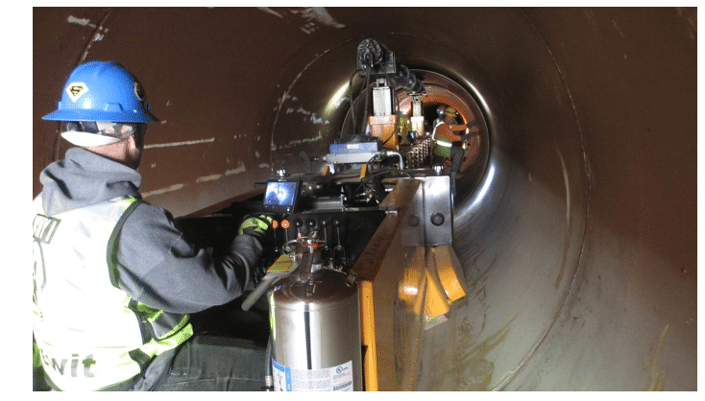
The Invisible Rehab of Phoenix’s Val Vista Transmission Main
June 22, 2017
Snaking its way through the densely populated and growing suburbs of Tempe and Mesa, Arizona, to ultimately reach Phoenix, the Val Vista Transmission main, a single-source water line, delivers approximately 220 MGD of potable water to as much as 60 percent of the City’s population.
As the City’s most critical pipeline, maintaining uninterrupted service was non-negotiable, which is why the City undertook a major rehabilitation project to add 50 years of sustainable life to the aging 35-year-old main with firsts in safety and trenchless technology.
Rehabilitating 6,250 lf of existing pre-stressed concrete cylinder pipe (PCCP) in a major urban area brings its own set of challenges. There was no opportunity to build a redundant line, workers operated in an extremely confined space, and an aggressive timeline of six months had to be met during the coolest time of the year when water usage was lowest in hot-climate Arizona.
RELATED: Emergency Manhole Rehab Project in Phoenix
Other factors made the 2015 project even more challenging: The Department of Homeland Security allowed no main shutdowns during the Super Bowl, shopping districts demanded roads be open going in both directions so holiday shoppers could move easily, and work continued even when 35,000 runners pounded the pavement through Tempe in Pat’s Run, a memorial 5K run for fallen Army Ranger Pat Tillman, an Arizona State University linebacker.
The 90-in. diameter pipe was rehabilitated by teams led by Kiewit Infrastructure West Co. (Kiewit) and Brown and Caldwell using sliplining, with 84-in. steel solid liners and 87-in. steel collapsed liners to upgrade the line. The trenchless technique for sliplining the transmission main was accomplished by installing new steel pipe liners – or a carrier pipe into a host pipe.
The trenchless technique of sliplining enabled crews to do an invisible rehab of more than a mile of the City of Phoenix’s most important water line, the Val Vista Transmission Main. There was no room for a regular open-cut excavation.
A Nearly Invisible Project
A new parallel transmission main was proposed, but because of Tempe’s growth within the water main right of way, there was no room to do a traditional open-cut excavation, with egresses and openings limited.
“There was no way we could build a redundant parallel line because of how densely populated Tempe is,” said Brown and Caldwell construction manager Randy Tirpak. “We had a fixed completion date that we couldn’t go beyond. It was either do this rehab or, due to its deteriorated condition, risk a catastrophic failure.”
RELATED: 2015 Top 10 Trenchless Design Firms Notable Projects
Sliplining the transmission main during low-demand, seasonal shutdown periods 25 ft underground resulted in a nearly invisible project to the residents of Tempe. The steel sliplining method allowed the team to install up to 52 liners per shift, which equates to one liner installed every 9.5 minutes, and equaled 1,100 lf per shift.
“By contrast, if this were a standard remove-and-replace type job, you would have to be excavating down 30-plus ft, and you would have to have areas that opened up 1,000 to 1,500 ft long. Instead, we put in a portal that is 45 ft long by 20 ft wide,” said Kiewit project manager David Markert. “Technology had a bigger role to play in this project. With new advances, we discovered in sliplining and safety, work was done in record time and a significant amount of stress was taken off crews and the client.”
Digging Deep and Getting the Job Done Safely
To gain access to the pipeline, access portals were created by excavating and installing specialized slide rail shoring. Two existing 20-ft segments of pipe were demolished to allow access to the interior of the pipeline. Once the portal development was established, the rehabilitation of the existing 90-in. pipeline started with the steel collapsed liners.
RELATED: Project of The Year- Rehabilitation Runner Up: Newport Beach Water Relining
The challenges of the project called for new innovative ideas and designs that are industry firsts for improved operability, safety and capability.
Customized Pipe Cart: Kiewit designed and built a diesel-powered cart specifically for underground space that crews were working in. Because of the 25-ft confined underground space, the pipe cart was built to transport 9,400-lb liners. With cameras mounted front and rear of the cart, operators were able to work safely within the pipe around crews at the install point. They were also able to see behind safely to back out of the pipe up to 1,000 ft without issue. Markert estimated that the cart did 95 percent of the work, which limited the amount of exposure to the crew to any potential safety issue working with heavy materials.
The crew did not have to move or pick any of the liners with hand tool or jacks to move it into place, but instead relied on the cart to move them into their final installation locations. The team also fabricated a cart that allowed them to line around corners up to 90 degrees easily, which increased the project’s efficiency and productivity. Kiewit has since used the pipe carts on recent projects in 2016 and this year.
Electric instead of diesel blowers: Using 7,000-plus CFM electric blowers proved to be a more environmentally-friendly way to move air through the pipe and maintain a safe working environment safe for the crew. Easy to mobilize from location to location with no trailer needed, the blowers were extremely quiet compared to their diesel counterpart.
Extreme Welding: Once entire runs of pipe were complete, which included fit-up to proper tolerances and tac welded into place, up to six welders per run worked eight- to 10-hour shifts to complete the welding scope of work. There was more than 22,000 lf of welding on the project with a failure rate of less than a hundredth of 1 percent, or 2 ft of repairs.
“These innovations, along with the amount of liners being installed every day, helped us meet our deadlines and schedules and at a more reasonable cost,” said City of Phoenix project manager Mario Brown.
The City of Phoenix credits Kiewit and Brown and Caldwell collaborating well with its operations staff to make a challenging project successful.
“It was a low-profile project because the public could not see us, but a high-profile project for Kiewit, the City, and Brown and Caldwell,” Tirpak said.
“It was a total team effort,” Brown added.
The project was completed 20 percent under budget and 14 days ahead of schedule. The Val Vista Water Transmission Main Rehabilitation won the Engineering News Record’s 2015 Award of Merit in its Best Projects category for the Southwest and was the subject of an Arizona State University student’s 2015 doctoral thesis: “Construction Management at Risk (CMAR) For Pipeline Rehabilitation: A Case Study on CMAR Performance Benefits.”
Leslie Mladinich is marketing communications specialist at Brown and Caldwell.