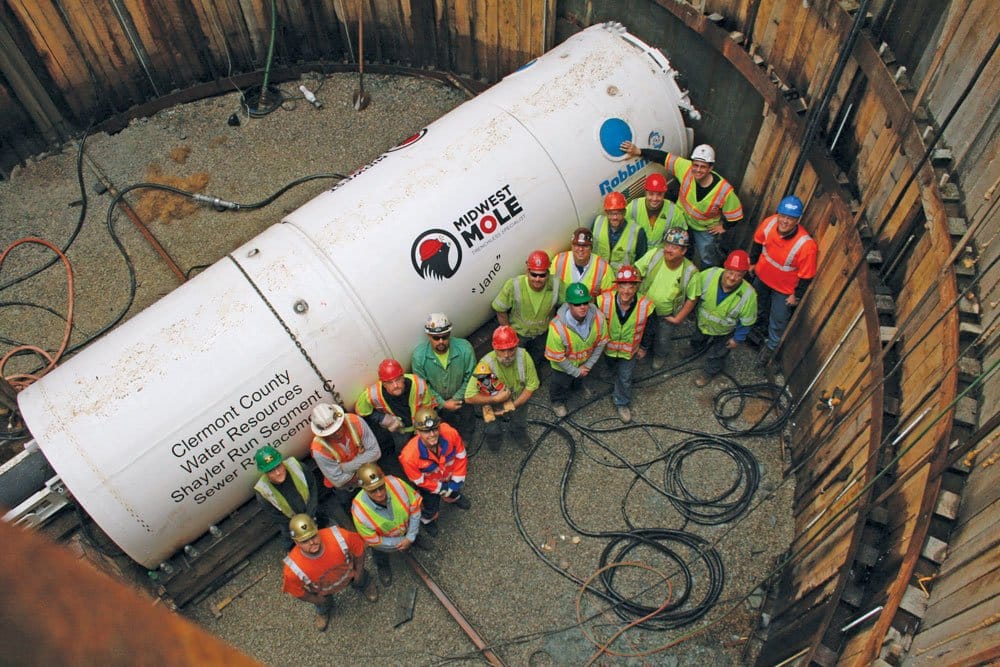
Small but Mighty: Midwest Mole Installs 520-ft Sanitary Sewer Line through Various Ground Conditions
In scenic Bloomington, Indiana, contractor Midwest Mole put its 36-in. Robbins Small Boring Unit (SBU) to work. The machine, which is owned by the trenchless technology company, bored a 520-ft crossing as part of the I-69 Section 5 Project owned by the Indiana Department of Transportation (INDOT). The project, as a whole, spans 21 miles and reaches from the south side of Bloomington to the south side of Martinsville. “We have completed several different aspects on this project,” said Midwest Mole project manager Brian Brown. “We have installed over 6,000 ft of 6-in. high-density polyethylene (HDPE) pipe for underdrain outlets, over 12,000 ft of four 1-in. conduits for IU Fiber, over 10,000 ft of storm drains, and finally water and sewer line relocations, as well.” On this particular crossing, Midwest Mole was contracted to install a sanitary sewer line. The SBU, fitted with a hard rock head, was launched March 7, 2017, in a 14-ft wide by 40-ft long pit. “We upsized the casing to 36 in., which allowed for additional tolerances,” said Brown. Based on anticipated ground conditions, the crew utilized an Axis guiding system for directional purposes and a 60-in. auger boring machine for required thrust and torque. The crew had to be mindful of a gas line located near the receiving pit, which was exposed during crossing. “Because we had to be very close to a gas main, we used the Vermeer Axis Machine to guide the Robbins SBU. Using the guidance system tubes ensured better production rates,” added Brown. RELATED: Navigating Under New York With a Remote Controlled SBU
Powering Through
Bloomington is part of Monroe County, which is known for its limestone quarries. Due to the large volume of limestone in the area, sedimentary rock was expected. Within the first 200 to 300 ft of boring, the crew surprisingly hit pockets of clay and significant water inflows. “We quickly experienced flowing water,” said Brown, “which required us to use a vacuum truck to remove the spoil in the pit. Once we got out of the water, we began hitting pockets of clay.” The differing conditions put additional wear on the machine, but the SBU still made it to the receiving pit on grade, which was proposed at .87 percent. The final carrier pipe was 16-in. ductile iron pipe. “The changes in ground conditions made this challenging,” added Brown, “along with the utilities we had to deal with. While the ground conditions weren’t as expected, the crew was still able to maneuver the machine and complete the job.” The crossing was completed on April 7, 2017. The durable SBU used on this project is just one of many Robbins machines in Midwest Mole’s inventory. “Midwest Mole has had a long relationship with Robbins through the years,” said company CEO Dan Liotti. “Currently we own five different sizes of SBUs as well as a 54-in. Rockhead. With the use of the Robbins SBUs we have been able to complete projects that were nearly impossible to complete in the past.”
Midwest Mole used its 36-in. diameter Robbins Small Boring Unit (SBU-A), a proven design capable of boring crossings in mixed ground or rock up to 25,000 psi UCS.
How an SBU Works
The system utilized in Indiana featured a 36-in. Small Boring Unit, also known as an SBU-A, and a 60-in. auger boring machine. An SBU-A, like the one used in Bloomington, is a small diameter cutterhead and thrust bearing assembly that can range from 24 to 72 in. in diameter and can be used with any auger boring machine from 36 to 72 in. Depending on the ground conditions, an SBU can be fitted with a hard rock or a mixed ground cutterhead. A mixed ground cutterhead can feature a combination of single disc cutters or two-row tungsten carbide insert cutters and carbide cutter bits. Cutters range in size from 6.5 to 9.5 to 11.5 in. RELATED: Crossing the Des Plaines River A project generally begins with the excavation of a launch pit, then a concrete or gravel pad is installed on the floor of the pit, based on the project’s line and grade requirements. Track is laid on the floor of the pit, which is then following by the auger boring machine. Before the machine is launched, crews weld the SBU to a lead steel casing. The casing is a pipe that will allow the transfer of the highest thrust loads to the cutting face and will also provide a stable environment for the crew to lay the final pipe after excavation is completed. The SBU and lead casing are then set into place on the track and attached to the auger. Within the casing is a full-faced auger, which is used for muck removal once boring begins. After assembly is complete, the machine can begin excavation. The auger boring machine provides forward thrust to the boring unit through the casing, while torque is applied through the full-face auger. In hard rock, the face of the machine moves in concentric circles; as the force on the rock increases, the rock beneath each cutter is crushed and fractured. This method is known as kerf cutting. Large openings on the face of the SBU, called muck scrapers, are designed to scoop up and transfer spoil from the rock face. This material is then passed through the face of the SBU and pushed out through the machine to the full-face auger for removal. The SBU-A can be steered to maintain line and grade. Some contractors even employ guidance systems, much like the Axis system that Midwest Mole utilized on the I-69 Section 5 sewer line, which can aid in maintaining line and grade on longer crossings.
How Durable Is an SBU?
Robbins SBUs can bore through rock strengths ranging from 4,000 to 25,000 psi UCS and can tackle crossings ranging from 100 to more thanr 500 ft long, depending on ground conditions. “Robbins offers superior rock cutting equipment, responsive service, and is always willing to jump in and help create a solution,” said Midwest Mole operations manager Joe Butor. RELATED: 20 Years Later: Looking Back at the Development of the Small Boring Unit Small Boring Units like the hard rock head used on the I-69 Section 5 project have been known to tackle more than 2,800 ft over decades of service. The 36-in. SBU used by Midwest Mole has bored an incredible estimate of 20 projects, proving the durability of these machines when properly maintained and operated.