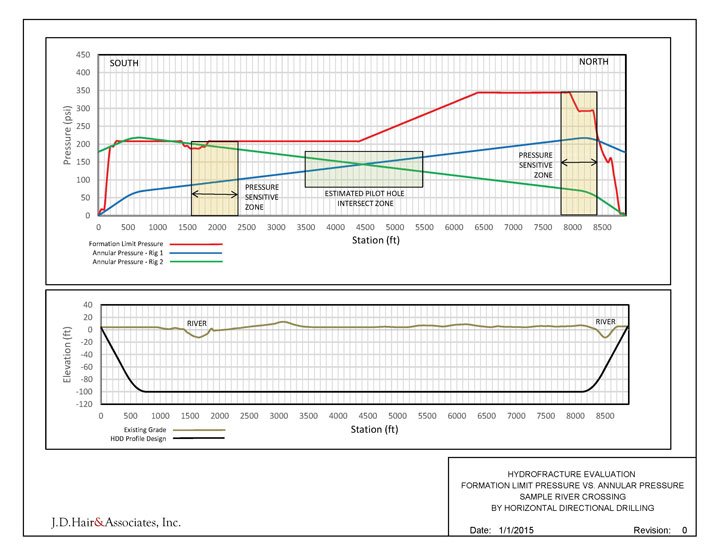
Proper HDD Design Is Key to Successful Completion
Photo above: Hydrofracture evaluation are typically summarized in graphical format. The graphs display the formation limit pressure along the HDD segment vs. the estimated annular pressure necessary for HDD operations. Since the crossing involved a pilot hole intersect, annular pressure curves in two directions are shown.
The risks for horizontal directional drilling, just like every construction project, increase, as the project’s size grows larger, highlight the fact that good designs are imperative to a project’s success.
As the acceptance of horizontal directional drilling (HDD) has grown — to the point where HDD is mandated on some pipeline crossings vs. open-cut methods — the companies that specialize in designing HDD projects have seen a shift in a client’s knowledge base. Where consultants once had to spend time explaining the very basic of the HDD construction process to a client, many now have been involved with numerous HDD projects throughout their career and have a general understanding of HDD. It is also more common to find an engineer who can design a crossing, but there are benefits to going with a specialist.
“An engineer who specializes in HDD will have a better understanding of what can and cannot be accomplished using HDD. He will have a better understanding of the limits of the technology and the capabilities of HDD contractors,” says Jeff Scholl, P.E. engineering manager for J.D. Hair & Associates Inc.
“With our firm, not only do we have extensive practical experience with typical engineering design tasks such as laying out HDD designs, evaluating pipe stress, etc., but we also bring extensive field experience to the table. The advantage of field experience is that you develop a greater understanding of the types of things that can occur, or go wrong, during HDD construction. This knowledge forms the backbone of the engineering judgement we use when designing a crossing.”
One of the areas that design engineers who specialize in HDD have focused more attention is in the area of hydraulic fractures and inadvertent drilling fluid returns. The goal of this increased focus is to identify areas where inadvertent returns are likely so that design modifications or other precautions can be taken to minimize the overall environmental impact.
According to Scholl, part of that increased focus is due in part to more rigid requirements and scrutiny from state and federal regulatory agencies. The agencies, Scholl says, like to see the design team taking a proactive approach in trying to minimize the environmental impact associated with HDD. A hydraulic fracture evaluation is one method that can be used to demonstrate due diligence on the part of the HDD designer. It shows that the project team is using all available tools from a design standpoint to minimize the risk of drilling fluid impact to the environment.
“Back in the day, frac-outs were seen as an acceptable, or at least tolerable, consequence of using the technology.” Scholl says. “If a frac-out occurred, you contained it, if possible, or in some cases, let it flow freely and continued drilling. Now, with increasing environmental sensitivity, greater efforts are taken both by engineers and contractors in an attempt to avoid their occurrence. “
One of the ways this is done is by going with deeper HDD designs. In the last 10 years, Scholl has watched as the industry slowly shift from a minimum design depth of 25 ft or less for a maxi-rig project to 40 ft or more. Adjusting the depth to soils with greater confining capacity is one of the benefits of drilling deeper.
“Another way in which we are attempting to reduce the risk of drilling fluid impact is by evaluating annular pressure and assessing the risk of hydraulic fracture of the subsurface. This allows us to identify areas along the drilled segment where there is an increased risk of drilling fluid impact,” Scholl says. “You can’t always prevent an inadvertent drilling fluid return. If there are naturally occurring fractures in the soil, the fluid will travel in the path of least resistance, so there is not always a way to prevent them. However, by looking at soil types and looking at the annular pressures, there are calculation methods that can be used to predict the risk of a frac-out.”
The “Delft Method” is the most commonly used technique to evaluate the allowable drilling fluid pressure. It was developed by Delft Geotechnics and presented in an Army Corps of Engineers publication, titled “Installation of Pipelines Beneath Levees Using Horizontal Directional Drilling” and is widely accepted across the HDD design world, according to Scholl. These calculations also highlight one of the biggest challenges any HDD design engineer faces: Properly quantifying the risk of a difficult crossing.
As the technology in the HDD industry continues to expand, the lengths and complexity of the bores become longer. Though Scholl has no problem with that, he says there is concern when these record lengths are completed and heralded but with little discussion of the numerous complications, delays and disputes that resulted.
“Just because there has been some success with crossings of this magnitude, does that mean other similar crossings should be attempted? What is the risk of failure? Should a crossing be attempted if there is a 1-in-5 chance of failure on the first attempt? What is the client’s tolerance for risk? Does the project schedule allow for the significant delays that may result if the crossing is attempted? These are the challenging questions we face,” Scholl says. The risk events or operational problems themselves are not all together very different from those encountered during shorter crossings, but the length of the bores magnifies those risks.
Scholl offers this example: With an 8,000-ft pilot hole, even a simple wire line short when 6,000 ft out from the rig, can involve the better part of a week to trip out, repair the wire line, and trip back to the hole face. When compounded on a very long crossing, even small problems like this can significantly increase the duration of a crossing. In the end, the originally estimated duration of a crossing may end up increasing by 100 percent or more. A good design engineer will make the client aware of risks like this during the planning phase.
This is also where an engineer who specializes in HDD can prove to be an advantage to a client. J.D. Hair & Associates, prefers to have an engineer onsite during construction to handle any design issues that may arise.
“A good example would be discovering previously unknown utilities or other obstructions right after the contractor mobilizes to the site. This is particularly true in urban areas,” Scholl says. “The field engineer can put together a workable design on the spot or review any changes that are requested by the HDD contractor, thereby avoiding costly standby time.”
A second example Scholl offers is daily monitoring of the position and curvature of the pilot hole. The field engineer can review and analyze the contractor’s downhole survey data after each shift and verify that the pilot hole is within specification. If a radius of curvature violation is discovered, it can be brought to the contractor’s attention the next day, minimizing the amount of re-drilling that may be necessary.
Thanks to increased knowledge, improved geotechnical data and better design software, rare are the days where a contractor receives an undrillable design. Scholl offers one final suggestion. Often overlooked in the design, but crucial to a successful project, is providing the HDD contractor with reasonable pilot hole tolerances. This gives the contractor flexibility to adjust the bore on the fly. Unnecessarily holding the contractor to strict line and grade requirements or strict radius requirements can increase construction duration, cost and public impact.
Mike Kezdi is an assistant editor for Trenchless Technology.