Pipe Bursting Rehabs Sewer, Alleviates Residents’ Anxiety
April 1, 2008

Located on Maine’s rugged eastern coast and home to approximately 1,500 residents, Northport is a resort community comprised mostly of seasonal dwellers. The place is so remote that the majority of Maine’s 1.4 million residents have never heard of it.
Those who make Northport their year-round residence go to great lengths to maintain the quaint integrity of this historic community, which has roots that date back to the early 1600s with the arrival of a contingent of French explorers. So it’s not surprising that when Matt Timberlake and crew arrived in town to tackle an intricate sewer line rehab project, the locals took interest.
“You have to understand the dynamics of the community to fully understand this project,” Timberlake says. “I don’t remember a time in the history of our company when a condition for accepting our proposal included a provision to educate affected residents about the process of how we would complete the project so homeowners understood exactly what was going on. The whole community got involved.”
Timberlake is vice president of the family-owned and operated Ted Berry Co., headquartered in nearby Livermore, Maine. Ted Berry Co. has been in business for more than 35 years and specializes in offering diverse methods of completing infrastructure installation and rehab projects. Timberlake had worked with the Northport Village Corp. since 2005, when Ted Berry Co. was contracted to implement an ongoing inspection of the town’s sewer system. During one of their routine inspections, Timberlake’s crew discovered a section of pipe that had become infiltrated by root growth.
Location, Location, Location
According to Timberlake, the project was a textbook case for a pipe burst. The affected sewer line originated from a residential street at its upper end, continued under four private residences, wound between two other homes and ended at a manhole located within 25 ft of the high tide mark of the Atlantic Ocean. Although the sewer discharge line was only about 200 ft in length, the beginning and ending manholes were not within view of each other. Excavation was a concern at the downstream end, given its proximity to the ocean and the highly visible Northport Yacht Club.
“Many things told us this was not an excavation job,” Timberlake says. “There were established trees and shrubs, walkways, lawns, patios and decorations to contend with. Had we plowed a trench, we would have had to dig right alongside the foundation of a couple of these homes. The long-term effects that disturbing a foundation may cause brought a whole other set of potential issues. Trenching was just not an option.”
Timberlake and trenchless technology supervisor Shawn Ready rolled up their sleeves over dinner one night and got to work on a proposal. Both had been on the inspection team that discovered the root infiltration problem, so the two men were intimately familiar with the layout. They quickly came to a consensus on the best rehab method, but the details of the plan took a bit more time and included stipulations that were somewhat unconventional compared to proposals the two had drawn up in the past.
“Although the village corporation had a legal easement to go through individual properties in order to maintain the sewer line, their first concern was how repairing it would affect the residents,” Timberlake says. “Explaining how we would complete the project to the affected homeowners and getting their buy-in made it an easy sell to the council slated to approve the job.”
The plan Timberlake and Ready proposed included going door-to-door with a representative of the village corporation to explain to residents exactly what needed to happen and how it would be accomplished. By doing so, Timberlake and his crew immediately won over the locals.
In order to preserve the downstream manhole near the shoreline and eliminate the need to employ excavation, the plan Timberlake and Ready devised called for pneumatic pipe bursting. Although the company had completed 40 to 50 static bursts in the past, this would be the first pneumatic burst for Ready and his crew. Therefore, Ready consulted with Brian Cowles, Ted Berry’s HammerHead rep, for guidance during the pre-planning phase and to ensure his crew was well-versed in the project’s details before getting started.
“We had traveled with Hammerhead to several pneumatic jobsites over the previous couple of years, so we were very familiar with the process,” Timberlake says. “It wasn’t really anything all that new. Some of the details of the pneumatic hammer, however, were things that internally we spent a great deal of time planning in advance. And HammerHead was a tremendous help.”
Timberlake went on to explain that the project would have been very easy to complete using static equipment, but he didn’t want to take any chances removing the downhill manhole or digging that close to the shoreline.
“Protecting the integrity of the site was important to us,” Timberlake says. “Nobody from the village corporation actually told us we had to do it a certain way. But we knew the smaller footprint we left meant they would be more apt to have us back. Plus, that’s just how we do business.”
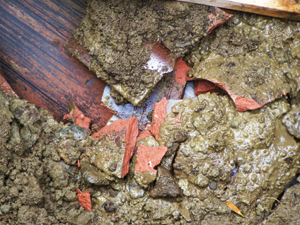
“The job was completed in under four hours,” Timberlake says, “witnessed by what we affectionately called the ‘advisory committee’ … made up of local residents. One of the homeowners was present when we dug the topside launch pit on his property. He had approximately 60 plastic pink flamingos randomly situated on the site. I have pictures of Shawn [Ready] repositioning each flamingo back to its original spot from the map we had created prior to initiating the burst. Most were facing east, but there were a few that faced west. We made sure that we replaced each of them in their original spots and facing the same direction.”
Tips for Other Contractors
While proud of the work his crew performed on the Northport project, Timberlake viewed the process as just another example of how Ted Berry Co. approaches every job. And while a pneumatic burst was uncharted territory for his company, Timberlake has some valuable advice for other contractors.
“Don’t be too proud to ask for help,” he says. “Contractors are typically bad at that. We’ve been in business long enough that we know we don’t know everything. But we have connections to people who have the know-how when we are in need of technical support. Like our relationship with HammerHead, for example, they were onsite from start to finish assisting with completing our company’s first pneumatic burst.”
Timberlake is also a firm believer in involving all interested parties in the project — not only his own crew, but the supervisors, project managers and the affected residents.
“Educate the public,” Timberlake says. “A lot of times we show up on these jobsites and the public is standing there looking at us like, ‘What the heck are you guys doing here?’ We make it a point to go out of our way to knock on doors and let people know what we are up to. I think contractors as a whole need to get better at that.”
A Job Well Done
Aside from all the planning, calculations and gratification of a job well done, it’s the approval of local residents that means the most to Timberlake.
“I understand their anxiety,” he says. “I know how I would feel if a bunch of guys in vests and hard hats were to invade my property with all this equipment and not knowing what was going to happen. We never lose sight of that. I guess the biggest compliment to come from the Northport job was when the guy who was there when we first started the burst later renamed his home ‘Sewer View Cottage.’ We laughed about it at the time, but afterward, it really sunk in just how monumental that was.”
Randy Happel is a technical writer, based in Des Moines, Iowa.