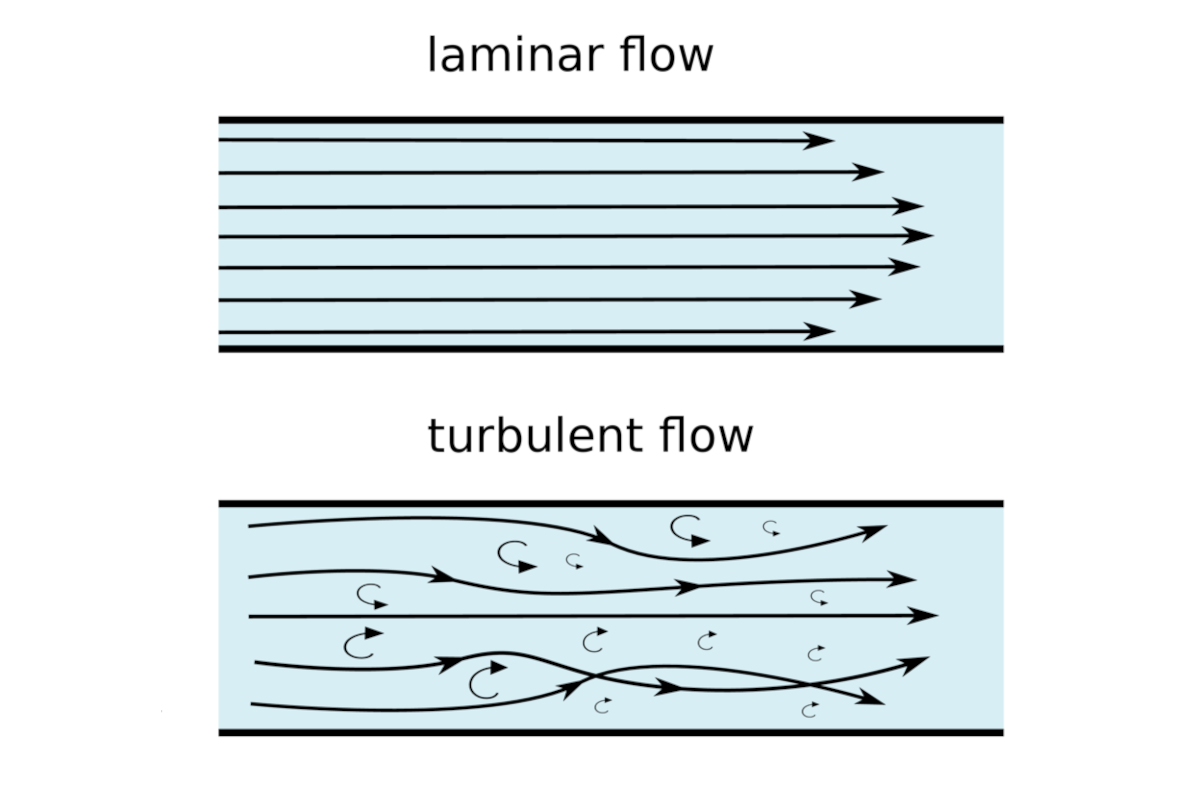
Managing Downhole Pressures in Horizontal Directional Drilling
Managing downhole pressures and the prevention of inadvertent returns has become a critical aspect of successful utility HDD installation. HDD operations allow for the minimal surface disturbance legitimizing the crossing of pipelines, cables, and conduits across roads, rivers, railroads, farmlands, and utility lines.
Controlling downhole pressures is at the top of the list among the issues essential to IR prevention. Leading to greater safety and successful drilling.
Understanding Downhole Pressures in HDD
Downhole pressure in HDD refers to formation pressure that is in the borehole. Borehole pressure has two primary sources but can be manipulated by several factors. The two sources are the drilling fluid, better known as drilling mud, and the formation pressures encountered while drilling.
Downhole pressure is essential to maintain the integrity of the hole by avoiding hole cave-ins, formation damage, and fluid loss. It ensures the effective removal of cuttings from the borehole and assists in conducting directional control of the drill.
Too much borehole pressure can overpower formations and result in IRs to the surface, or fluid loss. So, understanding the basic fluid hydraulics and the role they play is key to a successful project.
Several factors affect the downhole pressure during an HDD project.
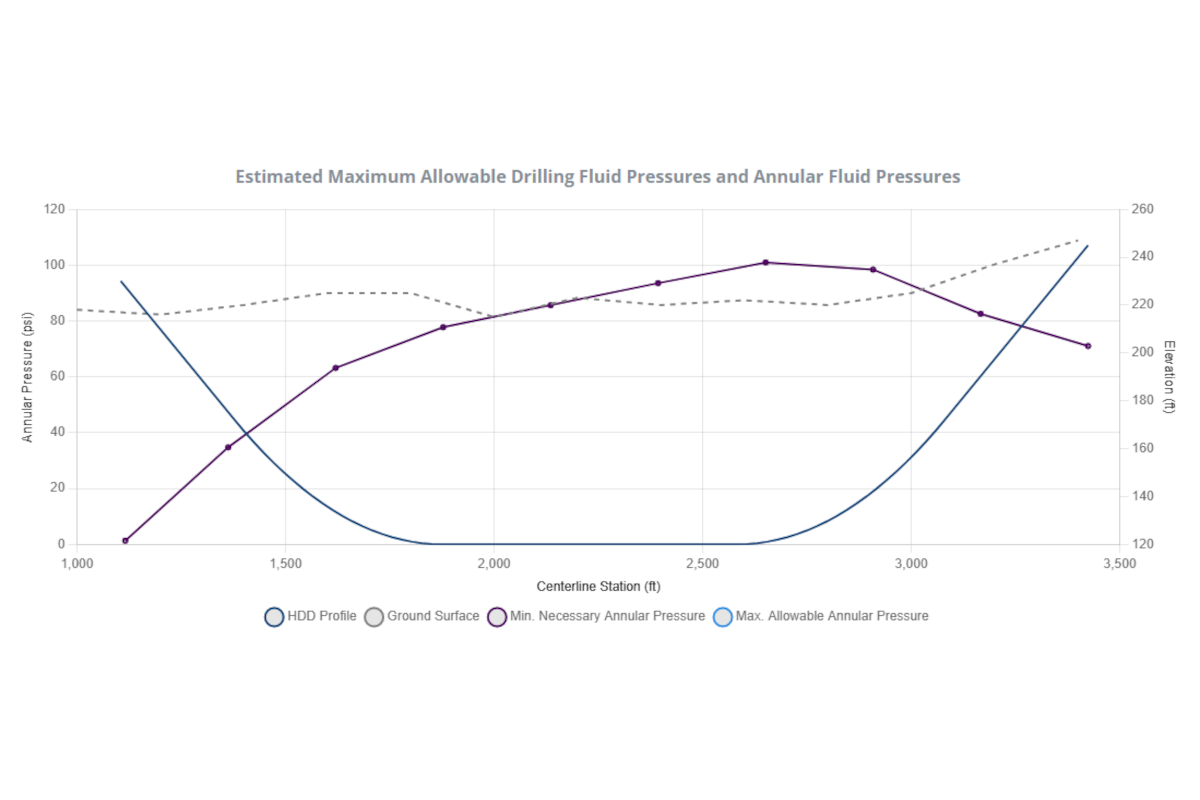
1 – Drilling Fluid (mud) Properties
Drilling fluid (mud) is a composition of several properties, the properties that contribute to downhole pressure the most are density, viscosity, and rheology.
- Density – Density provides hydrostatic pressure to counteract formation pressure. The ideal density can vary by formation but can range anywhere between 8.5 to 12.5 pounds per gallon (ppg), sometimes as high as 14 ppg. A higher density may be required to counter ground water, or for formations with higher pore pressures.
- Viscosity – Viscosity is a measure of a fluids resistance to flow, viscosity should be optimized to balance the need for suspension and removal of adequate cuttings, without adding excessive formation pressure. Generally viscosity can range from 35 seconds/quart to over 100 seconds/quart depending on cuttings suspension needs, and maintaining formation pressure.
- Rheology – Rheology is the science behind a fluids hydraulic capability in relation to its environment. Rheology is broken into two parts. Yield point (YP) and plastic viscosity (PV) (yes, another different type of viscosity). Yield point and PV work in unison like a game of tug-of-war, as one goes up the other goes down. Yield point is related to the reamer diameter, as reamer sizes increase so should the YP. A general rule of thumb is to keep your YP equal to your reamer/bit diameter. Plastic viscosity is your dissolved solids content. As you add bentonite, additives and the likes, your PV will go up. But unless you’re adding YP enhancing products, an increase in PV will push your YP down. Plastic viscosity can range from 8 to as high as 35, depending on the density, and solids % of your drilling mud.
2 – Cuttings Suspension
Efficient cuttings suspension helps balance the flow of drilling mud returns and borehole pressure. Yield point from our rheology is the key factor to estimate adequate suspension. Insufficient suspension can cause cuttings to drop out building cuttings beds along the borehole, thereby building formation pressure during drilling. Which can lead to accidents, such as IRs or a stuck pipe.
3 – Flow Rate
There are two types of borehole flow. Laminar and turbulent flow, with the latter being necessary to maintaining a consistent ROP while minimizing bedding risk. Sufficient pump rate is crucial not only for the circulation of drilling mud, but for cuttings removal. Insufficient flow rates will result in poor formation pressure, and the risk of poor hole cleaning, adding to a cutting bed risk in the borehole. Over pumping and having turbulent flow can wash out the borehole, leading to over excavation, which in turn can cause sinkholes, and mud loss. A general rule of thumb for maintaining laminar flow is to take your bit or reamer diameter and ten times the inch diameter for your pump GPM.
4 – Tooling
HDD reamers and tooling can influence borehole pressures by determining the volume of soils that are excavated during the reaming process. Over excavation will affect the fluid hydraulics within the borehole. Proper reamer selection will help maintain a fine balance between borehole and formation pressure, while inadequate tooling can lead to fluctuations in pressure that may compromise the borehole.
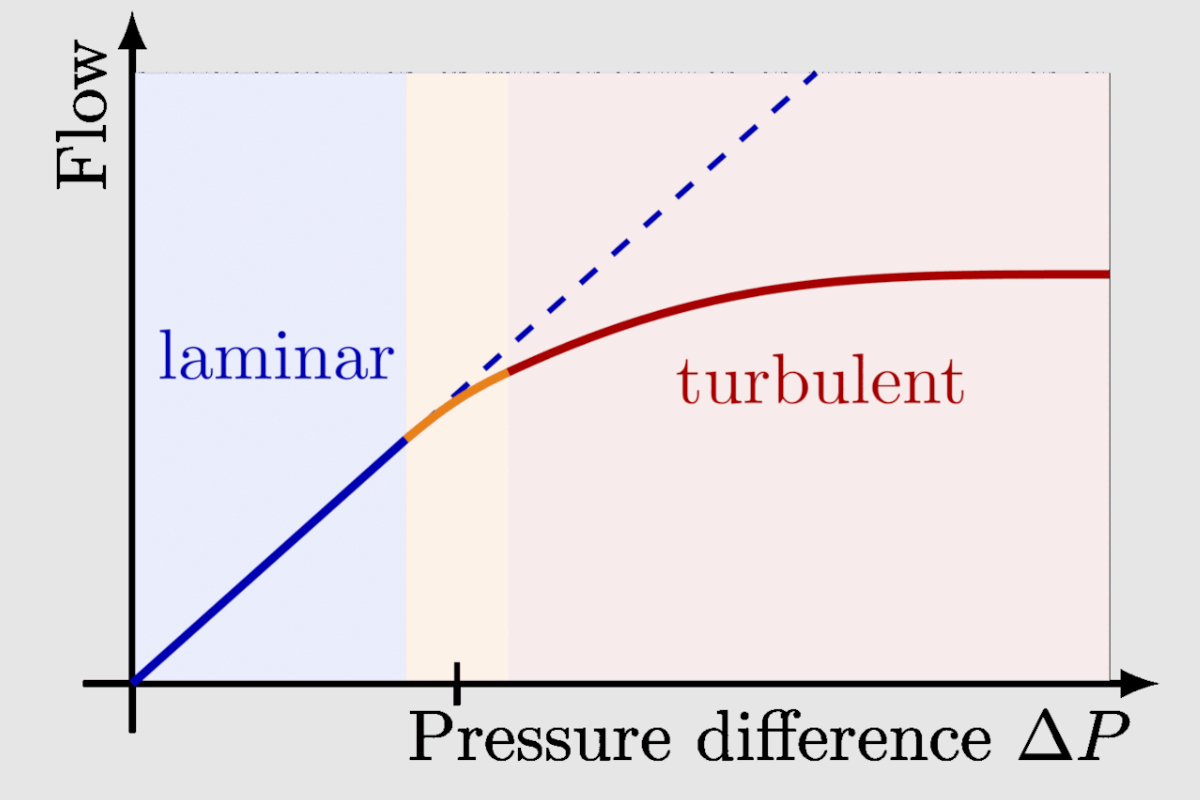
Conclusion
Managing downhole pressure is vital for ensuring the success and safety of utility HDD installations.
The ability to control these pressures plays a critical role in IR prevention, and borehole stability.
Contractors can control borehole pressure by carefully adjusting factors such as viscosity, PV/YP, cuttings suspension, adequate flow rate, and proper tooling. All of which directly impacts the risks of inadvertent returns and the overall integrity of the drilling process.
Maintaining an optimal balance between formation pressure and drilling fluid hydraulics is crucial in avoiding accidents, such as stuck pipes or fluid loss, while ensuring efficient cuttings removal and maintaining directional control.
By understanding and managing these factors, HDD operations can continue to provide safe and effective crossings for a wide range of infrastructure projects.
Bridger Cottle is president of Trenchless Engineering Group. Blake Chargois is field engineer at Trenchless Engineering Group.