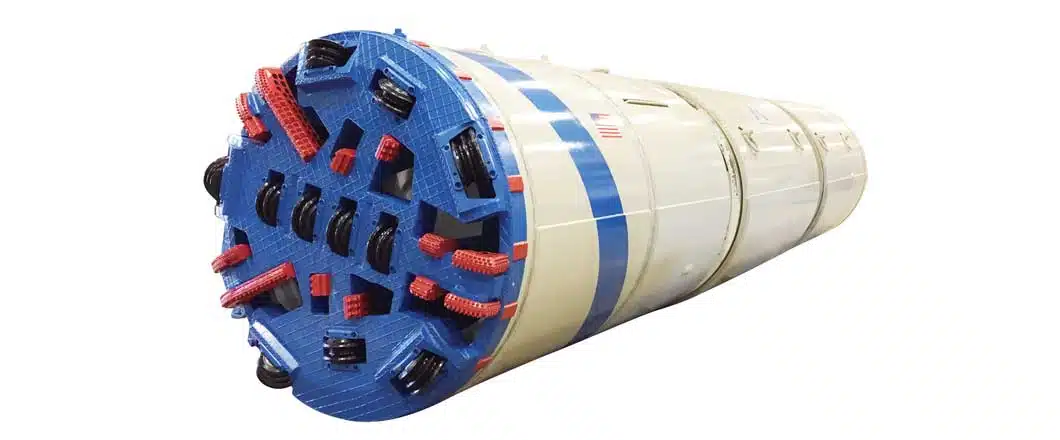
Tunnel Boring Machine Cutter Head Selection – A Manufacturer’s Perspective
A tunneling project consists of numerous intertwined puzzle pieces. Often, the cutter head on the tunnel boring machine is the most critical. It is the front line to progress. Without a properly designed cutter head, production can be slow or nonexistent.
The cutter head design and its tooling are dictated by the anticipated ground conditions on the project. The best results come from a cutter head design that is specific to the project’s ground conditions.
Deciding where the cutter head tooling should fall on that spectrum requires some considerations:
- How long is the drive?
- How hard is the ground?
- Is the ground abrasive?
- Will you be able to dig up the machine if you encounter an obstruction or need to replace tooling?
- What will it take to replace tooling underground?
- Is it possible to replace the tooling underground?
A good geotechnical report can answer many of these questions.
Tunneling Ground Conditions
Ground conditions can vary significantly from one project to the next and even every few feet along the same alignment. For now, let’s focus on some of the most common ground types experienced when tunneling – sand and gravels, clay, mixed ground and rock.
Each ground condition requires different cutter head tooling to be successful, and when appropriately selected, can significantly mitigate risk. Soft ground cutter head tooling typically includes cutter teeth, cutter bits, and scrapers. When hard ground or rock is expected, cutter discs are used. Mixed ground cutter heads blend the soft ground and hard ground tooling and are required when softer materials surround cobble or boulders.
The most reliable tooling usually costs the most, but there is peace of mind knowing that the cutter head will handle it if something unexpected is encountered while mining.
The manner of tooling installation should be considered – specifically whether the tooling will need to be serviced underground or not. Soft ground tooling is mounted on the cutter head in two manners, weld-on or bolt-on. Soft ground tooling comes in many different styles ranging from a simple mild steel plate to purpose-built bits with mounts and carbide tipped inserts. Discs cutters are installed from the front of the cutter head or the rear.
Some cutter heads are designed to maintain the tooling integrity throughout the entire drive length. In other instances, cutter heads will need to have the option to replace tooling underground. If the cutter head will need maintenance while underground, a machine with face access is required, allowing for cutter head access from inside the machine.
RELATED: Building Big with Microtunneling
Rear-loaded discs are replaced from behind the cutting face. Keep in mind, in some conditions, ground stabilization or hyperbaric pressurization may be required to perform underground maintenance of the cutter head.
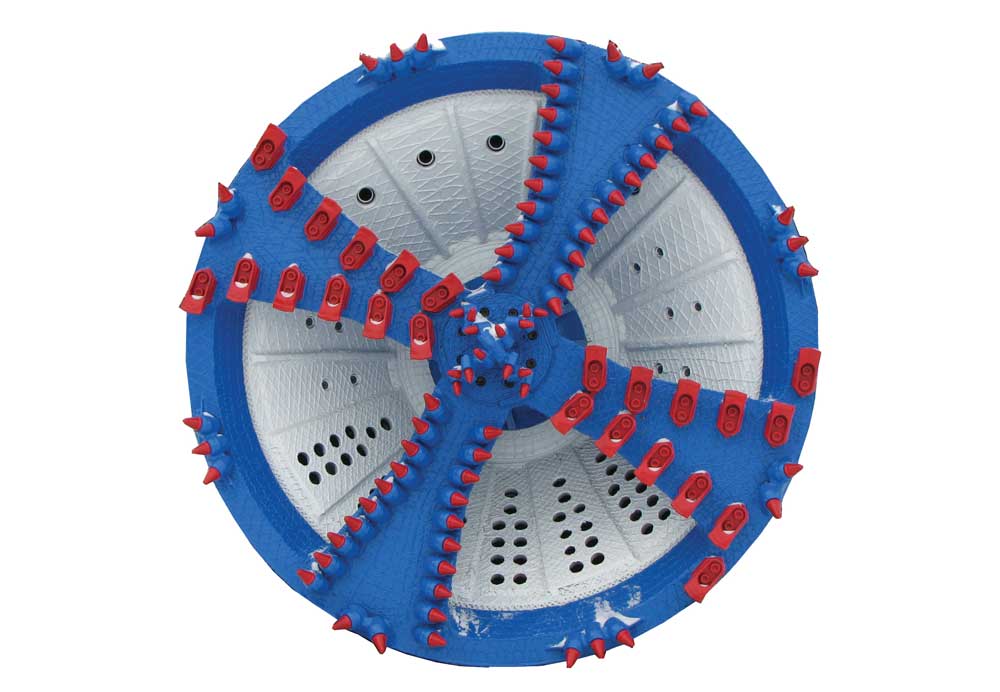
Soft ground cutter head tooling typically includes cutter teeth, cutter bits and scrapers. Soft ground cutter heads have the largest percentage of openings to allow for material consumption, typically between 40 to 60 percent.
When considering a rock cutter head, it is essential to understand the characteristics of the rock. How strong is the rock? How much rock is there? Is the rock fractured, stratified, or bedded? What is the orientation relative to the alignment? The answers to these questions will guide the design of the cutter head and should be discussed with your supplier. In general, closer disc spacing and higher thrust is required to process harder rock. The quantity and the size of the disc cutters increases the thrust capacity of the cutter head. Also, understanding of the thrust capacity of the cutter head is critical to disc cutter longevity and suitable production. Thrusting too hard will reduce the disc-bearing life. A damaged disc bearing will result in skidding and loss of production.
RELATED: The Benefits of Disc Cutters
Another important disc cutter head design feature allows the discs to process the material to the appropriate size in front of the faceplate before consuming the fractured rock. Some cutter head designs incorporate material grading screens to control the size of material allowed to pass through the cutter head openings; often these are called grizzly bars. Grizzly bars are added to the design to alter the openings in the faceplate. They are welded or bolted in place and screen the size of the material allowed through the faceplate. Bolt-on grizzly bars can also be used as access doors to the face and removed if tooling replacement must occur.

When tunneling in hard ground or rock is expected, the rock cutter head contains disc cutters discs to process the material to the appropriate size in front of the faceplate before consuming the fractured rock. Hard ground cutter heads openings are typically in the 10 to 20 percent range.
Cutter head faceplates have substantially different opening percentages based on the project’s anticipated ground conditions.
Soft ground tends to be easier to process; therefore, the design allows for fast advance rates. Soft ground cutter heads have the largest percentage of openings to allow for material consumption, typically between 40 to 60 percent.
Hard ground cutter heads experience the slowest production, and spoils created by a disc cutter head are small, fractured chips consumed by the spacing around a disc cutter. Hard ground cutter heads openings are typically in the 10 to 20 percent range.
Mixed-ground cutter heads fall somewhere between the two bounds set by the soft ground and hard ground heads. A 20 to 40 percent opening percentage allows hard material to become processed by the disc cutters while the soft and fractured hard material to be processed through a larger scoop opening.
The abrasiveness of the ground is another consideration for cutter head selection. Protection of the cutter head from abrasive material is just as important as selecting the correct tooling. Over time, abrasive material will erode the tooling and base structure of the cutter head, causing carbide inserts to fall out of the cutter bits rendering them useless for the remainder of the drive.
Abrasive material can also wear away at the disc cutters. If the material wears through the disc body, it could breach the bearing cavity causing the disc cutter to stop rotating. Some manufacturers add hard face weld or carbide impregnated wear plates to increase life and combat abrasive material wearing at the cutter head. By reducing the risk of failure, a cutter head can perform as intended for a long time.
Every tunnel will have its unique challenges regarding ground conditions, and no two tunnels will be alike. There can be a lot to consider when picking a cutter head but planning to minimize risk after the machine is launched will help streamline the path to success.
The best way to assess the risk is to get a hold of someone involved in cutter head design – they will be more than happy to help.
Cameron Landherr, P.E., is a design engineer at Akkerman Inc.