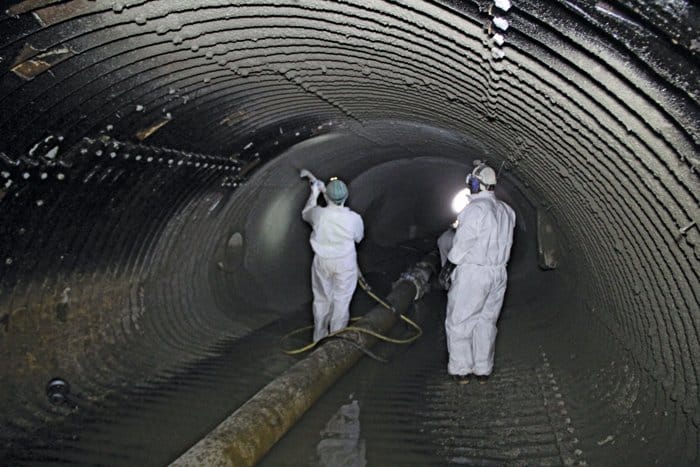
Innovative Geopolymer Rehabilitation Process Proven Effective in Repairing Deteriorating Stormwater Systems
March 5, 2015
The aging infrastructure of nearly every city in the country is crumbling and in dire need of repair. Yet, repairs to the vast network of underground utility systems have largely been ignored.
However, after the Interstate 35 Bridge collapse near downtown Minneapolis in 2007 — an unexpected aboveground visual event that served as a plea of help from an injured belowground infrastructure, city officials began shifting their focus beneath the surface. With the number of rehabilitation projects increasing, rehabilitation contractors are continually searching for new and improved rehabilitation repair solutions.
And to that end, Inland Pipe Rehabilitation (IPR), along with development partner Milliken, developed the proprietary EcoCast Geopolymer Lining System. Introduced in 2010, the EcoCast method has since proven to be an effective, strong and efficient approach because of its many advantages. EcoCast also has the unique distinction of being the first “green” geopolymer structural lining rehabilitation process ever developed.
“EcoCast brings an important fifth unique element to the traditional combination of geopolymer lining process requirements in that it’s the first sustainable approach,” says IPR president and CEO Joseph Cutillo. “The process utilizes the most advanced application equipment with a custom-formulated geopolymer specifically designed for consistent application and long-term strength.”
EcoCast is applied by mechanical pumping, spraying or trowel application that forms a crystalline structural liner effective in halting further water infiltration by rebuilding the surface. The innovative new method also offers higher resistance to acids resulting in greater long-term surface durability. EcoCast is exceptionally resistant to environmental factors like heat and cold, and also cures quickly, providing shortened stormwater by-pass time. It’s is also a highly adaptable approach suitable for a variety of material applications including culverts, manholes, wet wells and more.
Takeoffs and Touchdowns Uninterrupted as Rehabilitation Completed “On Time” Beneath Busy Seattle Airport
At Seattle’s King County International Airport (KCAI), more than a mile of stormwater system situated directly beneath the runways of the nation’s 15th busiest airport had gradually deteriorated and in need of attention. Thorough inspections of the 30-in., 36-in. and 48-in. diameter pipes revealed heavy infiltration and offset joints — some as much as 3 in. in length — due to years of subtle settling and shifting. Due to strict FAA and OSHSA safety guidelines, other rehabilitation approaches were not plausible without shutting down airport runways.
In making the final decision to rehabilitate the pipes, KCIA’s consulting engineering firm ultimately chose EcoCast because of its proven track record of success in similar situations. The quick set-up and tear-down and small construction footprint was especially important for airport and city officials as completing the repairs in a timely fashion — without any takeoff and landing interruptions — was essential.
“EcoCast is the perfect rehabilitation system for this kind of application,” says Rob McCrae, vice president-Western States for IPR. “The flexibility of the EcoCast application process was especially beneficial for the airport project, given FAA takeoff and landing regulations. Once we were set up and began applying the GeoSpray geopolymer lining material, we were able to cease application — as required by the FAA — immediately when alerted of an incoming flight, and get our crews back to the safety zone before the plane landed.”
To minimize these interruptions and maximize the crew’s safety, IPR could not begin operations until after 8 p.m. and had to be cleaned up and off the airfield before 6 a.m. each day. Strict safety protocol had to be followed and all IPR crew received all required safety and driving certifications necessary for the airport’s restricted access guidelines.
Moving steadily from manhole to manhole, EcoCast was applied in a timely manner. The IPR crews were able to thoroughly restore the condition of KCAI’s underground stormwater sewer — quickly and effectively — to a long-term and sustainable condition. In all, 959 lf of 30-in., 3,757 lf of 36-in. and 573 lf of 48-in. CMP of storm sewer were rehabilitated.
“Most of the pipe sections only required one pass to ensure the sections most affected by infiltration were leak-free for the long haul,” McCrae says. “We were faced with some pretty severe weather conditions throughout the project that held us up on occasion. But we successfully completed the project without any airport closures, shutting down a single runway or interrupting the takeoff or touchdown of any flight.”
Stormwater Deterioration and Sinkhole Formation Threatens Residential Neighborhood
After an extended period of severe drought during 2013, the skies above the south Texas town of McAllen opened up. Subsequently, the soil beneath became saturated, inflicting continuous groundwater infiltration on nearly a half-mile side-by-side section (4,420 lf total) of 114-in. stormwater corrugated metal pipes (CMP). No longer able to sustain the long-term exposure to the excessive groundwater flows, the damaged CMP located beneath a residential area of McAllen finally caved — literally. Severe deterioration including several offset joints and partial collapse of the pipes in numerous places had resulted in too much damage and the quickly deteriorating stormwater line had fallen into desperate need of repair.
To complicate matters a sinkhole had formed directly above the afflicted system located in an upscale residential neighborhood that presented additional challenges. Controlling the excessive stormwater flow was critical and required an additional component to the work plan to effectively control flow. A bypass pumping system and series of temporary dams were constructed to halt and divert the continuous groundwater infiltration during the duration of the rehabilitation process. Since the stormwater system was a double barrel, side-by-side configuration, IPR was able to divert water to one pipe while repairing the other and vice versa.
“There were several challenges and extenuating circumstances, including many sections that required extensive prep, patch and sealing work,” says IPR South Central regional manager Collis Parrish. “The collapsed section, more than 400 ft long, was completely removed and replaced with CMP, then lined with EcoCast. Most of the damaged pipe joints were in really bad condition so we applied carbon fiber grid reinforcements to stabilize, strengthen and seal the area between the joints. This step in the process was deemed necessary because of the severely compromised condition of the joints.”
The project took four months to complete, with much of the time spent replacing the collapsed pipe segment, repairing severely damaged sections, and prepping the line for the EcoCast application. All was done without disrupting everyday activities in the subdivision, and for the homes closest to the storm drain’s path, prevented a potential erosion disaster from the underground river that was undermining the foundations.
Toll Road Traffic Remains Uninterrupted During Timely New Jersey Stormwater Rehabilitation Process
The stormwater system situated beneath the heavily traveled Garden State Parkway in New Jersey had finally deteriorated after years of ground settling and shifting. After a section of the aging stormwater infrastructure collapsed, a thorough inspection revealed many sections of the decades-old series of pipe had not been draining properly, leading to flow back-ups and flash flooding during heavy rain events. Tasked with structurally restoring and relining the concrete storm drain system that ranged from 60 to 160 in. in diameter, IPR employed the EcoCast system as the most viable rehabilitation approach.
“[The system] was chosen because of its ease of use and proven performance in the relining aging concrete culverts,” says Andrew Gonnella, business development manager of IPR Northeast. “The fact that it had already been approved and used successfully by nearly 40 Departments of Transportation (DOTs) across the country served as validation by municipal officials that EcoCast was the appropriate repair solution.”
Of particular concern for IPR rehabilitation crews was the amount of silt and sand buildup throughout the drainage system. “The most time-consuming aspect of this project was the cleanup,” says Gonnella. “There was upward of 5 ft of sand, silt and debris in the concrete stormwater network so cleanup was a monumental task. When you add the infiltration and corrosion issues to the situation, it’s no wonder the system was performing so poorly.”
Confined workspace considerations for minimizing traffic disruption was also a factor, so given the minimal amount of equipment needed to apply the EcoCast lining system was beneficial. A 26-in. box truck that houses a mixing hopper, along with a forklift and compressor are the only fixed pieces of equipment present aboveground.
“We were able to repair the culvert section without shutting down any lanes of traffic because the equipment was set up in a safe area alongside of the toll road,” Gonnella said. “I can’t imagine what a mess it would have been if the Toll Road Authority had to shut traffic down during the repair. It is another of the many advantages of the system process.”
“Another component that sets EcoCast apart from other geopolymer lining methods is strength,” says McCrea. “IPR verifies strength on every job by taking several measurement samples. We take product samples and conduct compressive strength tests after one day, 14 days and 28 days for every project. We’ve found that is it’s not unusual for EcoCast to exceed 10,000-psi strength when fully cured, which is well beyond the 8,000-psi industry standards requirement.”
In addition to EcoCast applications, the various rehabilitation approaches offered by IPR exceed more than 1 million ft and CIPP-relines nearly 2 million ft annually. “IPR does not operate on a one-size-fits-all solution mentality,” adds Cutillo. “We are committed to providing a variety of options to our customers and are constantly improving current methods while always looking for innovative new rehabilitation approaches and underground trenchless repair solutions.”
Brian Wing is business development manager at IPR.