Reducing Construction Risk in HDD Projects:
July 1, 2008
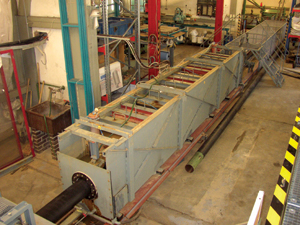
These described problems mostly can be traced to underestimated friction conditions. The R&D project, accomplished at the Department for Surface Mining and International Mining of the TU Clausthal, has taken up this procedural set of problems.
Based on a patent application, the objective target of the investigation was to reduce the tractive forces that are required for the pipe installation process by applying vibrations to the pipe. This article abstracts some selected essential results and findings of the recently finished research project.
Tasks & Objectives
The major task of the research work was to develop an approach in order to optimize the pipe-installing process by investigating several influencing parameters on the tractive forces. Primarily the effect of high-frequency vibrations was investigated within the frame of pull tests being performed in a pilot plant scale experimental setup. On one hand, the tractive forces that appear while the pipe is being pulled should be reduced, and on the other, the opportunity should be provided to release/break an already sticking pipe, thus reducing the initial breaking forces.
In the first project phase, the general applicability and feasibility of the vibration method was investigated by using a small scale pilot testing facility. The positive test results gave reason to continue the project in a continuative research phase, particularly aimed at the quantification of the tractive force’s influencing parameters. Based on these findings, statements for the process optimization, as well as for the large-scale insitu application have been derived. The practical investigations were supplemented by theoretical considerations and model calculations.
A testing facility was built to scale closer to reality. The test pipes were led through a steel box that was filled with soil. Through a circumferential cable, the pipe could be tracked by two different speed levels (1 m/min. and 0.5 m/min.); the tractive force was measured constantly with a dynamometer that was centrically installed at the top end of the pipe. For the tests, two different types of soil were chosen (sand and silt) that are typically traversed within HDD projects.
In order to simulate an insitu soil pressure or rather borehole stress conditions, a static load was induced to the soil material by using pneumatic pads. The main item of the testing facility was the vibration unit, which was installed inside the pipe, and whose rotational frequency could be varied infinitely. For the test series, mainly PE-covered steel pipes in dimensions of DN100, DN150 and DN200 were used, as well as one DN100 non-covered steel pipe in addition, in order to get information about the influence of the pipe shell conditions.
Results
The results of the several test series in general affirmed the theoretical approach that the initiation of high-frequency vibrations to the pipe lead to an effective reduction of the required tractive forces. This applies to both the initial breaking force, as well as the constant pulling force during the steady installing process. Within the frame of the lab-scale tests, the results show a considerable dependency between the tractive forces and the initiated vibration energy, which again depends on the frequency of the vibrating unit. Best results have been archived in the cohesive soil material (silt). Generally, the highest vibration frequencies that have been investigated, at most 200 Hz, result in the maximum reduction of the tractive forces. In some test series, the silt material maximum pulling force reductions of about 15 percent for the sliding force and approximately 20 percent of the breaking force have been attained. In sandy material, maximum tractive force differences of approximately 8 percent for the initial breaking force and approximately 11 percent for the sliding force have been achieved.
A reduction of the pulling velocity effects — according to practical experience — leads to an additional decrease of the pulling force. In the investigated sandy material, an average additional tractive force reduction of about 5.5 percent for all PE-covered pipes have been achieved; in the cohesive soil (silt) the sliding force difference was approximately 7.6 percent, influenced by the pulling velocity only.
Relating to the pipe mass that has to be activated by the vibrations, it is assumed that an appropriate higher application of vibratory energy is required corresponding to an increasing pipe dimension. Corresponding with an increase of the pipe’s cross-sectional geometry, accordingly a higher vibration energy is required, which can be recognized by the incremental shift of the point to the right side where the force curve starts to drop down, thus in the region of high frequencies.
An explanation for the tractive force reduction resulting from vibrations can be given on closer examination of the geo-mechanical procedures, which come along with the vibration impacts on the surrounding soil. The vibrations effect a partial fluidization of the soil material in a close circumferential area around the pipe’s surface, combined with an increase of the pore water pressure in the corresponding zone.
The impulses resulting from vibrations lead to a reduction of the adherence between the pipe’s surface and the surrounding soil or rather cutting loaded drilling mud, and thus benefiting the reduction of friction or rather the tractive force. Further, the vibrations ensure a more constant and smooth installing process, which means that no slip-stick effects occur while the pipe gets pulled, particularly not when using uncovered steel pipes in non-cohesive soils.
The application of vibrations within the frame of HDD projects is advisable to break an already sticking pipe or rather in case of a sudden disproportionately high increase of the tractive force, as well as for force reduction in fine-grained and cohesive subsoil conditions. The development of the partial fluidization zone resulting from vibrations requires a full contact between the soil and the pipe surface. The same applies for thixotropic and cutting loaded drilling muds. Particularly in this case, high-frequency vibrations may contribute to maintain the so-called sol-phase (fluid phase) of the mud. It can be considered that the use of drilling mud — which could not be realized within the frame of the lab tests — causes even more considerable effects due to the initiation of vibrations or rather the reduction of the tractive forces.
A calculational stress analysis of the pipe material by using Finite-Element-Method (FEM) yielded that the vibrations investigated within the project do not cause damage of the pipe material. The admissible values for the material strength will not be exceeded. With regard to an infield application, where appropriate more powerful vibration units must be used, this should be re-checked based on project-specific requirements. An analytical approach was developed, which can be used in order to conservatively evaluate the pipe material stress resulting from the vibrations.
According to experience, vibrations cause soil compaction within a certain effective range if the vibration frequency of the exciter cell is in the range of the resonance frequency of the subsoil. This is specifically and technically utilized for soil improvement/soil stabilization, but must be considered as counterproductive within the present application. Thus, it is required that the initiated vibrations are explicitly higher than the soil’s natural frequency in order to avoid soil compaction. In particular this must be considered for a large-scale application or rather the design of a practicable vibration unit.
Today, numerous technical solutions exist in order to generate directed vibrations with the required frequency and amplitude, and particularly avoid critical revolution speed ranges during the run-up and run-out of the vibrator that may cause negative impacts on the subsoil due to natural vibrations. For an infield application, it is recommended to design an in-pipe vibration unit that is mobile and that can be braced centrically within the pipe.
Conclusion
Due to the achieved research results it generally can be considered that the vibration method for HDD applications can be transferred to practical in-field conditions. Within the study, calculational approaches have been developed that can be used for estimating the required vibrations for a field application. All research results and findings are recorded in the final report of the research project.
All research results and findings are recorded in the final report of the research project. It should be pointed out that the exact and detailed reproduction of the real insitu situation, boundary conditions, as well as the respective interactions of the influencing factors in a lab-scale experimental setup can take place rudimentary and incompletely. Calculational approaches or rather modeling methods can only consider the complex relationships through approximations. On this account, finally only a field test under real conditions can provide further expertise, which would be desirable for a next research step.
Dipl.-Ing. Stefan Rossbach, Univ.-Prof. Dr.-Ing. Habi and. Hossein Tudeshki, Department for Surface Mining and International Mining, Institute of Mining, Clausthal University of Technology.