Gyroscopic-Based Mapping Aids
December 1, 2008
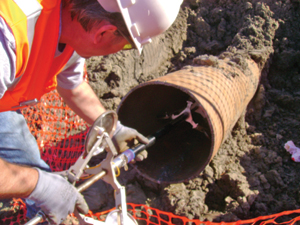
Inner duct was pulled through the steel casings and joined to the open-cut conduit. HDD was the selected construction method due to future civil construction projects involving elevated roadways and light rail transit stations, as well to avoid environmentally sensitive areas where open-cut wasn’t an option. Fifteen bores and associated casings were advanced for this project, which ranged from 300 to 1,600 ft in length; a few of them achieved depths of 90 ft or more.
Concerns arose during the project about the “as-drilled” location of the HDD bore shifting once the final back reaming activities were completed and the steel casing was pulled through — potentially creating an as-built that differed from the “as-drilled” location. The changes that may have taken place were based on the varying geologic conditions present at the site, as well as the operator controls during back reaming operations. Of added concern was a tight right of way.
Geospatial’s mapping technology pinpointed the exact as-built horizontal and vertical location of the installed HDD pipelines by mapping the inside centerline of the casings through the use of inertial-based measurement units and recording accurate positional information in the X, Y and Z planes throughout the linear distance of the pipeline structure. The gyroscopically-based probe records changes in both the horizontal and vertical directions at the rate of 800 times per second. The acquired information is then uploaded into proprietary software enabling production of plan and profile coordinate-based drawings.
Upon completion of the pilot bore, back reaming and installing the pipeline product, the casing was mapped from each of the open ends of the HDD pipeline entry and exit points. Once the pipeline casing was mapped in both directions, the collected data was uploaded onto a computer. Through the use of Geospatial’s proprietary software, the data was analyzed onsite within minutes of the actual data collection. The software also contains diagnostic capabilities so that the GIS field mapping technicians could run quality assurance (QA) checks on the collected positional data.
An accurate as-built vs. an as-drilled plan was provided as a result of the technology, enabling the responsible parties to view the exact location of the utilities and aid in avoiding future conflict issues that could arise. Since the entire construction project was tied to a State Plane Coordinate system, Geospatial had the top of the ends of the pipeline surveyed for both horizontal control and vertical elevations. This information was entered into the computer software, allowing the resulting positional data collected with the gyroscopically-based probe to be evaluated and rectified to the same project coordinate system and vertical datum.
In each of the 15 HDD installed casings, plan and profile data was submitted back to the client within 24 to 48 hours. One of the benefits of this type of technology is having the immediate verification of the location of the HDD pipeline and how it relates to the project requirements and design specifications.
Project engineers constantly face the challenge of congested corridors and having to deviate around competing underground infrastructure. Differing soil conditions and/or the proximity of existing lines can force utility contractors to change their construction methods in real-time to perform the work and stay on schedule and within budget. In today’s construction arena, the use of a new technology, such as Geospatial’s Smart Probe, allows project managers, engineers, contractors and owners to make fast, effective decisions by knowing and trusting the location of their HDD installed pipelines and conduits.
Pete Monday is operations manager and Linda S. Ward is executive vice president of business development at Geospatial Corp., based in Atlanta.