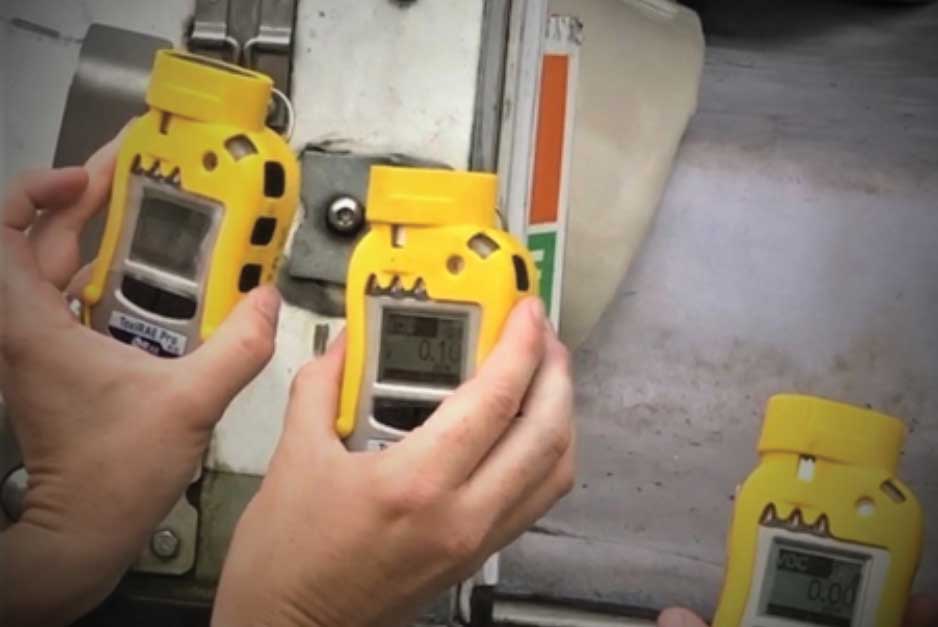
Styrene Barrier Products – A CIPP Solution to Address Styrene Emissions
Cured-in-place pipe (CIPP) products have grown in usage over the years as an increasingly popular solution for repairing pipes without requiring extensive excavation. Funding from the 2021 Bipartisan Infrastructure Law, which provides about $50 billion for water and sewer projects, has facilitated many municipalities planning CIPP projects to prioritize the upgrade and repair of existing infrastructure in a cost-effective and timely manner. However, the most common and inexpensive CIPP applications are made with liners that are infused with resins containing styrene.
The Need for Caution with Styrene
Styrene is a colorless liquid contained in resins, commonly used in the curing process for CIPP materials. Styrene is activated during the curing process to harden the liner and emits vapors as a byproduct. According to the Centers for Disease Control and Prevention (CDC), breathing high levels of styrene can cause a variety of negative health effects including changes in color vision, tiredness, feeling drunk, slowed reaction time, concentration problems, or balance problems.
These emissions become especially troublesome when working on pipe relining projects near occupied structures like residences, businesses and schools. The risk is heightened for projects near buildings with dry or damaged p-traps or older buildings without p-traps at all. Sewer projects near older buildings and neighborhoods are good opportunities for considering styrene barrier products because lateral pipes connecting homes to the broader sewer network can carry fugitive emissions from nearby sewer projects.
What CIPP Professionals Need to Know
Styrene barrier products are one innovative solution for minimizing exposure to styrene. As a director of business development for new markets at The Haartz Corp., I’ve worked alongside countless professionals to supply hundreds of thousands of feet of CIPP liner material nationwide. One aspect that stands out regarding styrene is that many professionals I’ve interacted with do not understand where emissions come from and how much a styrene barrier product reduces them.
Styrene fumes are not solely let off during the curing process. According to a study from the CDC’s National Institute for Occupational Safety & Health (NIOSH), styrene emissions also occur during the wet-out and storage stage – when a tube is saturated with the styrene-containing resin prior to installation in the host pipe. Fumes can also be released from the refrigeration truck transporting the products and the cutting points when the liner is connected back to lateral connections after curing is completed.
How It Works
Nearly all CIPP products consist of a nonwoven substrate with an extrusion coating laminated to the textile. As the coated fabric is shaped into a sock and then wet-out, standard CIPP coating allows styrene to permeate through the coating, causing fumes throughout the process and on the jobsite.
Styrene barrier products include a coating within the extrusion layer with properties that considerably reduces the amount of styrene monomer chemical compound from migrating through the coating. Sometimes a pre-liner is also incorporated to further control emissions.
The Haartz Corp. recently participated in an industry study measuring the efficiency of styrene barrier products. The tests compared styrene emission levels for standard products against those incorporating a barrier coating. Measurements were taken during the opening of the refrigerator truck – a point in the process with high styrene emission levels.
When opening a refrigerated truck containing liners impregnated with styrenic resin, values usually measure between 200 to 300 ppm. The test found that when utilizing a styrene barrier coating, styrene emission measurements fell to 0.27 ppm – more than 99.8 percent less than standard CIPP products.
Important Factors to Consider
Most styrene barrier products can be cured using steam, hot water or UV. A reliable barrier should have a strong bond to the nonwoven layer and excellent chemical resistance properties. These factors reduce the risk of delamination and guarantee that the barrier will withstand exposure to harsh chemicals and corrosive materials as part of the wet-out process before installation and high-pressure jetting/flushing as the pipe is cleaned during its service life. The time it takes to cure the material is also crucial to consider since a shorter curing time improves efficiency and reduces project turnaround time.
Regardless of the type of project, it’s important to consider whether the styrene barrier coated nonwoven will be flexible enough to dimple at a lateral connection point. A styrene barrier product that does will accelerate and simplify the lateral reinstatement process, reducing potential tears and damage to the newly in-place liner.
The Take-Away
As CIPP projects for pipe repair continue to gain popularity, it’s crucial that professionals explain the pros and cons of various CIPP solutions to their customers, including potential health risks associated with curing styrene resins. Styrene barrier products are one of the emerging solutions to address these concerns. When selecting a styrene barrier product, it’s important to understand its quality of performance in the field – they should have similar qualities throughout the process from wet-out to inversion and curing.
Having a trusted supplier with decades of experience and a strong track record for quality and performance is key. Suppliers who serve as partners won’t treat you like a transaction. They should take the time to understand your needs and even work with you to develop a custom solution to meet the unique challenges of your project.
Samit Sadavarte is the director of business development (new markets) at The Haartz Corp.