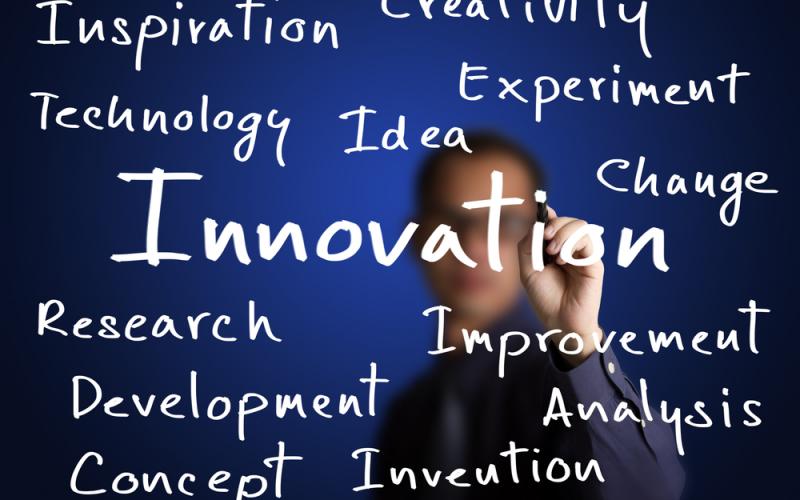
Innovations Drive Industry Growth – New Installation
Self-Contained Horizontal Directional Drill Rigs
When discussing the top innovations, Trenchless Technology publisher Bernie Krzys made note of self-contained HDD rigs. “In my opinion, one of these top really cool innovations was the introduction of the self-contained rigs that we have today. Drill rig, drill pipe and power supply are all contained in one unit,” he wrote.
In his January 2014 column, Krzys highlighted the advancements of HDD Self-Contained Rigs. For this section, we reached out to Richard Levings, director of product management for American Augers; Seth Matthesen, HDD product manager at Ditch Witch; and Tod Michael, product manager of trenchless core products at Vermeer.
What significant developments have occurred in this area?
Levings: The use of rack-and-pinion thrust systems and vise type wrenching system. American Augers recognised and adopted this very early in the development phase of the HDD industry.
Matthesen: The implementation of pipe-handling systems, which have been updated with automated features. These advances help reduce labor and operator contact with drill pipe.
Michael: Our thrust and rotation speeds in the 1990s would have been under half what they are capable of doing today. When you talk about thrust speed or carriage speed, it doesn’t necessarily mean you’re going to drill any faster, but they have helped make the equipment more productive and really aided contractors in getting higher footage numbers compared with 10 years ago and especially 20 years ago. Another item is improved operator comfort with both ergonomics and the introduction of cabs back in the early part of the 2000s.
What were some of the limitations or challenges with the technology previously?
Levings: Most early thrust systems utilized a chain system to propel the rotation carriage. This worked well but proved to be limiting in how force was applied to the thrust carriage and service life of the thrust components. As a result, chain stretch and breakage occurred regularly resulting in more down time than desired. Rack-and-pinion systems solve these issues and add excellent service life.
Breakout and make up of drill pipe was done in many different ways in the earliest days of HDD, especially in the smaller utility systems. These early systems proved unreliable and often required regular maintenance to keep them working. The vise wrenches have changed the effectiveness of the pipe wrenching system making HDD systems more effective.
Matthesen: Before pipe-handling systems became available, operators needed an additional person to help load and unload drill pipe. New systems require only one worker to lift drill stem and transfer pipe into a drilling rig, reducing worker exposure to potential injury in a pipe yard or on a jobsite.
Michael: As far as the operator comfort piece, what we’ve seen is the expansion of winter drilling in cold weather, where before contractors pretty much shut drills down in the winter and came back after the spring thaw. At the other extreme, crews are working in 110 degrees and out in the sun. We’ve tried to make it more bearable sitting on a machine in those conditions.
What has been the impact of these developments in the market?
Levings: They have become industry standards that set the pace for industry adoption of HDD as the primary method for installing underground utilities and pipelines.
Michael: Our goal at Vermeer always is to give real productivity advantages to the customer, to lower their cost of operation and to help them be more profitable. The industry really hasn’t evolved in giving contractors more money per foot. Over the last 10 to 15 years, the price per foot, especially in the communication market, has dropped. So, we want to help contractors be productive so they can stay profitable.
Some other innovations I haven’t mentioned yet that are part of that effort include giving contractors the ability to do some self-diagnostics on the controls and hydraulic circuits from our display screens, which used to be all analog and today are digital. It gives them the ability to provide more information to the operator.
How is the technology continuing to evolve?
Matthesen: The increasing use of automation has improved speed, and reduced operator error in the process of making and breaking drill pipe.
Michael: For Vermeer, one focus is on expanding upon electronics and providing even more information about the machine. This is not only information that is available at the operator’s station, but also telematics and GPS systems that provide that same information to an office employee or the owner.
People who are not at the jobsite can see what’s going on with a machine as it happens, rather than after it gets to the shop and, if there’s an issue that needs resolved, trying to figure it out before they have to go out the next day.
It helps them service a machine, and not only with their own service personnel, but also by taking advantage of the service expertise in the Vermeer dealer network. That gives them a better opportunity to fix it the first time, rather than go out and diagnose the problem and then have to come back for a part.
HDD Intersects
What significant developments have occurred in this area?
Billig: The key development that has facilitated the introduction of HDD intersects as a viable technology has been the possibility of downhole ranging. This is where the two drilling assemblies being used to perform the intersect are able to physically measure their separation downhole instead of relying on measurements from the surface or calculations from the respective entry points. Ranging downhole over short distances (typically no larger than a couple of meters) gives a high accuracy location because of this and the distance from any potential sources of interference. The two main ranging technologies used are based on magnetic sources — the Axial Magnet (generally for use with jetting assemblies with a range of up to approximately 6 m) — and the Rotating Magnet (which uses the rotation of a mud motor to spin a magnet sub creating an alternating magnetic field).
Halderman: Without any doubt the driving innovations for increased accuracy and lengths in HDD have been the introduction of TruTrack in 1989, the addition of ParaTrack in 1999, and now the initiation of the first practical gyro in 2007.
What were some of the limitations or challenges with the technology previously?
Billig: Prior to downhole ranging, the risks of interference and location uncertainty were considerable when attempting intersects with only surface ranging. Imagine — if all your surface information tells you that you have hit the target, but you have not, where do you steer to now?
Operational risk. Initially, with few intersect projects to refer to a lack of experience and understanding of correct procedures and limitations of tooling (eg drillpipe) and formation led to an increased perception of risk in the intersect procedure. With more previous project examples to examine, finally clients and engineering companies are more comfortable considering a project that involves intersect technology.
Halderman: Prior to 1989 we were limited to magnetic steering, which was often affected by nearby magnetic fields or large masses of steel — electric railroads, electric transmission lines, steel bridges, cathodically protected steel pipelines to mention just a few. Consequently, pinpoint accuracy was impossible without plain luck. This did not inspire confidence in owners.
What has been the impact of these developments in the market?
Billig: Increased length. The longest pilot hole completed to date stands at 3,900 m. Longer projects are being considered, you can expect to see projects at 5 km and greater coming to market in the coming 12 months. Long reach projects (more than 2,000 m) are no longer seen as high risk. Intersects can now be proposed confidently as a contingency should ground conditions complicate a single shot drilling.
Increasingly Casing to Casing projects over shorter distances are using intersect technology to reduce the risk of not entering pre-installed exit casing, or to ensure that the pilot hole accurately enters the centre of large diameter casing.
Halderman: The demonstration of consistent accuracy has given owners and their engineers the confidence to plan HDDs that would have been too risky before. Drilling multiple lines closely spaced inside narrow ROWs; pinpointing targets in tight areas; drilling under and parallel to electric railroad lines; are some examples of new designs. Intersecting capability has nearly doubled the distances for new HDD concepts.
How is the technology continuing to evolve?
Billig: At bit inclination is being introduced for motor drilling to give more accurate steering/dog leg control.
A large field beacon is being developed for increased accuracy when drilling under long blind sections which when applied to intersect projects this can reduce the separation between pilot holes.
Halderman: HDD was developed 40 years ago simply to cross under a river. Now HDD is used to cross under and drill around any conceivable obstacle. New uses are being designed every day. Need, confidence and capability are the keys. As a result creative designers will rise to the occasion as they always have.
Notable projects or products that use the new technology.
Halderman: An accurate 3-mile drill is not out of the question now! It’s not difficult to imagine the applications.
Location
In July, Krzys tackled locating and tracking and oil line navigation systems. For this issue, we separated the two selections into separate sections. For locating and tracking we reached out to John Bieberdorf, Subsite HDD product manager and Siggi Finnsson, product manager at Digital Control Inc. (DCI)
What significant developments have occurred in this area?
Bieberdorf: Excluding the wireline systems, (Krzys mentioned in his column) the walkover guidance systems ability to project the exit point. Call this drill to or remote guidance. This type of guidance has drastically changed in the last 10 years. The maximum communication distance between the locator and drill head establishes the distance limitation or how far ahead the locator can be set in front of the drill head.
In 2005, Ditch Witch introduced the 8500 system that doubled the distance of previous systems by giving the ability to not only drill to the locator, but also drill away an equal distance without moving the locator. In 2013, Ditch Witch introduced the TK guidance system that increased the locator to drill head communication distance by 40 percent, thus achieving the same drill to distance as the 8500 system.
Finnsson: The ability to deal with interference, which means being able to drill through areas where other interfering signals are present, continues to be an area where advancements have been made. DCI has introduced XRange mode, which is a transmitter mode that can significantly increase the range of the data signal (roll/pitch) in high interference areas. A new extended range version of the transmitter (19 in. in length) allows for an unprecedented data (roll/pitch) range of 200 ft. These transmitters also monitor downhole fluid pressure monitoring and depth to a range of 100 ft.
In 2013, Subsite introduced the TK guidance system that increased the locator to drill head communication distance by 40 percent.
What were some of the limitations or challenges with the technology previously?
Bieberdorf: The limitations to a remote guidance system is the amount of power that can be generated by a battery-powered transmitter in the drill head, which relates to the maximum communication distance.
Finnsson: Projects at greater depths or in areas of high active interference would typically require cable transmitters or a wireline guidance system, which meant greater expense and duration. A non-wireline option like XRange would make these types of projects less complex, less expensive and easier to complete.
What has been the impact of these developments in the market?
Bieberdorf: Ability to cross roads, ditches and other obstacles when walkover guidance is dangerous or not possible. (The technology) changes the need to have as much knowledge and experience in the walkover guidance operator.
Finnsson: This is a recent development but we are seeing project completions that would typically have required more expensive equipment. In particular, the walkover fluid pressure monitoring capability, which is increasingly being required.
How is the technology continuing to evolve?
Bieberdorf: Alternate power sources that deliver more power for the downhole transmitter can potentially increase the communication distance.
Finnsson: The challenge is to continually improve performance, reliability and user experience. In the case of fluid pressure monitoring, the newly released DigiTrak Aurora remote display allows the rig operator to monitor fluid pressure on a real-time graph where pressure warning levels are clearly indicated. The warning levels are set by the rig operator based on each projects requirements. This allows for easier control of annular drilling fluid pressures since potential corrective action can be taken.
Notable projects or products that use the new technology.
Finnsson: Klondike Directional Drilling recently completed a 700-m (2,300-ft) bore to a maximum depth of 25 m (82 ft.) where fluid pressure monitoring was required for the entire bore. An installation of this scope would typically require a wireline system but with the DigiTrak 19 in. fluid pressure transmitter, the pilot bore was completed within two days with a drill time of only nine hours. Pressure and other locating data was consistent and the DataLog file (data logging) indicates that the bore followed the plan closely. Fluid pressure readings were fairly constant and ranged between 80 to 120 psi with a static pressure of 60 to 70 psi at maximum depth. The XRange (extended data range) capability of the transmitter was not needed as the readings in standard mode were more than sufficient for accurate locating.
Navigation
Horizontal Technology, Inc.’s HDD Steering Class with above ground training coils. The ability to use a DC current and create an artificial magnetic field to verify the precise location of the magnetic steering tool was the catalyst for the unbelievable growth in HDD.
For this section we received responses from John English, owner and president of Horizontal Technology Inc. and Eric Skonberg, P.E., of Trenchless Engineering Corp.
What significant developments have occurred in this area?
English: The most important factor is knowing precisely where the drill bit, thus the drill path, is located. With all the “new technology” DC tracking remains the most accurate HDD steering method, by far. While there have been improvements, there have been no advances in the ability to verify the bit’s underground location since the advent of tru-track. The ability to use a DC current and create an artificial magnetic field to verify the precise location of the magnetic steering tool was the catalyst for the unbelievable growth in HDD. Knowing the location of the bit is critical and documenting the drill paths location was mandatory. To date, nothing is as accurate or as easy as setting a temporary coil on the surface. Our software is much better and today’s new high-resolution magnetic steering tool is even more accurate and at greater depths.
There is too much bad information and no way to separate fact from fiction. People making the decisions don’t know the difference between one method or another. They don’t know how they work, yet they think they are specifying the latest and greatest. Today, the “HDD experts” don’t know the difference between DC tracking (by far the most accurate) AC tracking or a gyro.
Skonberg: The Paratrack magnetic wireline tool with pilot hole intersect capability was introduced in the United States in 2003. This allowed HDD rigs from each side of the crossing to drill a pilot hole and meet in the middle. Other magnetic wireline tools have since provided similar capabilities.
SlimDril introduced the fiber-optic gyro in the United States. This tool does not depend on the Earth’s magnetic field for guidance. The tool is astoundingly accurate, and is beneficial in applications where magnetic interference may be high and where secondary surface locating systems may not be practical.
What were some of the limitations or challenges with the technology previously?
English: Limitations are now being placed by the increased number of people on a jobsite telling others what they can’t do. The technology to know the precise location of the drill bit is being ignored, by the unknowledgeable “experts,” often demanding contractors use varying technologies, even if it is inferior. In fact, contractors are required to pay more for less accurate methods. There are so many HDD experts and consultants that bad methods are becoming specified procedures. There are more people on a site who tell workers what to do and how to do it (driving up costs) than there are people doing the job. Ignorance has become king and authority has become a form of currency. DC tracking is so accurate, I have seen contractors required to pull back and redirect a drill because the inclination is off the equivalent of the thickness of a dime yet a complete drill can be installed using a gyro method where they have no clue where they are until the bit exits the ground, and that’s acceptable.
Skonberg: Both tools still require the use of a wireline (a wire inside the drill pipe from the tool to the surface). The wireline connections are cumbersome and time consuming.
What has been the impact of these developments in the market?
Skonberg: Pilot holes, and therefore HDD installations, were limited to a drilled length of 5,000 to 7,000 ft. This was the distance the HDD contractor could “push on a rope.” With the intersect technology, HDD drilled lengths are now doubling.
The fiber-optic gyro tool is very accurate and not influenced by magnetic anomalies. Where great accuracy is necessary and where surface locating coils are not practical, the fiber optic gyro provides very good results. In areas of high magnetic interference (steel piles, bridges, other pipelines), the fiber-optic gyro can provide accurate locating data and ensure a safe installation.
How is the technology continuing to evolve?
English: So far, it has evolved in the wrong direction. Be skeptical, new technology isn’t always better and often isn’t even new. Proven methods are the key to success, not shortcuts. Why would someone specify a less accurate steering method? Only one reason, ignorance. Yet it happens every day. Ask yourself, what are the qualifications to become an HDD consultant?
Notable projects or products that use the new technology.
English: New technology is the hiding place of the HDD incompetent. They don’t know proven methods and practices so they can only discuss new technology. Attend any HDD show and there are fewer than 1 percent of people who can discuss HDD practices, the rest (HDD experts all) will all be asking about and talking about new technology, while the best contractors are out installing lines using proven HDD methods.
Curved Microtunneling
On May 19, 2010, Northeast Remsco Construction successfully completed a planned, curved microtunnel in Hartford, Conn., on behalf of The Metropolitan District Commission follow the design of AECOM.
In October 2014, Krzys tackled curved microtunneling and for this section we received responses from Rory Ball, senior project manager at Hatch Mott MacDonald and Richard Palmer, tunneling manager for Northeast Remsco Construction Inc.
What significant developments have occurred in this area?
Ball: Outside of North America, the world has been completing curved drives for a long time. Although we are still playing catch up, we are way ahead of where we were even five years ago. What has happened recently has been a drastic leap forward for us in terms of the kind of projects contractors and owners are willing to do. However, this is just the beginning of where we will go.
Recently, contractors have been more willing to bring forward value engineering proposals on their own that incorporate curves and offer savings in terms of the impact to the public or in terms of saving time and money. This has been the huge step for the industry because most owners have not been willing to go out to bid with curves in the design drawings. Soon we will get to a point where owners are willing to have curved drives on their actual bid sets.
Palmer: The most significant development to me is the growing acceptance within the Engineering Community that curved microtunneling is a viable option in the North American marketplace. This has been reinforced by the inclusion of a curved microtunneling section in the 2015 edition of the ASCE Microtunneling Standards (ASCE 36-15), which fairly discusses the benefits of curved microtunneling, as well as the associated design and construction challenges.
What were some of the limitations or challenges with the technology previously?
Ball: Historically, owners have not wanted to step forward and take on the risk of bidding curved alignments. It took one contractor stepping forward with a value engineering proposal and taking on all of the risk himself on that drive. Since then, the majority of curves have come from the contractors who have had to present proposals in a way to the owners that made sense in terms of the benefits and management of each of the risks.
In terms of engineers and planners, many do not have the experience and understanding in design and construction to address risks in terms of curved microtunneling. The contractors have taken the lead in pushing the industry for not only the owners, but in challenging the engineers to step up their expertise.
A major challenge is that pipes available to North American contractors need to be able to go through the curves properly, and maintain both their structural and joint integrity.
Palmer: The principal challenge was to overcome the liability concerns associated with curved microtunneling. U.S. engineering firms were reluctant to design a project that required the use of a “never been done in the U.S.” microtunneling technique. In order to help break down that barrier, in 2010 Northeast Remsco proposed a curved microtunneling alternative on a project in Hartford, Conn., in lieu of a straight microtunnel reach and an open cut reach. Fortunately, the designer engineer and the owner were receptive to the idea and collaborated on the final version of that curved microtunnel. It is interesting to note that the change order authorizing the curved microtunnel included language that shifted all of the risk to the contractor; shedding the risk was paramount to breaking down the barrier.
What has been the impact of these developments in the market?
Ball: The major impact has been that more owners are willing to talk about curved microtunneling. Now that they are seeing projects completed successfully in North America, they are engaged in the discussion and eager to learn more. They are more receptive to comparing the advantages and risks and see if it makes sense to do a curve.
As the infrastructure inevitably becomes denser — being able to reduce the number of shafts, reduce shaft depths, provide flexibility along the right of way or that alignment and avoiding obstacles, sensitive zones or utility crossings — more significant direct and indirect cost savings will be realized.
In terms of pipe quality, we have seen a partnering approach between contractors and manufacturers to step up the pipe quality, tighten up tolerances and provide more joint configuration options.
Palmer: Curved microtunnels are now being designed into projects from the beginning rather than being proposals after the fact made by the microtunneling contractors. Even with the additional challenges associated with curved microtunneling, when used appropriately it can solve alignment problems, reduce the impact on neighborhoods and lower project costs.
How is the technology continuing to evolve?
Ball: Advances in machinery as well as the ancillary support systems that work with the machines are improving. In terms of machines themselves, we have advances like the Direct Pipe system; it’s an advancement that is relatively new almost worldwide that offers a great option for the engineering and construction community. It is getting more and more use with contractors having bought the machines for their own use in North America.
Some MTBMs now have circumferential lubrication so the rear of the machine can actually inject lubrication on its entire circumference as you mine. This is a great improvement for both long distance and curved drives to maintain the integrity of the annulus.
Other advances include better metallurgy of wearable components that support curved and longer drives, better real time data recording capabilities and higher efficiency separation plants. In terms of data recording, contractors and engineers must learn to use the available metrics on a daily basis to pro-actively address risk on all microtunnel drives.
Palmer: Several supporting technologies have already been on the market for a number of years outside the United States. These include: gyroscopic and laser theodolite guidance systems, enhanced auto-lubrication systems, and innovative packing systems for load transfer across deflected pipe joints. I believe the near term evolution of curved microtunneling in the United States will be our effort to “catch-up” by embracing these technologies.
Notable projects or products that use the new technology.
Ball: Much of the most advanced usage of curved tunnelling is happening in Canada under Ward & Burke. They are successfully completing longer drives and more complex curves like the Keswick WPCP Effluent Outfall Project, which had both a horizontal and vertical curve.
The Santa Ana River Interceptor (SARI) Project utilized Jackcontrol’s hydraulic joint and joint monitoring system for the first time in North America. Fowler, the microtunnel subcontractor, utilized this system to provide real-time feedback on the joint loading and rotation. This option provided comfort to the owner and engineer as a risk mitigation, thereby helping the value engineering proposal to be approved.
Palmer: The Homestead Avenue Interceptor Extension in Hartford, Connecticut, included the installation of 3,350 lf of 72-in. PVC-lined RCP via microtunneling through mixed ground and varied clays in five drives. The contractor proposed extending the final 310 lf microtunnel and additional 290 lf and incorporating a curve to accommodate a planned 4 degree horizontal deflection. The resultant drive was 600 lf comprised of a 200-ft tangent followed by a 200-ft curve on a 1,359-ft radius followed by a 200-ft tangent. The contractor used 10-ft pipe lengths and limited the joint deflection to 0.25 degrees in order to use standard 3/4-in. plywood joint packers. A VMT laser theodolite system was used for the curved guidance, and an auto-lubrication system to reduce jacking loads.
Ground Improvement
Brian Fulcher, Kenny Construction, discusses the intricate pre-excavation grouting program associated with Arrowhead Tunnels in Southern California during the 2014 the second annual Ground Improvement Short Course.
For ground improvement, we turned to Hayward Baker senior vice president of engineering George K. Burke and Dr. Raymond Henn, chief consultant for Brierley Associates.
What significant developments have occurred in this area?
Burke: Ground improvement technologies have matured…applications are many and experience grows. Product perception is also better, and constructability and logistics are better understood. This is certainly the case with jet grouting, soil mixing and chemical grouting.
Henn: The increased use of ultrafine/microfine cement for grouting of soil and rock.
What were some of the limitations or challenges with the technology previously?
Burke: The product perception and the verification requirements have often been unrealistic, causing extreme conservatism, very high construction risk and qualifications. Understanding the differences would make for a lower cost, completed faster, with a product that could meet the design intent.
Henn: Ultrafine/microfine cement costs between three to five times more than the cost of Portland cement.
What has been the impact of these developments in the market?
Burke: More applications and reduced risk and costs.
Henn: Being able to use common grouting equipment for ultrafine/microfine grouting, the type used to mix and pump Portland cement base grout, has allowed contractors to self-perform water cutoff grouting with their own on-site forces.
How is the technology continuing to evolve?
Burke: All of these technologies continue to adopt processes and equipment that improve efficiency while maintaining the minimum requirements of the product.
Henn: Suppliers are coming up with smaller and smaller sized cement particles for their ultrafine/microfine products. Also, pumice-based ultrafine (manufactured in the United States) is getting a bigger and bigger market share.
Notable projects or products that use the new technology.
Henn: The Arrowhead Tunnel Project – these two tunnels which are located in California each measure 12 ft in diameter and have a combined length of 9.6 miles. These tunnels were excavated using two hybrid tunnel boring machines (TBMs) with the West tunnel being the most difficult, taking over four years to bore through the mountain.
Slurry Handling
Packaged mud recycling systems and linear shakers are two of the latest advancements in the world of slurry handling.
Responding to our slurry handling questions were Raymond Pietramale, marketing manager for Kemtron Separation Technologies and Trevor Young, president of Tulsa Rig Iron.
What significant developments have occurred in this area?
Pietramale: What we’ve seen over the past 10 years are the packaged mud recycling systems — the trailer-mounted units that contain all-in-one processing equipment. It has the pumps, it has the shale shaker on it, the power pack, the mud hopper for mixing in new bentonite, all of the capabilities that you need in one unit.
We’ve seen innovation going from small 65-gallon-per-minute (gpm) units all the way up to 1,500-gpm units. The advancement has been in refining the systems and making them as compact as possible with the most amount of capacity and trying to handle everything from the small water well driller to the big directional driller that are doing some of these record-breaking bore lengths.
As package refinement continues, a lot more companies are making the packaged systems.
Young: Although no major ground-breaking developments have occurred, probably the most significant advancement has been the move to linear motion shakers away from elliptical or orbital motion shakers. Most advancements have been refinements to the technology to allow better performance, longevity, and operator ease.
What were some of the limitations or challenges with the technology previously?
Pietramale: We were one of the first companies to create a packaged mud system. Before that, we had a lot of people who knew about mud recycling and the benefits, and they would make their own systems by piecing here and there. They may have had it on a trailer but it was someone else’s shaker, someone else’s hydrocyclone manifolds, someone else’s power pack. It was all being individually sourced out and butchered from certain elements.
Limitations included education of the contractor. If you go back in the old days, it was a dump and run scenario. They were creating giant reservoir pits, hauling off the slurry, and paying to dispose of it somewhere else. They were not realizing the cost benefits of reusing their drilling fluid or reducing the amount of waste haul off.
Young: When using the old elliptical or orbital type shakers, you could not run a very fine screen and obtain a dry solids discharge.
What has been the impact of these developments in the market?
Pietramale: We’ve educated contractors on ease of operation and highlighted the cost savings. The systems, if properly maintained, last over 10 to 15 years. The system becomes a profit center after the first four years of use. They really understand the benefits and as the drilling rigs have gotten bigger, they really have to do something with all of that fluid.
Microtunnelling, water well installation, everyone across that spectrum is embracing mud recycling. If you want to go further with your recycling you can add a centrifuge. A typical mud recycling systems gets you about 25 microns, if you add a centrifuge, you can actually remove all of the mud and end up at 0 micron and end up with what you call white water. A zero discharge, closed loop environment, where the dirt is almost clean enough to refarm on the land and reduces haul off.
Young: Every Tulsa Rig Iron unit uses linear motion shaker technology When using linear motion shakers, you can run much finer screen mesh’s and get a dry solids discharge. This allows for a cleaner, more environmental friendly jobsite, less solids haul off, and a cleaner mud.
How is the technology continuing to evolve?
Pietramale: The real improvements we will see are in the control panel technology and remote operation will play a big factor. Kemtron recently unveiled a system with a touch screen control panel and it has wifi capability. Operating from an iPad, iPhone or laptop from a drillers cabin reduces labor costs.
The linear motion shaker that sits on the unit has been the biggest evolvement. The oil and gas industry has used shale shakers since the 1940s. As time has gone by, there have been small incremental adjustments in shaker design, we brought a brand new shaker design to market last year on the oil and gas side, and we implemented it over to our HDD line. The shaker is the most important piece on the unit. The tank is a tank, the pump is a pump, what has seen the most change is the way you arrange, orientate and manufacture your shakers.
Young: Continued refinements that will allow for the cleanest possible mud, which will protect the mud pumps used in the drilling process.
Notable projects or products that use the new technology.
Pietramale: The Kemtron Technologies Tango 600HD2 is the first mud recycling systems that features the touch screen control panel with Wi-Fi capabilities.
Mike Kezdi is assistant editor of Trenchless Technology.