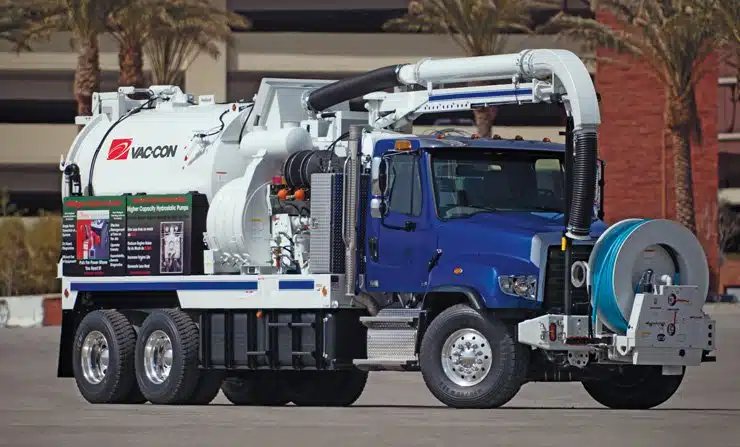
Pipe Cleaning: Fans vs. Blowers
June 28, 2016
Knowing the difference between fan and positive displacement machines will help you make the right purchase for your business.
Customers in today’s combination sewer cleaner market have two choices with which to generate vacuum: centrifugal fan or positive displacement blower (PDs).
This column is not intended to sway, discount or condemn either method, but rather dispel the myths long-associated with both vacuum methods and components.
Neither fans nor PDs were originally intended for the sewer cleaner market, but both were designed to convey. To better understand how they ended up in this market, you must first learn a little history.
Positive Displacement
The positive displacement machine was invented around 1860 as a “more efficient” water wheel. Made of wood, it was put into the millstream and as water flowed through it, the rotors turned and power was generated from the output shaft. Over time, wood components swelled and ruined the clearances, causing the mill to stop. The unit would then have to be taken out of service and dried out, shrinking the components their original dimensions. As soon as the rotors would turn, a power source was connected to the output shaft to speed up the drying process.
Someone noticed that this arrangement cold move a significant quantity of air and the use of air blowers began.
Cupola blowers became the first application for this newfound technology. Each rotation of the rotors represented a specific amount of air being forced into the furnace, thus allowing the furnace mater to develop the theory that the more rpm the blower turned, the hotter the fire became. The positive displacement machine was originally intended for pressure applications, which led to the original nickname, “blower.” Only in the last 30 years has the machine been adapted to provide negative pressure in truck-mounted vacuum applications.
The PD machine is constructed with two lobes that rotate in a cast steel housing in opposite directions of each other. The design of the PD is such that each lobe traps a specified amount of air — depending on the size of the PD — for each rotation. PD machines rely on close tolerances — as small as .009 of an inch — to trap the air. Unless the PD is designed to run fully blanked off, relief valves are necessary to protect the unit from building too much vacuum, which creates too much heat and subsequently causes the internal components to expand and collide with each other. Generally, the input speed of a PD blower is approximately 2,200 rpm, which produces 16 to 18 in. Hg while creating 2,400 to 4,200 cfm.
One common misconception of PDs is that no matter how deep, no matter how far, a PD can “pump” the water or material. This is untrue. A PD machine has a finite lifting capability; once a PD reaches its lift capacity, an operator must fluidize (add air) to continue conveying material to the holding vessel. PD machines work well in liquids, sludge or thick materials, and vacuuming over a long distance horizontally.
Centrifugal Fan
The centrifugal fan was designed in/or around the 1960s for conveying grain. The conveyor’s orginial design had a centrifugal fan powered by a diesel engine, piping in which the material was conveyed, a cyclone and an airlock. The technology was aimed at off-loading grain from ocean-going cargo ships more efficiently that the shovel and bucket method. This machine could vacuum material from the berths of a cargo ship and lift it into a cyclone. Grain would drop out of the cyclone via an airlock, and the exhaust or pressure side of the blower would then push the material to the storage vessel onshore. The unloading process, which previously took several days, could now be completed in hours.
The centrifugal fan uses rotating “fan” blades to compress air in compound stages. This device in its most powerful configurations is capable of lifting a column of water 200 in., the equivalent of approximately 14 in. Hg (vacuum). It is fully capable of vacuuming material under water up to its rated lift performance, either with or without air induction. The closest tolerance in a fan is roughly ¼ of an inch. The air is drawn to the inlet of the fan blade, and as the blade spins, it moves and compresses the air.
One common misconception of the centrifugal fan is that it cannot vacuum under water. That is absolutely untrue. A fan can vacuum to its rated lifting performance whether it’s underwater or not. If a fan is rated at 200 in., it can lift an 8-in. column of water to 16.67 ft. If the level of the water is less than 16.67 ft from the top of the boom, the fan can vacuum under the level of the water with no attachments. If the water level is greater than 16.67 ft, a fluidizing nozzle is used to add air into the air stream. Centrifugal fans work well in moving liquids and solids at more than 100 ft vertically or horizontally.
This timeless topic has been and will continue to be the single- most argued point in the combination machine industry. The fan vs. positive displacement argument rivals the Ford vs. Chevy debate. Books have been written regarding the benefits of fan over PD and vice versa. Each of these vacuum generators has applications where it outperforms the other.
The single-most important thing to consider is the application for which the machine is going to be used the most. If you are still unsure of which machine to purchase, contact your local sales engineer who is trained in the operation of both of these machines.
Mike Selby is national service manager at Vac-Con.