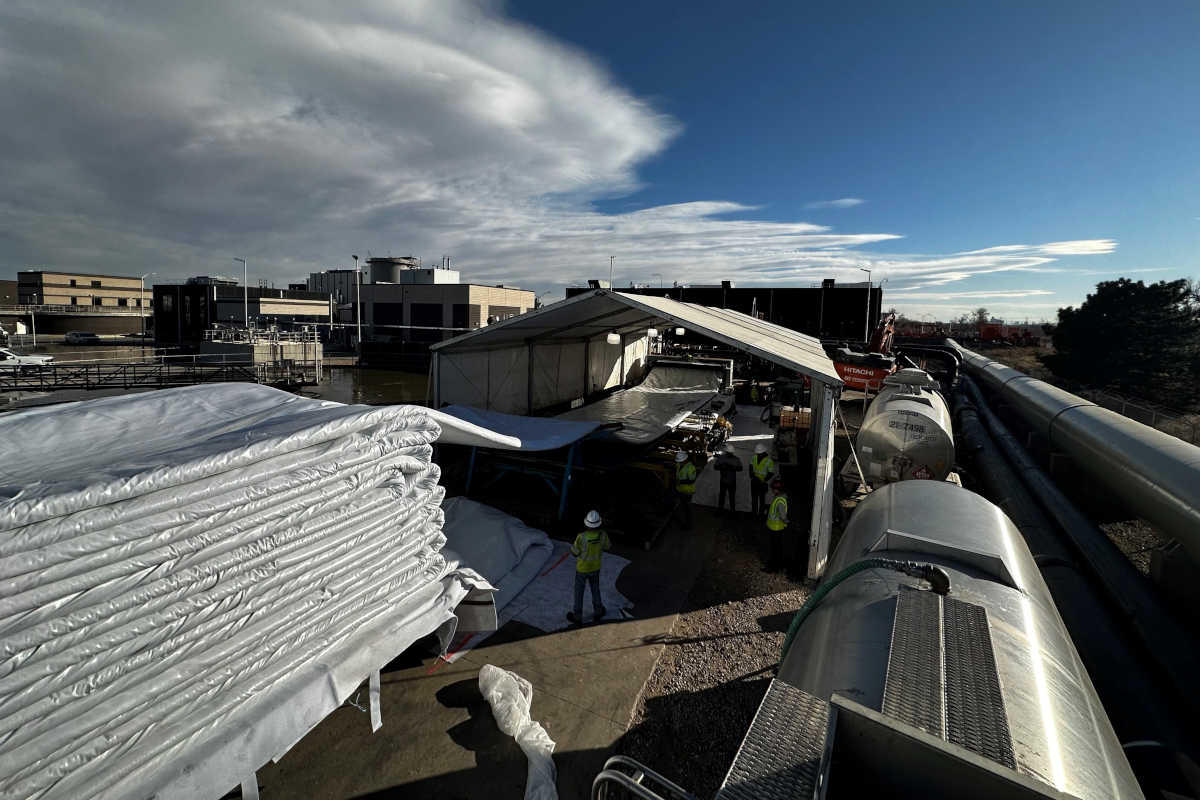
2023 Trenchless Technology Project of the Year Rehab Winner: Robert W. Hite Treatment Facility and Interceptor Rehabilitation Project
Everyone is familiar with the six Ps of any successful project: Prior proper planning prevents poor performance. The rehabilitation of critical pipes to – and inside of – Metro Water Recovery’s Robert W. Hite Treatment Facility (RWHTF) highlights this saying well.
Colorado-based Metro Water Recovery (Metro) serves more than 2.2 million people in an 805-sq mile area and is the wastewater treatment authority for most of the Denver metropolitan area.
The RWHTF, which opened in 1966, has a rated capacity of 220 million gallons per day (MGD) and averages a daily flow of about 130 MGD. The RWHTF has two liquids streams at the facility, the north plant and the south plant, that each treat roughly half of the rated capacity.
The Robert W. Hite Treatment Facility and Interceptor Rehabilitation Project is part of a routine and robust inspection and rehabilitation program that has been in place for years. With approximately 43 interceptors and 240 miles of pipe under its purview, Metro inspects roughly 10 percent of its system each year.
“Based on those inspections, the areas that are rated the poorest we will incorporate into our yearly rehabilitation budget,” says Mark Hofmeister, P.E., Metro Water Recovery. “This project was broken into three phases. Phase 1 and Phase 2 were on our interceptor system and Phase 3 (RWHTF) was our treatment plant site lining the influent conduit that comes into our north primary clarifiers — it’s the main line that goes into our treatment system.”
Employing a construction manager at risk (CMAR) project delivery method allowed Metro to handle the bulk of the project engineering design and Inliner Solutions, a PURIS Company, to handle the construction management and contracting work for the project in a collaborative manner. This collaborative effort across design, scheduling and execution, resulted in a critical project being completed on-time, while maintaining 100 percent plant operation, with zero safety or environmental incidents and staying within budgetary expectations.
Though there are many aspects of the job that are award-winning, it’s the rehabilitation of approximately 2,000 lf reinforced concrete pipe (RCP) at the RWHTF via cured-in-place pipe (CIPP) and sliplining, while maintaining the plant’s 130 MGD average daily flow that earned the Robert W. Hite Treatment Facility and Interceptor Rehabilitation Project the 2023 Trenchless Technology Rehabilitation Project of the Year award.
The overall scope of trenchless work for this third phase included the CIPP lining of 885 lf of 114-in., 410 lf of 84-in., 157 lf of 66-in. and 394 lf of 48-in. RCP. An additional 205 lf of 6-ft by 6-ft square conduit was sliplined with fiberglass reinforced mortar pipe. As this was the major line feeding the North Primary Clarifiers, an in-plant diversion of 30 MGD to the south plant and a bypass of 40 MGD of daily flow was necessary. The bypass required 100 percent redundancy (80 MGD).
But, to better understand the project, it’s best to briefly look at how Metro got here.
Formulating a Plan
As mentioned before, Metro cleans and inspects 10 percent of its system annually and builds its repair and maintenance program accordingly based on the level of disrepair and criticality to the overall system.
With the RWHTF serving approximately 2.2 million people in the burgeoning Denver Metro Area, the rehabilitation of the pipes – which date to the early 1960s when the plant was opened – quickly evolved into a top priority.
Inliner Solutions, with a local office in Kiowa, Colorado, was selected to perform the role of construction manager in August 2020. Inliner’s initial scope for pre-construction services included guidance and support for constructability, means and methods, schedule development, and cost estimates for rehabilitation options; its role expanded into construction management for all phases.
It was during this initial period that both Inliner and Metro determined the best approach for the overall project. This included moving the RWHTF portion to Phase 3 to allow for proper planning and coordination given the complexity of the rehab and the intricacies of the bypass.
According to Mark Slack, regional vice president of Inliner Solutions, Metro’s initial thoughts were that the RWHTF was the most critical and should be done first. Leveraging Inliner’s years of experience, Slack and his team determined that the lining project that would become Phase 1 and Phase 2 could readily take place while planning for Phase 3 was ongoing.
“We started with a small preconstruction services contract, we defined scope and defined what we needed to do as we went along,” says Slack. “That is how we were able to start what is now Phase 1 when we did. That was the easiest part of the three phases. We talked about the RWHTF for about 1.5 years before we did anything with it.”
No project is without its challenges, but Slack and Hofmeister agree that because of the close collaboration of all parties – thanks in part to the CMAR approach – these challenges were kept at a minimum and didn’t impede the project’s on-time completion.
“Truthfully, all of these collaborations are only as good as the people. It could have been a real slugfest going through if this were normal design-bid-build and it would have taken a lot longer,” says Slack.
Take for example, Phase 1. As mentioned before, this was a relatively straightforward relining and Inliner negotiated and collaborated with Metro on a price so the team could quickly move on with the work. No sooner did work commence than resin scarcity became an issue and prices skyrocketed.
“On Phase 1 we were able to hold our price. We had mostly finished pricing on Phase 2, but we could not bear the cost increases on that. Metro was cooperative and understanding that costs skyrocketed,” says Slack. “Those issues reshaped priorities of the project. By moving the RWHTF to Phase 3, it allowed us to see those things that would become increasingly scarce, and we made procurement decisions early so we could stockpile some materials we’d need.”
A Phased Rehab Approach
From late 2020 to late 2022, Inliner coordinated the lining of approximately 40,000 lf of interceptors ranging from 8 to 78 in., using traditional CIPP and a trial installation of 5,000 lf of UV-CIPP on certain sections of 8-, 12- and 24-in. lines. During these phases, Inliner self-performed the work using its over-the-hole and UV crews. Concurrently, its project management team worked closely with Metro to plan, coordinate and procure the necessary equipment to support the RWHTF phase.
“Interceptor rehabilitation work is familiar to the agency,” says Hofmeister. “Phase 1 was the easiest portion and focused on what could be done right away. Phase 2 required more coordination and had more challenges. Phase 3 involved the plant shutdown, which required equipment procurement and coordination between our operations and facilities maintenance crews.”
He adds, “The CMAR project benefit was the ability to talk through these plans as a group – the operations team, engineering and Inliner together – to discuss scheduling, procurement and sub-contractor coordination.”
Among the items discussed were the best time to take the north plant clarifiers down – October to February (minimizing risk from wet weather events), which rehabilitation technologies would best fit the RWHTF repairs, and what other repairs and improvements could be made at the plant during this scheduled downtime. The team also planned the extensive diversion and bypass system and ran flow model simulations followed by actual flow operational simulations of the proposed system in November 2021, a year before actual work commenced.
Pre-planning, including testing, modeling alternatives, constructability reviews, and securing critical equipment in the early stages of the project, eliminated the challenges and created a clear path for continuous progress.
Phase 3 Commences
The planning was complete and in October 2022 work on Phase 3 commenced.
It was determined that the best rehab approach would be CIPP for the bulk of the project. The largest portion being the 885-lf section of 114-in. RCP. According to Slack, the installation is considered one of the largest and longest CIPP installations to date in North America.
“The combination of our in-house manufacturing of the CIPP tube [by Liner Products], the in-house design and manufacturing of the over-the-hole installation equipment and significant number of CIPP installations between 78- and 110-in. each year, gave us the confidence to consider thoroughly and then advocate for the installation of the 114-in. influent line,” says Slack.
With the only viable location to install the influent bulkhead and pumps being in the north grit basin at the beginning of the 114-in. final influent pipe, both CIPP and sliplining using Hobas pipe were used to rehabilitate this section. CIPP was used for most of the pipe and enabled rehabilitation through numerous turns within the pipe. The sliplined portion was a short section from the CIPP insertion pit to the bulkhead. The CIPP and slipline installations were joined using fiberglass joints and then encased in concrete.
According to information provided by Metro, Inliner’s selection of subcontractors provided enormous support for ancillary work. The subcontractors performed as extensions of the project team and were strongly engaged throughout Phase 3.
Key subcontractors handled bypass pumping (Velocity, a Cogent Company), the removal and replacement of 12 sluice gates (Velocity Plant Services Inc.), sliplining (Albuquerque Underground Inc.), miscellaneous structures installations, concrete corrosion protection coatings, structure modifications and repairs (Reynolds Construction Inc.).
“This was open heart surgery, and we kept the patient alive during the operation,” says Slack. “Everything we did at the plant, required a lot of coordination between us and Metro Water Recovery and a lot of in-house coordination between Metro’s engineering and operations groups to just make the plant work so that we could take that 114-in. pipe offline.”
Owner: Metro Water Recovery
Engineer: Metro Water Recovery
Contractor: Inliner Solutions, a PURIS Company; subcontractors Albuquerque Underground Inc.; Reynolds Construction Inc.; Velocity, a Cogent Company; and Velocity Plant Services Inc.
Manufacturers/Suppliers: Liner Products, Applied Felts, Hobas Pipe USA
Value of Trenchless Project (US$): $31,000,000