Drilling Fluids: Tackling HDD Spoil Disposal Issues
April 1, 2008
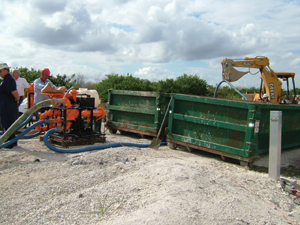
One of the biggest problems in disposing of used drilling fluid is that landfills automatically refuse anything containing free-liquids that can bog down trucks entering and leaving landfill facilities. It can wreck havoc on a landfill’s leachate collection system — which gathers rainwater and liquid residue from the decomposition of the waste for removal from the landfill. The only practical alternative to dumping liquid drill spoils is to turn the material into a solid waste, which is easier to dispose.
The standard test that landfills use for determining free-liquids is called a paint-filter test. A paint filter (such as one you would find in any hardware store) filled with the material to be disposed, is mounted over a graduated cylinder and timed for five minutes. If no liquid is present in the graduated cylinder after five minutes, the material is considered to have no free-liquids.
Paint-Filter Test
Dewatering of drill spoils has been an option used primarily in oilfield drilling and occasionally on large maxi rig river crossing projects due to high cost. Dewatering often requires the use of a coagulant or acid to lower the pH of the drilling fluid in order to destabilize (coagulate) the stable suspension of bentonite and drill solids. During the coagulation process, you can immediately see the release of some clear water in a sample of the material.
After a coagulant is added, the correct flocculent (of the proper ionic charge and molecular weight) is blended with water in a pre-mix tank to the required concentration, and is then mixed into the drilling fluid at the precise dosage (overdosing or under dosing will not achieve the desired results). The flocculated material is then introduced into a mechanical means of liquid/solids separation such as a horizontal decanting centrifuge where centrifugal force of around 3,000 times the force of gravity is applied in order to split the material into a clean liquid phase and a separate dry solids phase.
Simply dumping a flocculent into a tank of drilling fluid will not yield the desired results and often creates more problems than it solves. Dewatering drill spoils is a complicated procedure best left to those not only familiar with operating horizontal decanting centrifuges, but with a good background in the use of flocculents and dewatering equipment. This is because dosages and types of flocculents required may change from project to project and may even do so through the course of a project. Horizontal decanting centrifuges are expensive and require an additional generator to power them.
Centrifuge Dewatering of Drill Spoils
Solidification is a process where a bulking agent or absorbent is added to soak up free-liquids in order for the material to pass the paint-filter test required by landfills. In the past, materials such as cement, cement kiln dust, fly-ash and even sawdust has been used as solidification agents. These materials greatly increase the volume of the material being disposed, which increases trucking and handling costs, as well as tipping fees charged by landfills. These solidification/bulking agents tend to be labor intensive in their application and require a lot of time and machinery (such as backhoes or excavators) to mix the material.
New high-tech solidification reagents emerging into the drilling industry today are making solidification a more viable cost-effective option. One example is PitDry, a reagent made by CETCO Drilling Products that requires a maximum dosage of 2 percent by weight for clear water and dosages can be as low as 0.5 percent for drill spoils containing high solids content.
This type of reagent requires the use of a specialized pumping/mixing unit, which can pump drill spoils from a pit or tank, inject the reagent at the exact required dosage, discharge it into a pit, dump truck or roll-off box where it will completely solidify in approximately 10 minutes. It can be hauled to a landfill for disposal or mixed one-to-one with native soil and backfilled onto the jobsite. This self-contained compact portable solidification system is capable of processing 80 gpm and yet is small enough to fit into the back of a pickup or utility trailer. This solidification reagent is also available in variations designed to handle (and encapsulate) material containing contaminants such as hydrocarbons and chlorides. Processed material continues to dry and shrink long after solidifying, which further reduces the overall volume of material to be disposed.
A Case Study
A Canadian company has been producing oil and gas in British Columbia’s Southern Foothills since it was formed in 1992. The operator has continuously invested in the area and recently opened new gas producing wells northwest of Fort St. John, the largest city in the northeast region of British Columbia.
The new wells are situated 4,600 ft above sea level in a rigid mountain terrain. The viable way to connect the wells and make production practical was to put a pipeline through the mountains; the landscape and environmental issues meant that going over or around the mountains simply wasn’t an option. The only solution was to take the pipeline through the mountains.
An Alberta-based horizontal drilling project management company, specializing in laying pipelines across demanding natural terrain was contracted to oversee the construction of the pipeline. A drilling services company was contracted to perform the drilling portion of the project.

In addition to being financially viable, processing onsite also offered environmental benefits in terms of less vehicle movements.
The goal was to treat the spent drilling fluids and cuttings to a level that met the Canadian company’s high environmental standard, then dry what was left to a solid state for burial onsite. The process recommended to the operator to achieve this was the PitDry slurry solidification product.
PitDry is the only product available that quickly converts spent liquid drilling fluids into disposable solids suitable for burial, even in environmentally sensitive areas like British Columbia’s Southern Foothills. It is a unique process, which allows the operator to simply pump the spent fluid through a PDA-300 mixing machine while adding PitDry reagent. The resultant outflow dries to a solid in minutes and can then be mixed with soil for burial onsite.
Although PitDry offered an ideal solution in terms of solidifying the cuttings and fluids, the project still faced further environmental challenges — challenges of nature.
A total of seven hills had to be accessed with equipment. With slopes of up to 28 degrees, simply getting the solidification processing system onsite was a challenge in its own right. Furthermore, the pipeline crosses a Caribou migration path, which meant that all of the cleanup work had to be completed and the contractors off location before the animals arrived in the area during October.
To compound the challenges of nature even more, a month of rain at the outset of the project made physical conditions difficult and delayed initial deployment. This combined with the need to move winch equipment and manpower up and down the mountains, resulted in mobilization taking three times longer than initially anticipated, thus adding further pressure to what was from the outset a limited time frame for the project.
Despite these challenges, the project was completed successfully and on time.
At the peak of the project, the CETCO equipment was processing more than 20 cubic meters of waste per hour. In total, 700 cubic meters of fluid was processed onsite, the equivalent of 184,800 gals, and 795 tons of solidified material was generated as a result of the PitDry process.
Despite the poor mixing and covering properties of the local natural soils, PitDry proved very successful, surpassing all the parameters that apply to a 3:1 mix, bury and cover process, including all microtox, SAR, EC and leachate tests.
All of the equipment utilized performed as planned without any unscheduled downtime and the project was completed as planned before the Caribou arrived. The project was both cost-effective and environmentally sensitive. It made development of the Canadian company’s new gas wells a more viable option and met with the operator’s goal, of being as environmentally friendly as possible.
The resulting gas production through the new pipeline will generate revenue for British Columbia’s government, which is committed to investing oil and gas revenues to protect and preserve its natural heritage.
George Dugan is southeast regional manager for CETCO Drilling Products, which is headquartered in Arlington Heights, Ill.