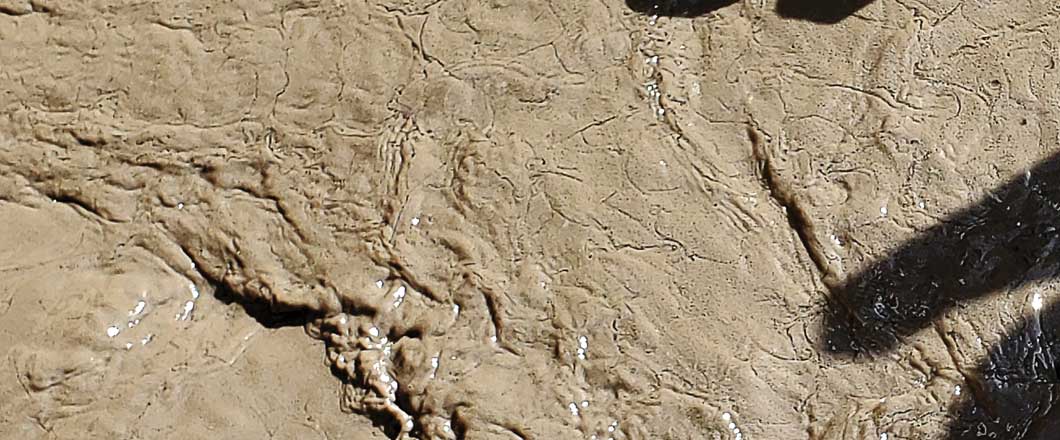
Engineered Drilling Fluid Programs – The Mud Engineer, You Never Knew You Had
Engineered Drilling Fluid Programs (EDFPs) act as a guide for tank hands, a bidding tool for contractors and as an educational tool for owners.
It exists so that everyone can utilize the mud product effectively, help them understand what each product is and why it is being used. This is all without the need for an expensive mud engineer. EDFPs can vary in appearance and format but all retain a common idea. They exist as an extension of a mud engineer’s knowledge and experience.
For an EDFP to be useful it must contain a drilling fluid mixture appropriate for the geology to be encountered, and which addresses the weaknesses and strengths of a particular trenchless method. An EDFP designed for an HDD will be of little use in a microtunnelling or direct pipe application. Inappropriate mixtures or applications can lead to unnecessary product usage, increased costs and increased waste.
What Is an EDFP?
In its most basic form, an EDFP is mixing guide for the tank hand. It denotes concentrations, dose rates, and fluid properties. Depending on the geology and specific additives used, these values can range from pure bentonite mixtures to complex inhibitive, bore stabilizing mixtures.
RELATED: Designing a Drilling Fluid Program
The goal of this guide is to ensure that the concentration of product doesn’t fall below the minimum effective threshold. Most drilling fluid performance problems arise from the inadequate maintenance of the system. Not adding an additional product with every addition of water eventually degrades the performance of the system leading more extensive problems later on.
Using the geotechnical report as a reference, the mud engineer designing the fluid system can point out potential problem zones which could have been overlooked. Contingencies can then be put into place to remove or mitigate these problems. These contingencies can resemble a simple viscosity increase or can be as drastic as preemptively mixing a lost circulation pill. A troubleshooting guide is also included which when used in combination with the prescribed fluid properties can be a powerful problem-solving tool.
There is no one solution to all applications and geologies. A fluid system designed for HDD cannot be converted to a Direct Pipe or microtunnel easily. A Direct Pipe may have been based on an existing HDD profile but the similarities end there.
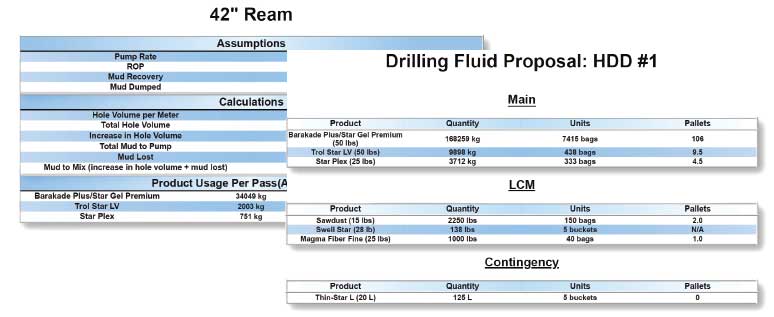
Direct Pipe and Microtunnel Plans
HDD programs focus on bore stability, cuttings removal and minimizing annular pressures. Direct Pipe and microtunnels operate on a different principle. In comparison to HDD these methods are relatively low pressure and deal with greater slurry volumes. In addition, these systems are closed circuits that suffer minimal losses. They are separated into two parts. The first part is a face slurry responsible for removing cuttings and counteracting the pressures found at the MTBM face. The second is a stabilizing fluid pumped into the annular space created by the overcut.
The face slurry is designed to minimize mud weights and maintain fluid velocity. To meet these requirements a microtunnel slurry in a competent geology will forego a typical bentonite mixture and opt for an inhibitory water-based mixture. For unconsolidated or fractured formations, a lean bentonite slurry is desired. This will build a suitable filter cake on the face to help resist losses and reduce wear on the cutters.
Direct pipes are usually designed with large elevation differences and have extended slurry lines but cannot utilize a pure water system due to the highly unconsolidated nature of the geologies that warrant a direct pipe. These requirements put a lot of stress on the slurry pumps so maintaining the lowest weight mud is major goal of a direct pipe EDFP.
One of the most important aspects of the stabilizing annular fluid is the lubricating effect it imparts on the tunnel segments/product pipe. A reduction of annular friction results in a decrease of the required jacking forces which is one of the limiting factors for maximizing drive lengths. For Direct Pipe, the fluid also acts as a buffer to protect the pipe from abrasion and formation sloughing.
In order for a contractor to do the work, it must be awarded. Providing an accurate estimate of products required and disposal volumes shows that the contractor has done their due diligence while putting together their proposal. Depending on the size of the project the drilling fluid bill could make up a large portion of the end amount. The excess usage of unnecessary products along with losses attributed to poor fluid system design can greatly increase disposal volumes and subsequently costs.
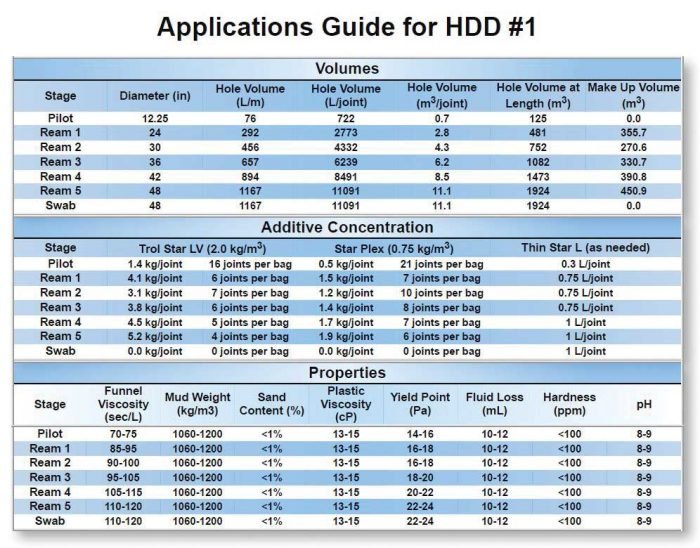
EDFP as an Estimator
Logistical considerations should also be made especially when projects are in remote or difficult to access areas. Unnecessary mud product usage, excess waste removal, and additional water deliveries can quickly add up and end up affecting the final cost of the project which could have been minimized by using an EDFP. By utilizing the EDFP as both a guide and a product estimator, it is much easier to obtain an accurate estimate for the bid, so that the project doesn’t exceed the estimated price.
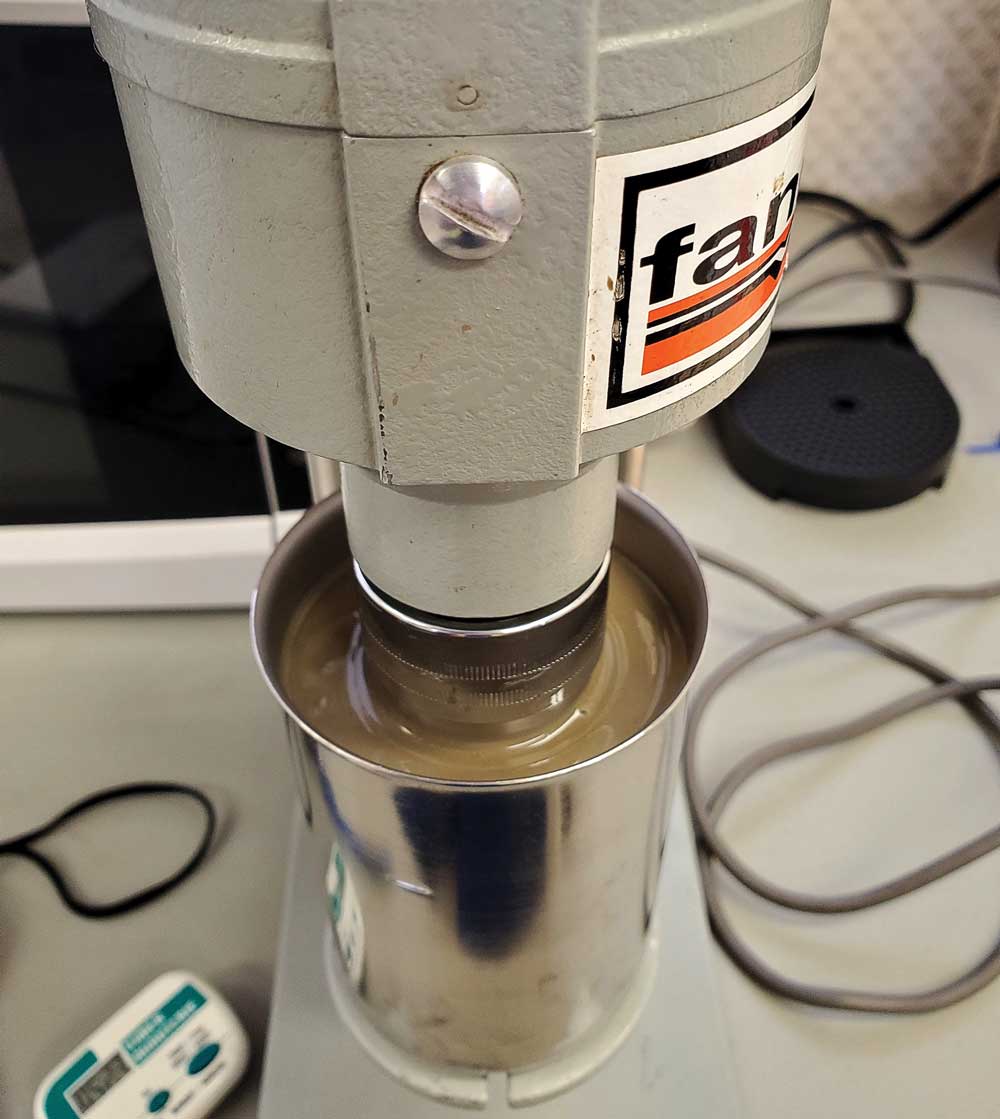
EDFP as an Educating Tool
Education is an important aspect of an EDFP. In the end it comes down to the owner to accept the plan and for the contractor to implement it. If they don’t see the reasoning or benefit behind a product, it is unlikely that it will be used. This could have, major consequences on the performance of the proposed fluid system. Providing justification for fluid properties and products can eliminate the ignorance around drill fluids which can later manifest as a major problem.
At every level an EDFP has a use. From acting as a guide for tank hands to mix the perfect fluid system tailor to their specific project, to the managers who can use the information to help formulate their bids. Even the owners benefit from the informative and educational contents of an EDFP. An EDFP is an extension of the author and in some cases a suitable replacement for a mud engineer.
Brandan McGuire is the technical services manager for NorthStar Fluid Solutions