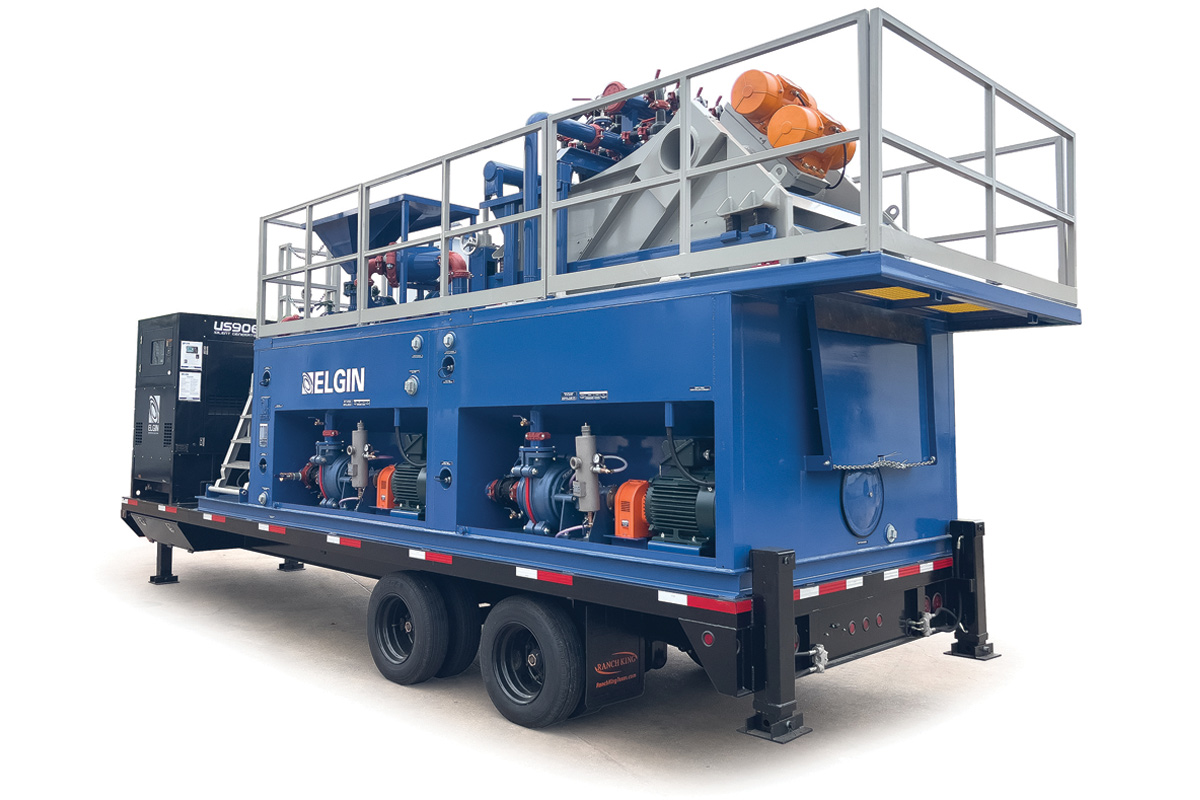
5 Steps to Optimize Your Mud System for Better Solids Control
Optimizing your mud system is essential for efficient drilling and cost reduction. By focusing on proper equipment, maintenance, training, and advanced technology, operators can optimize solids control, extend fluid life, and minimize downtime.
Here are some helpful steps for better liquid/solids separation.
Ensure a Balanced System
A balanced mud system is the cornerstone of efficient drilling operations, ensuring seamless integration of key components such as shale shakers, hydrocyclones, centrifugal pumps capable of processing fluid based off the capacity of the drilling rig.
This synergy effectively removes solids without overloading key components with an undersized reclaimer. Maintaining a well-balanced mud system is essential for effective solids control, cost reduction, and sustained success in drilling activities. By correctly sizing a mud system, operators can enhance drilling performance, minimize downtime, and reduce solids disposal costs.
Benefits of a Balanced System:
- Enhanced Rig Performance: Streamlined operations with minimal downtime.
- Extended Fluid Life: Solids removal on the first pass can extend drilling fluid lifespan by two to three times.
- Cost Savings: Reducing waste and fluid replacement lowers operational expenses and environmental impact.
- Improved Equipment Longevity: Properly sized and maintained systems increase the lifespan of components.
To maintain balance, Pietramale recommends choosing a mud system with a processing rate of 1.5 to 2 times greater than that of the drilling rig.
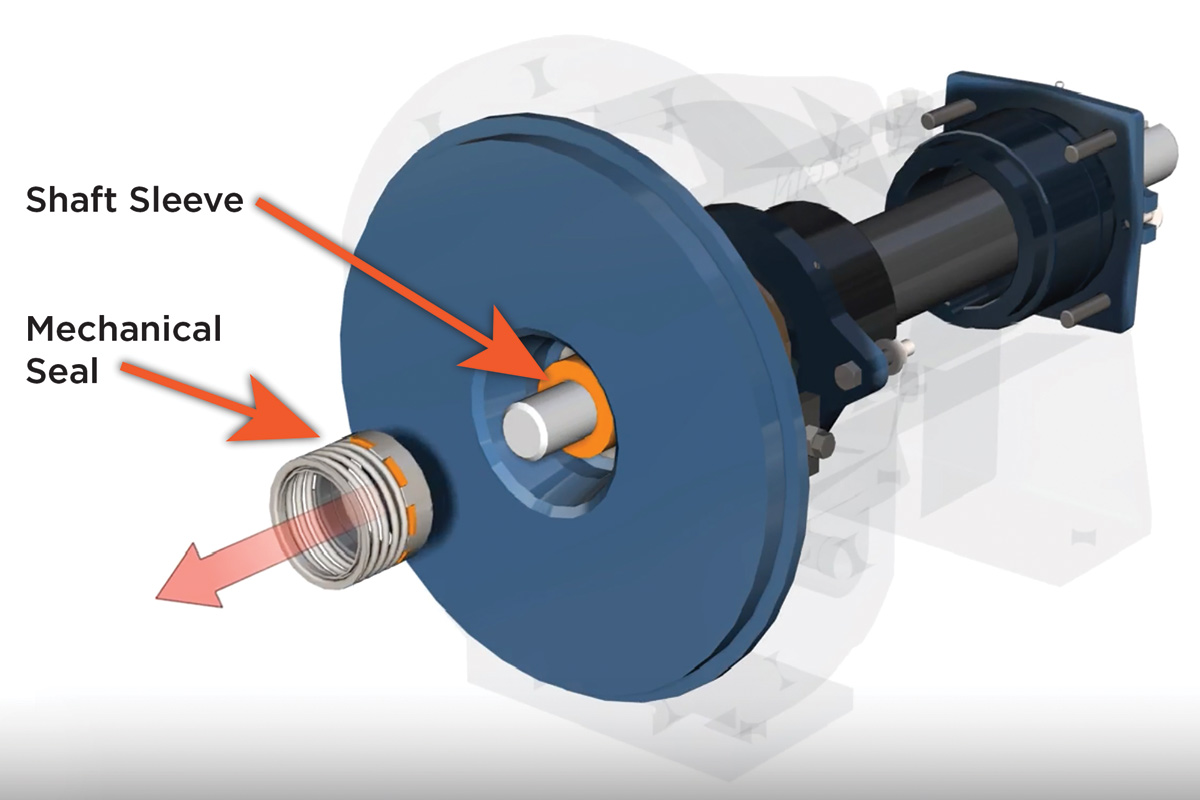
Prioritize Maintenance
Regular maintenance is critical for peak performance and longevity of your mud system. Neglecting maintenance can lead to inefficient operations and contamination risks, as worn or malfunctioning components fail to remove solids effectively.
Core Maintenance Practices:
- Shale Shakers: Inspect and wash screens daily, replace polyurethane strips or crown rubbers at 50 to 75 percent wear, lubricate vibrator motors, pump motors, and leveling jacks, and ensure proper alignment and secure wedge block installation.
- Pro Tip: To check if your screen is properly seated, stand at the discharge end of the shaker and step on the screen. If additional material discharges, it’s a clear sign that the screen isn’t securely in place. Proper alignment and fit require a team effort—ensure two team members work together to evenly install the screens and secure the wedge blocks, minimizing the risk of misalignment.
- Pro Tip: Always spray at an angle, not directly on the screen, and limit the pressure to a maximum of 1,000 psi. For optimal results, use an Elgin pressure washer, pre-calibrated to 1,000 psi for precision and safety.
- Hydrocyclones: Maintain adequate pressure (minimum 30 psi), inspect cones for wear, and flush to prevent blockages.
- Pro Tip: When the unit is idle, use a small hand pump (120V utility pump) to winterize the manifold. Insert the hose into the top threaded port or the main inlet pumping standard 50-50 radiator fluid through it, coating the manifold with coolant.
- Pro Tip: Apply weekly WD-40 or PB Blaster to all Victaulic clamps throughout the system as well as on the ball valves of the Desilter Manifold to prevent valves freezing in position and complicating inspections.
- Centrifugal Pumps: Align pumps properly, check seals and impellers, and avoid running pumps dry to prevent damage.
- Pro Tip: Address fluid leaks promptly, as they often indicate seal or shaft cover failure. A common but ineffective approach is adding packing, but this does not correct the root problem. The issue often lies not with the mechanical seal but with the shaft sleeve—this accounts for 90 percent of failures. Using the full kit not only includes the mechanical seal itself, but everything required to ensure a reliable seal and long-term performance.
Strategic Benefits of Preventative Maintenance:
- Extended equipment lifespan.
- Reduced operational costs and downtime.
- Enhanced solids removal and drilling efficiency.
By adhering to a consistent maintenance schedule, operators ensure reliable system performance across applications like horizontal directional drilling, waterwell, geothermal and microtunneling.
Select the Right Equipment
Choosing the correct equipment tailored to your operation is vital for effective solids control. Each component must function harmoniously to maximize efficiency and minimize downtime.
Key Components and Practices:
- Shale Shakers: Choose a shaker with a double-deck configuration for initial scalping and second-stage liquid/solids separation.
- Shaker Screens: Match screen sizes to drilling conditions and use API 13C standards for effective solids removal.
- Hydrocyclones: Ensure the right configuration of a desilter or desander hydrocyclone manifold based on the processing capacity for efficient operation.
- Centrifugal Pumps: Invest in abrasion-resistant pumps with thermal siphons for durability and run-dry protection and overheating.
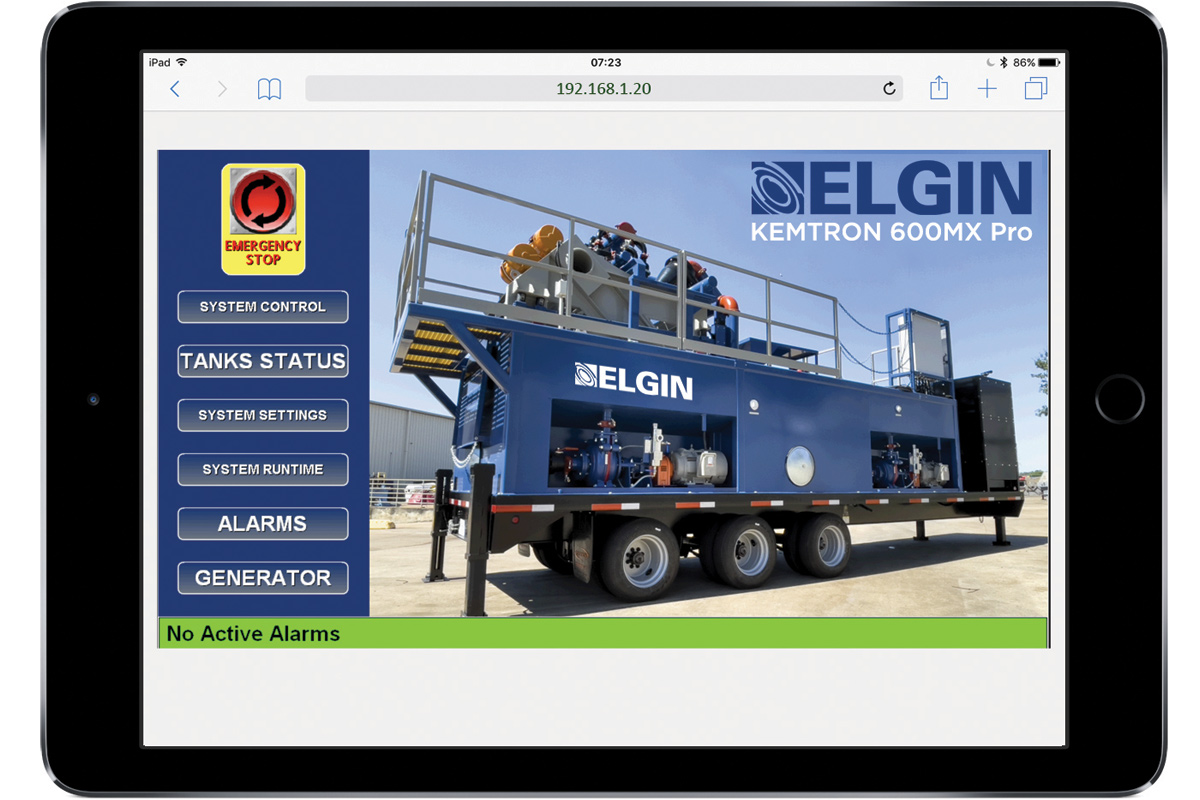
Advanced systems feature best-in-class screening surface area, abrasion-resistant pumps, and ceramic lined hydrocyclones.
These innovations improve efficiency, reduce waste, and lower costs.
Train and Certify Your Team
A well-trained team is as important as high-quality equipment. Proper training ensures efficient operations, reduces errors, minimizes downtime, and prolongs equipment lifespan. Skilled operators can identify and address issues before they escalate, prevent costly disruptions, and maintain compliance with safety and environmental standards.
Steps for Training:
- Certify operators on core equipment like shakers, pumps, and centrifuges.
- Provide hands-on training for screen selection, hydrocyclone monitoring, and pump maintenance.
- Offer periodic refresher courses and collaborate with OEMs for support and resources.
Leverage Advanced Technology
Modern mud systems incorporate advanced technologies to enhance solids control, reduce downtime, and improve efficiency.
Key Innovations:
- Variable-G Shakers: Allow seamless adjustment of G-force for optimal solids removal when dealing with sticky material.
- Multi-Pass Cleaning: Improves performance of shakers and hydrocyclones.
- Smart Controls: Wi-Fi-enabled panels enable remote operation and monitoring.
- Durable Components: Ceramic-lined cones and rubber-lined pumps withstand abrasive conditions.
Advanced systems offer cutting-edge features, variable-speed dual-motion shakers, abrasion-resistant pumps, high-shear mixing hoppers, and system automation controls.
Conclusion
Optimizing your mud system is essential for maximizing solids removal, improving drilling efficiency, and reducing costs. By maintaining a balanced system, prioritizing regular maintenance, selecting the right equipment, training operators, and leveraging advanced technology, companies can achieve superior performance and long-term success. Investing in these practices not only enhances operational efficiency but also ensures compliance with industry standards and environmental regulations.
Raymond Pietramale is director of marketing at Elgin Separation Solutions.