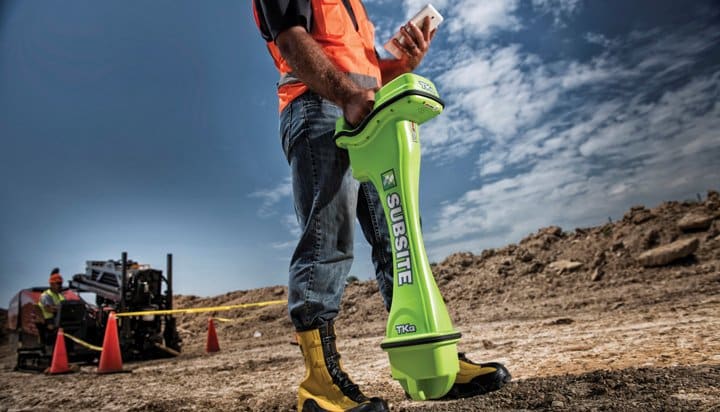
Directional Drilling: Tracking and Guiding 101
The middle “D” in the acronym HDD stands for “directional,” and without directional capabilities, horizontal directional drilling (HDD) could never have become the primary trenchless construction method for installing underground utilities that it is today.
For HDD units installing underground pipe and cable–models ranging from 5,000 to 100,000 lbs of pullback, the directional information is almost always communicated with walk-over electronic tracking and guidance systems.
RELATED: Directional Drilling: HDD Locating Systems Improve As-Built Data
Basics of Tracking and Guiding a Pilot Bore
A small radio transmitter in the drilling head transmits information about the location and orientation of the drill bit’s slanted face to a crew member who walks directly above the drill head with a handheld receiving unit. Information is displayed on a screen at the top of the receiver and to a remote display at the drill machine’s operator station and provides information necessary for the driller to change direction of the bore. The drill operator makes steering adjustments by stopping rotation of the drill string, positioning the face of the bit, and pushing the bit forward. Friction with surrounding soil changing direction of the bore path.
HDD guidance systems have come a long way since the first HDD equipment was introduced and crews used utility locators and makeshift methods to track bore location and make guidance changes.
However, it wasn’t long before trackers were developed specifically for directional drilling, and tracking systems have evolved steadily ever since. Walk-over guidance systems do things today that they couldn’t do a few years ago.
For HDD units installing underground pipe and cable — models ranging from 5,000 to 100,000 lbs of pullback, the directional information is almost always communicated with walk-over electronic tracking and guidance systems.
Significant Advances
One of the greatest advances in today’s HDD trackers is the ability to operate in areas where there are high levels of electrical and electronic interference. Not only are there existing utilities emitting signals that can conflict with the tracker, but most everyone on the work sites these days has a smart phone, adding to the clutter interfering signals.
Multiple frequencies of today’s equipment can typically provide at least one clear signals under these conditions, enabling them to work along with conflicting signals.
Signals that can see through the interference and more transmitter power give today’s trackers greater depth capabilities–to 100 ft and more. In some instances, the extended depth can allow walk-over equipment to be used in situations that once required costlier wireline tracking when bore depths exceed the limited range of earlier walk-over tracker models.
RELATED: Subsite Electronics Launches Commander 7 HDD Guidance Display
Another important advance available on Subsite Electronics guidance systems is the “Drill-To” feature.
Positioning the walk-over receiver ahead of the drill head and long the projected bore enables the path of the bore to be monitored in real time and to anticipate corrections to follow the intended bore path. The drill-to mode not only provides a projected depth based on inclination of the drill head and the distance from the tracker, but saves time. Drill to is extremely useful when drilling in areas where walking over the bore path is impossible or impractical–busy highways, steep slopes and bodies of water, for example.
The straighter the pilot hole, the easier and faster the product pullback and real- time monitoring provided by the drill-to feature helps reduce the number of directional changes which ultimately can mean a faster, more trouble-free product installation.
User interfaces have been simplified and screen displays are brighter with more contrast to be easily read in daylight.
Battery Options
Battery size and type vary with equipment model, but the use of off-the-shelf rechargeable NiCad (nickel cadmium) batteries in the tracker allows for cost savings over off-the shelf batteries.
In cold weather, batteries may lose power more quickly, and many drillers switch to NiMH (nickel metal Hydride) batteries, which can have two to three times the capacity of equivalent size NiCd products and a have a higher density of energy.
Care and Maintenance
Tracking system manufacturers have devoted great attention to making guidance equipment rugged and resistant to the harsh conditions in which they often are used. Keeping equipment in protective cases when not in use limits the possibility of damage. It is of critical importance to keep circuit contact points clean, free of dirt and clean off any signs of the beginning of corrosion. Wipe off water and mud before it can dry, especially on the display window, which can be scratched or damaged when cleaning. Keeping circuits clean is especially important when operating in the winter months.
Availability of service and support are factors to consider when evaluating equipment. Where will it have to go for repair? What is the turnaround time? Are loaner units readily available?
More Than Tracking
Today’s top-end equipment does more than just report drill head location and orientation. Models are available that work with bore planning software and can capture and store data to create an as-built record of the completed bore path.
Such systems can provide quick-reference information on bend radius for more efficient use of drill pipe and installed product. They record drill head position each time a new drill pipe is placed in the ground and during pullback, the position of the product.
RELATED: The Importance of Bore Planning
They compile information, including number of pipe joints used, depth estimates, drill head roll angle, pitch, directional transmitter temperature and battery level, plus date and time.
Information can be downloaded and additional jobsite information added such as utilities crossed, obstacles encountered and other details. One model is available with a mobile app to download bore data direct to wireless phone or notepad as well as a laptop computer. The tracker and software eliminate the need to hand write bore details and can print out complete as-built reports, including graphs representing the bore, to present to the client and retain as a record.
John Bieberdorf is senior product manager at Subsite Electronics, a Charles Machine Works Inc. company.