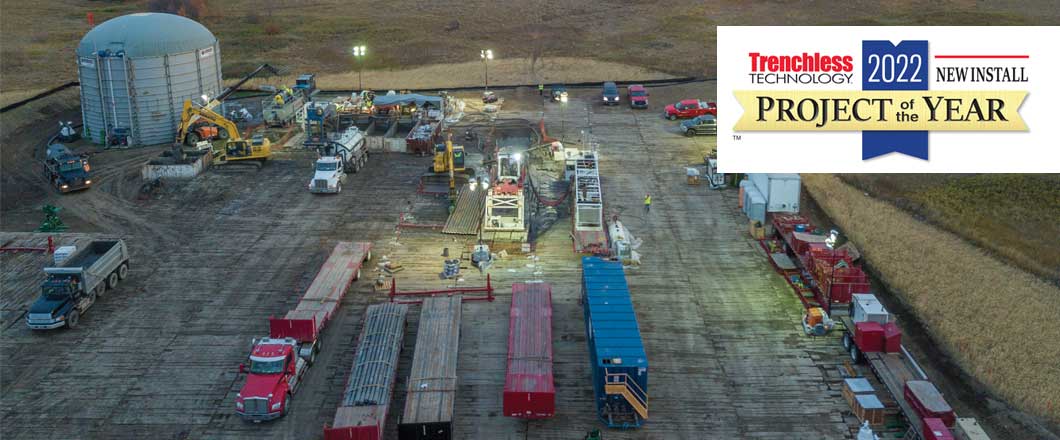
2022 Trenchless Technology Project of the Year New Installation Winner – North Bakken Expansion-Lake Sakakawea HDD
Pipeline Constructed to Aid in Reduction of Natural Gas Flaring
Three years ago, an owner, an engineer and a horizontal directional drilling (HDD) contractor came together to map out the design and construction of a 15,426-ft, 24-in. steel natural gas pipeline crossing near Watford City, North Dakota. Challenges for this project were numerous, among them how to precisely and safely cross a massive body of water, called Lake Sakakawea.
The collaboration between WBI Energy, CCI & Associates and Michels Trenchless Inc. produced a stellar and successful design, which included a 15,426-ft intersect HDD under the bed of Lake Sakakawea at a depth of more than 300 ft. Pre-drilling geotechnical investigations provided critical data of the underwater terrain and proved crucial to the drilling design and construction.
The overall purpose of the project seems simple enough on the surface: WBI Energy wanted to construct a natural gas pipeline in order to reduce natural gas flaring in the area. The route would connect WBI’s Tioga Compressor Station near Tioga, North Dakota, with the Northern Border Pipeline Co.’s mainline at a new interconnection point south of Watford City.
RELATED: 2020 Project of the Year New Installation: Bakken Missouri River Crossing
The pipeline is designed to provide up to 250,000 Dth per day of firm transportation service and included construction of approximately 63 miles of new 24-in. diameter natural gas pipeline, 30 miles of 12-in. diameter natural gas pipeline and .6 miles of 8-in. natural gas pipeline. The selected route required crews to construct the new pipeline adjacent to Tobacco Gardens, a popular, seasonal resort near Watford City.
Given the overall length, design elements and amount of skill required to complete this crossing — reported to be the longest HDD crossing involving this length and pipe diameter — the WBI Energy North Bakken Expansion-Lake Sakakawea HDD was selected as the 2022 Trenchless Technology Project of the Year for New Installation.
“We are extremely honored to have been selected as the [winner] of the Project of Year,” says Matt Smith, president of Michels Trenchless Inc. “Michels has always believed in pushing the limits of technology to deliver the best product for our customers.”
“CCI is very proud to have been a part of this project,” says Justin Taylor, vice president of engineering U.S. operations for CCI. “The success of this project relies on everyone involved, including the owner, WBI Energy, and contractor, Michels [Trenchless Inc.]. The trenchless industry is constantly pushing boundaries, doing new and exciting things. We are really honored to be included in the ranks of all of those previous and future recipients, whom I’m sure will continue to push things forward and continue to break new ground.”
Smith notes that successfully crossing Lake Sakakawea using HDD to construct this pipeline vs. designing the route around the lake resulted in significant time and financial savings, not to mention that any alternative route would have caused substantial disruption to the environment. Any reroute around the lake would have added hundreds of miles of pipeline, he says.
Project Breakdown
With HDD the only practical method of installing a crossing of such a substantial length, WBI enlisted the services of CCI & Associates in 2019 to create a design that could be used to successfully traverse the lake. After reviewing the existing site conditions, as well as recently completed crossings of the lake at other locations, a preliminary HDD crossing design exceeding 15,000 ft in length was created as a starting off point.
Taylor notes that the sheer length of the crossing was a major challenge, requiring designers to push past the boundaries of what had been completed in HDD in the past. “Physical constructability with the equipment that was available in the industry was the first hurdle to consider,” he says. “No use in going too far down into the detail of the design if it wasn’t going to be physically possible to do. We had to look at both the distance that had to be drilled and reamed, as well as the equipment and drill stem required for that to work. We needed to confirm the preliminary installation analysis and whether the pull force could be maintained below a million-pound threshold with a 24-in. pipe section at the 15,000-ft length.”
At this point, the Michels team was brought into the discussion to provide a constructability review of the proposed crossings; Michels was familiar with the terrain and lake due to recent experiences in drilling under it, albeit for a different owner and at a different location along the lake. Design amendments were made, based on those collaborative conversations and that familiarity, including to the drill geometry for some of the radii and to the exit angle to better accommodate Michels’ pipe thruster, which was intended to be set up on the exit point. By bringing in all three parties before completion of the final design, everyone approached the construction phase on the same page.
“[WBI] was open to early involvement by the contractor and working hand-in-hand to come up with a feasible, good plan,” says Jeff Mueller, senior vice president of Michels Trenchless Inc. “We strongly feel the success of a project of this magnitude hinged on the early collaboration between the contractor, engineer and owner. Working together from the earliest planning stages mitigated risk and optimized safety and efficiency.”
“That collaboration continued through the drill,” Smith adds, noting this example: “We had a redesign on this crossing to get a better designed depth, which was another critical point of why we wanted the boreholes to be deep. Our onsite supervision worked directly with CCI and [WBI] to make sure we were able to quickly turn around a different elevation drill design.”
“Working 24/7 is stressful on the construction crews, especially on such a high-profile crossing,” Mueller notes. “It also requires attention to details, coordination and logistics for a project this size. The crews worked flawlessly together with the owner and engineer to solve the many problems head-on as they occurred throughout project. The turnover between shifts was critical to the following shift to understand where we were in the process of the drill and ensure unnecessary problems did not arise.”
The design produced an intersect method application for the pilot hole that required two 1.2 million-lb HDD rigs (built in-house by Michels) positioned on either side of the lake. After the pilot hole was successfully complete, Michels reamed the hole in multiple passes using a 24-in., followed by a 36-in. hole opener. Pullback commenced on Oct. 23, 2021, and by midday on Oct. 25, the NPS 24 product pipe was pulled through the reamed hole, successfully completing the 15,426-ft crossing. A Brownline gyroscopic steering tool was used for guidance during the pilot hole to ensure everything was perfectly lined up due to the impossibility of laying surface coils on the water.
This was a true water crossing, the CCI and Michels team point out, noting that more than 13,000 ft of the crossing took place under water — making the drill a huge undertaking and challenge. Because nearly the entirety of the crossing was under water, assurance that there was enough depth underneath the edge of the water on either side was critical. Michels also used its proprietary threaded casing on the entry and exit sides to stabilize unconsolidated layers closer to the surface, as well as maintain drilling fluid returns and hole conditioning.
Mueller also notes that Michels Trenchless utilized Michels Pipeline to handle the pipe support needed for the project. Laying out the 15,000-plus ft steel pipe needed for pullback was tricky but was able to be done in two long sections, one of 426 ft and one of 15,000 ft.
Project Challenges
Projects of this size bring with them layers of complexity that necessitate an incredible amount preplanning and coordination. As stated earlier, the project site was adjacent to a popular, seasonal resort so no part of the project could impact that environment. The pre-drilling geotechnical investigation, which would provide the blueprint for how to conduct the HDD, included a series of six overwater geo-boreholes, vertically drilled from a barge, as well as three on land on either side of the lake. The boreholes were drilled more than 300 ft below the lake’s surface and, though a time-consuming effort, the data collected enabled crews to maintain the drill path in optimal strata and avoid coal zones, as well as completing detailed hydrofracture analysis to ensure risk of fluid release to the lake was minimized.
“The [geo-boreholes] did show some significant coal seams in and around the proposed depth of the drill path, which can be an issue for drilling and can be a conduit for drilling fluid loss” Taylor says. “A crossing of this length to come across a coal seam and start losing fluids would kneecap the rest of the installation, as you can’t have that good circulation of fluids back to the entry [point] to make sure you are cleaning out that hole.”
Optimization of the product pipe wall thickness and evaluation of buoyancy control were also critical components in the design of the crossing so that anticipated pull forces would be within the range achievable by the largest HDD rigs available. Designers determined whether the pipe needed to be filled with water during pullback to counteract the buoyancy of the pipe and reduce that installation force. WBI decided it wanted additional wall thickness inside the pipe for added safety and extension of the life of the installation.
RELATED: HDD Used to Untap Energy Resource in the Bakken
“We ended up going with a pretty thick-walled pipe, at 1-in.,” Taylor explains. “With that thickness, the additional weight from that was suitable to counteract a lot of the buoyant weight of the pipe this size. So, filling the pipe with water wasn’t needed.”
He adds that this decision also simplified the pullback operations for the Michels team, as well, by not having them deal with the logistics involved with a buoyancy control plan on the crossing.
No Limits
Successfully breaking the 15,000-ft plateau for an HDD crossing at this diameter across such a swatch of water continues to show how far HDD has come from its early years or even the last decade. This milestone project shows how tenacity, perseverance and experience all play a role in such a positive outcome.
“The industry has now seen that a project of this magnitude, of these kinds of lengths is possible,” Mueller says. “From [our] standpoint, we don’t think we are anywhere near the limitations of HDD. Getting a project like this performed, nearly flawlessly, very efficiently and highly successfully, really does open opportunities to continue to design and complete these kinds of challenging projects forward. It allows the development of solutions to what was previously thought of as an unachievable project.”
Owner: WBI Energy
Engineer: CCI & Associates
HDD Contractor: Michels Trenchless Inc.
Manufacturers/Suppliers: Brownline, CETCO, and Groundwater & Environmental Services Inc.
Sharon M. Bueno is the editor of Trenchless Technology.