Trenchless Methods Finding Success in South Africa
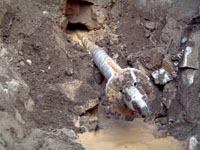
South Africans can be avery hard and suspicious people, which is totally understandable for historicalpolitical reasons; therefore to change a mindset is somewhat of a majortask.
Using the term hard is not used lightly; not only are the peoplehard, but the conditions are extreme as well. This article details a hydrogengas line project — The Overland Hydrogen Gas Pipeline — that took place June2003 to February 2004 in the Johannesburg area at elevation levels ofapproximately 1,752 m (5,746 ft). The purpose of the project was to transfer gasfrom the supplier to the end-user. Eighteen crossings were initially planned,pulling back 114-mm steel pipe, but by the end of the project that totaldoubled.
It is somewhat unique as all the people who were involved hadnever directionally drilled in such conditions before or used guided rockdrilling systems. And to make things even more surprising, they had a 100percent success rate.
Drilling under roads has been around for sometimein South Africa. This is a fairly crude yet somewhat effective method ofdrilling a hole 8 m under a road and then pushing the product in by hand. Thismethod is not steerable; you just aim and drill. It is still used today and insome cases is quite cost-effective.
However, there is an increasingdemand for the use of trenchless technologies in South Africa. As the businessand residential communities throughout the country push for more pipelineinstallations under both manmade and natural obstacles to upgrade theinfrastructure, ways to meet this demand must be considered that will be lessinvasive and intrusive for the general public.
HDD has now presenteditself in South Africa as a trenchless method of installation, giving a viablealternative to the common pipe jack. Not only can this method of installationinstall both sleeve and actual product over short distances, but with thetechnology that TRG International Pipeline Co. (Pty) Ltd. has in South Africa,contractors are able to install product up to 500 m.
Formed in 2002, TRGInternational is a civil engineering contracting company that specializes in thetrenchless technology market in South Africa, Europe and the Arab Peninsula. Thecompany handles HDD, impact moling, pipe ramming, auger boring and pipe jacking.Its founders, Steve Edwards and Andre Wood have a combined 31 years ofexperience in the trenchless market.
With the myth attached to directional drilling — that it is only suitable fordrilling short bores in soft ground — dispelled, TRG is constantly breaking newground in this market, whereby making pipe installation cheaper, faster andstill having the accuracy to install sewer grades. Length is not a factoreither, as TRG has installed product pipe of 450 mm in diameter at lengths of1,000 m and depths of 167 m.
With this in mind, the consulting engineersand project owner hired TRG to install sleeve pipes under roads and railwaylines, in towns and under highways as part of a 110-km gas line project betweenthe Free State and Gauteng Province. A Vermeer D50x100a drill was used for amajority of the crossings, with a smaller D24 unit used for five ofthem.
In preparation, TRG purchased privately a number of INROCK holeopeners and reamers. Starting in the City of Vanderbijl Park and ending in theCity of Springs, the project covered approximately 110 km, crossing 33 roads,rails and highways. From a geological standpoint, TRG crews encountered sands,expansive clays, boulders, mudstone, dolerite, basalts, dolomite, bolderformations, sand stone and quartzite.
With its in-house geotechnicalengineers and the foresight of what was to come, TRG invested in the latesttechnology, namely mud motors and HDD rock hammers, to undertake the project.With its expertise in HDD, time taken to do a 167-m bore (the longest of all thecrossings) was just five days, and an average rock crossing of approximately 60m took on average four days.
With penetration rated on the pilot bore of15 m an hour (including steering) through solid rock, like the quartzite andsand stones in the City of Heidelberg. Complex steering methods were undertakenby the teams (steering both horizontally and vertically at depths of 9 m deep)of lengths in the order of 140 m.
The project initially started with 18crossings and ended up with a total of 36. A proposed bore plan was done foreach crossing, calculating the bend radius of both the product and the sleevethat was to be installed, as well as trying to reduce the distance from the rigto the horizontal section where the pipeline begins.
Beginning in theCity of Vanderbijl Park, 10 crossings were completed. The geology varied fromred sands to expansive clays over this portion of the contract. The longest bore(167 m) involved crossing the R59 Highway, as previously mentioned, in fivedays; the actual installation of the sleeve took a little over three hours. TRGdid a forward reaming operation under a railway line; the depth of the bore wasapproximately 9 m deep.
From this point, TRG moved south across thecountry toward the City of Heidelberg. The geology here varied from mudstone,sandstone, ferrocrete and boulders. Upon entering Heidelberg, sandstone andquartzite were encountered. By this time, TRG had imported a Halco mud motor;the first of its steerable, rock drilling tool. Andre Wood went to Europe to seethe latest technology — a directional air hammer from Halco that was to beshipped to South Africa.
From this point, the focus was on the City of Heidelberg, whichhas a reputation for rock — and lots of it. Eight crossings were done inHeidelberg. With a specialist driller who was brought to South Africa to trainTRG’s South African teams with the latest technology, the first steerable, rockcrossing was done. On the first day, 70 m of the pilot bore was done; on thesecond day, the first forward reaming was done, increasing the initial pilotbore diameter from 133 to 298 mm. Then the product was installed using aconventional hole-opener.
It was believed that the next crossing would bea 137-m, solid rock crossing, that would involve the drilling of a compoundcurve — drilling along a pre-designed alignment, involving change of directionon both the horizontal and vertical scale — and reaching the desired point (atrench). To date, TRG is of the opinion that a South African company has neverattempted this method of installation.
The third crossing seemed to befairly straightforward, but as usual, things are not as they would seem. Onexcavating the exit and entry pits, crews found that on one side there was solidrock, and on the other side, boulders with loose rock and little matrix werefound.
The pilot bore drilled fine, but the reaming took crews bysurprise: over the backfill portion of the crossing, the drilling fluid wouldnot support the bore. The crews had complete fluid loss, which in the HDDindustry is fatal. Going back to the traditional method of using a hole-openerproved to be problematic. In this process, two hole-openers were destroyed,leaving TRG with a major problem — broken tooling downhole. With no geotechnicalreports having been done, TRG had no idea as to where the backfill started orended or even how deep it went.
Now the options TRG had was to eitherconduct probe drilling or consider changing technology to finish the crossing.Probe drilling would not have been cost-effective and would have resulted in aloss of valuable time. TRG decided to use pipe jacking (using its owncustom-built machine), a more expensive operation, as well as moretime-consuming (which at this stage of the contract was vital). So two teamswere deployed to do just that, while the drill rigs moved on to the nextcrossings.
It was onward through the dolomite areas to the City ofKwaThema and finally into Springs. These areas were somewhat of a challenge,with seven crossings being completed and thus ending the HDD portion of theproject.
As this was the largest HDD contract ever done in South Africato date, the following items were of paramount importance in the design,execution and success of this work:
• Engineers understanding thetechnology
• Design of bend radii
• Limitation of technology
• Locationof services
• Drilling fluids (bentonite)
• Drilling equipment and itslimitations
• Downhole tooling
• Bore plans
• Easement/right of wayaccess
• Setback distances vs. depth
• Ground penetrating radar (services& geology)
• Service location
What made this project successfulwas the commitment by the project owner and the consultant engineers. They areto be congratulated for having the foresight and the experience within theindustry to acknowledge the method of HDD; and as is TRG International PipelineCo. for dispelling the myth that HDD could only be used for small road crossingsand small diameters and is not a serious contender for the well established butaging technologies that are still used today within South Africa.