A Colossal Bore
January 1, 2009
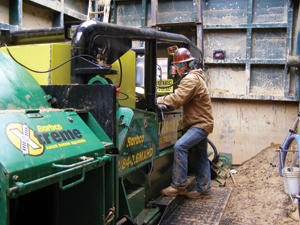
A drive of this diameter would typically be spec’d for a tunnel boring machine (TBM) or hand-mined. Nevertheless, the 130-ft length of the drive put it in a no-man’s land method-wise. The length is just short enough that a TBM might be prohibitively expensive to deploy, but just long enough that hand-mining would be too time-consuming. Auger boring seemed like just the right fit given the length and the soils, but no bores of this diameter had ever been performed. In fact, no manufacturer made such a machine.
The primary contractor, John D. Stephens Inc., has a lengthy history of infrastructure and utility work in the area. Subcontractor Strack Inc. is another longtime area contracting force with a great deal of experience and had already completed a few runs when it approached the crossing beneath the Norfolk Southern Railroad.
“We had done two runs with TBMs,” explains Whit Grahm, general superintendent with Strack. The TBM drives were 460 and 230 ft. “When we got to the railroad, though, we wanted to take a different approach.”
In fact, the crossing was specified as a shielded hand-mining operation. Auger boring was not initially considered for the crossing. The railroad was concerned with settling given the diameter and depth of the drive. More importantly, an 84-in. diameter auger boring rig was unheard of.
“No,” Grahm chuckles. “They wouldn’t have spec’d it that way because they didn’t know of such a machine.”
Strack approached the railroad with a proposal to complete the drive with auger boring. The railroad was initially hesitant about auger boring, but they eventually approved the drive. Now all that was left was finding an 84-in. auger boring rig. Fortunately, Strack knew just where to look.
East Canton, Ohio-based Barbco Inc. has been manufacturing auger boring machines since it was founded in 1989 by James S. Barbera. Over the years, Barbco has been no stranger to innovative solutions to meet the increasingly complex demands of its customers’ projects.
“Many customers have inquired about bigger machines over the years,” says Dave Barbera, vice president of Barbco Inc. “But none have taken the plunge and gone ahead with the machine.”
“We had developed larger machines on paper,” adds Tony Barbera, also Barbco vice president. “We’d researched the main issues with building a bigger machine – horsepower and torque and so on – so we had a base to work from when Strack called us.”
The Barbco team made careful assessment of what an 84-in. machine would require from the gearbox and drivetrain to handle the torque Strack required – and then they exceeded those requirements.
Upsizing the power meant increasing other parts as well. “Everything from the pushbar to the track rails has to grow,” explains Ken Clever, Barbco vice president of sales. “Everything about the machine has to be bigger.”
Everything including safety. “That’s something that shouldn’t be lost in all of this,” Dave Barbera says. “We wanted to make this machine as powerful as we could, but also as safe as we could.”
To that end, the machine can be controlled via radio remote and a tip-switch feature was installed to pull in the clutch and shut down the motor if the machine rolled – a potential danger in auger boring. “If the auger is out there spinning and hits enough of an obstruction to stall, that torque comes right back into the machine,” explains Tony Barbera. “With the kind of power we knew the machine would have, it was important to be extra careful.”
With the machine built, it was time to tackle the job. “The machine worked great,” Grahm says.
The machine mined through the clay and installed 84-in. OD wall steel casing. Grahm adds that the sporadic railroad ties in the bore path did not present a problem. No settlement along the alignment occurred.
“We’ve used that same rig on a few other crossings for that same project since then,” Grahm says. “We just did another 84-in. bore that went 115 ft.” As on the initial bored crossing, the machine made quick work of the soils without too much trouble.
Auger boring machines may not need to get much bigger – material strength and cost issues may become prohibitive. Nevertheless, Barbco is waiting eagerly for the next call for a bigger, badder machine. “If there’s a contractor out there who’s willing to push the limits,” says Dave Barbera. “We’ll build the machine that will do it.”
Greg Thompson is assistant editor of Trenchless Technology.