HDD Used to Install Oregon High School’s Geothermal System
January 21, 2014
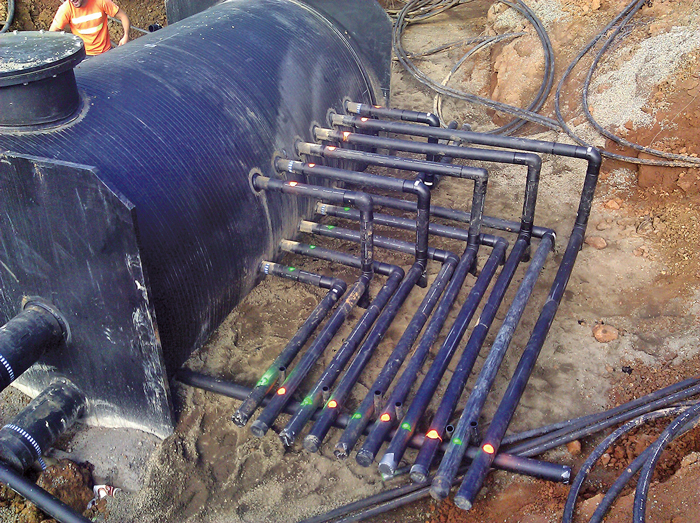
A new high school in Sandy, Ore., was no exception to the environmentally-friendly attitude builders and engineers around Portland possess. Located less than 30 miles outside of the city, the new school was designed to accommodate a growing high school population. The 310,000-sq ft building situated on 82 acres along Bell Street is almost double the size of its predecessor, and the campus will accommodate a minimum of 1,600 students and support space for an additional 200.
Prioritizing Energy Efficiency
To ensure environmental sustainability and build an efficient and cost-effective system for heating and cooling, the new school’s design included a geothermal system.
Geothermal systems use a safe, renewable source energy that is stored within the earth. A constant temperature is maintained below the earth’s surface and that energy can be harvested from its natural source to efficiently heat and cool a building. At the same time, the use of this type of energy does not harm the environment and is not reliant on non-renewable fossil fuels.
In a geothermal system, the source of the energy from the earth is captured by creating a series of horizontal and vertical loops underground. The loops are filled with water (or a water-based liquid) and are connected to a heat pump inside the building. The pump circulates the liquid through the ground loops, which creates a heat exchange. A geothermal circuit vault works as the central control point of the geothermal well field where the loops are connected. A circuit vault that is prefabricated helps save time and money during installation.
For this project, Interface Engineering, of Portland, designed the building, Hoffman Construction Co. served as the general contractor and GeoTility Geothermal Systems was chosen as the main geothermal contractor. ISCO Industries LLC supplied the geothermal materials.
The project offered several unique building methods, like horizontal directional drilling (HDD) to install different sizes of high-density polyethylene (HDPE) Unicoils. A Unicoil is comprised of a manufactured u-bend that is factory fused to measured lengths of HDPE pipe. This was the first time HDD was used to install this type of piping for a geothermal system in the West. The pipe coils were installed under a field in order to connect to a geothermal circuit vault.
The Unicoil lengths were some of the longest that the HDD drilling company, Lovett Inc., had ever worked with — the longest of which were 750 ft (for a total of 1,510 ft) — and the longest to have been manufactured. According to Lovett project manager Waylon Knight, putting in a total of 610 ft of pipe was more typical for other types of HDD installations.
Addressing Geothermal Supply Needs
To meet the geothermal supply needs for the project, GeoTility worked with Shelby Heritage, with ISCO Industries to provide the materials. ISCO supplied a custom 72-in. HDPE Geothermal Circuit Maker Vault. The prefabricated vault included butt-fused circuitry and data-logged joints.
“The original design specification included the use of a concrete vault. However, I worked hard to get the specification changed to an HDPE vault,” said GeoTility project manager Gerard Maloney. “We are very happy with the time and energy saved on this project, as well as the quality of the product and its leak-proof feature.”
ISCO also supplied 104 of the 1,510-ft Unicoils, 96 sets of 1,010-ft Unicoils, as well as fittings and pipe fusion equipment.
HDD Installation
To install the pipe coils, Lovett Inc. drilled 675 ft under a baseball field, which was left undisturbed during the entire process. The length of the baseball field was approximately 450 ft. At certain ends, Lovett needed to drill a total of 725 ft, which included the entrance and exit points of the drill. This required the use of the 750-ft, 1 ¼-in. u-bend pipe coil. Lovett bored on one side of the field and then pulled the pipe back underneath the field from the other end.
“The drilling went better than expected,” Knight said. “The soil condition is a little different than originally reported but we stayed on schedule. The soil was mostly clay with some boulders, and the project took us about four months to complete.”
According to Knight, normally when they used HDD for installing utility pipe, the pipe only needed to be installed 3 to 4 ft deep. For the geothermal application, the pipe was installed significantly deeper underground. Some coils were installed 30 ft deep, while others were 15 ft below the surface. To install the pipe using HDD, Lovett bored a hole in the ground, attached the pipe and pulled it back through to the other side. They had 35 to 40 ft of extra pipe available in order to know how far to pull back.
GeoTility and Lovett ran into one challenge while installing some of the coils, mainly due to where the drill was set up to bore under the field. Because of the location of the drill in relation to the site, the coils could not be grabbed from the u-bend to pull underneath the field. However, GeoTility was able to uncoil the pipe and attach the drill to the loose ends of pipe to pull through to the other side.
When only 22 coils were left to install, GeoTility senior estimator Jerry Carter said, “There were a lot of schedule opportunities and we are ahead in the drilling.”
Overall, the HDD installation ran ahead of schedule. The contractors were able to install six coils per day using HDD, which is comparatively fast for this type of installation and application.
Geothermal Vault Installation
To install the vault, GeoTility excavated approximately 9 ft down. The base for the vault was made of sand. Once the vault was inside the excavated site, the headers for the project, which were prefabricated by GeoTility, were dropped in and fused to the header pipe. Next, the pipe coils were tied into the vault. Once that was complete, GeoTility tested all the individual circuits, with a total of eighteen 3-in. circuits.
“ISCO has been very helpful,” added Carter. “Everything we needed here they have gotten for us. Overall, it has been a great experience. We look forward to more projects together.”
The new high school now has the added advantage of using a renewable, environmentally sustainable and efficient system to heat and cool its building. And with HDD, large tracts of land were undisturbed and the geothermal system installation was both speedy and successful.
Melissa Moody is public relations coordinator at ISCO Industries Inc.
Comments are closed here.