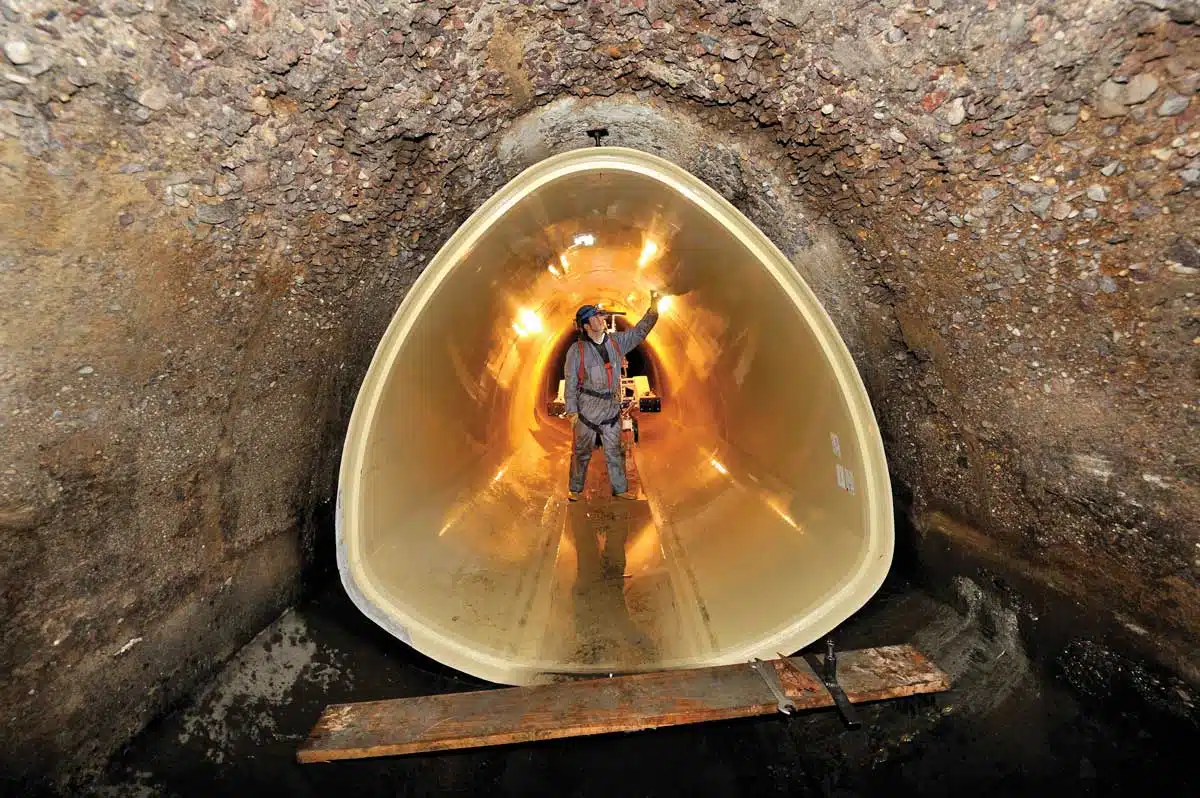
Sliplining Considerations – from Curves to Coefficients
Sliplining a new liner pipe into a deteriorated host pipe provides the lifespan and benefits of a brand-new pipe with minimal construction cost and social impact, offering public works departments a way to maximize the value of an existing resource in a way that is less invasive to the neighborhood.
In segmental sliplining, new factory-made pipe is pushed into place into existing deteriorated pipe, adding one segment at a time to the “train” to provide a new, corrosive-resistant, leak-free, long-term solution.
How do I decide if my existing deteriorated wastewater or sewer line is a good candidate for the sliplining rehabilitation method?
An accurate survey using a CCTV camera will show the extent of deterioration and other issues regarding the existing host pipe. The answers to these issues will determine the best method of rehabilitation:
- Shape of the host pipe: circular, non-circular
- Structural integrity of the existing line
- Condition, such as significant sagging, mineral deposits, cracks, etc.
- Foreign materials intruding into the host pipe, such as exposed rebar, hanging gaskets or roots
- Locations of extreme bends, curves, deflections, offset joints or undersized host pipes
- Distance that the liner pipe will have to be pushed
In addition to the survey, a hydraulic analysis will reveal flow characteristics in a gravity line or forced main, including the maximum flow and velocity during peak hours and in association with rain events. This additional information will help determine the optimal diameter of a liner or replacement pipe.
If the survey determines that segmental sliplining is a good option, what are my next considerations?
“The first consideration is what size liner pipe should be chosen. Liner size will affect not just constructability, but ultimately the sizing choice affects the capacity and hydraulics of the pipeline,” stated Kimberly Paggioli, P.E., vice president of engineering at Hobas Pipe USA Inc.
Calculate Diameter – What Pipe Will Fit?
“The general rule of thumb for relatively straight sections is that the liner pipe’s outside diameter (OD) should be 5 per cent smaller than the host pipe’s inside diameter (ID) with an absolute minimum of 1-in. difference on radius between the liner OD and host ID (or a 2-in. difference in diameter),” Paggioli explained.
For example, consider a 26-in.-diameter FRPM pipe with a 28-in. outside diameter that is being sliplined into a 30-in. host pipe. The difference between 28 and 30 in. is 7 percent.
The difference on radius should be at least 1 in. or 2 in. in diameter, easily meeting the 5 per cent rule.
Most sliplining projects range between 30 and 126 nominal in. OD. “We keep seeing the pipe diameters increase with recent projects: 120 in. Ø in Houston and 126 in. Ø in Los Angeles and Milwaukee,” says Paggioli.
One of the tightest fits Hobas Pipe USA ever recorded was in Los Angeles, where a 30-in. nominal pipe with 32-in. OD was inserted into a 33-in. clay sewer, allowing only a ½-in. radial clearance.
Consider Push Distance and the Number of Access Points
Standard practice utilizes existing manholes as sites for access pits. The host pipe will be sliplined alternately downstream and upstream. Very often it is possible, when the existing line is straight, to push through several manhole reaches and then come back with smaller shafts to set a new manhole or rehabilitate the existing manhole.
Access pit size is partially dependent on the longest length of pipe segments, but also must accommodate the contractor’s jacking frame, TBM and hydraulic pump.
Push distances of one mile have been accomplished successfully, but calculations are made considering pipe weight, pipe capacity and the estimated friction factor.
In addition to pipe weight, pipe capacity and the estimated friction factor, push distances are often determined by alignment changes, required manhole spacing and condition of the existing host pipe.
According to Mike Rocco, trenchless manager for AUI Inc., of Albuquerque, New Mexico, one of their longest pushes was sliplining 66-in. liner into a 72-in. host pipe for a distance of 1,200 ft in each direction from an pit located centrally between two manholes.
In Oakland, California, in 2019, Mladen Buntich Construction Co. performed a single push of 96-in. diameter Hobas liner 2,520 ft as part of a total 4,400-ft sliplining project, reported Cameron Landherr with Akkerman.
There are jacking systems capable of jacking smaller and larger pipe diameters. The limiting factors for larger pipe diameters are friction force, pipe weight, and project lengths, according to Landherr.
Solving Issues with Extreme Curves and Deflections
In many cases, the existing line is not straight. It could be a monolithically poured curve, have angularly deflected pipe segments, or even a series of mitered fittings. Elastomeric joints can negotiate modest curvatures of up to about two degrees, depending on the diameter of the pipe, according to Paggioli. In cases where the angular deflections exceed the joint limitations, mitered fittings can be made to meet the existing sewer alignment and inserted via a small point excavation. For a line in Los Angeles that included three curves each with a 45-degree radius, sections as short as 2.5 ft were pushed at the front of a 3,500-ft push to exactly match the existing alignment without the need for an intermediate excavation, reported Paggioli.
Calculate Length of Liner Segments
The joint lengths will depend not only on restriction due to the pit size, but also on the alignment of the sewer. When navigating the liner through the host, what will fit and what will seal (joint capability) are the two greatest concerns. Although longer 20-ft joint sections are the most economical, very often shorter sections are required to fit through certain sections of the line.
Considering Hydraulics
Capacity needs also affect the sizing. Hydraulic analyses of flow capacity before and after a sliplining project often document flow capacity increasing anywhere between 10 and 30 per cent due to the reduced friction of the smooth, clean interior of the new liner pipe.
When a 110-in. diameter segmental liner was installed into a 120-in. host pipe in Milwaukee in 2017, the flow capacity actually increased despite the reduction in diameter due to the decrease in roughness. Post project hydraulic testing showed that flow conveyance capacity increased from 575 million gallons per day (MGD) to 650 MGD.
In free flowing (flow by gravity) conditions, Manning’s Equation can be used to predict the roughness and resulting capacity of pipes. Manning’s Roughness Coefficient can be calculated by using meter data and the as-builts both before and after the lining to obtain a value that symbolizes whether the liner has a rougher or smoother surface than the host pipe, and thus a decreased or increased ability to convey flow. As “n” is in the denominator of the Manning’s Equation, a lower n-value correlates to a smoother pipe, and subsequently, the ability to convey more flow.
Each slipline project is unique and analysis of the existing line along with consideration of the future needs can guide designers to an optimal project outcome.
Liz Moucka is a construction industry reporter.