What’s Holding Back the Open-Cut Sewer Industry From Using HDD?
April 1, 2008
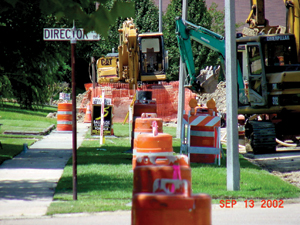
The Metropolitan St. Louis Sewer District (MSD) and many other sewer districts worldwide look forward to using HDD for gravity flow installations, but they want the HDD industry to match the open-excavation specifications. Engineers do not want to make design changes simply because HDD cannot consistently install tight grades below .50 percent. We must give some credit to those HDD firms that have an employee or owner who has developed the special touch for installing gravity flow sewer mainlines. The volume of work that the sewer industry offers will require many crews installing mainline sewer pipes and the construction method of using HDD must be consistent and trainable.
However, the lack of a tight-fit, back reamed hole required to prevent pipe flotation has limited or often precluded the use of HDD for all but a very limited sector of the sewer industry. Engineers and utility owners have only considered utilizing HDD when potential capital cost-savings were extremely high and there was no question that the savings would be double or triple the likely future maintenance costs. Therefore, most sewer mains installed by HDD in the recent past have been located in areas where significant variations in the design grade were available and noticeable sags and dips were reluctantly accepted. This approach has held up HDD to being widely accepted by the public works industry. HDD is a good construction technique and in order for the method to be widely accepted by the sewer industry, procedures must be developed to assure the utility owners that the technique is consistently reliable.
What Sewer Utility Owners Face
Most new or replacement sewer installations are in areas where there is just one-shot at getting the main in the right place and an attitude of “Well, that is close enough” cannot be tolerated. What the sewer industry has been lacking with respect to using HDD as a construction method is a way to be reasonably assured that the main will be installed in its proper place prior to the full length of the pipe actually being put in place. In open-trench applications, an inspector can physically see sections of the pipe as the main is installed and to verify the location of each joint by survey techniques. In microtunneling, a laser sight is used to determine the relative real world location of each section of the tunnel as it moves through the ground, within hundredths of a foot.
Most other sewer construction techniques can use the same approach of using reasonable means to verify the location of the installation of the main line pipe prior to actual completion. Directional boring typically utilizes locating devices that relay information that indicates where the stem location should be within some range of a foot, based on the depth of the locating device.
With traditional HDD methods, the true accuracy of the pilot stem information can only be determined after the pipe is installed and some kind of inspection device is used to see how the pipe flowline looks. This wait-and-see approach is stressful to everyone involved and can result in significant problems for the contractor, the utility owner and the general public later if the main line pipe is not correctly installed.
HDD & Gravity Sewers
Two key elements must be addressed in order to successfully install gravity flow sewer on a consistent basis at slopes of less than 1 percent utilizing HDD.
First, the locating equipment will need to be improved to allow for more reliable indications in all
areas of intercity projects with airwave interferences and wire mess interferences of the actual location of the beacon housing for both line and grade or a process will need to be used that provides accurate verification of the beacon housing at certain points throughout the installation.
And secondly, the pipe should be installed in a back reamed hole that is not much larger than the maximum outside diameter of the pipe while still preventing pressure buildup in the hole. Displacement of the volume of soil of the pipe being installed is the key factor to preventing this pressure buildup. By having a bore hole that is close to the same size as the maximum outer diameter of the pipe, the potential deflection and flotation of the pipe in the hole during installation is limited, both with respect to line and grade.
In order to address these issues, a process must have a way of displacing the physical volume of soil or fluid that it will take to install the pipe. The process should also have a way of verifying the actual location of the drill string at certain points along the path of the installation, primarily due to limitations in current locating equipment reliability at any significant depth.
Such a process is currently available to contractors. The patented ArrowBore process has been developed by Trenchless Flowline Inc., a Columbia, Mo.-based technology development company that currently specializes in developing trenchless construction technologies with full focus on the open-excavation sewer and water industry.
The ArrowBore method complements existing HDD electronics and incorporates physical verification of the location of the directional boring machine’s stem as it is advanced through the ground. Excavations, termed “sight-relief holes” are used at certain points throughout the bore path to provide both the contractor and the utility owner’s inspector with a way to visually inspect that the drill stem is installed in the correct place prior to final installation of the mainline pipe. Two important things happen, the boring crew is held accountable based on the documentation at each sight-relief hole and projects are consistently completed. The process takes two weeks to learn and uses existing open-excavation employees with little or no experience in HDD.
Once the pilot bore is completed, a back reamer sized just slightly larger than the main pipe, typically ¼ to ½ in. larger than the outside diameter (O.D.) of the pipe is connected and a hole is reamed ahead of the pipe to be installed. The distance between the back reamer and the pipe is determined by the greatest distance between the sight-relief holes. The sight-relief holes allow for the relief of fluid pressure, while a portable vacuum machine removes the excess spoils created during the placement of the main. The “tight-fit” hole eliminates the possible deflection and flotation from line and grade that can occur when a hole is reamed to a size 1.25 to 1.5 times the O.D. of the pipe as is general practice with conventional HDD methods. ArrowBore also allows projects to be installed at depths that vary from 15 to 25 ft with little change in cost. Much deeper depths are achievable and can possibly omit the need for lift stations in some areas.
A Potential HDD Market?
The largest potential market for HDD sewer installations is in areas that are currently constructed utilizing open-excavation methods. Although HDD machines are a little more sophisticated to operate than most open-excavation equipment, with training and personal initiative, open-excavation operators can easily learn the machines.
HDD requires smaller beginning pits, typically the size of excavations required for placing manholes so excavation costs are less. Typical sewer length installations have relatively little adverse impact when using HDD and often a longer installation is less expensive per foot than a shorter one since mobilization and preparation costs can be allocated over the longer distance. Another significant advantage for contractors includes the fact that the machines can be used for installing other types of utilities during periods of low volume sewer work.
Most areas considering the use of HDD are installing new sewer systems to eliminate septic tanks, installing a new sewer to replace the existing mainline system at deeper depths to allow for future flow, or reverse flow the mainline system to a new treatment plant. HDD in high water table areas is great due to the fact that HDD doesn’t require dewatering of the mainline area that can disrupt the lives of home and business owners.
Techniques involving processes and improved locating equipment are rapidly improving the viability of using HDD for gravity sewer applications. By accepting it as a potential method, the public works sector can help to refine, promote and improve the use of this incredibly diverse tool and help to achieve the goal of constructing new, safe and reliable sewer and water lines while minimizing the impact to the general public.
Ted R. Dimitroff is president of Trenchless Flowline Inc., Columbia, Mo.