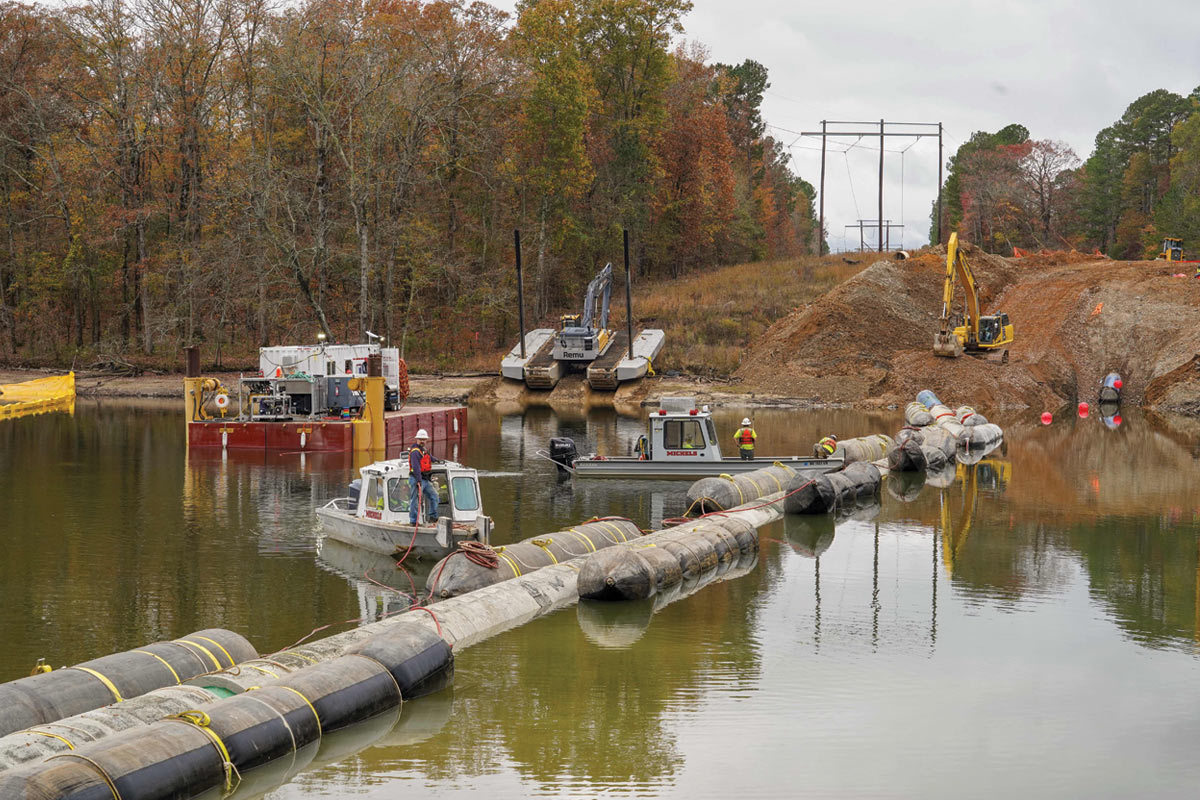
Lake Ouachita Water Supply Benefits from Trenchless Crossings
Stretching from Lake Ouachita to a new treatment plant, the gravity-fed Hot Springs Water Supply Project reinforced the importance of water to the city of Hot Springs, Arkansas and surrounding area.
Hot Springs is known for its blend of natural beauty, historical charm, and recreational opportunities. Primarily known for its namesake natural hot springs, as well as the surrounding Ouachita Mountains and abundant lakes, water is fundamentally important to the city’s identity.
This 17-mile project is a crucial infrastructure initiative designed to secure a long-term, reliable water source for the city of Hot Springs.
Recognizing the increasing strain on its existing water resources due to population growth, tourism, and potential drought conditions, the city opted to tap into Lake Ouachita. It is an exceptionally clear, 40,000-acre reservoir created by damming the Ouachita River at Blakely Mountain Dam.
The Hot Springs Water Supply Project will provide up to 23 million gallons of water per day. This is part of the city’s largest-ever infrastructure project.
Multiple Trenchless Methods

Successful completion of the trenchless aspects of this complex project required one contractor to use three distinctly different trenchless construction methods on critical crossings.
Brownsville, Wisconsin-based Michels Trenchless Inc. (Michels) used Direct Pipe, microtunneling, and float-and-sink construction methods. This helped to construct a safe, reliable water supply line without disrupting environmentally sensitive and visually stunning natural areas.
Lake Ouachita Design & Construction
Building the half-mile Lake Ouachita water tap and raw water intake pipe proved to be among the most central and challenging aspects of the project. After reviewing several trenchless construction methods, the design-build team of Michels COWI, and Bennett Trenchless Engineers turned to the Direct Pipe method. This was used to install a 54-in. diameter pipe under Blakely Mountain to a predetermined end point in a natural cove in Lake Ouachita.
After careful review of geotechnical conditions, anticipated challenges, and technical capabilities, Michels opted to use a 60-in. microtunnel boring machine (MTBM) and pipe thruster (Direct Pipe). This allowed the installation of the 2,569-ft long, 1.0-in. thick steel intake pipe. Notably, it is the longest Direct Pipe installation at this diameter in North America. Site constraints dictated that setup of the equipment, pipe handling, and all operations be performed on an 8 percent grade.
After a drive powered by machinery and a team, a wet retrieval was performed to remove the MTBM from 40 ft below the surface of Lake Ouachita. Next, divers installed an intake structure and valve to complete the water tap and raw water intake pipe project.
Now that we know how the water tap and raw water intake pipe project ended, here are more details into what it took to make it happen.
The design and construction process began with detailed geological surveys and engineering designs to determine the optimal trenchless path for the Direct Pipe installation. Ultimately, a path was selected to bore through Blakely Mountain rather than going above or around it.
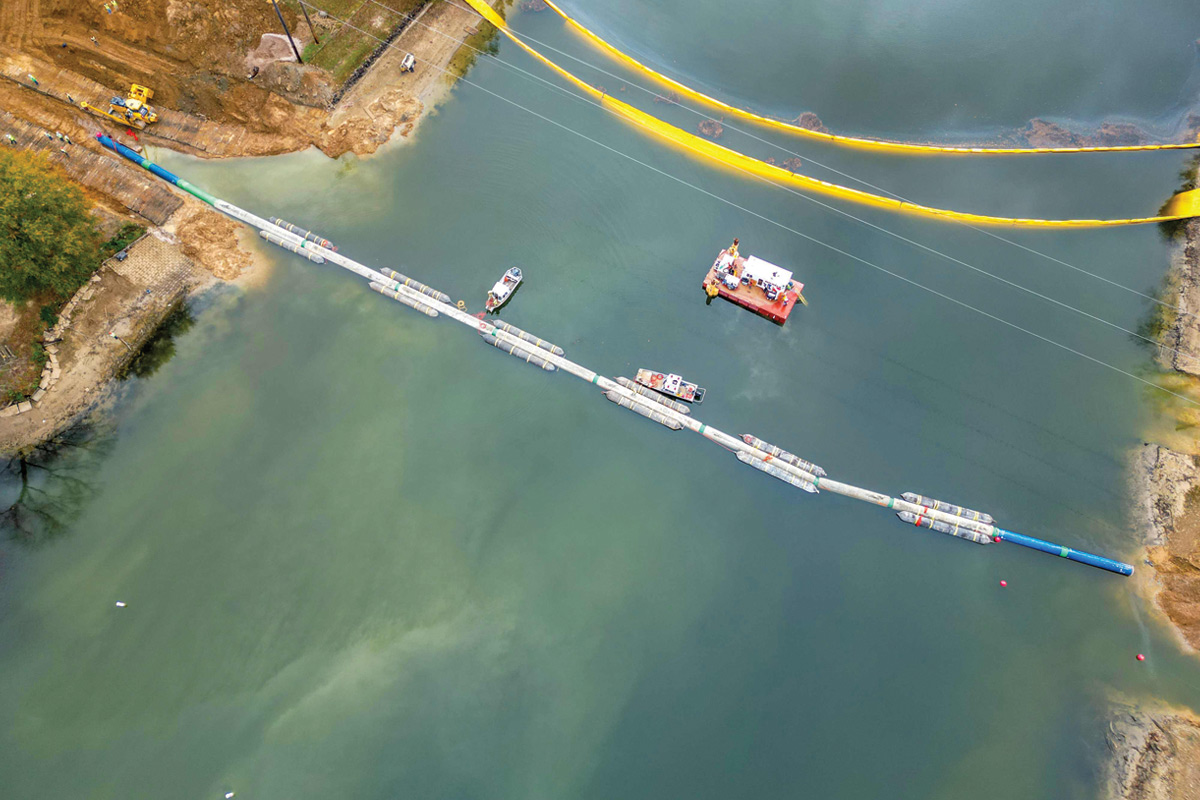
Geological Complexity
However, Blakely Mountain’s highly complex and variable sequence of folded and faulted sedimentary rocks presented challenges of its own. Anticipating the difficulties posed by the hard, abrasive rock, the design-build team proactively planned for the high likelihood of tooling changes.
Consequently, the capability to replace discs was integrated into the project’s overall design. This influenced key decisions about equipment selection, installation methods, and groundwater control strategies to ensure the project’s success. A 72-in. knife gate valve was designed into the tunneling operation as a safety shutoff. This would be used if extractions were necessary due to heavy water inflows.
True to expectations, tooling was changed more than 15 times. This required the team to extract the cutter head and 54-in. diameter pipe and make tooling changes at the face on several occasions.
Early in the process, Michels developed a way to pump the groundwater down. This ensured safe entrance into the tunnel without the risk of flooding and allowed cutter disks to be replaced downhole through an access hatch at the front of the MTBM.
Different types of disc cutters were used, depending on the geology encountered along the way. This allowed for significant research and development into cutter tooling. Some of the rock encountered had unconfined compressive strengths of up to 28,230 psi, presenting a formidable challenge to both cutting tools and the crews.
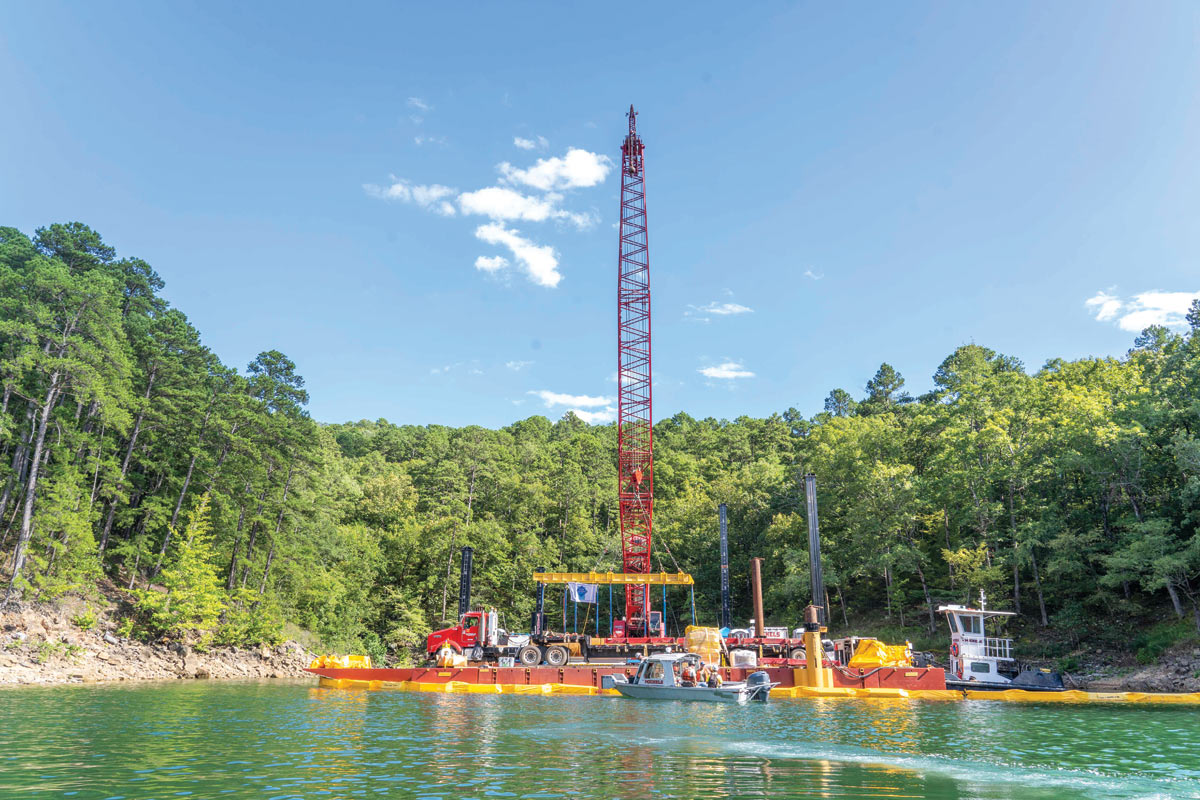
Other challenges included the flow of groundwater into the tunnel and the shale layer at the lower third of the rock face. This impacted the ability to steer the MTBM on alignment. Despite these obstacles, the team persevered, even when production rates were severely slowed. At the end of the day, this was another challenging installation completed by Michels and our partners.
The MTBM reached Lake Ouachita on July 8, 2023. Divers were sent to retrieve the machine, marking a significant milestone in the project. The pipeline was then carefully placed in its final position and securely grouted to ensure long-term stability and integrity.
Adam Stremcha is a general manager with Michels.