Canadian Crossing
August 1, 2008
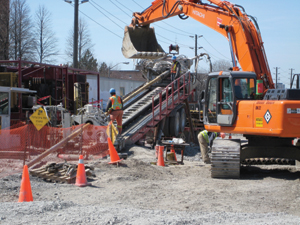
The project was set to begin in early January 2008. Setting up in restricted worksites near residential areas of Toronto within 200 ft of homes and condominiums, Mears was required to work within the limited area allotted by power line and existing pipeline rights of way, as well as comply with strict environmental protocol and local noise ordinances requiring sound damping equipment and restricted work hours.
Mears first set up its American Augers 880,000-lb drill plant utilizing as little space as possible in order to minimize future reclamation of the site after the completion of the project. Following a well laid out site plan, the plant was assembled with one access point running through to the back of the plant allowing the necessary access for the delivery of materials and tooling during the project. In order to comply with the environmental protocol, the site was stocked with hay bails, silt fence and other materials and equipment to use should they be required for containment of drilling fluids that might inadvertently return to the surface somewhere along the crossings’ profile. Heavy sound curtains were hung on the power equipment, shielding the condos from the 94 to 96 decibels of engine noise that would come from the equipment running throughout the duration of the project, which satisfied the directives given by the city to reduce the noise to an acceptable level.
First Crossing Challenges
The first crossing at Lawrence Avenue had site preparation and drill plant setup scheduled in January, but due to delays in right of way preparation because of weather conditions and other unforeseen conditions, commencement of the drilling operations did not get under way until Feb. 5. Within 110 m of drilling, the first sign of difficulty involving the ground conditions became apparent as the geology became very firm. Drilling with the conventional tooling that was being utilized, known as a jet assembly, proved inadequate. The drill stem was tripped back to the rig in order to change the tooling designed to penetrate and steer in the ground, known as the BHA or bottom hole assembly. The tooling typically used for softer soils was removed and replaced with a bit and mud motor designed to penetrate much more compressed soils and rock formations.
Careful Steering & Teamwork
Because of the proximity of an existing pipeline, the installation of the new 36-in. steel pipe required careful steering throughout the profile. When Mears began drilling the pilot hole, vac trucks were brought in to physically locate the drill bit and the existing pipeline, often referred to as a “hot line,” before drilling passed. The same precaution was carried out when drilling past the hotline on the exit side of the crossing. The pilot hole was completed on Feb. 15 and preparation for the reaming operation commenced immediately.
RB Somerville was contracted to perform rig operations on the exit side of the crossing, commonly referred to as the “catch rig” operation. For this, the contractor used its American Augers 185,000-lb rig. The catch rig receives, or “catches,” and breaks down the drill stem as it comes out of the ground on the exit side during the ream pass. The catch rig also aides in providing a constant pull force. This helps to ensure a more constant and uniform formation in the ground when reaming through different layers and shelves of soft and hard geology as was experienced during both crossings.
Second Crossing Frac-outs
The second crossing began on March 27 at Victory Park, a few miles down the right of way from the first crossing. The new mud mixing and reclaiming system designed and built by Mears (a three-component system), specifically for use in cold weather climates, was employed on this crossing. The same challenges pertaining to the geology were encountered on the second crossing as well.
In areas of the second profile, the ground was extremely hard and again proved impenetrable by conventional tooling. Like the first crossing, a mud motor was utilized on the Victory Park crossing. A creek that was to be paralleled during the second crossing was cause for concern because of the possibility of inadvertent return of the drilling fluid to the surface, or a frac. Because of this, Mears had a contingency plan in place to contain any drilling fluid requiring silt fence and straw bails to be placed in strategic locations on the site.
As it turned out, a frac did occur close to the creek; however, with a quick response and implementation of the spill containment plan the drilling fluids were contained and cleaned up before reaching the creek. The client representative was contacted as per protocol, in conjunction with the onsite environmental representative, and the plan of plumbing a return line through the box culvert to run under the road was implemented.
As per the request of the environmental representative, steel pipe instead of a vinyl lay flat hose was used to pump the drilling fluid from the frac area back to the mud reclaimer. Use of steel pipe was to ensure that the return line would not be compromised when pumping fluids back to the drill plant and cause a spill into the creek. The pilot hole was completed without further incident. Mears made the final pull of the pipe for the Victory Park crossing on June 11.
Despite the challenges that arose throughout the project, Mears completed both projects on time and within budget.
This article was submitted by the Mears Group and edited by Trenchless Technology.