
Same Day Water Main Rehabilitation in Deep River, Ontario
The Town of Deep River, Ontario is situated on the Ottawa River. It is approximately 200 km northwest of Ottawa along the Trans-Canada Highway.
In 1944, the Canadian federal government began planning for the town as part of the Manhattan Project. This plan was to house employees of Chalk River Nuclear Laboratories. Chalk River, along with Los Alamos and Oak Ridge, was pivotal in the nuclear effort involving global scientists, engineers, and tradesmen.
Following World War II, Canada continued its atomic research efforts. Since the 1950s, various nuclear research reactors at Chalk River Laboratories have been utilized. These reactors produce nuclear material for medical and scientific purposes. At one time, Chalk River Laboratories supplied approximately one-third of the world’s medical isotopes. It also supplied half of the North American isotopes. In 1962, the experimental Nuclear Power Demonstration (NPD) reactor was initiated as a prototype for subsequent CANDU reactors. This reactor was operated by Ontario Hydro until 1987 as a training facility.
Town construction occurred between the late 1940s and 1950s. Currently, the town has 47 km of water main pipes, which have a replacement value of $68,705,200 as of 2022. Based on pipe age alone, 47 per cent of the pipes are classified as being in poor condition, 5 per cent in fair condition, 37 per cent in good condition, and 12 per cent in very good condition.
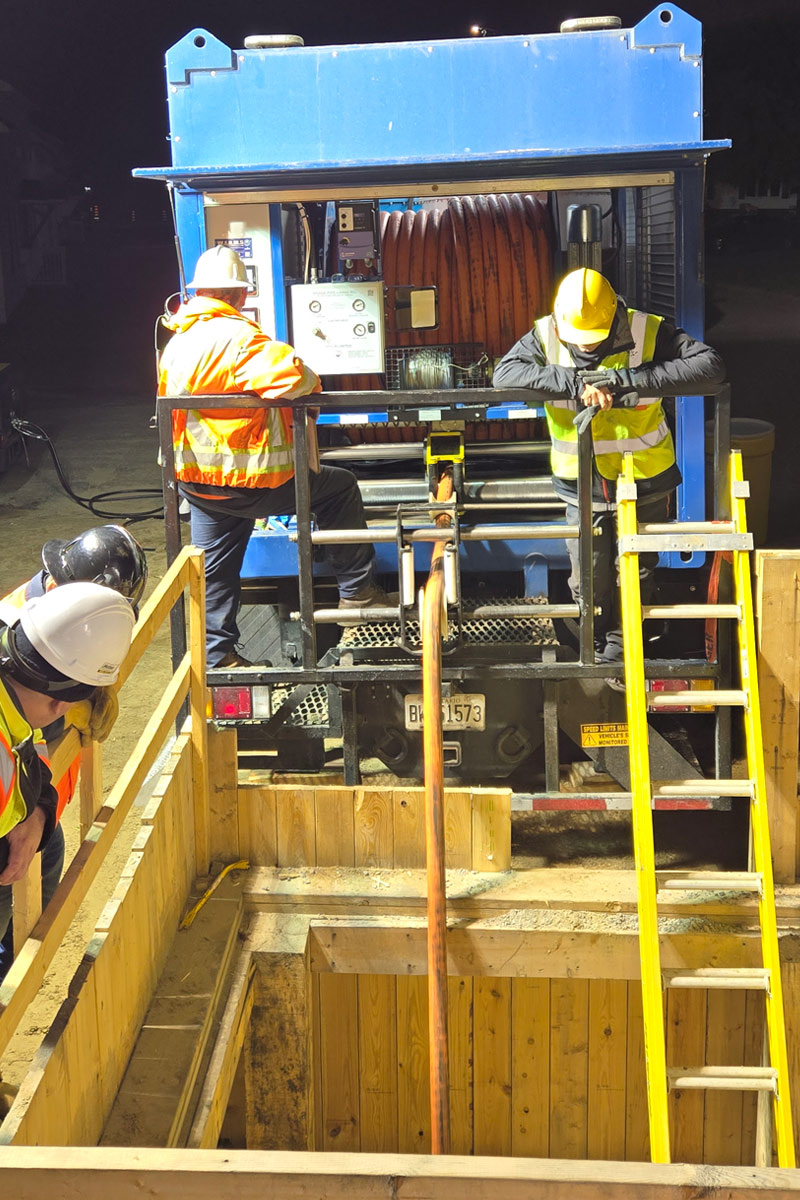
Deep River’s Population Growth Prompts Pilot Project
The Town of Deep River is now expecting to experience population growth of approximately 15 per cent over the next 10 to 15 years. This increase will be primarily influenced by the two major employers in the region: Canadian Military Base Garrison Petawawa and Canadian Nuclear Laboratories. Residential housing expansion is expected to occur mainly within the municipal urban area. It will also occur through the development of additional subdivisions.
In 2023, the Town of Deep River partnered with WaterTight Lining Solutions (WLS) to design a long-term strategy. This plan is to utilize their spray-in-place pipe (SIPP) for watermain cleaning, lining with Resiline 320, and return to service.
Deep River was interested in the same day return to service. This interest was because the unlined cast iron water pipes installed in the 1950s had minimal external corrosion, few breaks. They also had internal tuberculation that reduced fire flows and caused discoloured water events.
The Town budgeted for a 2024 pilot project with WLS, confident that it would extend the pipe life for more than 50 years. Improvements in fire flows and reductions in water quality complaints were also expected. The same-day approach was appealing because it eliminated the need for temporary bypass construction. It reduced construction time and costs, minimized staff requirements, and lessened disruptions to the public and businesses.
In 2024, the Town collaborated with WLS and eTrenchless Group Inc., to identify potential pipe segments for lining and develop the pilot lining program. This program included selecting pit locations, completing the liner design, and creating the disinfection protocol.
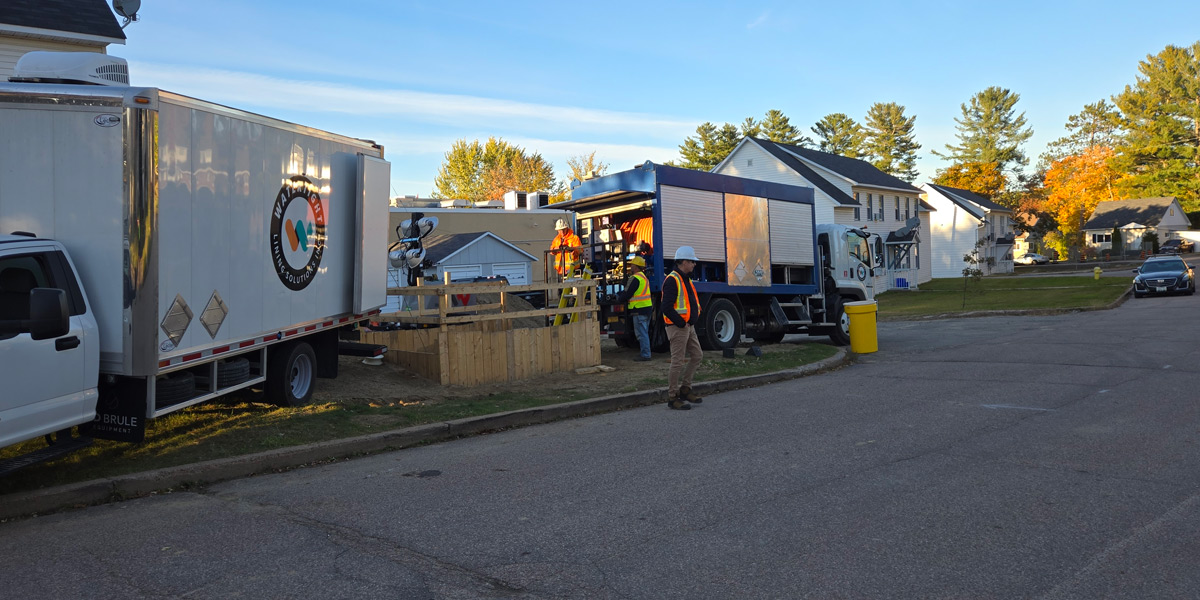
Pilot Project Ramps Up
WLS proposed the installation of a 3-mm thick Resiline 320 liner to comply with AWWA Class III requirements. This material would bridge a 20-mm pipe wall hole and provide adequate ring stiffness. This stiffness is to resist external hydrostatic pressures when the main is out of service. It will also resist in-service short-term vacuum conditions. It was recommended that the 3-mm thick liner be applied in two 1.5-mm coats, with one coat spinning the spray head rotating clockwise and the second counterclockwise. This method was intended to ensure thorough coverage at the joints and service connections. The Town also retained M. Sullivan & Son Ltd. to manage the project, dig and restore the pits, decommission, and reinstate the watermain.
In October 2024, WLS in collaboration with Canadian Induracoat Corp., successfully cleaned, lined, and disinfected 485 m of 150-mm and 200-mm diameter pipe sections within one week. This process was completed without the need for a temporary bypass. This project was divided into five pipe segments, each ranging from 81 to 108 m in length. This same-day return-to-service approach is innovative within Ontario and Canada.
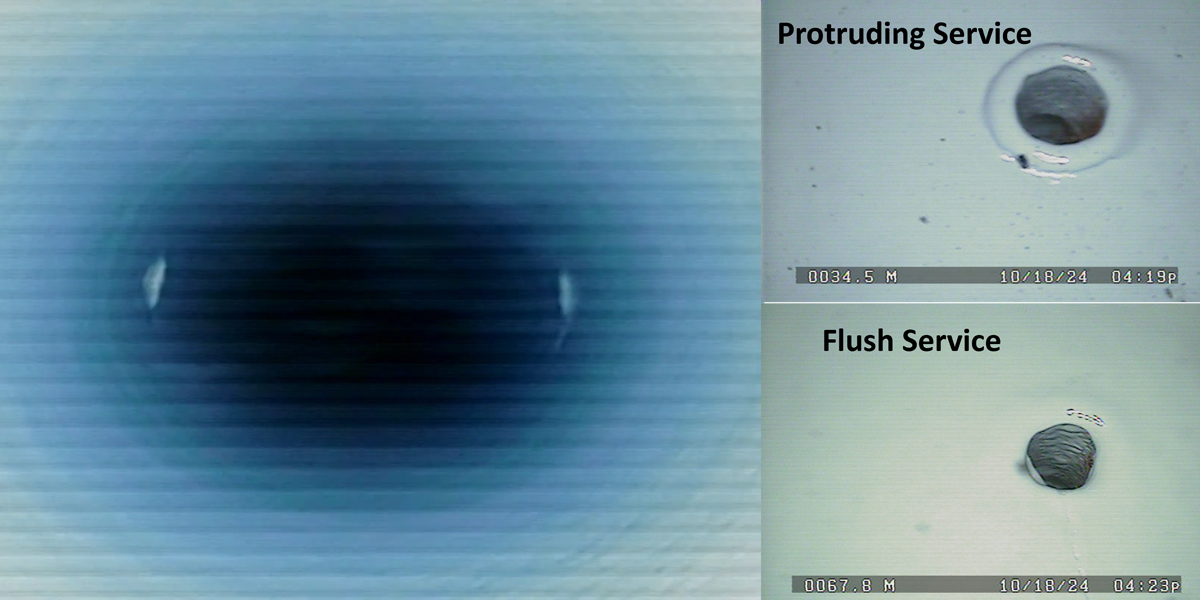
All but one pipe segment was cleaned, lined, disinfected in one day, and returned to service without a boiled water advisory.
On the final cleaning and lining day, 101 m of 200-mm pipe was cleaned and lined between 8:30 a.m. and 4:30 p.m. The pipe was then disinfected and returned to service by 6 p.m. The pipe underwent drag cleaning followed by Tomahawk abrasive stone cleaning to remove all internal corrosion material. This process ensures the liner bonds to the host pipe with bond strength ranging from 3.5 to 7.0 MPa (500 to 1,000 psi).
All water bacteria test results indicated absence of bacterial contamination. Upon receiving the results, typically within 48 hours, M. Sullivan & Son initiated final commissioning of the mains and pit restoration.
Lessons Learned
The Town, in conjunction with the local health department, authorized the rehabilitation pipe’s return to service without requiring a boil water advisory. This decision was made because each pipe segment remained isolated from the water system, NSF/ANSI/CAN 61 materials were utilized. AWWA C-651 Spray Disinfection along with Ontario Drinking Water disinfection procedures were adhered to, under the supervision of a Certified Water Operator.
The Town of Deep River needs to verify and update its water system drawings. During excavation, unexpected pipe bends and Tees were found. This led to additional unplanned excavations, increasing both project construction time and cost. In the future, the Town plans to map the water system before starting a lining program.
The watermain exhibited 30 to 40 per cent tuberculation with minimal external corrosion and internal graphitic corrosion penetrating up to 40 per cent of the wall thickness. Installing a Resiline 320 Class III liner, as opposed to a Class I liner, proved to be an excellent decision. This choice did not significantly increase project costs or lining time, and it provided extended asset life at a nominal cost to the town.
Immediate return to service is feasible without the need for a temporary bypass system or a boil water advisory.
Mark Knight, PhD, P. Eng, is CTO of SIPP Americas.
Latest Posts
- Ezee Fiber Begins High-Speed Internet Expansion in Washington
- How Crews are Optimizing HDD Tooling with the Vermeer Bit Boss™ Retention System
- Digging Safer and Smarter with Mud Dog® Vacuum Excavators
- GEONEX Horizontal Hammer Boring Systems
- Fiber Optic Cable: Redefining Standards in Sewer Inspection