Hatch Mott MacDonald
December 1, 2008
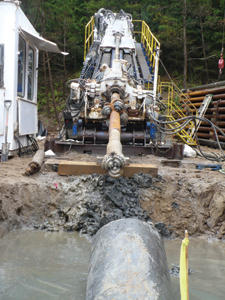
Perhaps in no business is this truer than in subsurface construction. The underground presents myriad challenges that, when left to the uninitiated, may lead to less-than-desirable results. So when building below the surface, making sure you have an experienced partner is Priority No. 1.
Hatch Mott MacDonald, a leading North American consulting firm involved in underground construction, offers a wealth of experience for water, wastewater, transportation and energy providers that rely on underground infrastructure such as pipelines and tunnels. Hatch Mott MacDonald draws upon its experienced staff and the collective experience of its parent companies to provide a specialized knowledge of the underground that is uncommon in the marketplace.
By drawing upon the experience of Hatch Mott MacDonald, facility owners have been able to successfully build, rehabilitate and repair pipelines and tunnels for a variety of end uses. Hatch Mott MacDonald professionals take pride in not only coming up with a solution that works, but one that provides the biggest benefit at the lowest life-cycle cost.
Since its formation in 1996, Hatch Mott MacDonald has grown to more than 1,800 employees across North America with annual revenues of about $320 million in 2008. According to Trenchless Technology’s annual survey of engineering firms, Hatch Mott MacDonald ranks second in 2007 trenchless billings with $40 million.
Beginnings
Hatch Mott MacDonald was a product of the underground industry — the offspring of a long-standing joint venture between the British consulting firm Mott MacDonald and Canadian firm Hatch Associates.
Mott MacDonald’s tunneling heritage dates back to the engineering of the London underground in 1902 and includes world-class projects such as the Channel Tunnel and the double-decker highway and stormwater tunnel “SMART” in Kuala Lumpur. Hatch Associates, meanwhile, was formed in 1955 and has a history in the mining, energy and infrastructure sectors.
The two companies — Hatch Associates and Mott MacDonald — began joint venture partnerships dating back to the construction of the Toronto subway, which began in the 1950s. In the 1990s, Hatch Associates and Mott MacDonald collaborated on the St. Clair River Tunnel between Sarnia, Ontario, and Port Huron, Mich., which utilized, at the time, the world’s largest earth-pressure balance tunnel boring machine, some 31 ft in diameter.
The new company — Hatch Mott MacDonald — took form in 1996 as an independently run company specifically focused on the North American market. Hatch Mott MacDonald has continued to grow, both organically and through selected acquisitions. One move that helped shape the company’s future was the acquisition of Killam Associates, a water, wastewater, environmental and pipeline services firm that complemented Hatch Mott MacDonald’s strong transportation and tunneling background. The move brought the upstart company to about 800 employees, and propelled Hatch Mott MacDonald into the realm of trenchless solutions.
Hatch Mott MacDonald has continued to expand its expertise and geographic footprint. Today, Hatch Mott MacDonald boasts more than 1,800 people in 57 offices throughout the United States and Canada, and can draw upon the expertise and resources of its parent companies’ combined staff of 23,000 worldwide.
Hatch Mott MacDonald Today
The company’s revenues derive mainly from the tunnels, transportation, aviation, water/wastewater, pipeline and environmental sectors. Most of its trenchless work — which involves utility tunneling, microtunneling, horizontal directional drilling, pipe rehabilitation and other applications — falls under the umbrella of the Tunnel and Pipeline Practice Groups.
Although the end uses and sizes of the subsurface facilities may differ, the company’s approach is similar. “Whether it’s a big bore or a small bore, our view is the same,” said Randy Essex, executive vice president and director of tunneling for Hatch Mott MacDonald. “We evaluate the individual challenges of the job, starting with the subsurface conditions. The better we can understand our clients’ needs and constraints, the more effectively we can identify an approach that best manages their risks. Whether it’s an HDD gas pipeline or a highway tunnel, our ability to be pro-active helps us deliver successful projects for our clients.”
Another unique aspect of Hatch Mott MacDonald is the company’s strong background in the underground. Whereas many firms offer underground consulting services as a sidelight to their overall services, Hatch Mott MacDonald offers trenchless and tunneling as part of its core services.
“Hatch Mott MacDonald has 350 staff in North America who just engineer tunnels and pipelines — there are very few companies that have that level of expertise,” said Mike Vitale, vice president and midwest tunnel practice Leader based in the Cleveland office, which helped spur the company’s trenchless design services. “Plus, we have additional expertise available internationally. It makes a big difference when you have people who are involved in the underground every day. Having our ideas and work products peer-reviewed by in-house experts is a very powerful process – no corporate defensiveness and no acrimony – just a consistent goal to generate the best solutions and best designs we can.”
Vitale says despite the fact that trenchless methods have become more widely known over the years, the need to educate owners — and consultants — remains. “There is still a misunderstanding of the technologies and construction processes. An owner may build a tunnel, but then not need one for years. If and when they need another tunnel, the staff may have changed. That’s when an experienced consultant who is familiar with the processes can help them choose the best method available.”
Coventional Trenchless: Microtunneling
One area that has been central to Hatch Mott MacDonald’s trenchless suite is microtunneling. Introduced in the United States in the 1980s, microtunneling is now used in all parts of the country because of its accuracy and its small construction footprint, which allows for the least disruption possible.
Microtunneling is still met with confusion, in part because of the name. “That’s because when you start talking about tunnels that are 10 ft in diameter or more, they aren’t viewed as micro,” said Vitale, who was a member of the ASCE microtunneling standards committee in the 1990s.
Defined as a method of jacking pipe via remote control, microtunneling can also be misunderstood in terms of its capabilities. “One common misconception is the belief that microtunneling machines can cover long distances in hard rock,” Vitale said. “While some machines are capable, it’s important that you consider the length, diameter and other risks and plan the bores accordingly.”
If the ground is accommodating, intermediate jacking stations can facilitate longer pushes without the surface impacts associated with intermediate jacking pits. “I had the pleasure of working on a pipe-jacking project back in the early 1990s that advanced 3,500 ft from a single jacking pit using 10 in-line intermediate jacking stations,” said Essex. “At the time it was the longest pipe-jacking project in the world, and I believe it still holds the record in North America today.”
One Hatch Mott MacDonald project that showcases the abilities of microtunneling machines is a project being done for the Bergen County Utilities Authority in northern New Jersey. The project involves the construction of five miles of sewer pipe in a heavily industrialized area with existing utilities. In some areas the alignment comes within 2 ft of the existing concrete pipeline it is designed to augment. In an effort to reduce disruption, microtunneling was chosen as the method of installation for crossings of the New Jersey Turnpike, State Route 46 and a CSX railyard.
Further complicating the project was the soil, which included very soft clays along a number of reaches and ground that contained cobbles below Route 46. As a result, Hatch Mott MacDonald and the contractor, Northeast Remsco, designed two different cutterheads for the different crossings.
For the soft ground crossings, the cutterhead was designed with two steering joints — one immediately behind the face and one in the tail shield. Providing the two steering joints was in response to a contract requirement, so that if steering was lost in the front in the extremely soft clay, the forward joint could be locked and steering accomplished from the rear. During a crossing of Route 46, the secondary steering joint needed to be activated and worked well, according to Zhenqi Cai, Hatch Mott MacDonald’s New York-based design manager who specified the requirement. Cai added that he knew the double steering configuration had been used before in South Korea, but believed that this was the first time it was applied in North America.
While portions of the project have yet to be completed, the more difficult crossings, beneath the New Jersey Turnpike and Route 46, have been successfully completed. Cai attributes the success to date to careful planning. “We analyzed the extremely soft clay carefully by using cone penetration testing in addition to soil borings. By spending extra money to test the areas of concern, we were better able to understand and explain to the bidders how the soil would behave.”
Cai sees an increasing demand for these types of projects, citing an example in Hartford, Conn., where the owner requires road repairs from curb to curb whenever a street is open cut. “When you consider all of the hard and soft costs of construction, including pavement replacement costs, microtunneling becomes a more cost-effective alternative,” he said.
HDD – The New Trenchless Frontier
Hatch Mott MacDonald has a long history of experience with horizontal directional drilling (HDD). The technology has been around since the 1970s, and its use and Hatch Mott MacDonald’s depth of expertise have both grown steadily over the years. Today, HDD design is a prominent area within the company.
“We’ve seen an increase in the pipeline construction market with the boom in the natural gas industry over the last several years,” said Jon Barbalich, a senior vice president and practice manager of Hatch Mott MacDonald’s Pipeline Group. “In our pipeline engineering business, we are seeing the use of trenchless methods such as HDD become more widespread. HDD is a highly effective means of minimizing environmental impacts when crossing under rivers, streams and wetlands, as wells as highway and railroads. In many instances, it’s not just a good solution, it’s the only solution.”
Because of the increasing demand for natural gas, pipelines are becoming larger. His requires more workspace and deeper, wider trenches, which creates more demand for HDD.

But HDD is not limited to gas pipelines. Glenn Duyvestyn, senior project engineer, recently oversaw the completion of a 4,100-ft long HDD offshore sewer effluent outfall in Oregon. As a result of that project, the owner is looking to use HDD to connect the outfall to a new treatment plant, which would shorten the route and eliminate or lessen the effect of a pump station.
“We are seeing many cases where we are brought in to find a solution for a specific problem, and in working with the clients they realize that we can help solve other problems as well because we can draw upon a pool of national experts,” Duyvestyn said. “As a result, the boundaries are being stretched for trenchless, which makes it even more of a growth area for us.”
Duyvestyn cited another example of an HDD project under consideration which would be launched from an upslope small construction footprint, and then drilled uphill, requiring a special packer to contain the drilling fluids. “There have been very few, if any, jobs done like that,” Duyvestyn said. “The key is identifying the risks, and then addressing those risks by selecting the right tool for the job.”
Future
As the need to repair, replace and build new infrastructure continues, trenchless techniques will no doubt play a major role, and that presents growth opportunities for design firms like Hatch Mott MacDonald.
Trenchless design services are being offered at more and more Hatch Mott MacDonald offices throughout the country and represent an increasing percentage of the company’s overall work. “The trenchless market is expanding and new opportunities are coming up,” Vitale said. “In Cleveland, for example, we had never done an HDD job until recently, and now we’ve completed eight projects in the span of nine months.”
Vitale also cites EPA-driven consent decree work that is being undertaken throughout the country as further reason to expect an increase in trenchless work. “The markets are already strong on the East and West coasts and in the Southeast, and there are a lot of growth opportunities in the Midwest and in the Mountain states,” he said. “The projects are there, and a lot of them are not going trenchless but should.”
However, once the decision is made to use trenchless, it must be the right tool for the problems at hand — and that’s where experience comes in.
“The key is gaining and then sharing our experience — in Hatch Mott MacDonald we call it Knowledge Management,” said Essex. “By sharing our lessons learned across a wide range of applications and geologic conditions, we can better deliver our collective knowledge to any one client and project. HDD, microtunneling, NATM, drill-blast, TBM tunneling in soft ground or hard rock … all of these applications have similarities in one respect or another. A lot can be learned from a big bore that can translate into a successful trenchless project. It all comes down to having and properly applying the right experience.”
James W. Rush is editor of Trenchless Technology.