Leave No Trace: The Challenge of Lateral Pipe Bursting
April 1, 2009
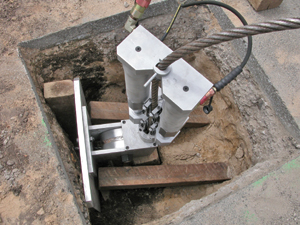
Before lateral pipe bursting was introduced, trenchless methods catered almost exclusively to municipal or government projects: horizontal directional drilling for new utilities, guided pneumatic impact moles for bursting large sewer and storm mains and hydraulic rod-pushers for replacing other sewer and utility lines. All of these methods and machines shared a common scope of work — each was defined by projects that were large and public. By contrast, the first lateral pullers entered an arena whose jobs were small and private.
In this new private market, there were significant challenges to overcome. One major obstacle was pipe approval. Fused HDPE had been used for years by the gas industry and was also the replacement material of choice for the current pipe bursting establishment. However, for the fledgling lateral bursting industry, HDPE wasn’t a preference — it was a demand. Yet this plastic was not listed in building codes regulating work on private property. Approval was granted, city-by-city, in the San Francisco Bay Area where commercial lateral bursting first took off in the late 1990s. Since then, both pipe and process have been added to national and international code books.
Other challenges were mechanical. Laterals commonly include physical turns — 1/8 or 1/16 bends in the line — to accommodate the flow path from building exit point to municipal connection. Sewers can exit a building from various points, which are often in restricted space or covered by surface improvements. City or county connections can be at the property line, in a side or rear easement or in the public right of way, depending on the local regulations that define owner responsibility.
None of the previously available bursting technologies were designed to deal with multiple bends and relatively small pipe (most laterals are 4 in. in diameter). CIP liners had arrived, but were better suited for spot repairs with no excavation at all. Liners were not as permanent a solution and compared to bursting, were neither practical nor cost-effective for most laterals, especially those in serious disrepair.
The first lateral bursting systems met these unique logistical conditions by employing flexible replacement pipe (HDPE) in concert with flexible steel cable to negotiate the inevitable bends in the existing pipeline. Further specialization was required of the pulling device itself. The prototypical models were modified post-tensioning rams mounted on a pulley base against a resistance plate, directing the cable and pulling force vertically rather than horizontally. This allowed for a very small footprint, which was invaluable for sewers that were either shallow, obstructed or in tight places (conditions that describe many home sewer laterals). These hydraulic rams were small, light and high-pressure rated, making them portable enough to carry and position by hand, yet powerful enough to burst most home sewers easily.
Trenchless lateral replacement has since been widely accepted and has become a specialized utility market segment. This niche industry has produced thousands of job scenarios, from which we can derive a few general guidelines for success.
Regardless of the equipment used, the task of lateral bursting is the same. That is, to pull a steel cone (mole or bursting head) through existing pipe, breaking it apart while simultaneously pulling in new pipe of the same or larger diameter. As mentioned, this existing pipe path can have many variables, some considerably more adventurous than others.
The first task is to gather as much information as possible about the sewer to be replaced before bidding a job. A thorough video inspection is essential to determine the location, material, size, condition and depth of the host lateral, including bends and connections along the way. Since they must be exposed anyway, all active tie-in points between entry and exit pits should be exposed prior to bursting and then joints and couplings should be removed before insertion of the pulling cable (or chain). No-hub couplings can collect on the mole, creating unnecessary drag during a burst. Also, bursting through a live connection can damage the auxiliary line and require extra labor and materials to reconnect later.
The direction of the pull is influenced by a number of factors. Location of entry and exit pits, pipe variables (such as size, depth, slope and material), soil conditions, adjacent utilities and of course bend locations all must be considered.
When possible, pulling up-grade (entering at the low end, pulling from the high end) has advantages. In very hard soil, bursting pressures can be greatly reduced by using a garden hose to fill the host pipe with water, which of course can only be done when the mole enters at the bottom of the line. A full pipe makes bursting and soil expansion markedly easier, resulting in less wear on equipment and faster pulling with systems powered by variable flow hydraulic pumps. Keep in mind that only the host pipe needs to be full of water, and not the exit pit, so reduce or shut off water if it overflows into your work area. In addition, pulling up-grade into bell-and-spigot cast iron joints is generally easier because the bell joints are more easily defeated from behind.
Bends in the line are often a major consideration. For example, if a bend is closer to one pit than the other, it is generally recommended to enter at the point closer to the bend. The shorter the distance between entry and bend, the easier it is for the bursting head to make the turn and avoid excessive side-drag and “corner-cutting” outside the original pipe path. Slight corner-cutting produces an even bend in place of a hard angle, which is good. Excessive corner-cutting can be problematic and may even stop the pull. Attempting to pull through hard corners such as 90-degree elbows or sweeping 90-degree bends in the middle of a long bursting path is not recommended. It is better to expose a hard corner, creating a third or middle pit and use that middle excavation as another entry or exit point for a two-staged pull.
Once decided, the direction of a pull determines the dig at either service end, and one end can be vastly different from the other. The exit pit needs to accommodate the pulling apparatus and eventual head extraction. The entry pit needs only to expose the existing pipe with enough working space to reconnect service and provide a sufficient access angle for the new pipe and head assembly to enter the old pipe. This access angle is driven by how much the new pipe can bend before kinking, otherwise known as the minimum bend radius for a given pipe size and SDR rating. For shallower sewers, the entry pits can be quite minimal. The deeper the service ends of the sewer to be replaced, the larger and more interchangeable the pits become at pipe level. In these cases, the more stable and unobstructed pit becomes the choice for the pulling unit.
Pipe bursting is mostly planning and preparation. The objective in lateral bursting is to install a new sewer with maximum efficiency and minimum disturbance to property and homeowners, and then repeat the process regularly. Achieving this objective creates satisfied customers and a profitable business.
John Rafferty is director of operations at TRIC Tools Inc., based in Alameda, Calif.

Tags: Laterals, TRIC Tools