Talking Lateral Cutters
August 1, 2008
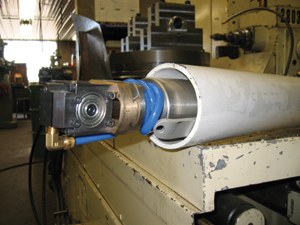
A lateral cutter that can handle the wear and tear of cutting through the new liner in a variety of pipe and pipe size is crucial to this process.
Simply stated, a lateral cutter is a remotely controlled unit that is used to reinstate the lateral connections in the renewed pipe. Its function is clear cut: The cutter is inserted into the mainline and advanced toward the lateral connection that is located via a coordinated measurement. The cutter makes an initial hole to relieve any flow that may have accumulated in the lateral and to help remove the remainder of the lining material from the lateral opening so the lateral can be reconnected.
These are busy times for rehab contractors and trying to touch base with contractors who handle lateral work to chat a bit about the cutter tool is nearly impossible because they are typically on the jobsite. Trenchless Technology contacted a few to ask them some basic questions about this tool that is so vital to reconnecting the lateral, post-rehab of the sewer pipe.
“[Lateral cutters] are an integral and critical piece of equipment in the lining industry, as all forms of trenchless rehabilitation require lateral reinstatement,” said J.T.V. Inc. president Joyce T. Velitschkowski, a 17-year, St. Petersburg, Fla.-based trenchless contractor who handles cleaning, inspection and CIPP work. “Before the development of lateral cutters, only pipe segments with no lateral connections could be reinstated via trenchless lining. With the evolution of lateral cutters, sanitary sewer pipe with several connections, smaller diameter pipe and thicker liners are all able to be reinstated at a faster pace and with a more accurate cut.”
Lateral cutters are big business these days, keeping lateral manufacturers busy to keep up with the orders. What are contractors looking for when shopping for a cutter? For contractors like ABEL RECON president Troy Abel, a contractor who specializes in structure and pipeline evaluation, rehabilitation and corrosion control, it’s the cutter’s reliability and ease of operation.
“A cutter that is maneuverable and that can perform with ease during operation is essential,” Abel said. “Just being able to cut through is not enough.”
Velitschkowski has similar concerns when looking at a new cutter and seeks out a cutter that can provide durability. “Downtime is loss of production and revenue,” she said. “Durability and ease of repair in the field is critical.”
One mistake that some contractors make in this type of purchase is fixating on the price and then signing on for a cheaper tool to save money. Bad move, contractors say.
“Some may purchase the least expensive cutter and [later] find that it does not meet their overall needs,” Abel said. “Or [they] purchase a cutter that is not best suited for their particular application.”
Velitschkowski echoed those thoughts, saying that the quality of the tool is the most important consideration. “[Some contractors] only look at the lowest price,” she said and that’s just not the way to go.
“You get what you pay for.”
Technological Improvements
As with any technology, evolution is key to its longevity in the market. For lateral cutters, its design and the materials used to create them have become keys to their success.
“New materials have become available over the years. These materials make the cutters more durable and able to wear longer,” said Jessica Bowman, general manager of operations with Bowman Tool Co., a leading manufacturer of lateral cutters based in East Berlin, Pa. As an example, she points to her company’s own Dominator line of cutters, which have evolved from a unit containing numerous internal parts to having just eight internal moving parts. She noted that the improvements to the cutter tooling over the years have been done to increase jobsite efficiency.
Velitschkowski also pointed to the size and durability as key advances to the cutter tooling in recent years. “Early lateral cutters were big, heavy and too complicated to work on in the field because they had too many internal operating parts, weak soldering parts and water leaks,” she explained. “Most of these issues have been resolved with the latest developments in cutter design. Cutter controls are also more precise and compact.”
Abel noted that some cutters have been made to be a little heavier to be more stable, while others have trimmed down the number of parts.
The lateral cutter is put through a grind on a daily basis so proper care of the tool is critical to extending its life. It may sound extremely simplistic but it can not be said enough that proper maintenance is essential — and that includes an annual manufacturer inspection to reduce any in-the-field repairs.
“A properly maintained cutter can last through a lot of cutting,” Abel said. “Checking for any excess wear or tightening any loose parts can eliminate an early re-build.”
Basically it comes down to commonsense. Bowman noted that one of her company’s customers cut 2,200 laterals in 77,000 ft pipe using the same cutter — that’s a lot of cutting for one tool. The care of the tooling cannot be understated.
“As with any mechanical device, servicing your unit — cleaning, greasing and lubricating — will extend its life,” Bowman said. “Further, the use of some types of bits can shorten the life of the cutter’s motors by creating too much resistance force. The best advice is to use the machine with sense and care.”
Sharon M. Bueno is managing editor of Trenchless Technology.
Tags: Lateral Cutters