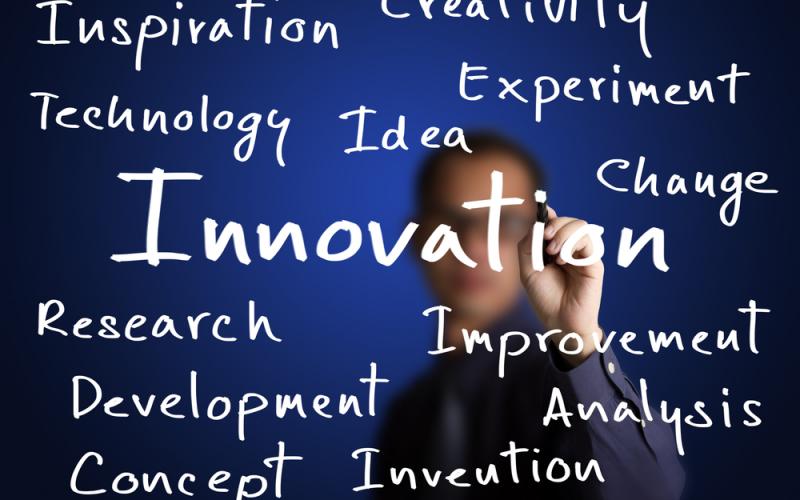
Innovations Drive Industry Growth – Rehab
Condition Assessment Innovations
For this section, we reached out to Piero Salvo, president of GAME Trenchless Consultants, and George Selembo, CEO of InfoSense Inc. Salvo noted that the technology he uses is ultrasound and acoustic, rather than sonar.
What significant developments have occurred in this area?
Salvo: Since the beginning of the applications in North America, we have been able to perform inspections in different situations than those found in the United Kingdom. The condition assessment tools have evolved by becoming more adaptable to our North America environment. The majority of the developments have been with respect to accessing the pipes. Most of these modifications and adaptations have been done by GAME Consultants in order to get the best results from the JD7 technologies we use.
Selembo: The Sewer Line Rapid Assessment Tool (or SL-RAT) was developed from a working relationship between Charlotte Mecklenburg Utilities and the University of North Carolina – Charlotte. The goal was to develop a tool that could quickly assess the blockage condition of a pipe to help prioritize cleaning operations.
The technology works as follows. A speaker (transmitter) is deployed at one manhole and “yells” down the pipe to a microphone (receiver) that is placed at an adjacent manhole. The receiver has a reasonable expectation of how much sound energy should reach the other end, and, based on this, provides a blockage assessment of the pipe. Scores range from 0 to 10, with 0 being completely blocked, and 10 being an open pipe. The entire process takes less than three minutes, there is no flow contact, and results are displayed immediately. The devices also log GPS coordinates which can be downloaded with the results via PC.
What were some of the limitations or challenges with the technology previously?
Salvo: The location of the hydrants and access points in the United Kingdom are different than the ones in North America. In our case, for the small diameter condition assessment tools, we have to modify every single type of hydrant to accommodate the insertion of the tools. For the larger diameter pipes, we have had to adapt to existing situations where in some situations the access point is not at the crown of the pipe, but on the side of the pipe sometimes making the insertion of the tools more difficult.
Selembo: There are a lot of great tools for pipe inspection, but the SL-RAT is the first one that can quickly inspect an entire pipe segment (manhole to manhole) in under three minutes. Prior to this invention, the most effective way to determine if a pipe needed cleaned was to inspect it with CCTV, which is actually more expensive that just cleaning the pipe. It’s important to note that the SL-RAT does not replace CCTV, it helps to prioritize where and when to use more expensive CCTV resources. The SL-RAT is a preliminary assessment or screening tool Our technology provides more information to the system operator when making decisions about where to deploy their CCTV resources for maximum benefit.
What has been the impact of these developments in the market?
Salvo: Over time we have been able to adapt to the North American market and we have become more successful with the inspections we provide.
Selembo: This is a revolutionary concept. This technology has caused municipalities to rethink how cleaning operations should be managed. Significant resources are wasted cleaning pipes that do not actually need cleaned, but prior to the development of the SL-RAT there was not a reliable means of rapidly assessing an entire length of pipe for blockages. The cost of doing acoustic inspections is 1/10th to 1/20th the cost of cleaning or CCTV inspection, so the potential cost savings can be quite dramatic.
How is the technology continuing to evolve?
Salvo: By communicating our limitations and challenges to the manufacturer, they will be able to make certain modifications that will be beneficial to the advancement of the technology.
Selembo: A companion product to the SL-RAT is our Sewer Line Diagnostic OrGanizer (SL-DOG). This is a cloud-based solution that allows the user to manage their acoustic inspection data via a web portal. Another important evolution of this technology is how the SL-RAT is being used by different customers. While most start out as using it as a cleaning prioritization tool, many users are seeing this as a tool that can enable condition-based maintenance as part of an effective asset management program.
Notable projects or products that use the new technology
Salvo: We have been involved in more than 51 different projects in the last two and a half years that have varied from a 4-in. condition assessment to a 48-in. leak detection/condition assessment. We have inspected more than 70,000 ft of live water mains. Of the 70,000 ft, approximately 45,000 are for pipes having a diameter of 12 in. or less and the remaining 25,000 ft have been in large diameter pipes greater than 14 in.
Selembo: There are more than 50 unique customers worldwide making use of the technology, and this is rapidly growing. Some examples are: Charlotte, N.C., was a key development partner and continues to support and use our devices. Augusta, Ga., has three devices and has been using them for over two years now.
CIPP Innovations
UV cure and styrene-free resins are among the latest innovations in the U.S. CIPP market. The technology is also more accessible equating to more contrctors and plumbers adding CIPP to their toolboxes.
For this section, we perspective is given from Gil Carroll, director of business development at Applied Felts; Mike Green, director of business development at Layne Inliner; Lynn Osborn, formerly of Insituform, now NASSCO technical director; and Kaleel Rahaim, business manager of remediation polymers, Interplastic Corp.
What significant developments have occurred in this area?
Carroll: We’ve had a number of recent developments at Applied Felts that include advancements in how we join the seams of our liners to offer both flame bonded and stitched solutions, as well as our in-house liner coating capabilities, offering PU, PP, PE and other polymers. However, our most significant advancement is our renewed ability to add fiberglass reinforcement to our liners. This not only offers the market innovation in gravity sewer CIPP rehabilitation, but also affords us the ability to offer CIPP liners as a solution for pressure pipe applications such as force main sewers and potable water mains.
Green: Layne Inliner has made significant investment over the last couple of years in the ultra-violet (UV) cure marketplace.
Osborn: Improvements include: production through improved procedures, equipment, training, logistics and materials; the use of high-tech robotics for reopening house service laterals and host pipe assessment/preparation; and fiber-reinforced products for large sewers and pressure pipe.
Rahaim: The most innovative new product available to the industry is the introduction of styrene free resins. These offer advantages over styreneated resins from an environmental standpoint. Also new resins have been developed to synergize the benefits of the new tube construction materials containing reinforcements. This allows CIPP processing for more pressure pipe renovation applications.
What were some of the limitations or challenges with the technology previously?
Carroll: With regards to our reinforced liners, previous challenges and limitations revolved around our ability to introduce the added strength of the glass reinforcement into our liners and deliver virtually the same performance as our traditional felt liners.
Green: Previous technology has served the wastewater industry very well. In some regions, concern expressed over environmental safety of styrene odor emissions and cure water discharge.
Osborn: As CIPP for gravity sewers became more of a commodity product, more CIPP installers entered the market. Training field crews to produce a quality product will remain a challenge.
Rahaim: Previously, tubes constructed of polyester felt only had some significant limitations in renovating pressure pipes. CIPP lines using resins containing styrene had some problems with noxious odor emissions and environmentally accepted discharges. UV cured liners had limitations in size and length of application.
What has been the impact of these developments in the market?
Carroll: We have been able to continue to strive to offer our customers new solutions to challenges both new and old. While all of our customers are in the business of CIPP rehabilitation of small and large pipelines, they all have their own unique methods of resin selection, impregnation, installation and many other factors that demand Applied Felts to supply them custom-made liners that maximize their efficiencies throughout the entire CIPP process.
Green: The UV market allows for better encapsulation of styrene and styrene odors, minimizes the need for water use onsite and allows for a downsized equipment footprint.
Osborn: Production improvements, along with competition, have led to lower prices. More products for pressure pipes, both sewer force mains and potable water, will continue to grow that market.
Rahaim: Using reinforcement containing tubes and resins designed for pressure pipes, more work will be available in force main and drinking water applications, effectively doubling the available market.
How is the technology continuing to evolve?
Carroll: I think we are continually in a state of evolution and re-inventing ourselves to keep pace with the ever-changing world of underground infrastructure repair and specifically the CIPP market. Given the developments already covered here, we will continue to fine-tune our products through practical experience and good old-fashioned “getting pipe in the ground.”
Green: By adding fiberglass to the felt tube, it has allowed for CIPP to be utilized in pressure pipe applications. In addition, advancements to UV-light train equipment may allow for an increase in pipe diameters where UV can be used.
Rahaim: More and better resins are being developed and more and better materials of construction for tubes are being engineered. More companies are attempting to get NSF approval for drinking water systems. Quality control and assessment are being evaluated in more detail and are better defined as requirements in bid documents.
Fusible PVC pipe offered underground utility owners an option other than HDPE for completing trenchless applications.
Fusible PVC Innovations
We spoke with Frank Firsching, vice president and general manager, Underground Solutions.
What significant developments have occurred in this area?
When Underground Solutions introduced Fusible PVC pipe in 2004, the diameter range was initially from 4 through 16 in. Since that time, we’ve continued to introduce larger diameter sizes to meet market and application demands. Four years ago we began to actively sell 36-in. Fusible PVC pipe.
Market demand has been growing for larger diameter, thicker-walled, higher-pressure class offerings for fusible, thermoplastic pipe. The HDD industry continues to evolve to more challenging and complex projects, which often involve longer and deeper crossings. In response to these project requirements, thermoplastic pipe offerings must provide higher safe pull force and safe buckling pressure to withstand the installation demands of these projects. Thicker wall, larger diameter plastic pipe offerings are also crucial for non-pressure applications such as casings and gravity sewer applications where there is no inside pressure to help the pipe resist long term, external soil loading. Finally, corrosion concerns are driving many utilities to switch from metallic pipe to plastic pipe, so larger diameter, higher pressure class offerings are increasingly required for many water and wastewater transmission mains.
What were some of the limitations or challenges with the technology previously?
Fused PVC pipe grew out of Underground Solutions’ original Duraliner product line. Duraliner was an expandable, close-fit, PVC structural rehabilitation offering. Duraliner was a PVC pipe that could be slipped inside an existing host pipe and expanded with hot water to provide a close-fit, structural liner. In order to install Duraliner, 40-ft PVC pipe lengths had to be fused together to create a monolithic pipe string that could be inserted into the host pipe prior to expansion
Prior to the introduction of fused PVC pipe, the trenchless industry primarily used steel and HDPE pipe, which facilitated the early growth and development of trenchless applications and the overall trenchless market in gas, water, sewer and electrical conduit. While steel pipe has enjoyed a long history of use in larger diameter water transmission mains, HDPE pipe was a less familiar pipe material to water utilities that predominantly use PVC and ductile iron pipe for water distribution. Water and wastewater utilities were largely unfamiliar with how to connect, repair or work with HDPE pipe, so the introduction of a fused PVC product that allowed them to go trenchless with a pipe material they were familiar with had built-in market appeal.
What has been the impact of these developments in the market?
Once the PVC pipe formulation and thermal butt fusion research was completed and commercialized, it quickly became apparent that fused PVC pipe had trenchless applications beyond just sliplining rehab applications. The technology quickly migrated into pipe bursting, directional drilling and other installation methods. It expanded the universe of trenchless to those who did not use HDPE pipe or wanted an alternative to HDPE pipe. The market now has more choices, which benefits everyone.
Higher-pressure fused PVC pipe offerings allow utilities, engineers and contractors to design longer and deeper crossings. Higher-pressure fused PVC is also increasingly being used for casings and conduits in trenchless installations of high voltage power cables.
How is the technology continuing to evolve?
Underground Solutions is constantly working to enhance the pipe formulation and fusion characteristics of the product.
The water market is continually demanding higher-pressure class offerings and we are in the process of developing new product sizes to meet that market demand. At 36 in., fused PVC pipe now comes in a 200-psi pressure class offering (DR21). Similarly, we are developing a 30-in. DR18 offering that will have a 235 psi pressure rating and a 20-in. DR14 offering that will have a 305-psi pressure rating. These offerings are important not only for the water market, but for the power market for use as casings to house conduits and high voltage power cables. In the power market, it is critical that casings and conduits maintain their dimensionality over time to ensure adequate clearance for high voltage power cables. The higher buckling resistance of these thicker wall pipe offerings helps ensure the casings and conduits can be properly installed by minimizing potential deflection during and after installation.
Notable projects or products that use the new technology
Underground Solutions has been expanding into the federal and military base market with fused PVC at a significant rate. We recently completed a project for NAVFAC in Hawaii where a 3,500 lf HDD installation was completed under Pearl Harbor to install a new 24-in. water line to supply Navy facilities on Ford Island. Fusible PVC pipe was sole-sourced for the project. It’s a very critical water transmission main because it provides potable water and fire water supply to Ford Island, the Pearl Harbor Naval Shipyard and Hickam Air Force Base.
Pipetel Technologies is the leader for robotics used in the inspection of what were once thought to be unpiggable mains.
Gas Industry Innovations
We spoke with past NASTT chairman George Ragula, distribution technology manager for the Public Service Electric & Gas (PSE&G) in New Jersey.
What significant developments have occurred in this area?
The entire area of inspection of gas mains has been revolutionized through the development and recent commercialization of crawler-type cameras for use in inspecting high-pressure gas mains without interruption of service to customers. Such platforms have served as launching points for the development of robotics equipment capable of inspecting unpiggable gas transmission mains that was never before possible using magnetic flux leakage non-destructive testing equipment to ensure the integrity and safety of such lines. These concepts are further being expanded to include maintenance operations from inside the pipe including water removal from low pressure gas mains, internal repair and locating.
The whole CCTV area has just been an unbelievable area for the gas side. As I see it, it has been used as a platform for moving research and development into the direction of internal inspection, maintenance and repair. CCTV systems are now no-blow and do not interrupt service to the customer when passing a service connection. There are options that allow the addition of a hose to the camera and perform dewatering operations without digging another hole in the ground. There are other options that allow you to locate plastic mains without tracer wire while also providing video on internal features (fittings, tee, offsets, etc.)
The CISBOT is a method of repairing multiple cast iron joints under live gas conditions out of a single opening without interrupting customer’s service. Tap into main and you are able to go about 1,200 ft total — 600 ft in two directions — and seal about 80 to 100 joints in a single excavation using CISBOT.
What were some of the limitations or challenges with the technology previously?
CCTV inspection capability under high-pressure live gas conditions was unavailable until the technology was developed. Unpiggable transmission mains could not be inspected internally with conventional pigging equipment, so alternate more costly and less effective conventional technologies were used. The industry continues to trend toward the development of technologies for the inspection, maintenance and repair of gas facilities internally.
A common problem with gas distribution cast iron lines is jute joints drying out and leaking. And joints in such lines are every 12, 16 or 18 ft. With conventional repair methods, you need to excavate over each joint and install external repair sleeves or encapsulation.
Unpiggable transmission mains were identified as a huge need back in 2001 and 2002, there was a big void there, and there was a lot of developmental R&D work started because of that need. The R&D work had its ups and down but reached a point of commercialization about three years ago.
What has been the impact of these developments in the market?
As new and remarkable as these new technologies are, getting the word out to the industry and education continues to be key factors for exposure and promulgating their use. These technologies enhance safety and reliability of the gas infrastructure. They also serve as stepping-stones from which new and improved concepts will ultimately be developed.
How is the technology continuing to evolve?
Like any new technologies, improvements and design enhancements come out of their immediate use as part of the process improvement process. Ruggedness, durability, reliability of operation all come with time as field use and experience provide that critical feedback necessary for the continuous design improvement process. The development of breakthrough technologies will continue and the successful commercialization and implementation of these technologies will continuously be enhanced and improved as they get used in operations.
Through R&D, you get major breakthrough technologies, like unpiggable robotics, and then there are technologies that we use day-in and day-out that always gets improved upon. It may not be looked at as a breakthrough but it is certainly an improvement to the technology, take CCTV advancements for instance.
Looking ahead, there might applications for better leak pinpointing methods, I think there are opportunities for gas service replacement both size-for-size and upsizing and there are a whole slew of ideas on the table that are heading in the whole direction of internal inspection, maintenance and repair.
Notable projects or products that use the new technology
Pipetel is the leader for the robotics used in unpiggable mains. Since it has been commercialized, pipeline robotics work for unpiggable mains has been used approximately 170 times throughout the United States and it continues to expand.
ULC Robotics is a leader in CCTV inspection, dewatering of gas mains and CISBOT for the internal repair of cast iron gas mains. CISBOT has been used extensively by Con Edison and National Grid and PSE&G leads the nation in using CCTV inspection from a gas utility perspective, but there are many more routinely doing it throughout the United States.
LMK’s T-Liner is one innovation that has pushed the lateral market to the forefront of the CIPP market. Both the mainline and lateral sections are formed as a structural cylinder that renews 18 in. and 360 degrees of the mainline and extends up the lateral pipe as one continuous lining.
Lateral Innovations
For this section, we received responses from Jerry D’Hulster, president of Perma-Liner Industries; Larry Kiest, president and CTO of LMK Technologies; and Kim K. Lewis, chairman and CEO of LiquiForce.
What significant developments have occurred in this area?
D’Hulster: Among the developments in lateral lining is the ability to line through a clean-out and lining through multiple bends, steam curing that allows for curing in as little as 40 minutes, scrim reinforced liners that eliminate stretch, 100 percent epoxies with zero percent shrinkage and crews can reinstate tie-ins in small diameter pipes. New technologies also allow for continuous inversions and you can put a push camera inside the liner prior to curing.
Kiest: The ability to renew a sewer lateral using CIPP and achieve water tightness that is comparable to new pipe by the inclusion of preformed gasket seals.
Lewis: Without the use of a front-yard cleanout or access from within the home, crews can prepare and measure from the mainline, removing all debris and roots before an installation. We can now complete lateral installations from large diameter mains, in most instances with no need for bypassing. We have incorporated the use of a patented hydrophilic gasket to top inflow and infiltration.
What were some of the limitations or challenges with the technology previously?
D’Hulster: In colder regions, cure times were longer, felt liners produced significant stretch during inversions, there were limitations when working with bends and crews were unable to line through Tee and Wye type clean-outs.
Kiest: Identifying the correct shape as lateral connections coming of the main consist of varying diameters and opening dimensions. For example, a Tee fitting intersects the main pipe at a 90-degree angle. The same is true for a sanitary Tee fitting; however, it has a completely different shape where the lateral intersects the main pipe. Likewise, a Wye fitting may intersect the main pipe at a 30, 45 or 60-degree angle and each possess a different shape in the opening of the main pipe. The challenge was to identify all of the varying connections and to produce molds for producing gaskets that will effectively provide a watertight seal between the main pipe and the lateral CIPP.
Lewis: There was an increased cost and time required to perform lateral work because a cleanout was required to prepare, measure, install and cure the lateral. Installations required bypass pumping. The difficulties in large main installations due to size limitations did not allow for the completion of the contract.
What has been the impact of these developments in the market?
D’Hulster: As the lateral lining technologies developed, the techniques became more user-friendly, leading to easier installations, increased installations and more installers entering the market. With steam curing advancements, colder regions saw an increase in installations.
Kiest: The impact for gasket sealing technology has advanced the trenchless industry as CIPP is now more comparable to new direct burry pipe than ever before. Today, the success of gasket sealing CIPP has resulted in the issuance of the industry standard ASTM F2561-11 that describes the use of hydrophilic O-rings that form a flexible seal as it relates to cured-in-place pipe for renovation of sewer service lateral pipes. The engineered O-ring gaskets provide for a specific shape, diameter and thickness that are rigorously specified by municipalities and utility owners. The adoption and significant use of preformed engineered CIPP gasket seals has led to a long-term study (10,000 hours) on the physical properties of the CIPP gasket seals including the expansive sealing properties, degradation of the materials, and hardness during hydration/dehydration cycles over a 10,000 hour test period.
Lewis: Projects are now completed in less time and at a reduced cost per lateral. As the technologies improved, push back from homeowners decreased because there was no need to dig for the cleanout close to or on private property. Measurements of the internal diameter and length of the lateral are precise.
How is the technology continuing to evolve?
D’Hulster: Through research and development and ongoing testing, the industry leaders are continuously looking for improvements.
Kiest: The CIPP technology for lateral renovation continues to evolve by the development of new materials and methods that allow for the simultaneous renovation of a main pipe section and multiple lateral pipes from a single piece resin saturated liner assembly. As these technologies continue to advance, municipalities and utility owners are able to exploit the use of trenchless technologies and reap the social benefits, cost reduction and speed of pipe renovation techniques.
Lewis: Equipment improvements allow for higher production rates leading to lower installation costs. New installation processes and liner materials allow for almost no “lost liner installations.”
CCTV companies havv worked dilligently to keep up with customer’s needs for new and improved equipment. This CUES Digital Universal Camera, for instance, is capable of digital side scanning. This photo originally appeared in the September 2013 Issue of Trenchess Technology
CCTV Innovations
For this section, we received responses from R.S. Technical Services Inc.’s Bob Grenier, western regional sales manager. We also received responses from Jake Wells, director of marketing for Envirosight.
What significant developments have occurred in this area?
Grenier: The ability to gather more detailed information from the video inspection and database that information to make decisions for CIP projects.
Wells: The biggest changes are under the hood. The latest generation of inspection crawlers are built on digital platforms that makes them smarter, more scalable and future-ready. For example, certain crawlers can now go online to update their firmware automatically as new features become available. Likewise, they gather and interpret data from a multitude of onboard sensors (pitch, roll, temperature, humidity, pressure) for safer operation and easier troubleshooting. And because they’re based on a network control architecture, these crawlers can accept a wide variety of accessories — including ones that may not even exist yet — helping them adapt to a broader array of applications.
Today’s CCTV systems also support more of the inspection work flow. Not only do they maneuver through pipe and send back video, they digitally record that video to internal memory, allow defect measurement and standards-compliant coding and upload complete inspection data to municipal databases and asset management software.
Finally, the latest generation of CCTV crawlers emphasize day-to-day productivity with design features like tool-free wheel changes and cable connections; extreme portability; and system-wide control via a single touchscreen pendant.
What has been the impact of these developments in the market?
Grenier: The challenges were properly assessing the condition of the pipe in a timely fashion and managing that data to determine the proper form of rehabilitation.
Wells: Digital technology has made crawlers more scalable, which means a single system can adapt to handle a wide range of inspection challenges. In the past, if you wanted to perform small-diameter CCTV, large diameter CCTV, side scanning, lateral launch and laser profiling, you’d need to buy five separate systems. Now, a single system can be accessorized to perform all these functions, and for a much smaller investment.
What were some of the limitations or challenges with the technology previously?
Grenier: The owners of the assets are able to save money by utilizing less expensive technologies to rehabilitate their infrastructure and complete the whole project in less time.
Wells: Systems without onboard intelligence and digital scalability simply cannot adapt to future needs; you’re stuck with the capabilities of the system you buy, and often those capabilities exclude even basic features like concurrent control.
Because pre-digital systems lack onboard recording and defect coding, lots of support equipment is required: a separate CCU, a PC with software, a video recorder, etc. Factor into this a heavy, bulky cable on an oversized reel, and basic inspection requires a large box truck and an expensive generator.
By contrast, modern digital systems are comprised of just a crawler, compact cable reel and handheld controls, which means they can be adapted to practically any vehicle and power source for inspection in most any setting, even easements and alleys.
How is the technology continuing to evolve?
Grenier: Engineers are getting more software to analyze the CCTV inspection data to help them choose the proper form of rehabilitation.
Wells: The pace of innovation in consumer electronics continues to benefit our industry. For example, HD video, while not essential for up-close inspection tools like crawlers and push cameras, is helping extract more visual information from look-see devices like zoom cameras and video nozzles, thereby expanding their role in pipe assessment. The miniaturization of digital processing has allowed onboard recording at the point of inspection, rather than requiring video transmission over long distances — this has made video nozzles a success, whereas traditional jetter cameras suffered due to costly, unreliable signal connections. Wi-Fi is evolving to replace cable in zoom camera applications, helping to streamline setup and improve safety around the manhole.
Notable projects or products that use the new technology.
Grenier: R.S. Technical Services Inc. continues to advance its Single Conductor technology with side scanning cameras, lazar and sonar profilers and CIPP reinstatement tool controllers all that interface with the industry’s leading data collection software.
Wells: Our ROVVER X was the first inspection crawler to fully embrace the digital paradigm described here. The onboard reporting it offers is also available in our VeriSight Pro push camera. Our JetScan video nozzle implements onboard recording of HD footage, giving jetter operators valuable intelligence where once they worked blind.
Mike Kezdi is assistant editor of Trenchless Technology.