Digging Under the Desert
June 13, 2014
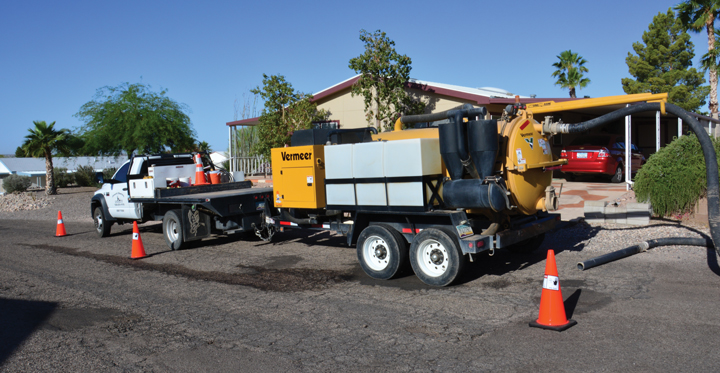
Desert Boring Excavation LLC arrives at a hot, sunbaked jobsite. The company has been called in for a utility expansion project in Arizona. The underground construction company is dedicated to locating underground utilities and using HDD technology to improve the infrastructure of the cities and towns in Arizona.
When Desert Boring arrives at one of these jobsites, the first man to step out of the truck is Michael Magill, co-owner of the underground construction company, based in Coolidge, Ariz.
“I’m an owner, but I’m also one of the operators. When we show up on the job, you’re getting the owner of the company and a crew that has pride in what they do,” Magill says. “We can handle many different operations.”
Their portfolio of services includes directional drilling, pit digging, utility locating and potholing. The latter of that list has become the bread and butter of Desert Boring, as potholing — for projects ranging from residential utilities to engineered canal systems — with vacuum excavators has grown in popularity in the Grand Canyon state.
Desert Boring was born of out of this demand for directional drilling back in 2006. Magill began working with another contractor to develop a directional drilling company that would help with boring lines for local phone and power companies. The fledgling company purchased a Vermeer 18×22 horizontal directional drill and a McLaughlin vacuum excavator and set to work as a subcontractor.
“We did primarily boring, typically five days a week, for the telephone or power company. I would estimate that 90 percent of our work came from another contractor. However, as that work slowed, we began branching out and started doing more custom potholing for other contractors,” Magill says.
Potholing is a key step in the underground construction process. The excavation method — which Desert Boring accomplishes with a vacuum excavator — allows the crewmembers to visually locate utility lines or underground obstacles by removing soil, water and other debris before any boring or trenching is started. This is a critical step in reducing the risk of damaging other utilities.
The company began to grow incrementally over the next few years, performing installations for contractors and other utility owners, all the while continuing to expand services further with vacuum excavation. During this time, one town discovered the capabilities of Desert Boring and contracted with them to perform a variety of the municipal utility projects for the city.
Florence and Excavating Machines
Florence, Ariz., is a town of approximately 25,000 in the south-central part of the state. Desert Boring was contracted by the City to primarily work with the water and wastewater departments; specifically, a majority of the potholing work is focused on assisting the water department in repairing leaks.
“Florence has its own vacuum excavator, but they still prefer to use us due to the high cfm capacity of our units, as it works better in the cobble and rocky ground conditions. At times we will have a full-time crew working with a 800-gallon vac unit just assisting in replacing fire hydrants,” Magill says.
In an effort to prevent shutting down service to an entire neighborhood, the city of Florence prefers to perform maintenance without disabling the water system; it is this continual flow of water during the repair process that has necessitated the use of a vac.
Desert Boring will typically show up at the jobsite with its Vermeer by McLaughlin V800LEHD vacuum excavator in tow. They will then use their McLaughlin Verifier G2 locator to identify where the utility lines run and use this location to excavate with their vac at the verified utility location. However, in the event that the leak has been flowing and the ground is too saturated, the crew does not have the luxury of time and will have to move in quickly with the vacuum excavator.
Once the material has been removed and the water pipe has been exposed, then the line can be repaired. Most of the lines that need to be repaired are 1.25 in. or smaller. Desert Boring will vac a large pit that is either 4 by 5 ft or 4 by 6 ft; then they will remove all the material so the utility can actually cut the line at the leak and install a compression-style valve in the line. Nonetheless, when the pipe is cut, the vacuum is in place to suck up the water as fast as it is coming out to help maintain a workspace.
Another major project that Desert Boring and the City of Florence team on is the replacement of fire hydrants. Much like the replacement of water lines, the process begins with locating all utilities. The crew then excavates a small opening and potholes down to find the buried depth of the hydrant that connects to the water main. By determining this depth, the utility company can order a new hydrant with the correct buried depth.
Once that depth has been calculated, Desert Boring will make the hole larger around the pipe so they can figure pipe diameter and circumference.
“After we figure those measurements, we will backfill the pit, and the utility company will order the new parts. When it is time for the new hydrant, we return to the site and excavate a pit large enough so the crew can cut the old hydrant out. We have the vac onsite to keep up with the reduced water flow coming out until the new fire hydrant is installed,” Magill says.
To handle the hefty volume of water that the company deals with at many of its jobsites, Desert Boring has had to increase the capabilities of its vacs. Originally, they rented an 800-gal, low cfm vac with a 400-gal water tank; after only two weeks of rental, Magill noticed the value and didn’t hesitate to invest in the larger vac. As the work began burgeoning and larger equipment became necessary, Desert Boring purchased a Vermeer by McLaughlin V800LEHD high cfm vacuum excavator.
“It made an absolute world of difference. When there’s a line that the utility company has cut through and you’re sitting there sucking up 2 in. of water blowing out of a pipe, in a 500-gal system, you might only get 45 to 50 seconds before the vac is full. If it is an 800-gallon vac, you’re able to go two minutes to two and a half minutes. It may not sound like a lot of time, but when you have somebody in the hole that’s trying to put a fitting on a line, that’s all you need,” Magill says.
According to Magill, the additional cost is more than worth it to have the greater capacity vac.
The Importance of Locating
With so much infrastructure construction and so many people relying on the water lines and fire hydrants of the city, accurate locating is crucial for the prevention of any damage. Magill will use a McLaughlin Verifier G2 locator to double-check markings for utility lines in order to minimize chances for striking any existing utility.
“The utility locator is a huge advantage for us. There is so much time-savings and cost-savings that we achieve by using a locator. Additionally, we know what we’re trying to pothole or what we’re going to be potholing around,” Magill says.
In Arizona, the extensive canal system can add another level of difficulty to locating. Often these canals are in rural desert areas of the state, which means reaching out to One Call and waiting for a representative to reach the jobsite can be very time-consuming and expensive.
“This is why we stress planning ahead and using our own locator. We are able to locate these lines by ourselves in a timely manner. When you’re charging the customer an hourly rate, that doesn’t look attractive to them if you are waiting around to locate or just taking a guess and starting to vac,” Magill says.
When Magill and his crew are able to show up, locate quickly and locate precisely, the guessing or waiting that lead to excess costs are eliminated.
Extending the Life of Excavators
Even with so much experience with the vacuuming and locating processes, Magill still stresses safety to anyone working around the equipment and the jobsite. The first and foremost items are personal protection gear, namely electrical gloves and eye protection.
“We use the gloves anytime that we are going to be potholing electric utilities, from street lights to power sources. Additionally, safety glasses are worn at all times,” Magill says.
Along with promoting crew safety, machine maintenance is a top priority for Desert Boring, especially with extensive hours on its machines.
The vacs, drill rigs and backhoes are all on a 200-hour maintenance schedule. Every 200 hours, Magill and his team change all of the fluids in the vac; every filter on the vac — air filter, fuel filter and oil filter — are also replaced at that interval, and every other day, the crews clean the suction side filters. The filter is pulled out, dusted off with compressed air and replaced in the machine.
Magill has to be aware of the cyclone units rusting, due to the amount of water leaks Desert Boring addresses with its vacs. Due to the volume of water filtered in and out of the vacs daily, Magill says the possibility of rusting is a concern. To alleviate these concerns, washing the cyclone units out every day to remove dust and moisture stuck in them, and leaving them open, has been a valuable solution.
“We think of these as standard procedures and cheaper maintenance. It is cheaper to get a $10 fuel filter than risk a filter plugging up on the jobsite and having to shut down and wait to fix a more significant problem,” Magill says. “That’s another benefit of being an owner/operator — I am able to keep a close eye on maintenance and the hours logged on a machine.”
The challenges and changing landscape of boring and excavating are forcing companies like Desert Boring to stay on the cutting edge. Magill has noticed the shear mass of all aspects of the equipment is growing; from the data logging potentials to the capacity of the vacs, capabilities are always expanding.
In the ever-evolving world of boring, excavating and locating, Desert Boring has kept a finger on the pulse of these changes. The company’s attention to detail has contributed to a growing reputation for success and customer confidence in vacuum excavator potholing and locating.
Darren Cline is a features writer for Two Rivers Marketing, Des Moines, Iowa.
Comments are closed here.