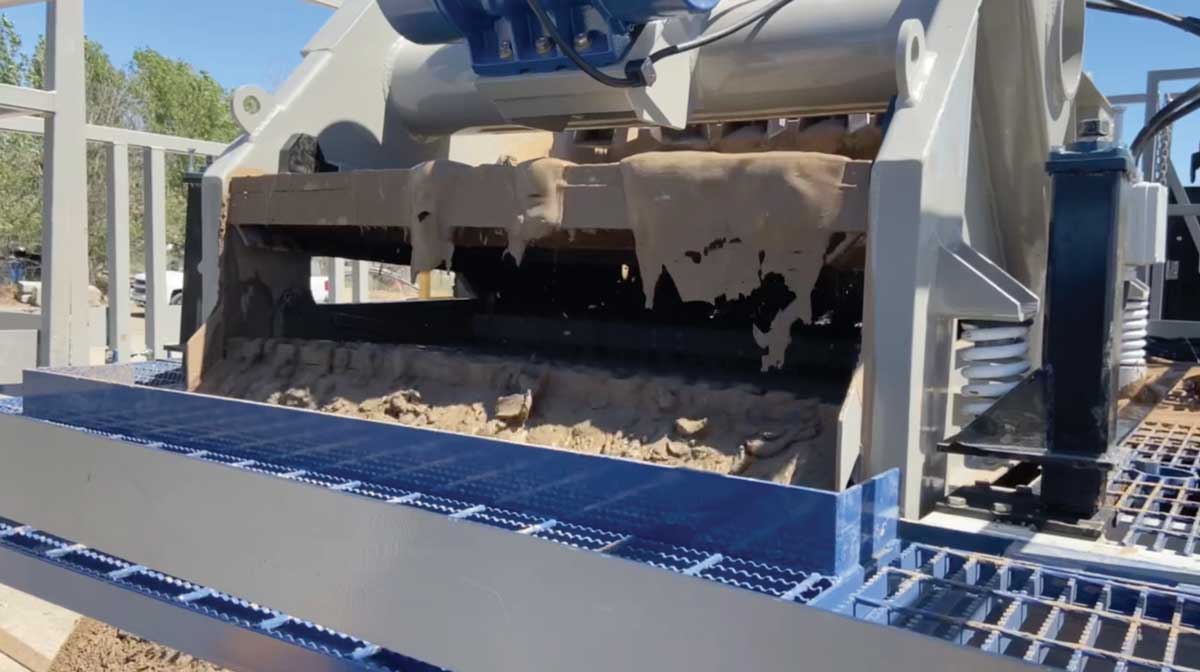
From the Pit and Beyond: A Breakdown of Your Mud Recycling System
Packaged mud recycling systems have become indispensable for most trenchless drilling operations, including horizontal directional drilling (HDD), geothermal drilling and water well drilling, among others. The increasing adoption of these systems is driven by the myriad benefits they offer. These benefits include, but are not limited to, reduced mud costs, increased lifespan of mud pumps and bits, enhanced rate of penetration and lower disposal costs.
Today’s mud recycling systems, whether referred to as mud reclaimers, recyclers or cleaning systems, represent a significant advancement from the makeshift oilfield-based units of the past. They are meticulously designed and engineered to suit the compact footprint of trenchless job sites, serving as a pivotal element in a project’s overall solids control strategy. Understanding the operational principles of a mud reclaimer and the fluid process flow through the system is paramount when selecting the appropriate unit for specific operations. In this discussion, we will delineate the operational process based on a unit capable of processing up to 600 gpm, effectively separating liquid/solids down to 25 microns.
Packaged mud recycling systems are all-in-one units featuring components such as shale shakers, hydrocyclone desilters/desanders, centrifugal pumps, solids loading hoppers, partitioned fluid tanks, and mud gun/top mount agitators. Sizing the appropriate mud system processing capacity for operations, Elgin Separation Solutions recommends multiplying the rig flow rate by two.
The process of every mud system commences with the pit, where used drilling fluid is discharged from the borehole into a catch basin. Subsequently, it is pumped to the reclaimer utilizing a submersible pick-up pump, also known as a ‘trash’ pump. Proper sizing of the pump based on the flow capacity of the reclaimer is essential, along with ensuring the inclusion of a heavy-duty strainer and chrome alloy impeller.
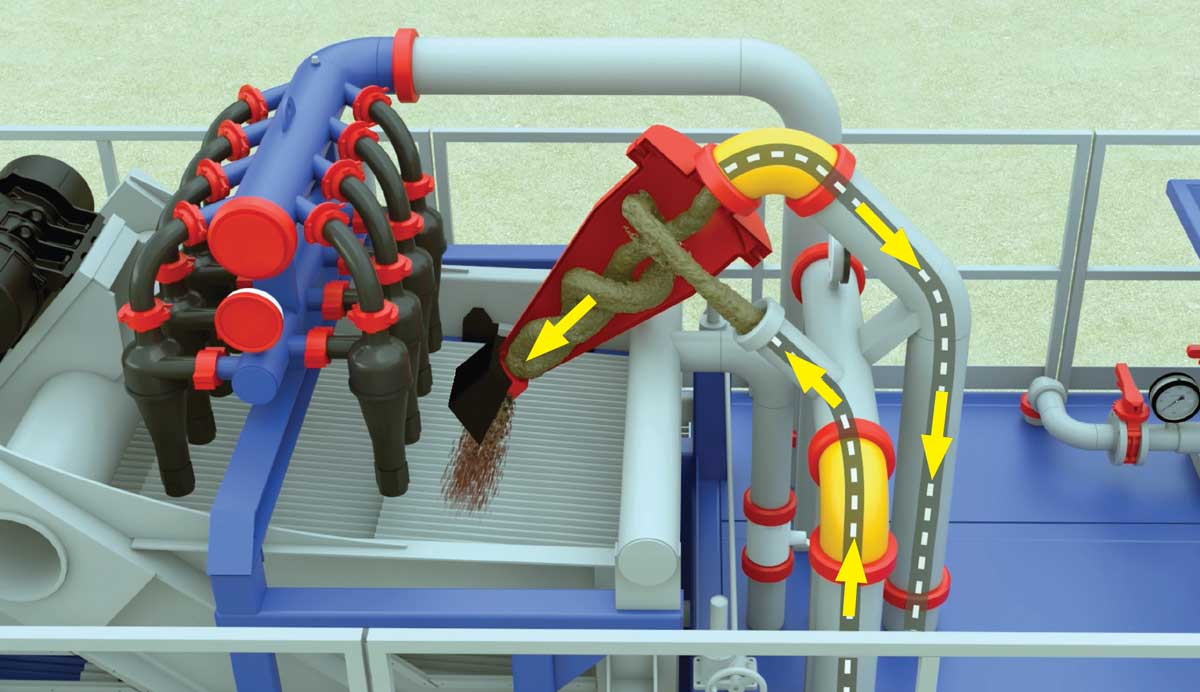
The fluid from the pit is then transferred to the onboard shale shaker, the cornerstone of the system. Depending on the system’s size, shale shakers come in two-, four- or six-panel double deck configurations. These shakers employ high G-force vibrator motors to induce linear or balanced elliptical motion patterns, facilitating the separation of solids from liquid. The first pass across the bottom deck of the shaker typically separates solids from liquid down to approximately 200 microns, achieved through screens installed on the shaker. Screen panels are a made of a rigid frame and layers of stainless-steel wire cloth designed with openings that allows fluid to pass thru while blocking solids of specific size range. Blocked solids are discharged off the end of the shaker for disposal. Screens are rated in various sizes known as either API rating or mesh count. Proper selection of screens is crucial for effective solids/liquid separation.
The fluid passing through the shaker screen collects in a partitioned tank known as the ‘dirty tank’ and is then pumped, using a dedicated centrifugal pump, into a set of hydrocyclone desilters/desanders to further separate solids and liquid. Hydrocyclones are essentially simple devices that convert pressure generated by a centrifugal pump into centrifugal force, causing suspended solids in the mud to be separated from the fluid. In drilling operations, hydrocyclones use these centrifugal forces to separate solids in the 25- to 250-micron range from the drilling fluid. The solids laden fluid is discharged from the lower apex of the cone, and the clean drilling fluid is discharged from the overflow discharge. The drilling fluid is discharged from the lower apex of the cone onto the top screen deck of the shaker.
In higher capacity systems, the fluid may undergo further processing through hydrocyclone desanders before entering desilter manifolds. Proper maintenance of hydrocyclone performance involves maintaining optimal pressure during operation, ensuring efficient solids separation.
The clean drilling fluid is discharged into the ‘clean tank,’ where it undergoes analysis for weight, gel strength and viscosity. Based on the results, necessary additives like barite or bentonite are incorporated back into the fluid using an onboard jet shear mixing hopper. The hopper discharge side features a jet shear piping configuration to instantly blend the additive and fluid. The blended fluid flows back into the clean tank and is pumped away from the reclaimer back to the rig by the onboard centrifugal ‘transfer’ pump.
Tank agitation in both the dirty and clean tank is managed via in-tank piping known as mud guns or by top-mounted tank blade agitators. During operation, it is crucial to maintain tank agitation to prevent the solids from settling at the bottom and keeping the material in an agitated state for efficient solids/liquid separation.
On the packaged mud system, the fluid in the clean tank is pumped into the mud gun piping for agitation. A standard reclaimer will have a dedicated centrifugal or Durolast RB rubber lined pump for desilter, hopper/mud gun, and transfer functions when moving the drilling fluid thru the system. When operating larger systems, an additional pump is added to feed the hydrocyclone desander.
In conclusion, the operational flow of a packaged mud recycling system is straightforward, but each component must function effectively to achieve the desired solids/liquid separation. Fluid traverses through various components before reaching the rig, with monitoring systems in place to ensure efficient operation.
Trailer-mounted reclaimers with dedicated generators offer mobility and convenience, contributing to operational efficiency and reduced environmental impact. A comprehensive understanding of packaged mud recycling systems is indispensable for modern operators, facilitating cost savings and environmental sustainability.
Raymond Pietramale is director of marketing at Elgin Separation Solutions.