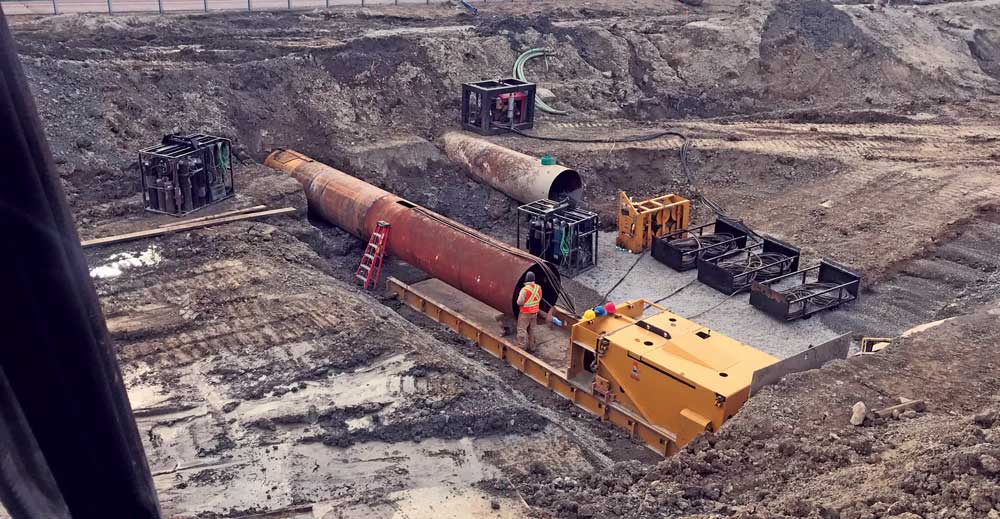
Auger Boring Expert Puts Latest Technology to Work
Jim Robinson, owner of Robinson Underground Contracting Inc. of Ailsa Craig, Ontario, has been an auger borer for nearly four decades. Over the span of his career, he’s been a sounding board for manufacturers developing new equipment, and even developed a few new innovations of his own along the way. He has also played an instrumental role in educating other contractors about auger boring methods and safety.
In addition to being well respected by his peers, Robinson is the guy contractors call when they need auger boring done throughout the Ontario Great Lakes region. His team understands how challenging soil conditions can be in this vast area created by glaciers.
“The environment throughout the region can be a bit unforgiving for performing underground installation work,” Robinson explained. “Dense boulders mixed in with clay and sand is all too common on most projects. And when it comes to auger boring in these conditions, trying to dislodge and remove heavy boulders takes a lot of patience and experience.”
The area’s ground conditions, as well as Robinson’s knowledge and passion for the job are a couple of the reasons why manufacturers turn to him when new machinery needs to be tested. One of Robinson’s most recent tested machines is the McLaughlin Workhorse 225 auger boring machine. After using it on two projects with multiple bores, Robinson gave it a high rating and purchased it on the spot.
Highway 7 Pipe Relocation Project
Highway 7 from Kitchener to Waterloo is in the beginning stages of an expansion project to help reduce heavy traffic during busy commuting times. The first step for Canada’s Ministry of Transportation was to relocate several large diameter storm sewer and water lines that run underneath the busy expressway.
RELATED: Auger Boring & Pipe Ramming the Thompson River Outfall
For the drainage bores, Robinson’s crews used the McLaughlin Workhorse 225 auger boring machine to install 48-in. casings at a distance of around 140 ft per bore. The bores were approximately 13 ft deep and pits were dug with sloped walls to give crew members more operating room and better visibility.
Compacted crush stone was used as a base, and Robinson said it was more than adequate for handling the operational weight of the auger boring machine. “The Workhorse 225 auger boring machine has 1-in. thick steel plate that runs the full width of the tracks to bring the pounds-per-square-inch down, so crush stone can be used instead of concrete, which saves time and money,” he explained. “This unit also has a slightly wider footprint than most other auger boring machines, so it’s more balanced and less top-heavy. This design helps reduce the likelihood of the machine digging into the base on one side or another as the foundation material becomes more compacted over time — a common cause of bore path deviation.”
Another feature of the McLaughlin machine that Robinson’s crew liked was that it could be operated remotely. “In the past, we’ve actually created our own remote operating systems for auger boring machines,” he said. “It’s great to see a remote as part of an original equipment manufacturer (OEM) machine. It allows our crew members to run the machine outside of the pit, which I believe reduces the risk of injury.”
While most of the bores on this project were short in distance, the crew ran into several boulders up to 48 in. in diameter. “Clearing boulders from the bore path is where experienced operators shine,” Robinson said. “To clear rocks, the operator has to slowly and precisely rock the auger back and forth from forward and reverse to loosen the rock so it can be removed. Hitting a rock is often when over-torquing the auger occurs. However, since the unit runs a Tier-4 Final engine with a flat torque curve, the auger can be run at higher rotations per minute (RPM), which reduces the risk of over-torquing and damaging the auger when coming in contact with a rock.”
RELATED: Auger Boring Market Remains Strong, Continues to Evolve
Another thing Robinson said his team appreciated about running a boring machine with a Tier-4 engine is how much quieter it runs compared to older models. “It was a lot easier to hear each other and there was much less exhaust — that is a big deal when working in a pit right next to the machine,” he said.
Highway 414 Bores
After completing the Highway 7 project, the Robinson Underground Contracting crew moved its operations north to Highway 404, where another road widening project was getting underway. The project called for approximately 3,610 ft of steel casings ranging from 36 to 60 in.in diameter to be installed.
“To expand the freeway from three to four lanes in each direction, the ditch in the middle needed to be replaced with a concrete wall,” explained Robinson. “Before the road work could start, there needed to be a few changes made to the existing utilities that run under the expressway to modify the way drainage from rain is handled. About every 0.62 miles, a drain was installed, and the lines we bored allows the water from the center to drain to the ditch.”
In addition to being well respected by his peers, Robinson Underground Contracting Inc. is the contractor customers call when they need auger boring done throughout the Ontario Great Lakes region.
For the longer-distance bores, the crew paired the Workhorse 225 with a 60-in. McLaughlin ON-TARGET Steering System (OTS). “We think of the OTS as the auger boring machine’s steering wheel,” Robinson explained. “If we’re going a short distance in good soil conditions, we may not need it, but longer bores require some steering. Being off by as little as ¼ in. within the first 20-ft casing can result in being off as much as 4 in. at the 100-ft mark. So, just like a person uses a steering wheel to drive straight down the road, we use the OTS to drive the casing straight through the soil.”
The auger boring machine was set up at a depth of 23 ft in an adjacent retaining pond being dug alongside the highway. The crew again used a compacted base of crush stone. Boulders were also an issue on this project, but in good soils, the team was able to bore the steel casing at a rate of 20 ft every 30 minutes.
RELATED: Staying on Target on New Mexico Auger Boring Project
“The Workhorse auger boring machine’s Rabbit Travel feature is what saved us a lot of time on this job,” explained Robinson. “Pulling the auger boring machine back to the start position to add a casing or pulling the auger when coming in contact with a rock is one of the time consuming and tedious parts of this job. On a normal 360-ft bore using 20-ft sections of casings, a crew can spend up to six hours just cycling the machine. The Rabbit Travel feature on the Workhorse machine reduces those cycle times. We’ve been able to reduce the time we spend cycling to just 45 minutes on a 360-ft bore.”
The crew put the McLaughlin Workhorse 225 machine through its paces and were happy with the results. “It’s absolutely amazing how far these machines have come during my time in the industry,” Robinson concluded.
Neville Missen is application engineer at McLaughlin Boring Systems.