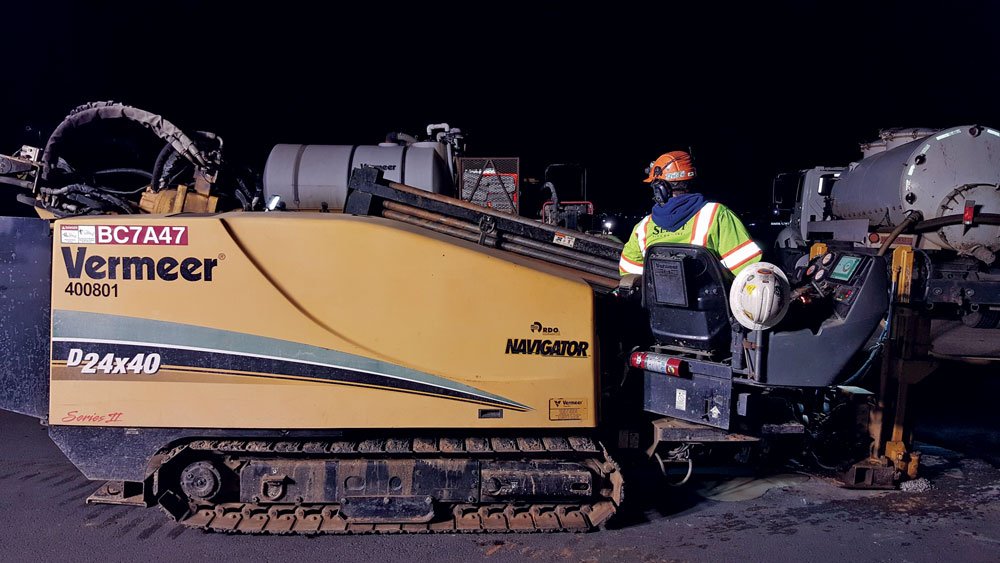
Airport Interference: Drilling Under Thick Rebar at San Diego International Airport
San Diego International airport is currently undergoing a rehabilitation project that focuses on repaving of runways and taxiways B1 and C1 and realignment of taxi way lighting, which is scheduled to conclude by year end 2018. Along with the surface paving operations, significant lighting work for signage, guard, and runways required running a new conduit below the taxiways. These taxi ways are heavily reinforced concrete about 2 ft thick.
Granite Construction Inc., one of the nation’s largest infrastructure contractors, was selected by San Diego County Regional Airport Authority as the general contractor for the rehabilitation project. Ensley Electric, a sub-contractor to Granite, awarded the taxiway conduit installations to Select Electric headquartered in Vista, California, which has more than 40 years of experience serving the electrical construction market in the San Diego region with primary focus on transportation infrastructure projects. Among their focus areas are traffic signals, highway lighting and electrical systems, airport lighting and electrical systems, and underground electrical conduit Installations to name a few.
RELATED: A ‘Wireline’ Bore In Heavy Interference — Without A Wire
The scope of the conduit installations comprised about 12 different HDD runs, all consisting 2-in. HDPE pipe, most of them single conduits with two conduits containing seven and eight pipe bundles. These conduits were primarily for power although fiber for communications will be included in one of the bundled runs. Planned depths of 6.5 ft with average length of 500 ft.
Knowing the thickness of typical airport concrete with reinforcement mesh (rebar), Select Electric suspected that there might be issues with tracking the bore and prior to drilling, Select Electric had to prove to the airport authority that the bores could be accurately tracked under the taxi ways. To test this, Select Electric decided to push its DigiTrak Eclipse transmitter down a storm drain running under the concrete to test the accuracy. The storm drain location was known and at a depth of about 6 ft. Once the Eclipse transmitter was inside the storm drain, the Eclipse depth reading was about 11.5 ft and the location was not correct. According Select Electric general foreman Keith Beagin, “The airport authorities required proof that we could accurately locate and control the shots under the taxi ways” and using the Eclipse was obviously not going to work.
It was clear that the heavy rebar was proving too much for the Eclipse system and the inspectors onsite would not allow drilling to commence given the test results. Select Electric had heard positive reports of the DigiTrak Falcon system, manufactured by Digital Control Inc. (DCI) and reached out to DCI field service manager Rick Johnson, to schedule a demonstration of the Falcon F5 system and, in particular, the Sub K (very low frequency) transmitter.
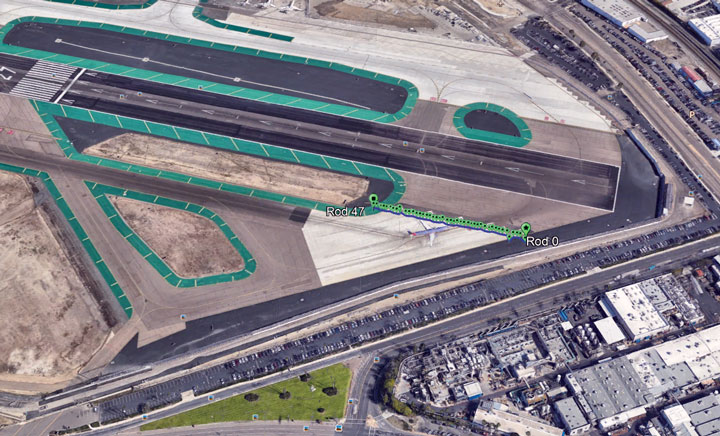
The aerial shot is a picture from Google Earth and the data came from the receiver’s iGPS module. Every time the locator recorded depth data, the receiver’s position is recorded using GPS, showing the actual path of the bore.
Interference
Interference varies from site to site and often over the length of a bore. DigiTrak Falcon systems allow the contractor to scan the intended bore path for interference, and then the system optimizes the operating frequencies and indicates the best bands of frequencies to use for that particular bore. To deal with passive interference (rebar for example) the Falcon system allows the contractor to select between 3 very low (0.3, 0.5 and 0.7 kHz) frequency bands, which provide the best option for success.
RELATED: “A Locator’s Odyssey” — Identifying and Dealing with Interference
Given that the bores were under active taxiways, the drilling operations could only take place between midnight and 5 a.m. This also meant that premobilization could not start until midnight and the machine had to be gone and site cleanup completed five hours later. This narrow time frame did not allow for much leeway.
The first pilot bore and demonstration took place in early February this year. Johnson spent about an hour explaining to the crew and inspectors how the Falcon system works and then to verify the performance of the system, a similar test as before was conducted. The sub K transmitter was run through the storm drain again and the Falcon system was generally unaffected. With the inspectors now satisfied, drilling could begin. The bore was logged using the Falcon locator and using the integrated iGPS module, each rod was recorded with a GPS coordinate.
Select Electric had mobilized its Vermeer D24x40 Series 2 drill rig and with Daniel Meza operating the drill and Duane Tyler locating, the pilot bore under taxiway B1 began around 2 in the morning. The airport was built on fill material so there was potential for differing ground conditions but on the first pilot bore the ground conditions turned out to be favorable, consisting primarily of sandy loam. Duane, having located with the Eclipse was quickly comfortable with the Falcon F5 and was impressed with the speed of the locator. According to Tyler, “Using the Falcon F5 compared to the Eclipse is like night and day. The information going from the sonde to the locator is very fast and the accuracy is improved. The rebar sonde almost completely eliminates false readings from passive interference and even the F5 regular sonde handles steel interference better than the Eclipse. It’s nice to have the right tools for the job.”
The pilot bore was completed about quarter to 4 in the morning and since the crew and rig needed to be off site and clean up done, the drill rods were left in the ground overnight. The following night the HDPE conduit was then successfully installed.
At the time of this writing, two more bores have been completed, consisting of seven and eight conduits respectively following the same pattern, pilot bore completed one night and the conduit(s) pulled back the following night. The bores have been around 500 ft long and all have been completed without any issues. After the successful first pilot bore, Select Electric purchased the Falcon F5 system and have been working with it since.
Beagin is excited to have a new tool at their disposal and stated, “The overall performance and capabilities of the F5 is very impressive, and we would have not been able to accomplish these specific drills without it. The technical and customer support we received from Digital Control was equally as enlightening and second to none. With their support, we were able prove and show off the types of drills we can now accomplish on any job, in any location, and in any environment”.
Siggi Finnsson is a product manager at Digital Control Inc.