Microtunneling to Exacting Standards in Holland
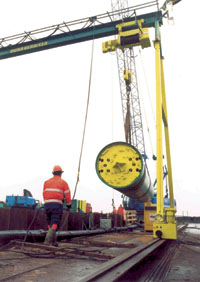
The WRK I and IIpipelines between Utrecht and Abcoude run parallel with the A2 Freeway. Duringthe next few years, Rijkswaterstaat (Directorate-General for Public Works andWater Management) is going to expand the A2 Freeway between Amsterdam andUtrecht from three to four lanes. For this reason, the pipeline to the east ofthe freeway must be moved some 60 m (198 ft) eastward over a distance of about 5km (3.1 miles).
Amsterdam Water carried out the preparatory survey workitself and had been able to decide the course the pipes needed to follow. Aftera pre-selection process, a building consortium, Visser & Smit Hanab,Papendrecht, Netherlands /Dura Vermeer Infra, Hoofddorp, Netherlands, was chosenas the most suitable partners. Good cooperation between Amsterdam Water and thechosen partners meant that a quick match between the owner’s theoreticalapproach and the contractor’s practical approach was possible and this savedtime to produce a good, final, detailed plan.
The building consortium hadlittle time for the drilling activities. The project involved a dual pipelinewith the final 9.5 km (5.8 miles) distance to be drilled. Four tunnel boringmachines, two supplied by Herrenknecht and two designed and manufactured by DuraVermeer were used by two teams for seven days a week for eight months, four dayson and four days off. The machines worked two-by-two toward each other using theslurry shield tunneling method. The route for the installation was divided intosections of a maximum of 900 m (2,970 ft) — twice 450 m (1,485 ft) from eachdirection. The drive pits were constructed at both ends of the section to bedrilled with a reception pit in the middle. The drive pits were speciallydesigned to be used in two configurations in two directions. This was anattractive solution in terms of logistics and economics because the drive pitswere larger than the reception pits, and more materials were needed, such assheet piling, underwater concrete and reinforcement steel. Dual use meant lessconstruction, lower costs and greater efficiency. After the first twoparallel-drilled holes were ready, the machines were reversed and worked in theopposite direction.
In the soft peat soil, the boring machines could notbe offset against the sheet piling as they would normally. The clay/watermixture does not exert much counter-pressure, so the piling would simply bepushed away unless additional measures were taken. For this reason, largeprofiles were filled in the middle of the concrete floor with frames behind itto offset the drilling frame and transfer the thrust to the surroundings throughthe concrete floor.
After the new pipeline had been laid and connectedto the existing one, the section to be replaced was removed. This meant removingaround 1,500 concrete pipe sections. Because the system could not be shut downcompletely and the water transfer had to be maintained throughout, the pipelineswere connected one at a time.
Soil Characteristics
The new part ofthe freeway is being built on an enormous sand bank whose weight compresses thepeat soil layer. Everything else under the freeway can be compressed and moved,including a pipeline. So, after examining the various options, Amsterdam Waterchose to relocate the new pipeline as deep as economically possible. Thetraditional method of construction by excavating a trench was also discountedbecause it would have been expensive and complex since the peat extends from thesurface to a depth of 6 to 8 m (20 to 26.5 ft). Instead Amsterdam Water chose toplace the pipeline in the Pleistocene sand layer under the peat since the newfreeway does not affect a pipeline at that depth. For the construction of apipeline of this size (outside diameter of 1,200 mm/48 in.), both concrete andsteel can be used. The consortium chose steel for economicreasons.
During the preparation, it became apparent that the permitauthority, Hoogheemraadschap Amstel Gooi en Vecht, would set exacting standardswhere the pipeline passed under the Geuzensloot. The Geuzensloot is an excavatedcanal at NAP level (Normal Amsterdam Water level). Because the banks of thecanal are regarded as primary water-retaining structures, the Hoogheemraadschapstandards are set for exceptional levels of construction stability and safety.For the crossings the new pipelines pass under the Geuzensloot in additionalcasing pipes with a diameter of 1,500 mm (60 in.). This alteration to the plansmeant more work and more time to get it done.
The entire project wascarried out with minimal removal of groundwater. The removal of groundwater andits discharge are sensitive topics in the Netherlands — especially in view ofthe fact that the pipeline is being built at a great depth through boring and agreat deal of drainage would normally be required in peat soil to keep the pitsdry. This meant that an alternative solution was required. The method chosen wasmore expensive than pumping out excess water but did not have the dischargeproblem. The pits were designed to be waterproof and the pipe jacking wascarried out without allowing water in flow. The pipes were jacked through aspecial rubber seal designed to withstand both the hydrostatic pressure and thepipe movement to prevent groundwater from entering the pit.
AmsterdamWater and the contractor’s consortium approached this project as a joint teamfrom an early stage. The fruits are evident in the quality of the detailed plan,while short communication lines and quick responses for decisions saved time.The consortium was able to carry out the project in the most economical way anddelivered the result that the customer wanted — an optimal win-win situation.
Summary
Where a technically complexproject is concerned, a year passes by in no time, even if the twin pipeline tobe built is only 5 km (3.1 miles) long. The pipeline was constructed entirely bymicrotunneling in Pleistocene sand at a depth of 10 m (33 ft). Peat is locatedabove this layer of sand, which is not the favorite kind of soil for pipelineowners or contractors. The performance of Visser & Smit Hanab/Dura Vermeerconsortium was unique in delivering this complex project on time, safely and toa high quality.