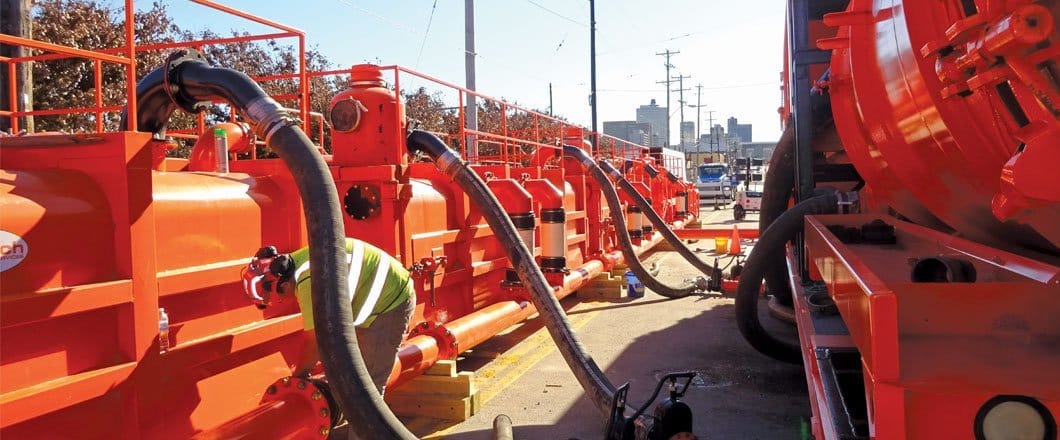
Front Street Cleaning – Memphis Project Requires Specialized Cleaning Approach
The City of Memphis, Tennessee, is working through its SARP10 program, a 10-year initiative to improve its entire sewer system.
The SARP10 — Sewer Assessment and Rehabilitation Program — is a series of condition assessment and construction rehabilitation projects and is expected to spend approximately $250,000,000 over the program’s life. A recently completed portion, the nearly $4.5 million Front Street Interceptor Cleaning project, highlights the benefits of collaboration and the challenges of cleaning large-diameter pipe.
Project Focus
The objective for this project was to clean three surcharged segments of the 105-year-old Front Street Interceptor, which were heavily impacted by sewer debris. The project was a collaborative effort between Baton Rouge, Louisiana-based Compliance EnviroSystems (CES) and Warren, Michigan-based Doetsch Environmental Services. Also working on the contracting side was Cambridge Construction Management Inc. CES handled project management and condition assessment and Doetsch handled the specialized large-diameter cleaning.
“With effective team approach, we were able to focus on the cleaning and CES handled the project management, safety oversight and the final and interim sonar inspections,” says Joe Schotthoefer, Doetsch Environmental Services. “We’ve been working with CES in Memphis since 2015. This is the largest project thus far.”
Schotthoefer, first connected with the CES leadership at a NASSCO event and the two companies completed their first team project in 2011.
RELATED: Big vs Small: Are You Ready for Large-Diameter Pipe Cleaning?
The team’s goal in Memphis was to remove solids and sludge from approximately 4,000 ft of the 94-by-84-in. arch pipe interceptor at depths of 60 to 90 ft. and do so with minimal disruptions to traffic and surrounding areas. A 6,000 ft-long reach reel with a double hose high-pressure cleaning operation was used and one set-up to alleviate traffic disruptions in downtown Memphis throughout the project’s life.
Challenges Faced
Making things more of challenging for the cleaning was that, at some point in the mid-1900s, the pipe’s flow direction was reversed, and a pump station was built to move the effluent. This meant that the project team had to work uphill, and at the same time ensure that none of the debris got through to the pump station.
“We were cleaning the pipe with flow, but the grade was uphill. That presented its own challenge because we didn’t have gravity on our side with this,” says Schotthoefer. “Because of the way that was setup hydraulically, it allowed for a lot of this garbage, ragging and junk to settle out, as well as sewer debris. What would be typically left behind is sand, gravel and particles that don’t convey to the waste treatment plant. In this case, we had that plus large amounts of sanitary trash.”
To make the cleaning a success, Doetsch pulled from all its experiences and combined that knowledge and equipment to create a complex cleaning setup that looked more like a microtunneling construction project than a sewer cleaning site. The planning began in Michigan where the team mocked up the project site – down to where hoses would run – in its parking lot. Setup in Memphis began in the fall of 2019, and the work went through the end of August of 2020.
RELATED: Compliance EnviroSystems a Southeast SSES Leader
Specialized Equipment
“This project used equipment that is specifically designed for this task. What we had and why you see what is there, is because of our proximity to the pump station. We were approximately 200 ft away from it,” says Schotthoefer. “The equipment is filtration and settling equipment so that we would not loosen up debris and send it on to the pump station. These multiple stages of filtration was certainly a first. This allowed us to work on recycled water as well. We were pulling the water out of the sewer, separating the debris, settling the debris, taking the water, filtering that and reusing that as our injection water.”
The depth, narrowness, and constant surcharge conditions made manned entry into the manholes a safety concern; however, the CES Doetsch team could clean remotely due to its long-reach capabilities, eliminating the need for manned entries or multiple equipment setups. The CES Doetsch team used a cleaning system capable of three to four times that of a conventional sewer cleaner for the project.
The high-pressure vacuum and hydraulic power unit generated enough head to remove densely compacted debris and large items of sanitary sewer trash.
With a classic combination jetting/vacuum machine, the water propels the cleaning nozzle up the line. If the nozzle is too small, the material is thrown behind and goes to each side or makes a small pile behind the nozzle and then spills over.
Like when shoveling snow or working in a garden, a shovel has a capacity. When the ability of the shovel is reached, the material will fall off. To increase the shovel capacity, the team used a larger shovel, or in this case, a larger ‘aqueous shovel.’
The custom large-diameter cleaning equipment and the process is designed to remove debris in a pipe of this size and under surcharge
conditions.
The CES Doetsch team customized the cleaning process for this project based on data from divers and experience with large diameter sewers. The changing or unknown water flow velocities of the sewer system required frequent modifications that depended on the conveyance of the water to remove the material.
The increased water flow and pressure allowed a 200-lb nozzle to propel through the sewer generating a giant ‘aqueous shovel’ that effectively moved more debris in the large diameter Front Street Interceptor.
A purpose-built apparatus launched the cleaning head nozzle under the water flow upstream — the device road on a rail fastened to the fabricated extraction tube. The crew utilized a relay system to shorten the travel distance of the nozzle.
The CES Doetsch team used step cleaning to monitor the amount of debris pulled back on each step to maximize the carrying capacity of the nozzle. It allowed for a more thorough removal of loose debris
in the pipe, leaving no residual remains behind. The process for extracting the debris was also unique as it took place at the bottom of a vertical manhole. The primary process was effective in removing large debris. The secondary process consisted of controlled extraction to remove finer material.
All told, the project team was able to remove approximately 400 tons of debris in 300 calendar days.
Editor’s Note: The Front Street Interceptor project was recently named the runner-up for the 2021 Trenchless Technology Project of the Year for Rehabilitation. This story originally appeared in print in the November/December 2021 issue of Pipe Cleaning PRO.
Mike Kezdi is the managing editor of Trenchless Technology.