HDD in Florida
October 10, 2007
Pinellas County, Fla., officials knew that when the county took over wastewater operations in one of its municipalities, there would be a need for a new pipeline to transport the untreated water to one of the county’s wastewater reclamation facilities.
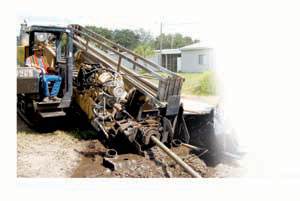
“We acquired the town of Belleair’s sewer system, including a treatment plant, with the intent of eliminating the plant and conveying the town’s wastewater to one of our major facilities, the South Cross Bayou Water Reclamation Facility,” says Mike Sweet, P.E., director of engineering for Pinellas County Utilities. “In the original proposal, we were going to convey the flow to another of our existing pump stations and, from there, send it on to South Cross.”
During the pre-planning, it was found that the age of the force mains, coupled with their location, would make the initial route for the project less desirable. Consultants determined that a better location for the new pipeline would be along the Pinellas Trail, an old railway that was converted to a popular recreational trail for jogging, walking and biking. Sweet explains that in addition to being the shortest route to the South Cross Bayou facility, the use of the trail area would also significantly streamline the process.
“What it did was eliminate having to put a lot of construction into Indian Rocks Road, a highly developed and heavily traveled roadway. To put in a force main and a returning reclaimed water line would have required tearing up nearly the entire roadway,” says Sweet. “According to the original project, not only did the sewage need to be transported to South Cross, but we also had an obligation to give them back an equivalent amount of reclaimed water, which they were giving to the local golf courses.”
While this adjustment prevented one major problem, it presented another. Chris Horton, president and CEO of Molehead Construction, the contractors for the Pinellas Trail project, explains that throughout the duration of the project, maintaining the trail’s availability was vital.
“The social concern on the job was the primary factor that we were given,” says Horton. “Do not mess up, keep the trail open and make sure people are happy. Most importantly, and the thing that Pinellas County has done incredibly effectively, is that they’ve communicated with their community on a consistent, on-going basis.”
The communication came in the form of a public relations campaign initiated by Pinellas County Utilities that explained the need for the pipeline, the methodology, the process and the eventual results. In addition to flyers and a utility bill insert, residents and trail users are able to call an information hotline to ask questions and learn more about the project. On the trail itself, field representatives are available throughout construction to answer questions and various message boards update visitors on the project’s status.
“The boards are up to tell them that the construction is going on but the trail remains open for use,” says Sweet.
With the hurdles of location and communication overcome, the next challenge that the team addressed was the design of the pipeline. With the route of the pipeline having shifted, the size of the equipment and materials also needed to adapt. Limitations on the length of the drill led to the decision to shorten it to 1,000 ft. Consequently, inlet and outlet points for each drill would be located every 1,000 ft; at normal construction depth, this would necessitate an air release valve at each of these points.
“Those are maintenance items, places where there is the potential on the sewer force main to have odor issues and those kinds of things,” says Horton. “So we wanted to eliminate as many air release valves as possible. To achieve this would necessitate taking advantage of horizontal directional drilling (HDD) technology and innovative techniques to drill at the shallow depth of only 8 ft below the surface.”
We were able to keep the trail open throughout the construction and set the line just off the trail and not have to worry about tearing up dirt along the whole length of the pipeline,” says Sweet. The pipeline is 35,000 ft in one direction and 35,000 ft coming back with the reclaimed waterline. There are two parallel waterlines drilled 5 ft apart within the trail right of way.
With the shallow requirements for HDD, the line is easy to excavate, allowing contractors to access the entry and exit points to lay the line flat — a technique referred to as ‘flattening the profile.’ Additionally, it allows operations and maintenance personnel to access the pipe in the future. According to John Giese, president and CEO of JR Giese Operations, the project was accomplished through a combination of precise engineering and open-mindedness on the part of Pinellas County representatives.
“In our opinion, this project is the exception to the way the HDD industry develops, designs and manages a project,” Giese says. “Usually a project of this nature would be designed for 2,000- to 4,000-ft shots with bigger rigs installing pipe 20 to 40 ft deep. We have to give a lot of credit to Pinellas County for not only taking into consideration the construction costs, but also evaluating the operation and lifecycle costs by saying, How can we do something a little different here and still provide our ratepayers with the lowest total cost infrastructure?”
“You could not have done this project, installing the pipe at an average depth of 8 in. with big rigs due to the mud pressure and fluid pressure downhole — you would have a lot of frac-outs and subsidence down the road,” Giese adds. “What we were able to do, through doing some engineering calculations on pullback and pipe stress and some mud calculations, was make an evaluation and commit back to the county that we could drill this pipe at an average depth of 8 ft. That is something new in this industry. We had a shallow profile, and we were able to maintain that flat profile except for some high points at road crossings.”
Jim Williams, P.E., project manager for JR Giese Operations and Molehead Construction, notes that there were natural high points in the design, as well as areas where extra caution was necessary. “We looked at road crossings where we would have utilities or where we were concerned about the integrity of the roadway and not disturbing that,” explains Williams. “We established some control points along the project where we knew we had to be deep. In between those though, we looked at the project based on Molehead’s ability to do this successfully and drill 8 ft deep, which is still a readily accessible depth to excavate.”
“Taking all of that into consideration, we could basically install it flat for the most part, like you would with open-cut and eliminate those high points except in places where you had road crossings or if there was a natural high point in the ground, which greatly reduced the number of air release valves.”
Aside from the technical complexities of the job, Horton reports that outside difficulties related to weather or soil were minimal — hurricanes and tropical weather have yet to impact the construction site, and while soil conditions continually vary (a feature not unusual in Florida), such eventualities were expected and are dealt with accordingly. In fact, Horton insists that it was the extensive planning — as well as the expert usage of smaller, more manageable equipment — that has helped the admittedly challenging drill to proceed as quickly and smoothly as it has.
“We do macro work with micro equipment — 100,000-lb rigs that can roll up — you don’t have to thrust block them, you can drop them down,” says Horton. “Our nimbleness, compared to someone with a 300,000-lb rig, allows us to recover the time and sheer cost. We’re not pumping 400 gallons a minute downhole, we’re pumping 125 to 150. Mud cost, fluid removal, the amount of infrastructure you need to support the project, all of those things are very small.
At the same time, we do the opposite from a management standpoint. Instead of looking at the macro, we’re looking at the micro fluid pressure. We always have a superintendent managing mud. We’re looking at all the mining variables, the speed at which we’re pulling pipe, what our ground conditions are; we look at a lot of things that larger diameter or larger drill rigs and larger type of work would look at.”
For a project that has so many intricacies, the pipeline has a remarkably short timeline for completion. Sweet says the notice to proceed was issued in November 2006, the pipeline will be operational in November 2007, and the entire project should be completed by December 2007 or January 2008.
According to Horton, a number of combined measures, from the rerouting of the original plans to the detailed monitoring of construction, have led to a smoother and more efficient construction job.
“Based on the experience we have, we were able to develop a game plan and the engineering and design work that was done allowed us to have a good game plan. The county was flexible as far as us being able to bring in the right people and the timing of the job, and ultimately to build it on schedule.”
Katherine Fulton is an assistant editor for Trenchless Technology.