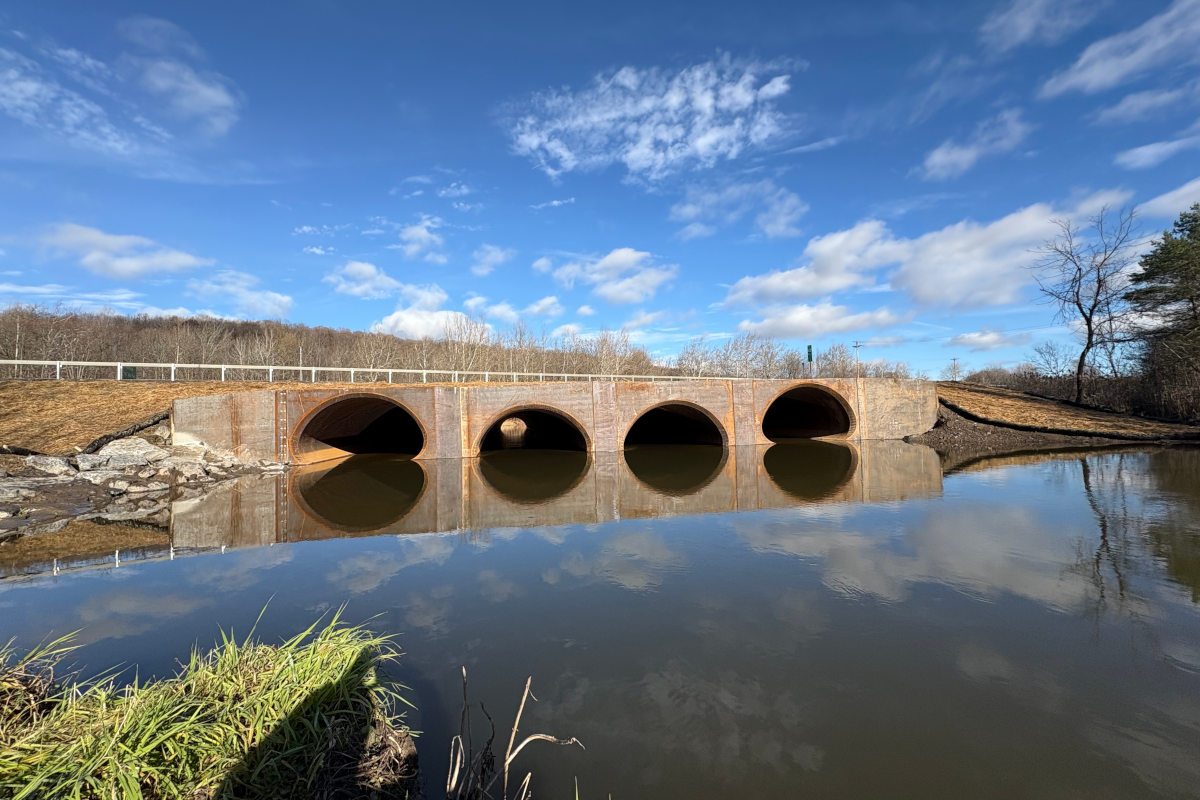
Using Sliplining to Rehab Culverts in New York
InfraSteel, a division of Precision Pipe & Products, recently collaborated with project design engineers to provide maintenance free solutions. These solutions were for three failing culvert bridges at two project sites in Upstate New York.
These designs met both the hydraulic and structural requirements for the sites. They included a calculated design life of 70 years.
By utilizing InfraSteel’s Flow Bell inlets, ¾-in. Steel Liners, Headwalls and Wing Walls, the rehabilitated culvert bridges now meet the design requirements for a replaced structure.
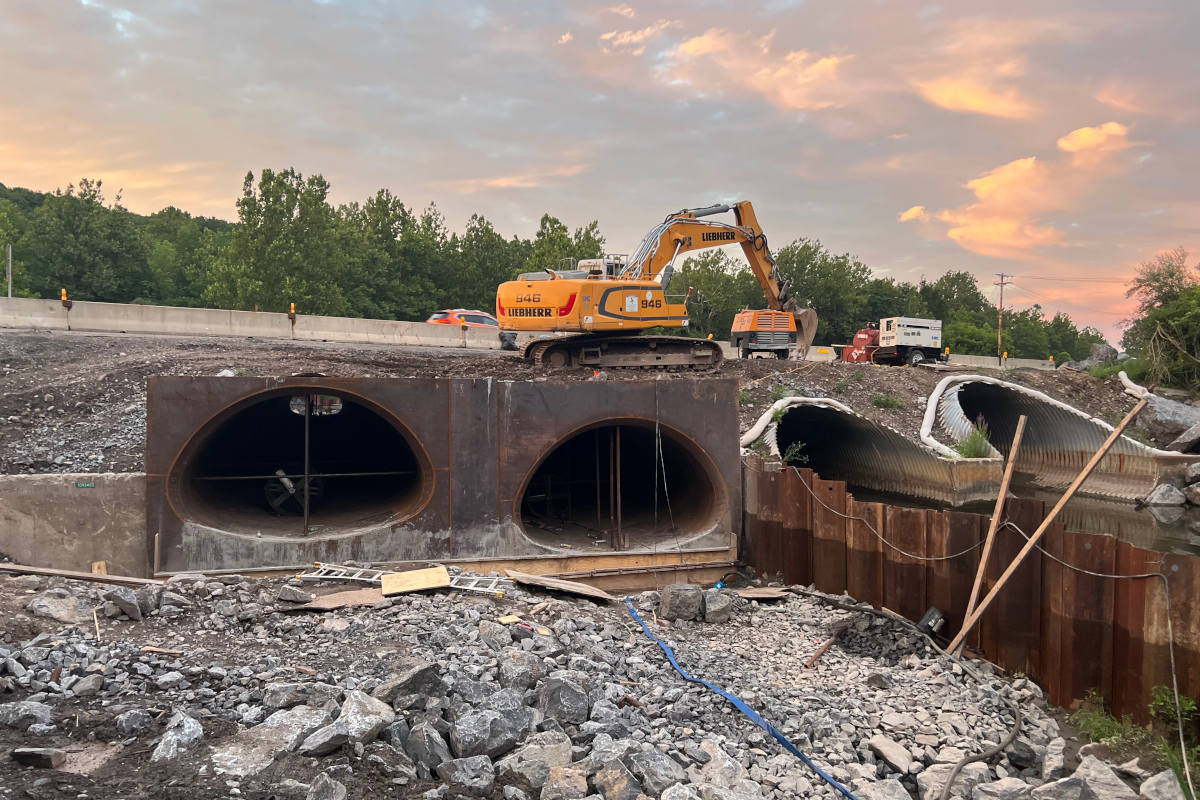
Camillus, New York Culvert Project
The first site was under Route 5 over Nine Mile Creek in Camillus, New York, a heavily traveled location. The existing culvert bridge consisted of four each 215-ft runs of 184-in. X 124-in. Arched corrugated metal plate culverts. The structure is in a floodplain where regulating agencies dictate that the design cannot result in a rise in the backwater.
The project designers evaluated all approved liner products in their system. They also evaluated a replacement bridge for the failing site. The estimate for the new bridge was approximately $7 million. This would result in significant delays in construction and traffic. This alternative was quickly ruled out.
It was determined that InfraSteel’s 169-in. ID X 105-in. ID X .750 Wall Arched liner maximized the cross-sectional area of the culvert barrels. This was relative to the other lining options. It also achieved the HL 93 loading requirements for the site. With the addition of InfraSteel’s Flow Bell inlets, consisting of a 1.5:1 (33°) bevel, the InfraSteel liner was the only rehabilitation alternative that lowered the headwater for each analyzed storm event.
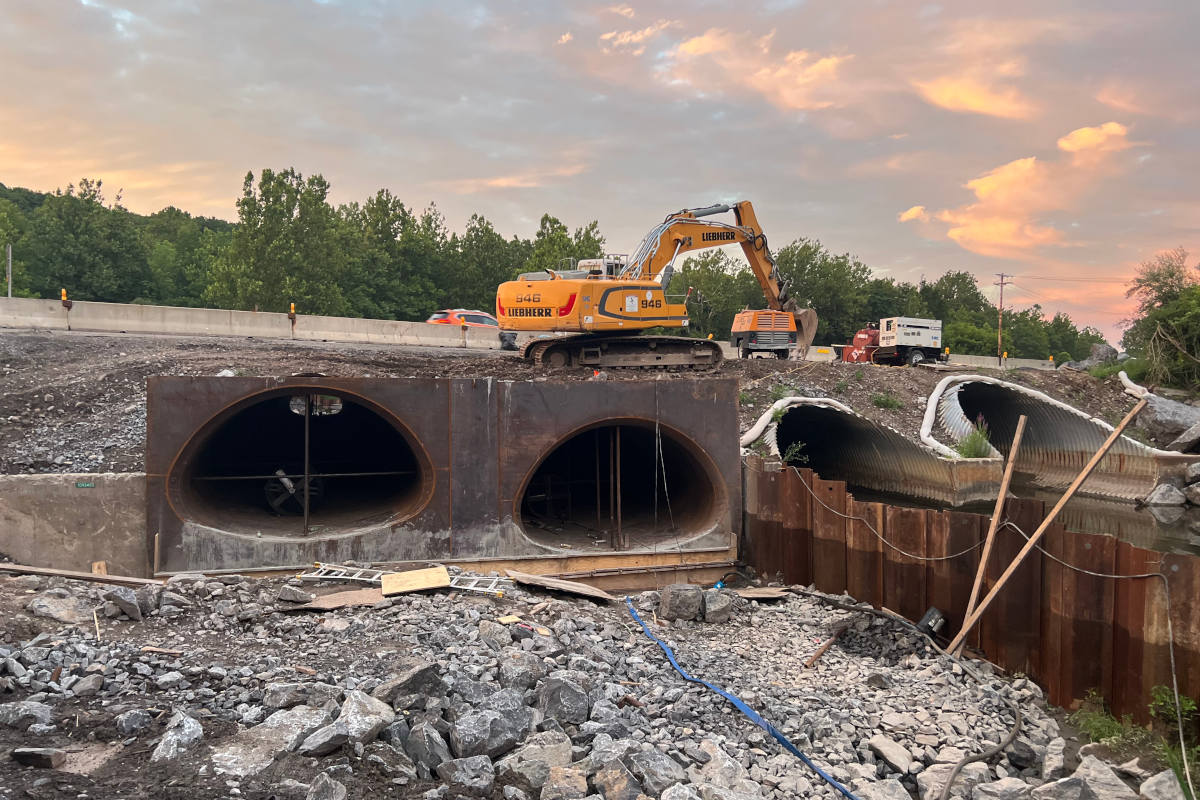
Sliplining Work Commences
The project owner put the contract out to bid. Slate Hill Constructors of Warner, New York were the lowest bidder at $4,633,691.00. Slate Hill ordered 860 ft of the liner with Headwalls in January 2024. The Liner, Headwalls, and Wing Walls were delivered to the site between April and September 2024.
Slate Hill worked on lining two culvert barrels at a time, while using the other two culvert barrels for water diversion. The liner sections were welded together and pulled inside of the existing structure with a Komatsu 360 excavator.
The excavator pulled the run lengths of 241,000 lbs into position inside of the existing structures. The end bevels of the liner sections were configured. This was done so that the bottoms were welded from inside of the liner while the sides and top were welded from the OD.
Each liner section had 2-in. grout ports positioned strategically so that grouting hoses could be attached from the ID. 100 psi cellular grout was pumped into the annular space once the liner run was in position.
The water diversion was then rerouted through the newly lined barrels, and the process was started on the remaining two barrels. The project was completed in October 2024 without traffic interruption. The final construction cost was just below the bid estimate.
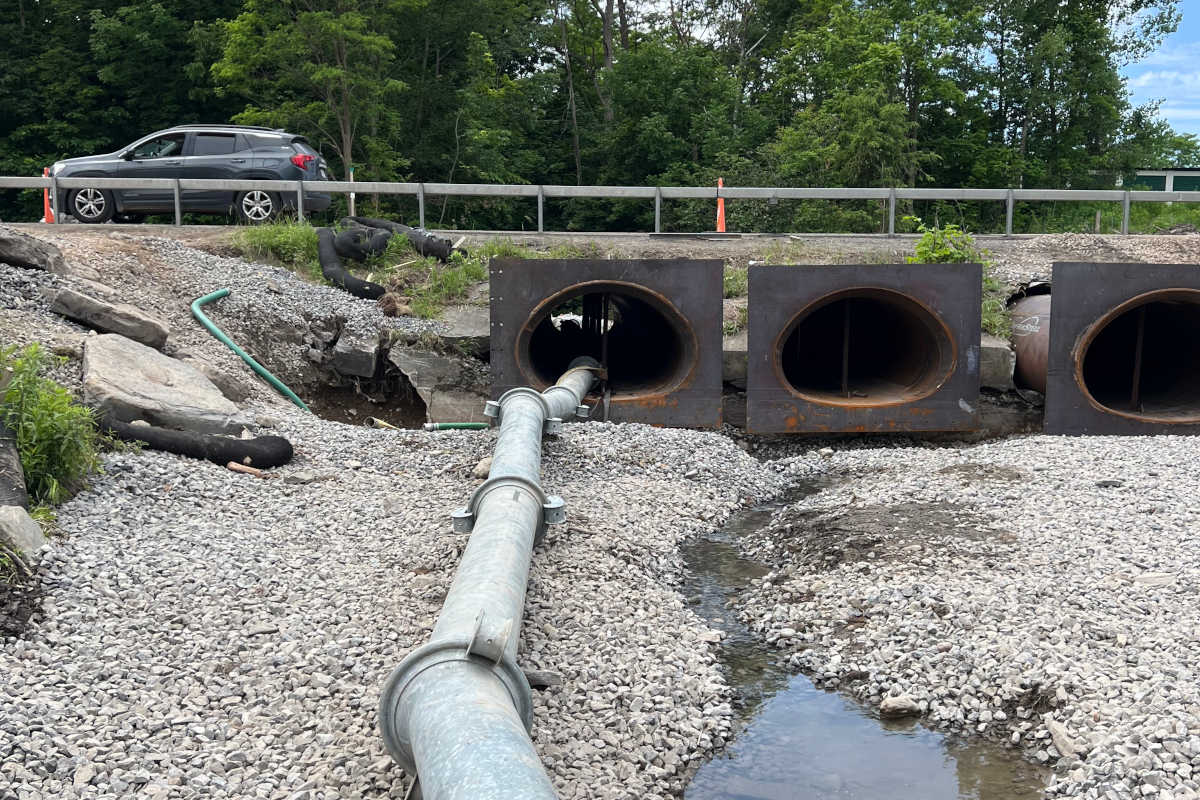
Pulaski, New York Culvert Project
At the same time designers were working on the Camillus site, they were faced with an emergency location under I-81 between the Pulaski, New York exits. The failing culverts are located on a tributary to the Salmon River. This is a salmon passage.
The designers once again evaluated all approved culvert lining systems that were available to them. All of the products evaluated had liner thicknesses that reduced the cross-sectional area of the culvert ID.
However, the high yield and tensile strengths of InfraSteel allow for thinner wall thickness. This achieves the HL 93 loading requirements, providing a minimum loss of cross-sectional area. The I-81 culverts also included InfraSteel’s Flow Bell inlets, which were incorporated into the Inlet Headwall design. This lowered the headwater relative to the existing structure, satisfying the environmental hydraulic requirements.
The I-81 northbound lanes consisted of three existing 150-ft long 84-in. X 61-in. CMP culverts that were each lined with 74.25-in. x 50-in. ID X .750” Wall liner. The liner for these sites also met HL 93 loading requirements and were designed for a 70-year life span. The northbound culverts also passed under an adjacent service road, making them 79 ft longer than the southbound lanes.
Time was of the essence to complete construction of the northbound structures for the 2024 fall salmon run.
The I-81 southbound lanes consisted of three 71-ft long barrels of 84-in. X 61-in. CMP culverts. Each were lined with 74.25-in. ID X 50-in. ID X .750-in. InfraSteel Arch liner sections. Suit-Kote Corp. of Cortland, New York had the Emergency Contract at the time and were responsible for construction at this site.
Suite-Kote was experienced with InfraSteel installations and decided to set up in the I-81 median. They decided to push the liner under both the southbound and northbound lanes from this one location. Stream water diversions were handled with coffer dams and pumps that passed water through the adjacent barrels.
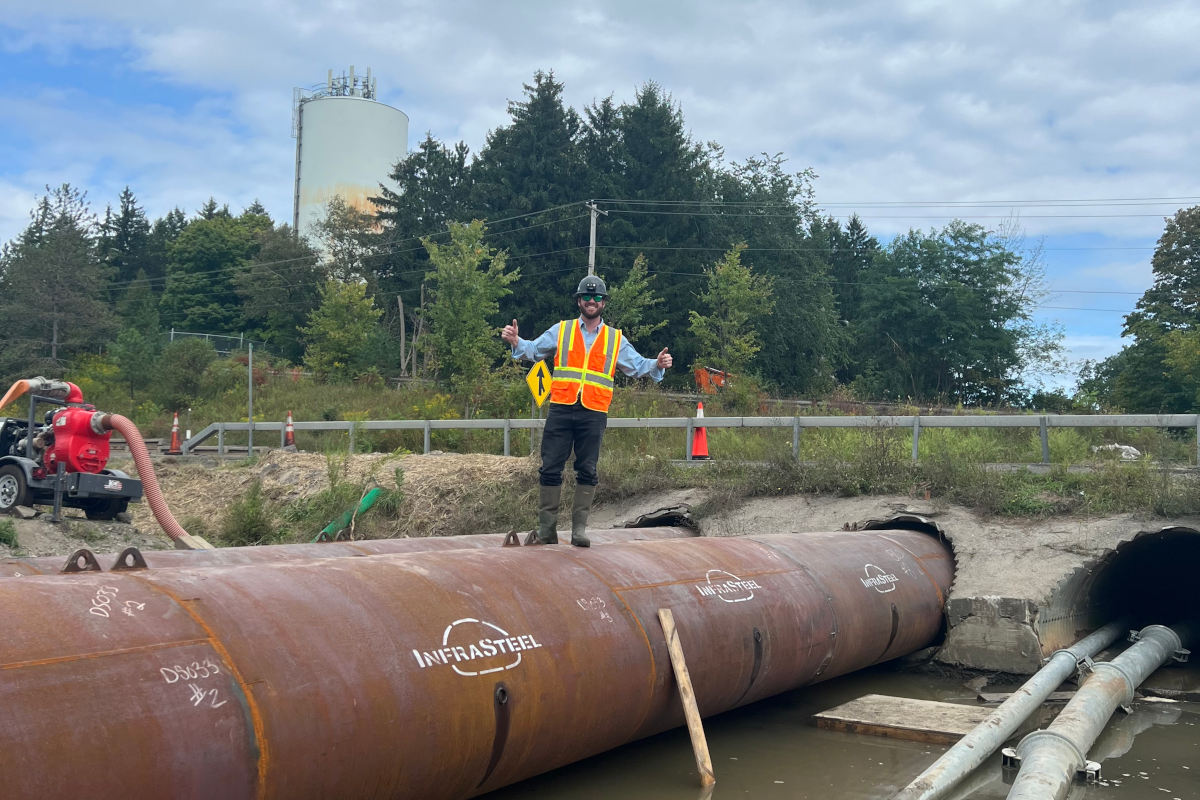
Sliplining Success
The construction time for lining and grouting was three months for both lanes. However, the work was completed in two stages. InfraSteel was onsite at the completion of the project and witnessed salmon running through the rehabilitated structures. The project was considered a success. It was installed without disruption to the traveling public and the 2024 fall salmon run.
We believe that a properly designed slipline project is a method of installing a new structure at the failing site. There are some, primarily on the environmental side, who advocate for replacement of these failing culvert structures by open-cutting roads and diverting traffic.
This ideology does not consider disruption to the traveling public. It does not consider delays experienced by emergency vehicles, nor the increased project costs. In instances such as these two, it’s imperative that all alternatives be investigated. This must be done to choose the best solution for each given site.
Cullom Walker is co-founder at InfraSteel and partner at Precision Pipe & Products.