. But unfortunately, everyone doesn’t look at it that way; some only look at the initial cost,” Carpenter said. “While ductile iron pipe may initially cost more, cradle to grave costs — such as energy needed to operate the pipeline, operation and maintenance and the length of its service life — make it a much better value than other pipe materials.”
As an example, Carpenter said the larger internal diameter of ductile iron pipe helps save energy. Look at a cookie press, Carpenter explained, it is harder to get the dough through a 1.25 in. diameter press than one that is 2.25 in.
Moreover, when utility companies say that pumping costs make up anywhere from 50 to 80 percent of their operating costs then, “They can save money every day by having a pipe with a larger inside diameter that costs less to operate.”
Ductile iron remains strong over the course of its lifespan, as evidenced by the numbers cited by DIPRA, and it is environmentally friendly, made almost entirely from recycled metal.
“Water lines constructed in areas where soil contamination has occurred or in areas that might be subject to accidental spills should be made of only ductile iron or steel pipe. These two pipe materials have pipe walls that are 100 percent impermeable compared to pipes such as HDPE and PVC, which are permeable and susceptible to installation damage in trenchless installations,” Carpenter said. “Iowa State, under the direction of the American Water Works Association (AWWA) and its Water Research Foundation, released a report that raised the level of concern for system contamination in these environments.”
Carpenter admits that he is zealous about sharing this concern and offering ductile iron pipe and steel pipe as solutions.
Carpenter presently serves as ASCE Pipeline Division Advisory Committee chair and previously served as Executive Committee chair, as well as chair of the 2007 Pipelines Conference. He recently received the 2013 ASCE Pipelines Award of Excellence and serves on the Program Committee for the NASTT No-Dig Conference.
Other AMERICAN employees are active as committee chairs, directors and chairpersons for various professional organizations, and Carpenter says the company’s commitment to industry associations like ASCE, AWWA, NASTT and others is strong.
That drive to be involved extends to AMERICAN’s desire to be the leader in trenchless applications of its products. It also helped AMERICAN weather the tough economy and economic downturn.
Trenchless Growth
AMERICAN first used ductile iron in a trenchless setting in 1994. The company used a 10-in. MT push pipe (the MT stands for microtunneling) in a pipe bursting application to replace a sewer line at its Birmingham headquarters.
Subsequent to that and based on needs voiced by its customers, AMERICAN developed the GS (gravity service) push pipe. Both non-restrained pipes were used in trenchless applications using direct jacking.
Carpenter, who has been with AMERICAN since 1992, says that the company’s growth in the trenchless marketplace began after its Flex-Ring joint ductile iron pipe proved to be ideally suited for applications using pipe bursting and horizontal directional drilling. In a 1996 side-by-side test of the Flex-Ring and HPDE pipe in Grand Rapids, Mich., the ductile iron pipe was successfully pulled through, while the HPDE locked up well short of the target.
“We knew then that ductile iron pipe with our Flex-Ring joint would be an excellent pipe material for trenchless installations,” Carpenter said.
Developed in 1985, AMERICAN Flex-Ring pipe’s original purpose was to restrain the effects of thrust in open cut installations. Because of the Flex-Ring’s ability to deflect while remaining restrained, it is well suited for trenchless applications, as AMERICAN’s 1996 test confirmed.
As is the case with any business, customer demand steered AMERICAN into the trenchless marketplace. “We are seeing greater demand for trenchless installations, and advances in technology are allowing us to successfully complete longer pipe installations,” Carpenter said. “This is having a significant impact on the industry, providing customers with solutions for problematic installations using ductile iron pipe, a sustainable, strong and durable pipe material that is dependable and safe for the environment.
“We were the first to offer flexible restrained joint ductile iron pipe for use in horizontal directional drilling installations,” Carpenter said. “The trenchless applications allow us to offer our customers a complete ductile iron pipe system. Horizontal directional drilling as a portion of a major pipeline project is a fairly small component.” For instance, in 2012, AMERICAN supplied 34 miles of pipe for an installation in Meridian, Miss. The cooling water line pumped treated wastewater to a new industrial facility in Kemper County. Of that, 4,400 ft. of pipe made up the four HDD pulls.
That project, as well as another in Pasco County, Fla., rank as world-record pulls of 1,640 ft each of 36-in. ductile iron pipe. These projects also served as the basis of a case study performed by Carpenter and Brian Dorwart, who developed a formula bearing his name that estimates forces on pipe during pull back.
In the case study, each of the 36-in. pulls was monitored for pull or thrust loads after each pipe section was pulled into the bore path. Carpenter and Dorwart compared the data to the values predicted by the Dorwart formula.
“In the end, the analysis proved that the Dorwart method was very accurate in its predictions,” Carpenter said. “However, we still need more data to make sure this correlation remains accurate.”
The Florida project will once again make its way into the discussions at the No-Dig conference. Carpenter said Bruce Kennedy, professional engineer and assistant county utilities administrator for Pasco County, will present a paper at the 2014 event that discusses the use of HDD to install 36-in. ductile throughout the county.
Since the two record pulls, AMERICAN has seen inquiries from engineers and utility owners about the use of ductile iron pipe in trenchless applications.
“Currently, we can install 4- to 60-in. diameter ductile iron pipe using horizontal directional drilling,” Carpenter said. “Or, armor-coated Fastite pushbar pipe is available in 4- to 64-in. sizes for installations using microtunneling or direct jacking.”
World records make a great selling feature for AMERICAN ductile iron pipe but the pipe’s benefits do most of the talking.
“Our Flex-Ring pipe is ideally suited for trenchless installations because it’s the most smoothly contoured joint available in the industry. It’s also the easiest and quickest joint to assemble, and it’s very strong,” Carpenter said.
“The smooth contour allows it to be pulled through a pipe bursting installation, where the fragments of broken pipe move smoothly over the smooth contour of the bell. It allows it to be pulled through a horizontal directional drilling installation, where you have the bore path filled with slurry consisting of a relatively small volume of drilling fluid, with the balance of the slurry being native excavated material that can flow smoothly over the bell as there are no obtrusive glands or surfaces that would impact the pull back loads.”
Carpenter also notes that ductile iron is the only pressure pipe recognized as a SMaRT choice for infrastructure development. The designation came in the last 12 months.
“SMaRT certified products are rated on product sustainability by the Institute for Market Transformation to Sustainability,” Carpenter said. “Ductile iron pipe received the Sustainable Gold rating based on numerous criteria including public health and environmental safety, renewable energy and energy reduction, use of recycled materials, and innovation in manufacturing.”
As for the future, Carpenter sees it as bright for ductile iron pipe as the economy continues to recover, and municipalities and their leaders see the long-term value of investing in their infrastructure. “We have new and exciting innovations on the horizon — the first one to be introduced to the industry will be V-Bio, a new and improved polyethylene encasement that has proven to be extremely effective in soils that are aggressive or corrosive to ductile iron pipe and contain biological components to corrosion.”
Industry-wide, Carpenter says the biggest hurdle facing utilities is funding. “Water rates, in general, have not been appropriately increased to finance the replacement of pipes that have provided service well beyond their customary service life. In the ASCE’s 2013 Report Card for America’s Infrastructure that was released in April 2013, the grade given to our nation’s drinking water and wastewater infrastructure was a D, which indicates many parts of our systems are approaching the end of their service life. Our municipalities must find the resources needed to ensure the reliability of our water systems and the safety of our water.”
To stay at the top as a leader and innovator in the super competitive global marketplace, AMERICAN must continue to provide product innovation and quality as well as service to the industry and its customers.
AMERICAN will accomplish all of this by continuing to do things ‘The Right Way.’
“It’s who we are and how we do business. We believe in hiring the best people, producing the highest quality products and standing behind our products with the highest level know-how and customer service,” Carpenter said. “Known throughout the industry for our Golden Rule business philosophy, we believe in treating our customers, each other and our communities the way we want to be treated.”
Mike Kezdi is assistant editor for Trenchless Technology.