Laser Technologies: Taking the Guesswork Out of Pipeline Condition Assessment
February 15, 2012
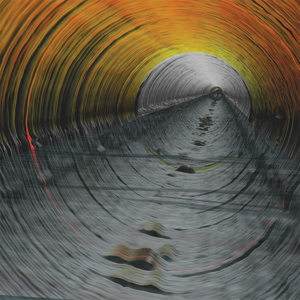
Wastewater managers make these crucial prioritization and investment decisions based on the best information available to them at the time. Unfortunately, this information is often incomplete and inconclusive at best. Closed-circuit television (CCTV), the primary technology for assessing sewer pipe condition, is a qualitative tool that captures video images from inside pipes. Especially in critical large-diameter trunks and interceptors, visual-only inspection is often unreliable and leaves decision-makers with the tough task of evaluating which pipes might appear to be deteriorating. With costly rehab decisions at stake, wastewater managers need facts on corrosion severity, not just visual evidence of potential problems.
Fortunately, a wide range of tools have been developed to complement CCTV inspections and provide wastewater managers with objective measurements. One of the most useful technologies is laser scanning, which precisely measures a pipeline’s size, shape and level of corrosion. These quantitative measurements can characterize corrosion deterioration, identify deformation and allow decision-makers to objectively benchmark portions of the collection system for prioritization of repairs or replacement. Over time, these measurements can provide a calculated rate of deterioration so managers can understand where and how problems are developing. In addition to these measurements, many laser technologies generate color-coded 3D models to visually show problem areas in an easy-to-understand format.
LIDAR & Structured Light Profiling
When someone refers to “laser scanning,” they are actually referring to one of two commonly used “laser” technologies: Light Detection and Ranging (LIDAR) or Structured Light Profiling. Both laser technologies are similar in that they only take measurements above the fluid level and do not work underwater. Inspection techniques that measure below the fluid level, such as sonar, can be combined with either laser technology to measure the full 360 degree cross-section of the pipe, which is critical to accurately assessing corrosion, deformation and sedimentation levels. While LIDAR and Structured Light Profiling collect similar information, they work using different methods.
LIDAR works by bouncing photons of light off of an object (in this case, the pipe wall) and measuring how long it takes for that light to return to the LIDAR scanner. This measured time-of-flight can then be converted to a distance measurement. Photons of light can be sent out by the scanner at all angles in all directions. These individual measurements can be assembled into a full 3D model of the pipe interior, called a “point cloud.” The 3D model can then be analyzed to highlight areas where the pipe is corroding or deforming.
Structured Light Profiling, often called “laser profiling,” uses a visible laser in conjunction with a conventional CCTV camera. The laser projects a red ring onto the pipe wall at a precise distance in front of the CCTV camera. With the lights of the CCTV camera turned off, this red ring is easily visible in the image. Image processing techniques can then measure the size and shape of the red ring. For example, if the pipe is deformed or misshapen, the red ring will appear to be an oval. If the pipe is corroded or becomes enlarged, the red ring will appear closer to the edges of the camera’s image. Each frame of the video constitutes another cross-section measurement of the pipeline, and as the inspection progresses through the pipe, these slices can be assembled into a full 3D model.
Which Technology Is Right for the Job?
LIDAR and Structured Light Profiling are both valuable technologies. Which technology will better meet the needs of a given condition assessment project will depend on the pipe’s size and the intended purpose of the survey.
Each technology works within a certain range of pipe sizes, so considering the pipeline size is a good place to start in choosing the appropriate technology for a given project. LIDAR has only been commercially used in pipelines of 30 in. in diameter and larger, but can be used to scan even the largest deep tunnels and underground chambers, including successful surveys of tunnels measuring 240 in. and larger. Structured Light Profiling can work in pipelines as small as 6 in. but is less feasible in pipes larger than 120 in. Structured Light Profiling is difficult to scale to larger pipe sizes, since the power of the laser and the distance it is fixed in front of the camera must both increase with the size of the pipe. Apart from size, both technologies work in round or non-round pipes and in all common pipe materials.
The purpose of the inspection may also play a role in determining which technology is better for a particular job. Both technologies produce similar condition assessment information such as corrosion levels, deformation, and size measurements. However, LIDAR can also provide additional information. Since LIDAR is scanning full 3-D point clouds, features like bends in the pipe can be accurately modeled and measured. When it comes time to slipline a given section of pipe, the precise bend angles and bend radius measurements from the LIDAR can be factored into the rehab design. Structured Light Profiling, since it is only measuring cross-sectional slices of the pipe, will not be able to measure bends. On the other hand, Structured Light Profiling surveys can often be done more quickly, and thus less expensively, than LIDAR scanning. Both technologies produce results of similar accuracy — typically 0.5 percent of the pipe’s diameter or better.
Fact-Based Decision-Making
Whether using LIDAR or Structured Light Profiling, wastewater managers will be able to base their decisions on objective and quantitative information. Instead of poring over videos and photos to deduce which areas might be suffering from the worst problems, imagine being able to compare a pipeline that has 1.4 in. of corrosion wall loss vs. another with only 0.6 in. By scanning the same pipeline over multiple years, decisions can be based on a rate of deterioration and a fact-based remaining useful life.
If you injure your leg, a doctor will likely complement their visual observations with an X-ray to objectively determine if you’ve broken a bone. Just like X-rays at the hospital, today’s laser technologies provide wastewater managers with objective information to take the guesswork out of condition assessment. With limited funds, this information allows wastewater managers to most wisely steward our infrastructure.
Kevin Lipkin is a technology specialist at RedZone Robotics.