Drill Bit Selection: Simplifying the Process
January 1, 2009
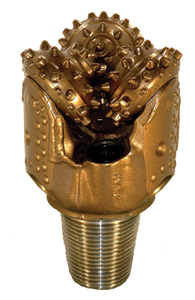
- Identify – Soil/Rock type(s)
- Classify – Soil/Rock category
- Choose – Bit type within the category
- Optimize and Adjust – Operating parameters/subsequent selection
- Perform a site (or sight) survey. Sometimes actual geology is exposed from pre-existing road work, other construction, or through onsite potholing.
- Contact the U.S. Geological Survey for geology specific to a location.
- Contact the Natural Resources Conservation Service (formerly Soil Conservation Service) for soil surveys in a specific area.
- Contact local water well drillers.
- Contact local construction companies.
- Contact tooling suppliers/manufacturers, they may provide information related to past experiences in specific areas.

Compressive Strength/Hardness | Range Soil & Rock Types |
0 to 10,000 psi/Low | Dirt, Clay, Cobble, Talc, Shale, Siltstone, Unconsolidated Sandstone, Slate |
10,001 to 30,000/Mid | Limestone, Dolomite, Sandstone, Coarsely Grained Granites |
30,000 +/High | Finely Grained Granites, Trap Rock, Chert, Iron Formations, Quartzite |
Classify – Define soil/rock category. To simplify, I suggest the following categories.
Choose – Choose a bit within the category. Bit choices progress from softer to harder in descending order. Choices listed within each category should produce cost-effective results. However, there can be overlap between hardness categories. Use of a downhole motor can influence bit choice. Blade and point attack type bits are commonly used without a downhole motor.
Compressive Strength/Hardness Range | Suggested Bit Types |
0 to 10,000 psi/Low | Drag or Blage Type (duckbill, spade, etc.) Point Attack, Shear Type (PDC) Milled Tooth & TCI Roller Cone, Single Cone TCI |
10,001 to 30,000/Mid | Milled Tooth Rollar Cone |
30,000 +/High | TCI Roller Cone with conical or round top (dome) inserts |
Optimize – Utilization and adjust subsequent selection if required.
- Talk to suppliers and manufacturers of these products. They can provide recommended operating parameters and guidelines for optimal use.
- Noting and identifying cuttings return characteristics while drilling can help in refining ongoing utilization and selection.
- Rig operating limits can influence bit selection.
- Torque requirements become greater in softer
- materials.
- WOB (weight on bit) requirements become greater in harder materials.
- Sealed, friction bearing, roller cone bits are preferred for fluid applications. However, open bearing roller cone bits are used successfully on shorter bores of less than 200 ft.
- TCI roller cone bits with round top shaped inserts will produce the slowest ROP (rate of penetration).
- Maximum gage, shirttail, (skirt) and leg protection is a must for roller cone bits.
- Your rig operating cost investment outweighs the cost of a drill bit. Choose a bit that produces the most cost effective balance of ROP and total run time. Trip time is costly – improved ROP equals less drilling hours and money spent.
- Conventional “petroleum” roller cone bits are not always best suited for HDD.
- Certain bits, designed specifically for HDD, can prove to be more cost effective.
- Re-run roller cone bits are “used bits.” No one can tell you how used they are. These bits are considered a risk and discarded by petroleum operators. Consider the investment in your bore and weigh the risks.