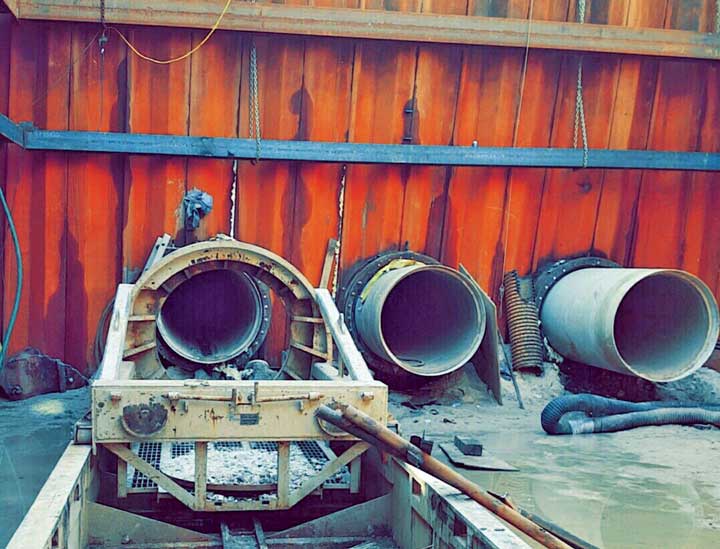
Microtunneling Under the Wolf River in Memphis
The City of Memphis, is home to a lot of cool things. Located on the Mississippi River in southwest Tennessee, Memphis is noted for the influential music of rock ‘n roll icon and king Elvis Presley and blues legend B.B. King, as well as BBQ and Beale Street, all of which and more attracts people from around the globe to this diverse and eclectic city.
The infrastructure of which makes Memphis go is aging like the rest of the underground water and sewer pipes in the United States — it needs help. A recent project utilized microtunneling as the method to replace aging and deteriorating triple-barrel siphons to ensure service would not be disrupted. The work took place under the Wolf River, which flows into the Mississippi River north of downtown Memphis.
RELATED: Trenchless Technology’s Evolution
The three inline sanitary sewer siphons were constructed in 1958 and connected to an 84-in. concrete interceptor tunnel. Given their age, it’s no surprise they had surpassed their lifecycle and needed replaced. For the replacement siphons, 45-in. fiberglass pipe would be used. Magnolia Underground Construction was the general contractor for the project. For pre-qualifications, City officials required an experienced tunneling contractor that had installed projects of at least 10,000 lf of 42-in. diameter or larger jacking pipe. J&J Boring Inc., Winfield, Missouri, met those requirements and had previously worked with both Magnolia Underground and the City of Memphis.
“We had previously worked in 2006 for the City of Memphis, direct jacking 72-in. fiberglass pipe,” says J&J Boring president Jennifer Bouquet. “We were precise with line and grade on that project so when this project came up, the City was confident that would could do it.”
Microtunneling was planned for this project, given its proximity to the Wolf River. Over time, the project morphed into a design-build type environment, with alignment changes, as well adjustments to pit locations due to the ground conditions (sandy clay, course gravel and river rock).
The project was located where Highway
40 at the North McClain Road overpass, a heavily traversed roadway with what Bouquet described as “major rush-hour traffic.” Getting the equipment and materials onto the jobsite was a concern. “An access road with a steep grade was built off the shoulder of the highway,” she says.
RELATED: Microtunnelling Under the Mary Hill Bypass
It was challenging at times to move the equipment and 1,140 ft (in 20-ft sections) to and from the jobsite. Once the equipment and pipe materials were transported to the site, work began. J&J Boring used an Akkerman SL44C microtunneling system, with a 5,200-gallon pump unit.
Project Challenges
The construction site was located just upstream of the Mississippi River, which historically experiences seasonal high water levels. The project became time critical to ensure that the work was completed and all equipment was removed in case the river rose to unsafe levels. Weather delays hampered the start of the work; because of flooding in Mississippi in June 2016, the pipe, though ready, could not be transported.
“We were fine with the delays because we were always concerned about the river,” Bouquet says. “If the Mississippi River floods [due to seasonal flooding], it would back up the Wolf River and that could have easily flooded our location because the area is very low lying.”
Each 380-lf barrel siphon was launched from a single, 20-ft deep shaft with minimal horizontal clearance between each installation. J&J Boring completed the three alignments while achieving outstanding productivity with its microtunneling system and maintaining exact line and grade, Bouquet says.
The first drive was completed on Feb. 17 in four, 10-hour shifts. Next, the crew mobilized the SL44C MTBM back to the launch shaft to set up for the second run. On this run, the crew was able to exceed the first drive’s production rate by installing 220 lf in a single shift. On Feb. 24, the SL44C emerged from the second run in just two, 10-hour shifts. On the final run on March 3, the crew logged another 200-lf before its completion in just 22 hours.
Magnolia Underground constructed the entry and exit pits and J&J Boring installed a pit seal for each run on the launch side and cut holes in the sheet piling at the exit pit, working with Magnolia Underground to control the inflow of material and water from the hole.
City officials were onsite to witness the arrival of the SL44C system into the reception shaft of the final run.
“The timeframe in which this project was completed was pretty impressive,” Bouquet says, noting how quickly each run went all the while maintaining line and grade. “We got faster as we went. The first run took us the longest and the other two were pretty quick.”
Bouquet says what aided in the pace of the runs was that the crew did not use a slurry separation plant, instead using a settlement pond with water pumped out of the Wolf River, which, while saving time, was also cost-effective. “It was on everybody’s minds to get in and get out as quickly as possible,” she explains. “And not using a separation plant allowed for better flow with the slurry system so it went faster.”
Bouquet notes that this project was unique for her company in that the three siphons were right next to each other, with just a few feet separating each one. “All of the lines came out within a quarter inch of line and grade, which is excellent,” she says.
And getting the project done without having to deal with a rising river, was also a good thing. “We were very concerned about both the Mississippi River and Wolf River. Obviously, it wouldn’t come up overnight; however, if we had seen any indications that the river was coming up — which it did right after we left — that meant there would be a lot of equipment to get out of there in a short amount of time. It was definitely on everyone’s mind.”
J&J Boring is a veteran trenchless company that handles large diameter pipe jacking, microtunneling, auger boring, hand tunnels and grouting projects. In business since 1983, the company was originally owned/operated by Bouquet’s father John Carroll and his partner Joe Wolken. Over time, Bouquet and her sisters, Josie and Jaime, as well as their mother Susan, took over operation of the business—pretty unique to have an all-female owned construction contractor.
RELATED: Akkerman Adds GRS-50 Family of Cutter Heads to Its Offerings
“We are very proud of our team on this project,” Bouquet says. “We have many longtime employees, including three brothers who have worked here 25-plus years. Our superintendent was Donald Lickteig, who has been with us for more than 30 years. Everybody was excited with the results.”
Sharon M. Bueno is managing editor of Trenchless Technology.