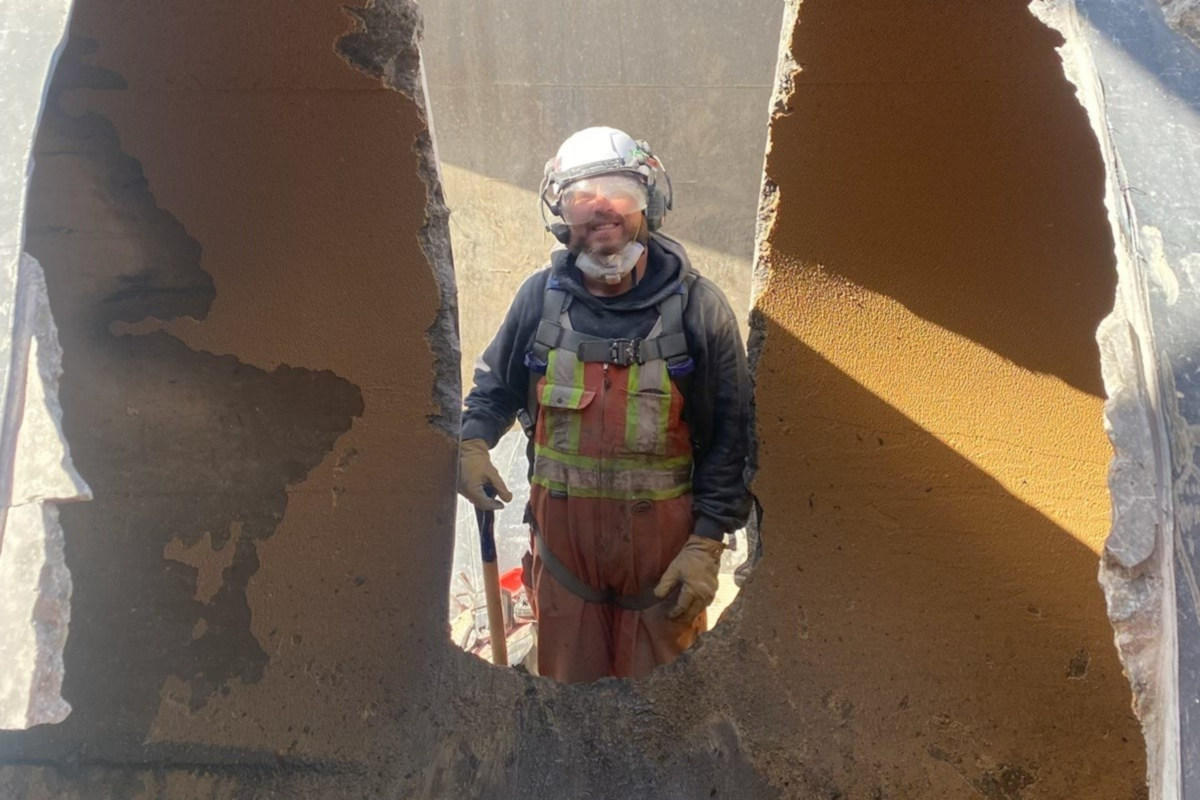
Large Diameter PCCP Water Main Failures
Water system owners have long known that certain vintage pressurized concrete pipes can break at a moment’s notice.
When looking at concrete pressure pipe for water applications, there are four AWWA classifications – AWWA C300, C301, C302 and C303. According to Chris Macey, P.Eng., AECOM’s global practice lead for condition assessment and rehabilitation, it’s the prestressed concrete cylinder pipe (PCCP) AWWA-C301 that really makes the news.
“The performance history of all the rest is much better and the predominant failure mode much less catastrophic,” he says. He adds that there is a particular era of vulnerability that is well documented for PCCP – pipes manufactured and installed between 1972 and 1984.
Sometimes when PCCP fails it is a slow burn to complete failure – allowing time to allocate funds and complete a repair. Other times, it’s an unexpected failure leading to an ‘all hands on deck’ emergency. It seems that every few years the latter occurs. There is a catastrophic break that draws national or international attention.
Notable PCCP Breaks in 2024
2024 happened to be such a year for the cities of Calgary and Montreal.
Both cities faced significant challenges with major failures that impacted thousands of residents. The breaks cost the cities millions of dollars with Calgary, estimating the break and initial repairs costing $20 million to $25 million.
The failures prompted investigations into the causes of the breaks, as well as looking for ways to repair the failed lines and harden their systems from future catastrophic events.
It’s important to note that both cities have condition assessment programs in place and both pipelines were either recently inspected or on the radar for inspection and repair.
“It is indeed an irony that the two cities in Canada that likely assess more PCCP than anyone else in Canada experienced these failures,” says Macey. “It does highlight the complexity of diagnosis in systems where the vast majority of PCCPs are not failing.”
Dave Russell, founder of Russell NDE and PICA Corp. – companies that specialize is pipeline condition assessment and associated technologies – notes that PCCP is rigid and good for pressure retention. However, when the steel prestressing wires corrode, it expands and makes the cracks worse.
“Then you get a lot of wires, close together, in adjacent spots failing. The hoop pressure inside the pipe from the internal pressure exceeds the ability of the cylinder to carry the load, so it fails,” he says.
Areas of wires failing close together are often referred to as broken wire zones (BWZ). When these BWZs fail, it’s a zipper effect.
“It’s very challenging to know exactly how much tension was there from the manufacturing process and where and when ultimate failure will really occur,” Macey says. “When it fails in this manner, it’s like a zipper coming undone.”
Bearspaw South Failure
Calgary’s water main failure occurred on June 5, 2024, when the Bearspaw South Feeder Main — a critical component of the city’s water distribution network — ruptured. This pipeline, built in 1975, of PCCP and carbon steel pipe segments, is responsible for transporting approximately 60 percent of Calgary’s treated water supply.
The rupture in a 4.9-m long section of 1,950-mm PCCP led to a local state of emergency, water restrictions, and significant disruptions for residents and businesses.
In response to the crisis, Calgary took several proactive measures. City officials ordered a third-party review by Associated Engineering and Pure Technologies to understand the factors that led to the pipe’s failure. The investigation revealed several contributing factors, including microcracks in the pipe’s protective mortar layer, high chloride levels in the surrounding soil, and severe damage to the prestress wires due to stress corrosion and hydrogen embrittlement. These issues had been developing over time, ultimately leading to catastrophic failure.
Macey notes that the discovery of high chloride levels in the soils is significant. “Areas that use de-icing salts for ice control on roads in the winter, or that have naturally elevated chlorides or very low pH soils (acidic) are problematic for PCCP,” he says, pointing to the crucial role the mortar layer plays in the construction of PCCP. (See PCCP Construction & Failure Modes sidebar below.)
Bearspaw South Repairs
From June 5 to Nov. 26, the city completed 29 repairs along the feeder main, including the original break and subsequent segments needing urgent repair following the break.
Looking at the Bearspaw South Feeder Main failure and the future needs for Calgary, the city is taking actions to improve the resilience of the water supply system. The city also implemented a medium- to long-term rehabilitation plan for the feeder main, including individual pipe replacements as needed.
“To improve the reliability of the PCCP portion of the Bearspaw South Feeder Main, several rehabilitation and replacement options have been identified and are currently being explored,” Calgary’s utilities delivery team wrote in its collective response to Trenchless Technology. “The options include open-cut pipe replacement, external reinforcement, internal lining and microtunneling of a new line. The microtunneling option has been selected as the most promising option at this time.”
Proactive Efforts
“For more than 40 years, the city has been managing water loss using leak detection strategies and technologies to find and repair leaking infrastructure,” said Calgary’s utilities delivery team. “The city has an annual inspection program for its pipe assets, including feeder mains. The logistics of inspecting over 5,000 km of pipe means that inspection data is supplemented with modeling of pipe condition. Inspection data are used to calibrate this model, which also incorporates factors of pipe material, pipe age, known condition, failure history, location, operating pressures, soil parameters and cathodic protection.”
As a matter of fact, the Bearspaw feeder main saw maintenance work in spring 2024. Test shutdowns also occurred at the end of 2023 and early 2024, in preparation of a planned full condition assessment at the end of 2024.
Based on historical information regarding feeder main breaks, Calgary focused its asset management practices for PCCP on mitigating the effects of high sulphate soils.
“The city also recognizes that our past risk assessment and prioritization approaches were biased toward the mitigation of the likelihood of failure,” says the response from the city. “In the case of the Bearspaw South Feeder Main, the likelihood of failure was extremely low when compared to other feeder mains within the network. This emergency has shown the need for our risk and asset management practices to put a larger emphasis on the consequence of failure, given the obvious severity of the break that occurred this past summer.”
The city is also studying further what led to the increase of chlorides in the soil, believed to be linked to the premature failure of the feeder main.
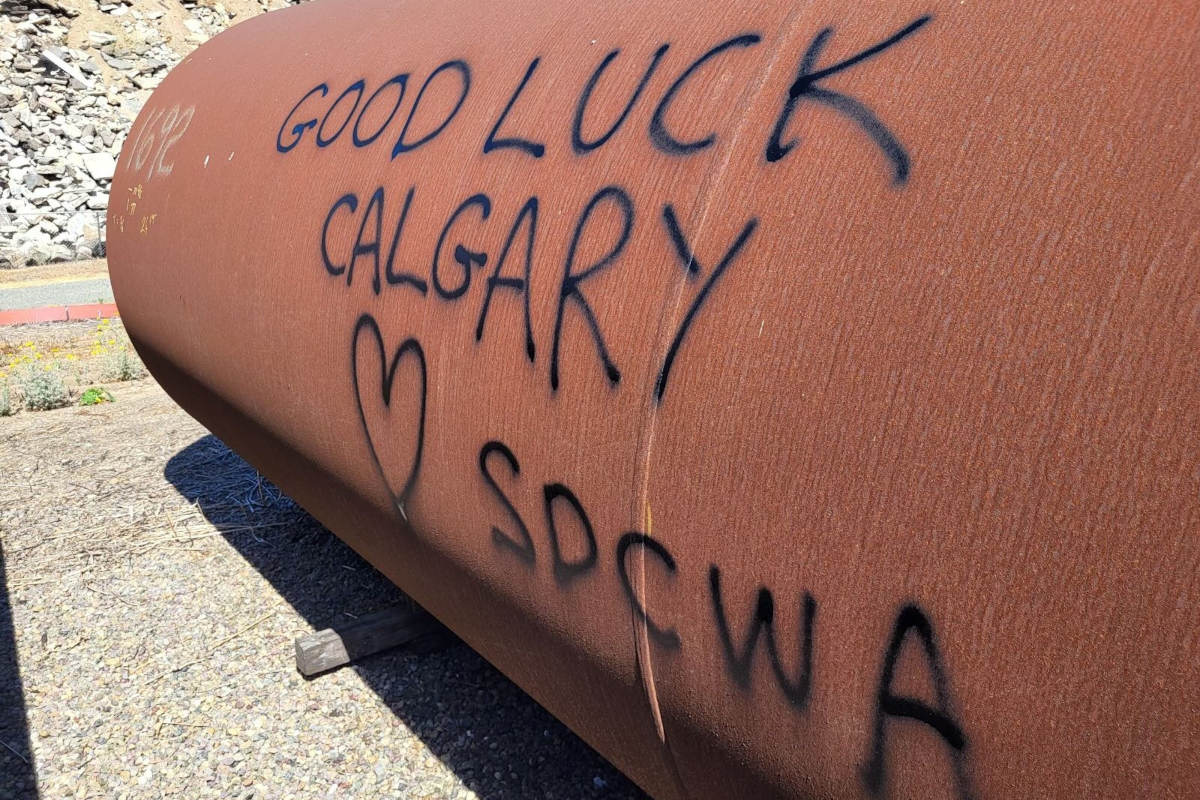
Calgary Is Not Alone
Though not as recent, several cities in the United States are keenly aware of the impact of pressurized concrete pipe failures in their systems. In 2023, we highlighted the reactive-to-proactive shift in Miami-Dade County following a catastrophic failure of 54-in. PCCP in 2010. Read it here: trenchlesstechnology.com/miami-dades-condition-assessment-program-keeps-the-water-flowing.
Another advocate of proactive management of PCCP is the San Diego County Water Authority (SDCWA). SDCWA is considered an industry leader in proactive management of PCCP pipelines.
SDCWA’s first pipelines were constructed in the late 1940s, and the aqueduct system expanded, on average, by 4.5 miles per year until 2015. The system has 308 miles of large diameter pipeline. Of that, 80 miles is PCCP.
“Following a localized failure of its oldest section of PCCP in 1979, corrosion studies and a subsequent rehabilitation of five miles of PCCP in the 1980s were performed,” says Martin Coghill, O&M Manager for asset management, SDCWA. “Fearing a widespread problem, a comprehensive condition assessment effort, initiated in the early 1990s, analyzed pipe that was between 30 and 40 years old.”
Initially, SDCWA used remote field transformer coupling (RFTC) technology, to determine baseline wire breaks; and hydrophone arrays, used to detect active wire breaks within the pipe in service. Hydrophone arrays were replaced by more advanced acoustic fiber optic (AFO) monitoring as the industry’s leading standard for active detection of PCCP wire breaks.
Unfortunately, much like in the case of Calgary, being proactive just wasn’t enough. “Prompted by another major failure in 2006, The Water Authority installed AFO within all its in-service PCCP from 2006 to 2009,” says Coghill.
2006 Data
Coghill notes that the 2006 failure proved fortuitous. The section of pipe that broke had the AFO cable installed just prior to the failure. What that meant is SDCWA had the wire break data to help build a model to avoid future failures.
“You can see in our data that there is one week between the first, second and third wire breaks,” Coghill says. “But in less than a day there were 16 breaks that led to the failure.”
This is important data to have, especially in the case of SDCWA in which the system doesn’t have much redundancy, and any break could have system-wide impacts.
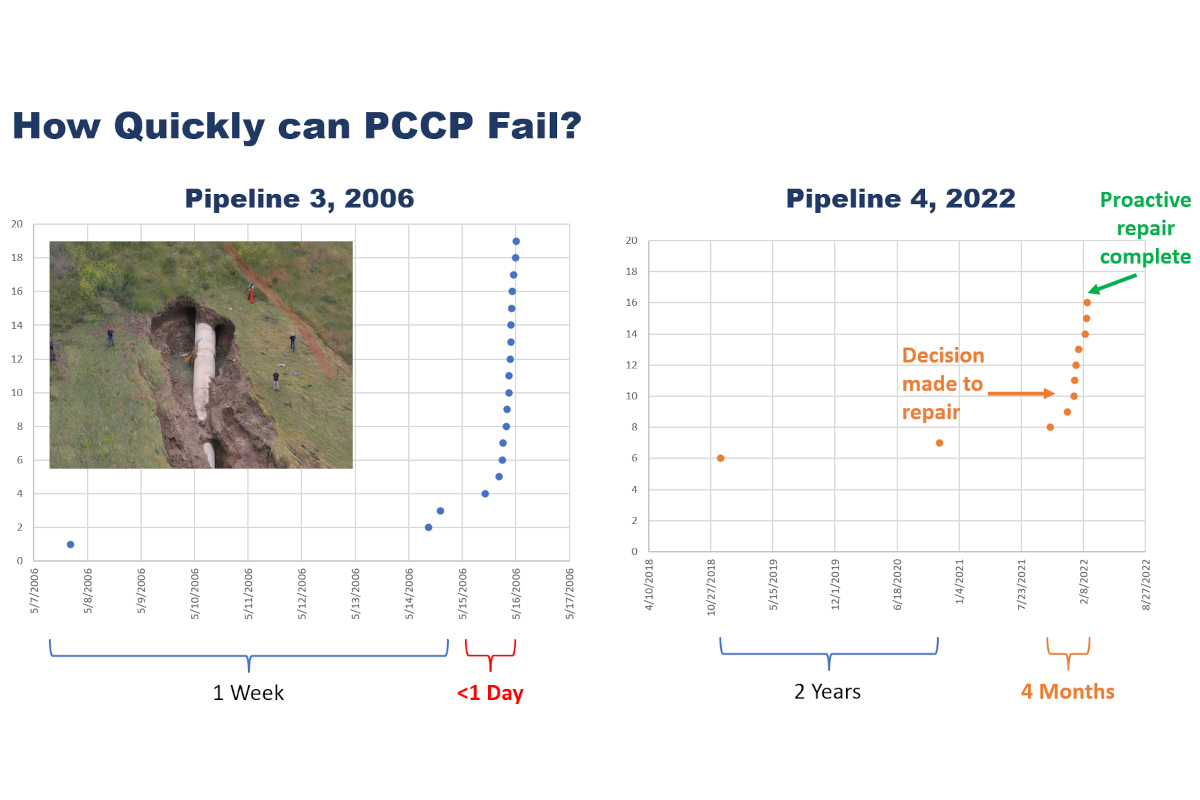
Lesson Learned
Fast forward to 2022, a segment of PCCP showed two wire breaks between October 2018 and October 2020. Then, starting in October 2021, an uptick in break frequency occurred. This prompted SDCWA to okay an urgent repair of the segment with the repair completed in February.
Between the decision to make the repair and when the repair was completed, the line experienced six further wire breaks. No doubt a path to failure, Coghill says.
“If the pipe had burst, there’s no way that we could have responded fast enough to isolate the pipeline before releasing millions of gallons of water,” says Coghill. “You see how little information that we made that decision on. And part of the reason for that is because of the impact — if that pipe stick had failed unexpectedly, we were in a whole world of hurt.”
In 2022, SDCWA performed a finite element analysis on the pipe section that appeared to be failing. This analysis was necessary because the pipe had to remain in service for several weeks before repairs could be completed.
“The resulting risk curve proved highly valuable in determining the need for an urgent repair and highlighted the susceptibility of the particular class of pipe in question to reaching a serviceability limit state with just a few wire breaks,” says Coghill. “As a result of this experience, the Board of Directors approved the development of risk curves for all remaining classes of PCCP pipes in service. Approximately 200 risk curves have been developed and are used to analyze the proximity to, or exceedance of, critical limit states.”
Repairing PCCP
Since the 1980s, the bulk of SDCWA’s problematic PCCP has been rehabilitated in-house using steel relining. The collapsed steel liner sections are inserted into the pipe, moved to its final location, the bands are cut, and the sections are welded circumferentially and longitudinally. Annular grout and mortar lining are applied as corrosion protection on both sides of the liner.
Coghill says that since the program started, the authority has rehabilitated 50 miles of PCCP with just over 25 miles of non-rehabilitated PCCP remaining in-service and actively monitored.
“It remains the water authority’s intention that all in-service PCCP pipe be actively monitored using AFO technology where technically feasible,” says Coghill. “Contracts for monitoring PCCP pipe have been established with the sole provider of this technology, Pure Technologies.”
Another option for the trenchless repair of PCCP is the use of carbon fiber reinforced polymers – from companies like Quakewrap, Structural Technologies and TCI Carbon Fibre Technologies – covered under AWWA C305.
Prevention Via Assessment
That is why having this condition assessment data is so important and all agree more work needs to be done.
“People are still using concrete pressure pipe. The use of condition assessment technologies is one of the key steps in avoiding these kinds of catastrophic breaks,” Russell says. “Another is employing cathodic protection measures when the pipe is first installed, however, it potentially can lead to hydrogen embrittlement cracking of the wires.”
Discussing the latter, Macey adds, “Cathodic protection is complex on PCCP as too much current induces hydrogen embrittlement of the wires. It can be done but needs to be done very carefully and galvanic anode systems are less risk than impressed current. Coatings in extreme environments and the use of silica fume in the mortar are also very effective.”
On the condition assessment front, Russell says that with frequent inspections – beginning within the first decade a pipe is in the ground – the likelihood of an unexpected failure lessen.
“Full time monitoring of the lines through fibre-optic cables inside the pipe can ‘hear’ the sound of wires snapping. Alternatively, running an inspection tool through the pipes periodically – maybe every five years and taking a proactive repair approach will avoid failures,” he says. “RFT in-line tools can detect wire breaks, cylinder corrosion and loss of preload well before the pipe fails. Acoustic tools such as Navigator, Smart Ball and Pipers can hear the sound of water rushing through a pinhole leak.”
Russell adds that the industry’s understanding of the cause of PCCP water main breaks and prevention has certainly evolved and improved over the years.
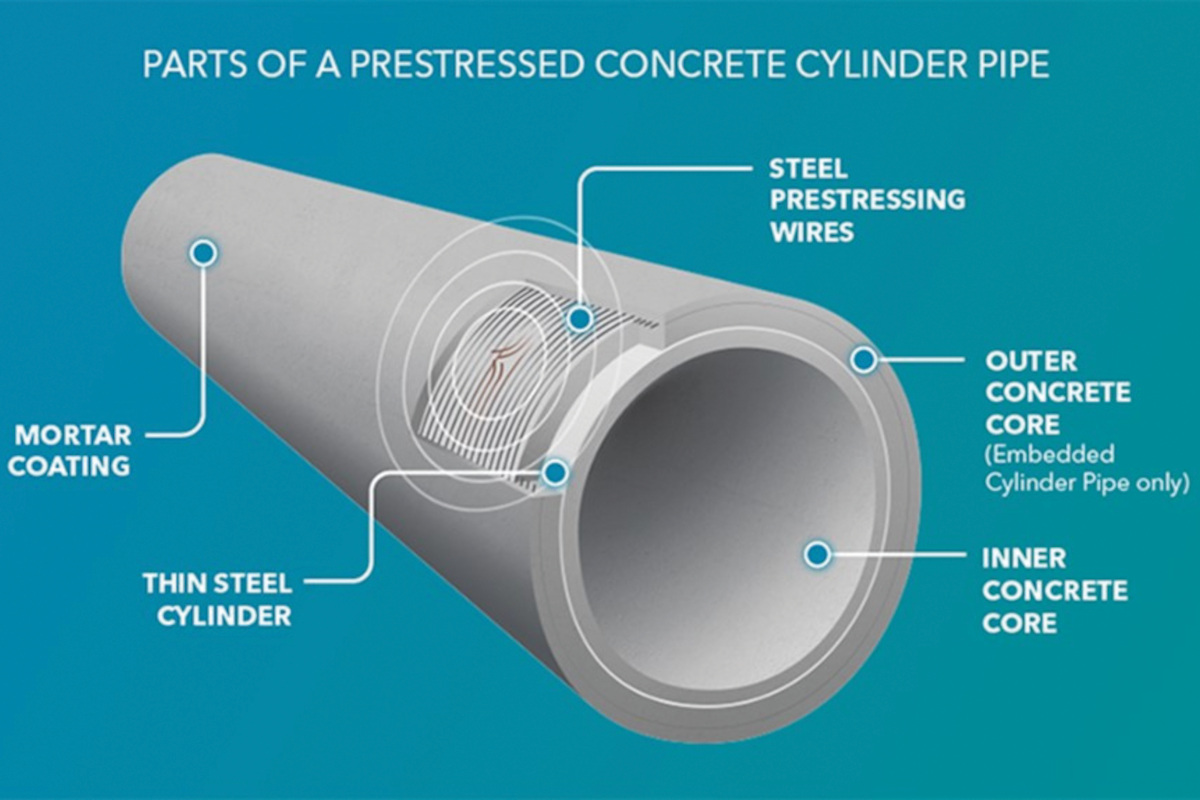
PCCP Construction & Failure Modes
Understanding the construction of PCCP is crucial to understanding its failure modes. PCCP consists of a concrete core, steel cylinder, prestressing wire and a mortar coating.
There are two kinds of PCCP. Lined cylinder pipe (LCP) has prestressing wires wrapped on the steel cylinder and covered with an outer coating of mortar. Embedded cylinder pipe (Bearspaw South Feeder Main) where the prestressing wires are wrapped on the outer concrete core and the steel cylinder is embedded between the inner and outer concrete cores.
“The high tensile prestressing wire is intended to keep the concrete core permanently in compression as concrete does not do well in tension,” says Chris Macey, P.Eng., AECOM’s global practice lead for condition assessment and rehabilitation. “The outer coating of mortar is critical and intended to provide corrosion protection for the prestressing wires and in lined cylinder pipe for the cylinder, as well.”
He adds that in the case of the Bearspaw South Feeder Main failure the high chloride levels are significant to note.
“The way the mortar provides corrosion protection to the steel wire and/or cylinder is not by being a watertight coating, it elevates the pH of the steel to 12 or 13,” Macey says. “When steel is that alkaline, it cannot corrode. What chlorides or other naturally acidic soils can do, is lower the pH of the mortar.”
Since the mortar is not watertight, the steel starts to corrode and increases in volume causing the mortar to pop off. As the mortar pops off more wires are exposed leading to more corrosion.
“As the wires are under very high tensile they are particularly vulnerable and the corrosion rate is accelerated versus that of steel that is simply exposed,” Macey says.
The latter is why Macey refers to the timespan between 1972 and 1984 as the era of vulnerability as many pipes in that area used higher strength and thinner diameter prestressing – known as Type III and IV wire. Both require less deterioration to fail due to the reduced diameter.
The other common failure modes of PCCP are failure of the steel joint rings that refers to leaking and blow-out failure of the welded spigot-bell joint. The other is failure of the steel cylinder and welded joints. This type of failure primarily occurs due to the low joint rotation tolerance of PCCP accompanied by relative pipe movement.
More Research Needed
However, there is some work that still needs to be done. Much of the information and detection to date is focused on corroded wire breaks, however that is only part of the picture.
“Studies by PhDs and specialist engineering companies have calculated the number of adjacent failed wires that must break before a loss of preload (and failure) occurs. What is not well understood is the failure risk of PCCP pipes that have wires that have hydrogen cracks but are not cracked in a local area,” says Russell. “Choosing the right type of ILI tool and technique can reduce the risk of misdiagnosis.”
He adds – as an overarching theme for all water utilities – frequency of assessment is key. The Calgary failure cost the city more than $20 million.
“Compare that to maybe a half-million dollars to inspect a length of pipe every five years. That’s a good investment,” he says.
Mike Kezdi is managing editor of Trenchless Technology.