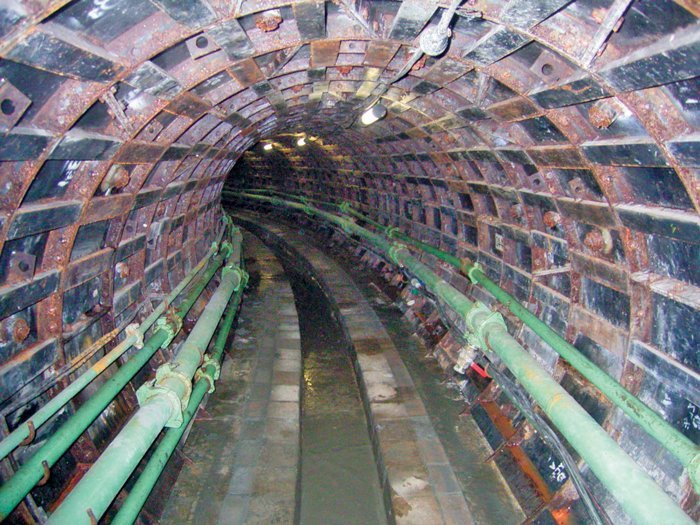
Japanese Manufacturer Considering Move to U.S. Market
November 13, 2014
The latest company looking to take a bite out of the North America’s growing pipe relining market is Ashimori Industry Co. Ltd., of Japan, with its PALTEM family of products.
Flow Ring After
Ashimori Industry Co., which developed its PALTEM cured-in-place pipe (CIPP) relining method in 1980, is looking for licensees and contractors for its Super-HL (hose lining) CIPP method for high-pressure water mains and its Flow-Ring structural relining system, which can be applied to a variety of pipes and conduits from sewer and agricultural water to cable and other buried utilities.
“We were attracted by the market size, the fact that the average pipe age is probably slightly older than in Japan and the expanding need for water pipeline rehabilitation,” says Katsuhiko Azuma, general manager of Ashimori’s PALTEM & Anti-disaster Product Division.
Ashimori developed PALTEM, short for Pipeline Automatic Lining sysTEM, in Japan in conjunction with a Japanese gas company and the first successful installation was in 1980. The first installation outside of Japan was in Britain, in 1987.
“Gas companies at that time needed to seal their cast iron pipes in advance. Ashimori Industry is a well-known fire hose manufacturer that was applying an inversion process to making fire hoses, and the gas company realized that the same process could be applicable to sealing cast-iron gas pipes underground,” says Azuma. “The fire hoses consist of woven fabric with an extruded resin coating on top of that, and this composite material turns outside in through inversion so that the resin layer becomes the inner surface of the hose. This is precisely the basic structure of Ashimori’s liner, which was named the ‘Hose Lining.’”
Since the early 1980s, Ashimori Industry continually developed its PALTEM methods, all of which are designed with Japan’s high-level of seismic activity in mind, meaning they have the capability to conform to the ground displacements caused by earthquakes.
In all markets and across the four PALTEM methods, Ashimori Industry Co. has installed more than 1,860 miles of liners.
The PALTEM Flow-Ring System is comprised of steel rings, plastic strips and a mortar grout, which attaches the system to the host pipe.
PALTEM Super-HL is strictly for high-pressure water mains and works with pipes that have a working pressure of up to 217 psi. The liner itself is fully structural and has a burst pressure of 725 psi. Liner installation is via inversion method and requires the same equipment already available on the market today.
The liner is comprised of epoxy resin impregnated layers of glass fiber matting as a strengthening layer, and a seamless base hose consisting of polyester woven fabric with extruded resin coating.
Super-HL, Azuma says, has an established track record in Japan where the product was recently used to reline approximately 440 ft (134 m) of 32-in (800-mm) pipe. Maximum installation length for Super-HL is 720 ft and is available for pipe from 8 to 40 in. The liner can negotiate bends of up to 90-degrees.
“The market for water pipeline rehabilitation in North America is not yet mature in comparison to the sewer market,” Azuma says. “PALTEM has a tremendous amount of knowledge and experience in rehabilitating pressure pipes and we believe that our Super-HL will be a good solution for municipalities.”
As for the large diameter sewer renewal market, Ashimori sees the Flow-Ring System as a new solution without a similar competitor.
The Flow-Ring System, developed in 2000, is not a CIPP process, rather a trenchless pipe renewal method that can be installed in any large-size conduit. The new structure is made of steel rings as framework, flexible plastic strips are attached to the steel-ring and the components are bound to the existing wall using a special mortar grout to create a reinforced concrete structure.
Available installation sizes range from 32 to 200 in., depending on the shape of the host pipe and speaking to the latter, Flow-Ring can be used in any shape from circular and rectangular to horseshoe. Because the system is installed onsite, there is no limit to the length of the project.
The steel rings and plastic strips are pre-cut at the factory and arrive at the jobsite ready to install to the host pipe. The steel ring and flexible plastic design allows Flow-Ring system to negotiate curves and level differences inside the host pipe.
“These two products are not yet available in North America, but we are currently in the test marketing stage and plan to enter the market as soon as we confirm that there is a strong need for the products,” Azuma says. The company will have a presence at the 2015 NASTT No-Dig show in Denver.
Mike Kezdi is an assistant editor for Trenchless Technology.
The PALTEM Super-HL cured-in-place pipe relining process is designed for high pressure water mains. Ashimori Industry Co. views the process as a perfect fit for the U.S. water pipeline relining market.