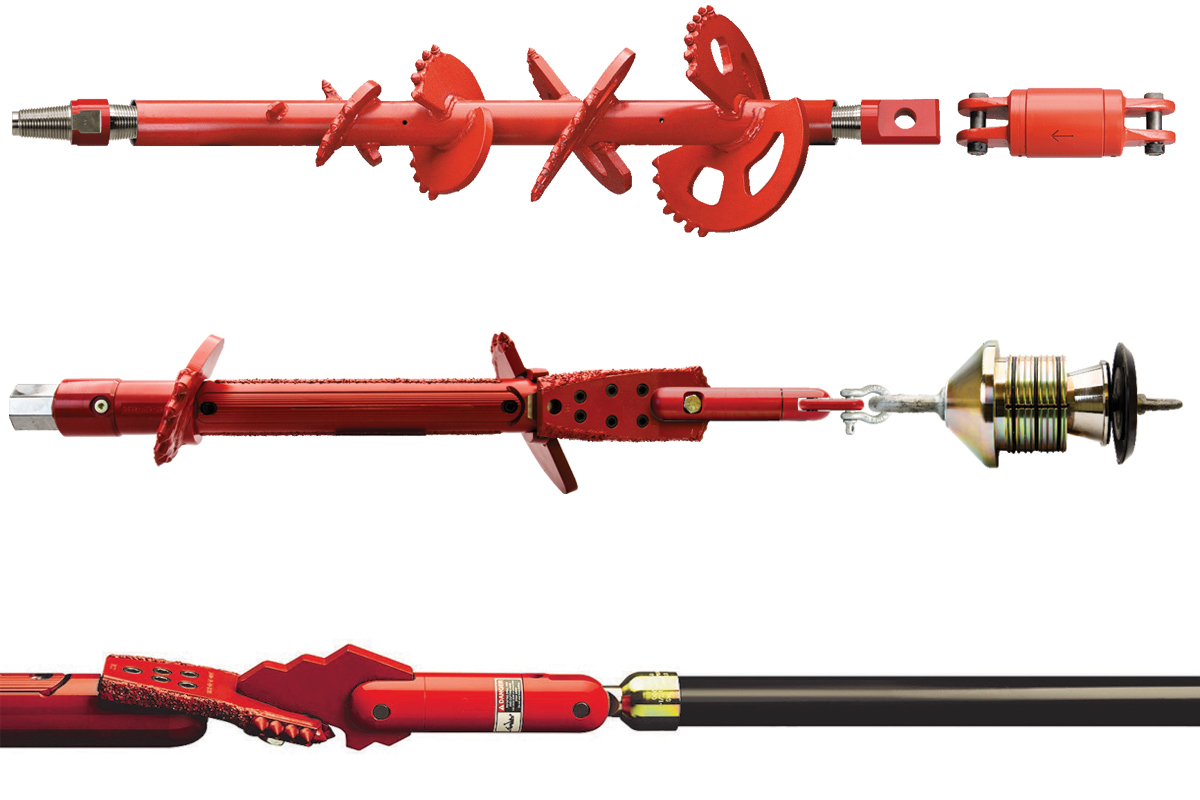
Understanding HDD Pullback Options
Comparing Conventional, Direct and Newer HDD Pullback Methods
Horizontal directional drilling (HDD) pullback methods plays a critical role in crew efficiency, project timing, and tool performance. While pilot bore planning often takes priority, selecting the right pullback setup is equally important.
This article explores the three primary HDD pullback strategies — conventional setup, direct pullback, and non-threaded connection systems — each suited to specific job conditions. Understanding these options can help improve decision-making and enhance overall jobsite productivity.
The Conventional Setup: A Trusted Method
Overview
The conventional pullback setup typically involves several threaded components, which may include:
- Threaded Backreamer – Attaches directly to the drill string to enlarge the bore path, creating sufficient clearance for the product pipe.
- Threaded Adapters or Pulling Eyes – Serve as connectors between the backreamer, swivel, and product pipe to ensure proper fit and compatibility across the entire pullback assembly.
- Swivels – Available in both threaded and bolt-on designs, swivels are often used to prevent the product pipe from rotating during pullback, which can help protect the pipe and maintain bore alignment.
In a conventional setup, after the pilot bore bit is removed, the transmitter housing is also often removed to be replaced with reamer and pullback hardware, typically requiring breakout wrenches and torque control tools. In uncommon applications, customers may wish to locate during pullback, which would require specialized tooling.
Where It Works Well
This method is the standard for medium to large HDD jobs, especially when encountering variable soil conditions or requiring upsizing through staged reaming.
Strengths
- Threaded connections provide compatibility with a wide range of tooling options that span various size ranges.
- There are industry-standard thread standards, such as UN or API, that help bridge the vast array of custom or OEM-specific proprietary thread variations.
- Provides robust tensile strength through threaded connections throughout the drill string.
- Supports multi-pass reaming and varied ground profiles.
Considerations
- Threaded joints can require more time to assemble and disassemble
- Proper torque and thread maintenance are essential
- Entry pits may need to be larger to accommodate tools and connections.
- Thread designations can vary significantly between manufacturers, necessitating adapters that introduce potential break points in the drill string.
Direct Pullback: Fast and Straightforward
Overview
Direct pullback is a simplified approach in which the drill head is left in place after the pilot bore, and the product is attached directly to it (hence the term direct pullback), typically using a pulling eye or integrated swivel. This approach skips intermediate tool changes and often eliminates the need for a separate reaming pass.
Where It Works Well
Direct pullback is commonly used in short bores through predictable soils, such as sandy loams or compacted clays. It’s ideal when the pipe size is small to moderate (about a 12-in. hole or smaller), and the bore path has limited complexity.
Strengths
- Requires minimal equipment changes, which increases productivity rates
- Reduces the number of adapters needed on hand
- Bore is a tighter space because drillers don’t need space for breakout
- Easy to train and execute with smaller crews
Considerations
- Your pilot tooling (housing and bit) must be compatible with direct pullback accessories.
- Has limited flexibility to upsize the reamer staging – usually not ideal for larger jobs
- Reamer-style options are limited and less adaptable to layered or abrasive ground conditions
Non-Threaded Connection Pullback: Rising Popularity
Overview
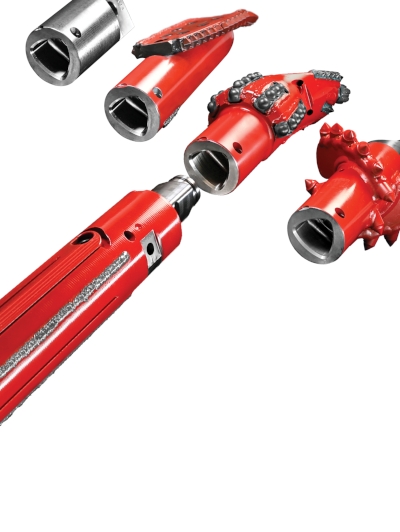
Non-threaded connection systems are an emerging class of tooling assemblies that focus on reducing changeover time and streamlining pullback operations. These systems often use mechanical interlocks, coiled pins, or spline-based couplings to securely fasten components without requiring traditional threading.
One example is Melfred Borzall’s Tri-Con System connection, which has gained traction for enabling tool changes without the use of torque tools. Another approach utilizes a spline connection system, secured with pins, that allows quick transitions between the pilot bore, reaming, and pullback phases.
Where They Work Well
These systems are ideal for urban utility installations, repetitive service bores, or projects with tight access areas. They are particularly beneficial when minimizing downtime and manual tool handling is a priority.
Strengths
- Significantly reduces transition time to a reamer for pullback
- Eliminates issues associated with galling or seized threads
- Allows for compact entry pits—some systems work in pits as small as 18 in.
- Offers strong tensile strength capacity needed for some pullback jobs
Considerations
- Compatibility may be limited to tools designed for that system’s connection style
- Initial investment in adapters or system-specific components may be required
- Operators may need training on installation and retention methods
Final Thoughts
Choosing the correct HDD pullback method isn’t just about tooling — it’s about aligning your approach with the specific requirements of the job at hand. Whether working on a short residential bore, a commercial utility install, or a longer multi-pass pipeline route, contractors benefit from having multiple connection strategies in their toolkit.
- Conventional threaded setups provide proven strength and adaptability across most bore types.
- Direct pullback offers a minimalistic and fast-track solution for simple installations.
- Non-threaded connection systems represent a forward-thinking option for contractors seeking to streamline workflows, reduce handling time, and boost overall jobsite efficiency.
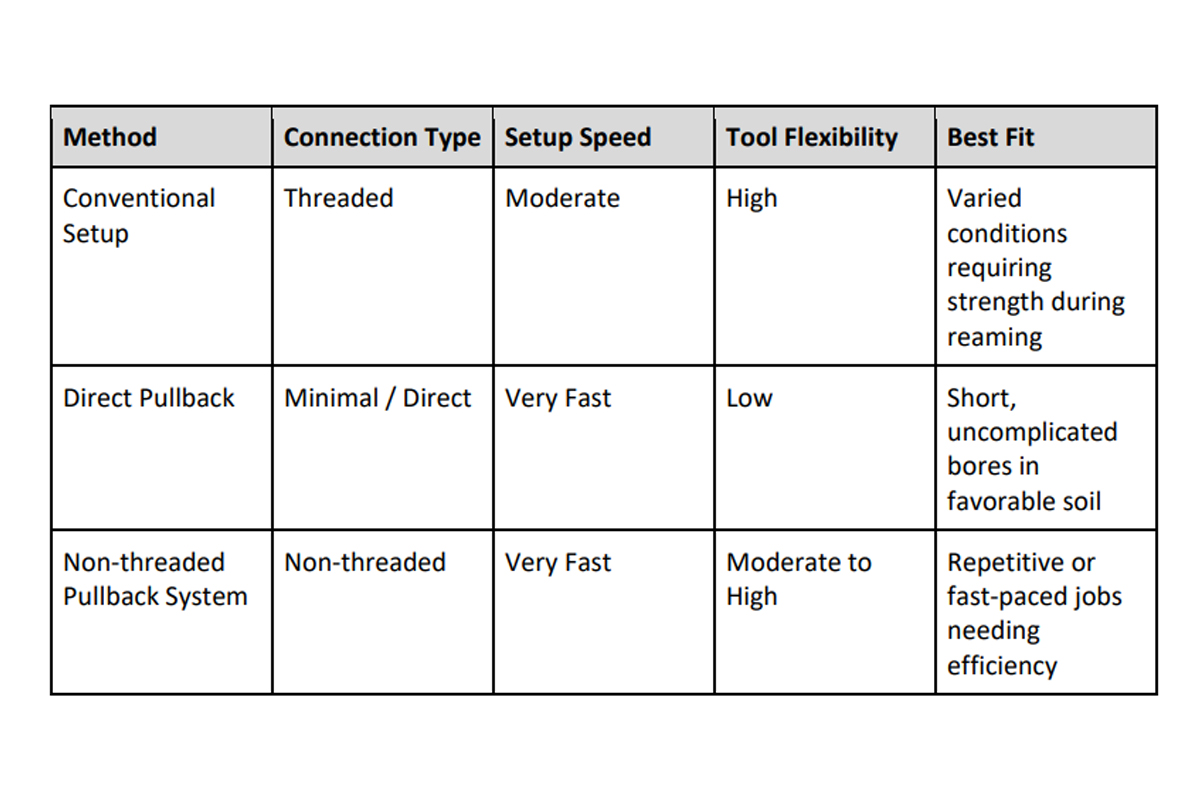
As HDD continues to evolve, the ability to flex between these configurations — or combine them with system-specific adapters — empowers operators to meet a wider range of challenges with greater speed and confidence.
Comparing HDD Pullback Methods
Each pullback option brings unique strengths to the table. Rather than viewing them hierarchically, they are best understood as complementary options — each suited to particular project conditions, time constraints, and crew preferences.
Joshua Parker is director of marketing and eCommerce at Melfred Borzall.