
City of Seattle Armory Way High Pressure Waterline Rehabilitation
The City of Seattle Public Utilities (SPU) has been providing water and wastewater services in King County, Washington, for more than 100 years, currently serving more than 1.3 million customers.
The utility’s drinking water system is supplied by 100,000-plus acres of watershed, with two treatment facilities, Tolt and Cedar Water Treatment Plants, which is conveyed to customers through 1,800 miles of pipelines. As many other cities are experiencing, their aging pipelines are starting to create operating challenges due to leaking and failing pipelines, with many of the easements having development on and around them since they were installed decades ago.
One such pipeline causing operation challenges for SPU due to joint failures was a 20- and 16-in. just south of downtown Seattle. However, because of the pipeline easement being under the freight railway yard, which is adjacent to the luxury cruise line harbor, and traveling under a highly utilized mixed-use park, the ability to replace the pipeline was nearly impossible.
Under the leadership of SPU senior civil engineer Alissa Lee, P.E., the city started an extensive evaluation of various rehabilitation technologies to renew this pipeline, providing assured service for another 50 years.
However, the operation parameters, geometry, and distance between feasible access pits for the rehabilitation led to extremely challenging parameters for a rehabilitation technology to achieve. The railway station and park placed the access pits for the installation approximately 1,800 ft between them. Within that easement, the pipeline had three 45-degree bends and one 90-degree bend. Finally, the pipeline normally operates at 225 psi, but can have pressures reach as high as 350 psi during high demand periods throughout the year.
Because of these hurdles, SPU completed a thorough search for a technology that could meet the extreme challenges of this pipeline.
After more than a year of discussions with a variety of pipeline rehabilitation manufacturers, SPU engineers determined that Primus Line high-pressure aramid (Kevlar) Flexible Fabric Reinforced Pipe (FFRP) was the only product that could provide the rehabilitation needs of the pipeline to provide another 50 years or more of service life. SPU determined that with the increased C-factor (150) of the Primus Line, and operating flows of the system, they would be able to install a 12-in. system for the rehabilitation. With a burst pressure rating of 1,535 psi and operating pressure rating of 638 psi, the Primus Line material was more than able to manage the extremely high internal pressure of this pipeline.
Internally, SPU developed plans and specifications for the bid solicitation of this pipeline rehabilitation in early 2024. The contract was awarded to Roadway Northwest, a local Seattle underground contractor, with the Primus Line installation being subcontracted to Advantage Reline, from Mesa, Arizona. The high-pressure material is not a standard type of liner that the United States Primus Line distributor MTC carries, so it was ordered from Cham, Germany where Primus Line is manufactured. After months of coordination and planning between SPU, the contractors, and Primus Line the project construction was scheduled for completed in June 2024.
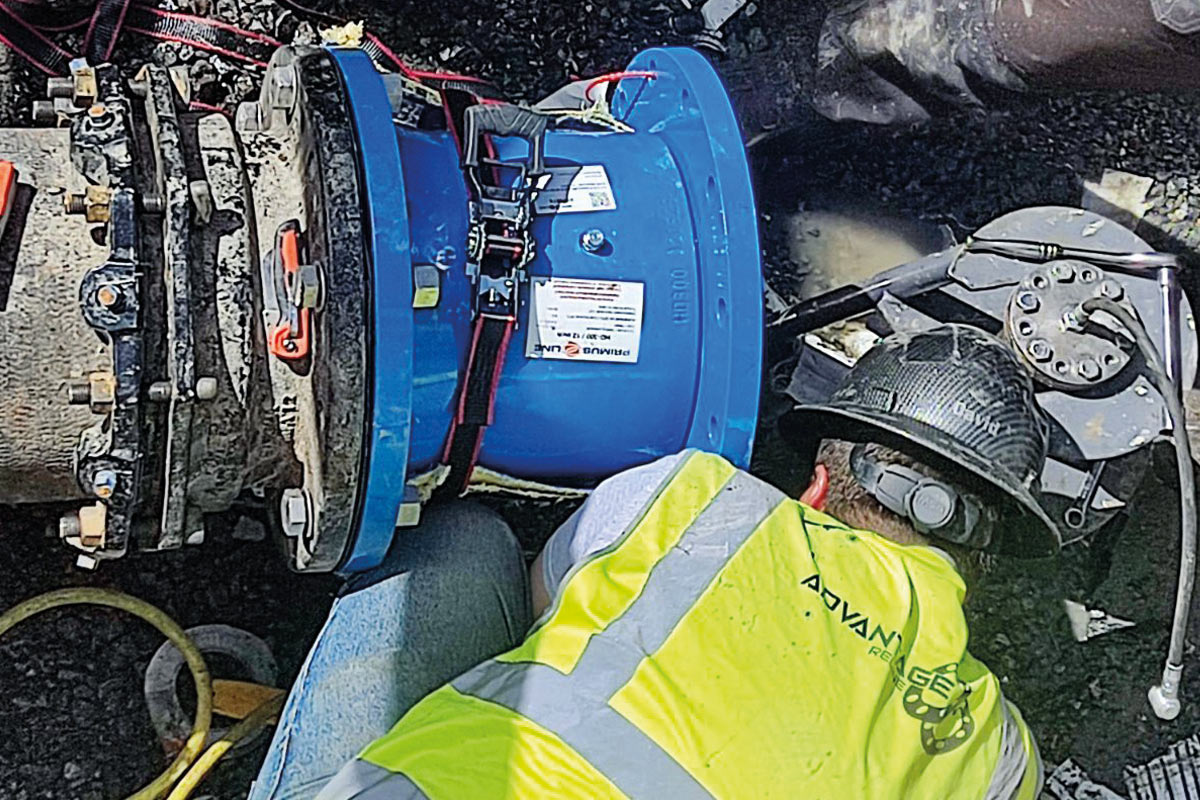
Roadway Northwest completed the construction of the access pits in the first week of June 2024, with one pipe located adjacent to a new shopping center, just east of the luxury cruise shipping port. This access pit was 10-ft by 10-ft, with a depth of 6 ft that required steel shoring boxes. The second pit was in a neighborhood cul-de-sac, adjacent to the park the pipe traveled under. This access pit was 20-ft by 20-ft, 8-ft deep, and was able to be sloped back to the finished grade. Because this pipeline was transmission for connecting two operating zones south of the city, there was no bypass pipeline needed while out of service. Both pits were developed in one week.
The second week of June, Advantage Reline mobilized on site to perform the installation of the Primus Line material. The first day on-site, the rehab crew completed pipe preparation, which requires any debris and sharp edges to be removed from the inside of the pipeline prior to installing the Primus Line. This was completed using combination trucks, as well as pipe swabs. Once completed, a robotic CCTV camera was sent into the pipe to ensure the surface was ready for rehabilitation. During this inspection, it was discovered that a section of mortar lining was 150 ft from the second access pit, and a cured piece of lead was on the invert from a prior joint repair completed on the pipeline. Both items were removed robotically using a cutting robot prior to the rehabilitation of the pipeline.
Once the pipeline preparation was completed, the winch cable was pulled into the pipeline, which required fewer steps of different sized lines to work up to the ¾-inch steel cable connected to the 12-ton winch. Because of the extreme pulling forces that the liner was going to experience during the 1,800 ft of pipe with multiple 45-degree and one 90-degree bend, a pulling head that was mechanically connected to the end of the Primus Line material at pit No. 1.
The pulling process started with the 12-ton winch at pit No. 2, which took approximately 1 hour to complete the liner installation through the host pipe. Once installed, the Primus Line was expanded on both ends with pipe plugs and then inflated with air to break the tape and expand the liner back to its round form that it was manufactured to provide. To obtain the round form, 8 psi of compressed air was filled into the liner. In addition to allowing the liner to expand to its full manufactured diameter, this also the contractor to verify the liner was not damaged during the installation and prior to the installation of the fittings.
On day three, the high-pressure Primus Line fittings were installed on Primus Line in both access pits, with connections to the host pipe using 150# ANSI flanges connected to the host pipe. When this process was completed, Advantage Reline was completed with the installation of the Primus Line material and fittings. To ensure the termination fittings were completed secure, Roadway Northwest waited until day four to complete the hydrostatic pressure test, which was completed using 300psi for 1 hour on the Primus Line material.
On the final day of the workweek, Roadway Northwest completed the mechanical connections at both access pits by placing valves and spool pieces in at each location to allow for future operational options for SPU. The following week, the pipeline was placed back into service and backfill, and restoration of finished grade was completed by the contactor.
This project was the first pipeline rehabilitation project that utilized the high-pressure Primus Line, which includes two layers of woven aramid (Kevlar) fabric that is protected by an external coating and internal lining of polyethylene.
The strength of this material allowed for the lining of Seattle Public Utilities’ water transmission line with access pits 1,800 ft apart, which resulted in a pulling force of nearly 10-tons (20,000 lbs) through multiple 45-degree bends and one 90-degree bends. Utilizing an innovative material for this rehabilitation save SPU millions of dollars of construction cost, reduced months of carbon emissions from construction equipment, and eliminated the need to work within other agencies (railroad, WSDOT, parks department, and private property owners).
As aging infrastructure continues to pose challenges for pipeline owners, the development and evolution of new pipeline rehabilitation products, such as FFRP, will continue to expand, providing clients such as SPU solutions to challenges that were no possible a decade ago.
Mike Ambroziak, P.E., is Primus Line representative- Southwest.
Latest Posts
- Maximizing HDD Tooling Longevity – Inspection, Maintenance and Replacement Tips
- Beneath the Frost: Trenchless Technology for Winter Resilience
- NCDD Completes HDD Intersect Under the Roanoke Sound
- Epoxytec Announces Winner of Manhole Photo Contest
- Watts Announces 2025 Backflow Hero Award Recipients