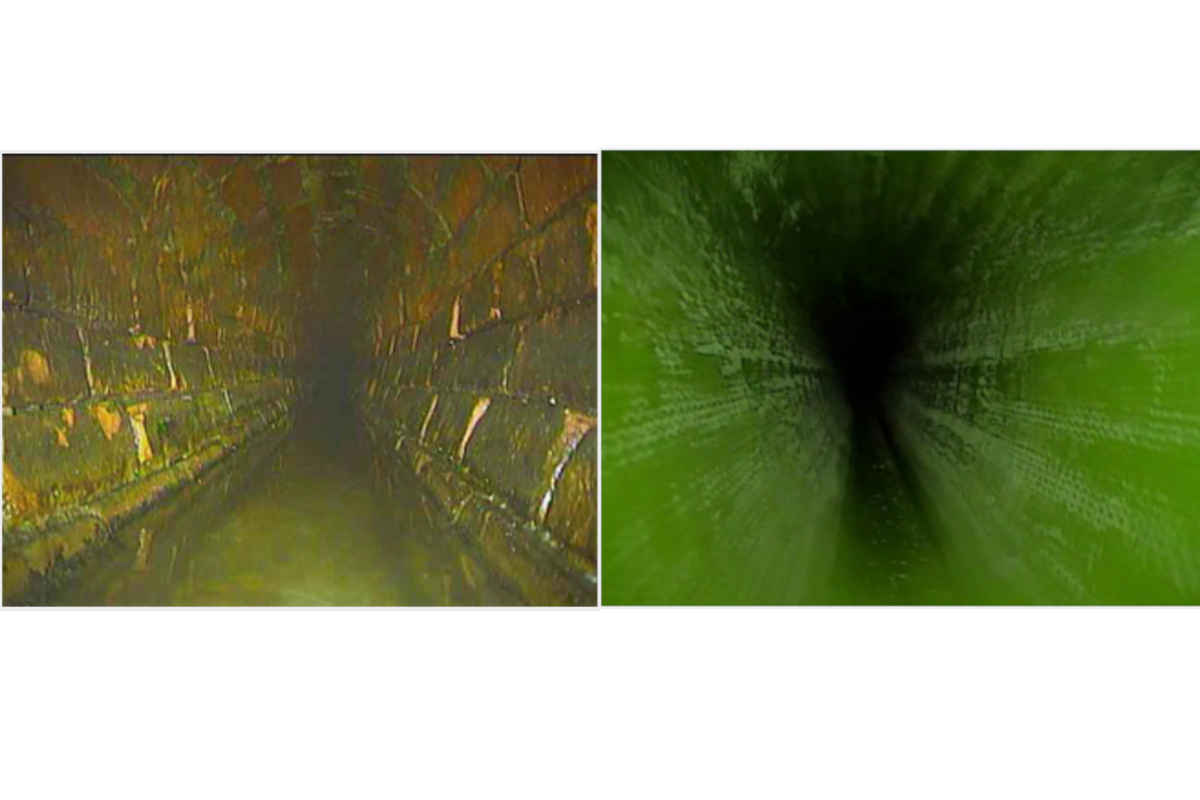
UV CIPP Lining an Egg Shaped to Circular Transition Pipeline
Cured-in-place pipe (CIPP) lining has become a reliable and cost-effective method for rehabilitating aging or deteriorating pipelines.
However, not all pipelines present standard challenges — particularly when transitioning between differing shapes and sizes. A recent project in Atlantic Canada showcased the expertise and ingenuity required to tackle such a complex pipeline rehabilitation.
The project involved lining a transition pipeline that shifted from a 570-mm x 420-mm brick egg-shaped profile to a 375-mm circular brick pipe.
This case study highlights the innovative techniques, precise coordination, specialized equipment, and rigorous quality assurance measures that ensured the project’s success.
Project Background
The pipeline in question was a critical piece of infrastructure with significant hydraulic and structural requirements. Its unique geometry posed challenges that went beyond conventional CIPP lining projects.
Egg-shaped pipelines, often found in older infrastructure, were historically used for their hydraulic efficiency. However, their rehabilitation requires adherence to distinct design standards — in this case, MOP145 for egg-shaped sections and ASTM F1216 for circular pipes. The transition between these shapes added complexity. It necessitated accurate measurements and close collaboration with the lining manufacturer.
The client required that the rehabilitated pipeline maintain its original hydraulic capacity. Ensuring structural integrity over the long term was essential. Additionally, third-party testing was mandated to independently verify compliance with design specifications and performance standards. This added an extra layer of quality assurance to the project.
Key Challenges
1. Transition Between Profiles
The shift from a 570-mm x 420-mm brick egg-shaped pipeline to a 375-mm circular brick pipeline required precise measurements and careful planning. Miscalculations could lead to improper CIPP liner fit, compromising the pipeline’s structural integrity and hydraulic performance. Furthermore, ensuring a smooth transition between the two profiles was critical. This prevented any points of failure or reduced flow efficiency.
2. Differing Design Standards
Egg-shaped and circular pipelines are governed by distinct design requirements. The MOP145 standard accounts for the unique load distributions and structural properties of egg-shaped pipelines. In contrast, ASTM F1216 applies to circular pipelines. Ensuring the liner met both standards across the transition required thorough engineering review, design verification, and close collaboration with the client and lining manufacturer.
3. Specialized Equipment Requirements
The irregular geometry of egg-shaped pipelines necessitated the use of specialized inspection, installation, and reinstatement equipment. Conventional CCTV cameras, cutters, and UV light trains are typically designed for circular profiles. However, in this case, unique wheelbases were required to keep the equipment stable and centered within the egg-shaped sections. Without these adaptations, the equipment risked tipping over or failing to maintain alignment, jeopardizing the inspection and installation processes.
Project Methodology
1. Preliminary Assessment and Design
A comprehensive assessment of the pipeline’s condition was conducted using advanced CCTV inspection equipment. The equipment was outfitted with a specialized wheelbase for the egg-shaped sections. Accurate measurements of the pipeline’s dimensions and geometry were taken. This ensured the liner would fit seamlessly across the transition. Coordination with the lining manufacturer played a pivotal role during this phase. The custom liner accommodated the transition, ensuring a tight fit and adherence to the applicable standards for both profiles.
2. Preparation and Cleaning
Prior to installation, the pipeline was thoroughly cleaned to remove debris and prepare the surface for the liner. Specialized equipment ensured the cleaning process was effective without causing damage to the aging brick structure. Particular care was taken in the transition area. This ensured a smooth and consistent surface, which was crucial for proper liner installation.
3. CIPP Liner Installation
The CIPP liner was impregnated with resin and carefully transported to the site. Installation was performed using UV curing technology. This method offers precise control and faster curing times compared to traditional steam or water curing methods. The UV light train, equipped with a specialized wheelbase, maintained stability and alignment throughout the egg-shaped sections. This ensured even curing.
To meet third-party testing requirements, samples of the liner were cured and tested off-site under controlled conditions. This verified the resin’s mechanical properties and adherence to design specifications.
4. Reinstatement and Quality Assurance
Following installation, lateral reinstatements were completed using a robotic cutter adapted for egg-shaped profiles. Final inspections were conducted to verify the liner’s integrity, fit, and compliance with the design standards.
Outcomes and Lessons Learned
The successful completion of this project demonstrated the importance of meticulous planning, specialized equipment, effective collaboration, and robust quality assurance measures.
Key Outcomes
- Seamless Transition: The custom liner fit perfectly across the transition from the egg-shaped to circular profile, maintaining structural integrity and hydraulic efficiency.
- Compliance with Design Standards: Adhering to both applicable design standards ensured the rehabilitated pipeline met all applicable regulatory and performance requirements.
- Specialized Equipment Utilization: The use of unique wheelbases for inspection, lining, and reinstatement equipment was critical to overcoming the challenges posed by the irregular pipeline geometry.
- Independent Validation: Third-party testing provided an additional layer of assurance. This validated that the project met the highest standards of quality and performance.
Conclusion
This project highlights the complexities involved in rehabilitating non-standard pipelines with CIPP. It underscores the importance of leveraging expertise, precision, and innovation to overcome these challenges.
By combining accurate measurements, tailored designs, specialized equipment, and independent third-party testing, the team successfully restored a critical piece of infrastructure in Atlantic Canada. This work extended its service life and improved its performance.
As infrastructure continues to age and present unique challenges, the lessons learned
Jocelin Bourgeois, P.Eng., MBA is an engineering associate at Inversa Systems.