U.K. Water Companies Turn to Relining to Rehab Pressure Pipes
May 1, 2008
With increasing pressures from government and industry regulators to address water supply system leakage rates and the state of repair of deteriorated pipes, water companies across the United Kingdom are tuning in to the advantages provided by many of the trenchless technologies currently available.
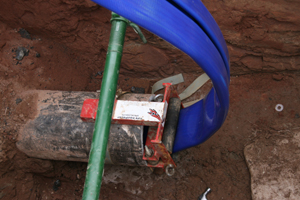
Currently offered under the newly created Insituform Blue business division, the Thermopipe system is one of a number of specialist renewal products used by ITL for the rehabilitation of pressure pipe networks.
The Thermopipe system is a polyester-reinforced, polyethylene structural lining system that offers advantages for the rehabilitation of pressure mains from 60 to 300 mm. The lining system provides a full structural renovation of the host main at a pressure rating of 170 psi (also at 230 psi for 100, 150 and 200 mm). The liner system also stops leakage by bridging and sealing holes and faulty joints, improves the quality of water, reduces social cost because of low footprint and minimal downtime and is a cost-effective way of extending the life of water supply infrastructure systems with its 50-year design life.
The system is designed for the rehabilitation of distribution water mains and other pressure pipe systems such as sewer force mains, fire water mains and industrial pressure applications. It is supplied as a factory-folded ‘C’ shape liner, which is winched into the host pipe from a reel located at one of just two main access pits required for an installation. Once winched into place, the liner system utilizes air pressure and steam that is applied to the inside of the liner to revert it to its fully round shape within the host pipe. Once inflated and heated, the liner forms a close-fit within the host pipe, creating a jointless, leak-free lining system able to carry the full pipe system internal design pressure, independent of the remaining structural strength of the host pipe. The installation process is simple and most installations can usually be completed within an eight-hour time period.
Several projects in the United Kingdom have been successfully carried out using the system.
Perryfield Road Project
A recent project carried out by ITL for Severn Trent Water in association with Severn Trent’s main contractor, Balfour Beatty has highlighted just how effective the Thermopipe system can be on water main rehabilitation projects.
The project comprised the rehabilitation of 1,720 m of 300-mm diameter water main in the Perryfield Road area of Bromsgrove, south of Birmingham. The rehabilitation was necessary because over time the pipeline had required a number of repairs to this section of pipe.
The main itself comprised a straight run of pipeline, which contributed to the quick and efficient completion of the project, well within the anticipated timeframe. ITL started work on the lining operations on Feb. 20, with a due date for completion of March 21. As it turned out, this timeframe was more than what was required. Excellent cooperation between Severn Trent, Balfour Beatty and ITL enabled the water main to be completely rehabilitated and restored to service in just eight working days. This just shows that effective planning, cooperation between the various involved parties, the use of an experienced rehabilitation contractor and the immediate provision of materials from ITL can come together to give massive savings in time, effort and cost. In all, seven individual liner installations were completed on the project.
This combined effort allowed the client to bring its rehabilitated main back into full service well ahead of its expected schedule. This in turn meant a significant reduction in disruption to local residents, businesses and the usual major traffic flows experienced in the area, which might otherwise have occurred over the longer, scheduled timeframe. The reaction to the results were nothing but positive.
Nigel McGuinness, acting mains renewal manager for Severn Trent Water, said: “Using conventional techniques, the disruption to traffic and local residents would have been too great. This solution allowed an effective and environmental solution to a difficult project.”
And Balfour Beatty Utility Solutions regional manager David Wilson said: “The project had to be completed within a very short timescale and I was impressed with the professionalism and commitment of all involved.”
John Beech, ITL business development manager, said: “We were extremely pleased to be able to bring this project to a close on such a quick timescale. We were able to achieve this due to our position as both contractor and materials provider which, alongside our 30-plus years of experience in the sector, is one of our biggest advantages in the U.K. renovation industry. Being able to ensure that materials are available as and when required without the need to rely on third party providers puts us in a very string position when it comes to project completion.
“The massive time-saving on the Perryfield Road project was, however, only possible because of the excellent cooperation between ourselves, Balfour Beatty and Severn Trent to ensure that the work sites were all ready and waiting for the renovation installations when they were needed. Praise must also be given to the ITL crew, which included Dave Gascoigne, Graham Dobie, Garry Farrel and Lawrence McGovern, without whose efforts this project could not have been completed in record time.”
Crossing the Ness River
In April 2007, Scottish Water undertook a renovation project in the town of Inverness designed to bring back into full service a 100-year-old water main running under the Ness River.
The route of the 150-mm diameter cast iron pipe runs under the river bed for a distance of about 100 m between the Ness Bank Church on the east side of the river and St. Andrew’s Cathedral on the west side. In 2005, the pipe was taken out of use when it became damaged by what was believed to be natural movement of the riverbed over previous decades. However, subsequent CCTV camera inspection revealed that it would be possible to effectively renovate the water main and bring it back into service with minimum expenditure.
The main water feed across the Ness River was maintained because there are four separate water mains that cross the River Ness at various points. The supply network can be adjusted so that different parts of Inverness can be fed from either Loch Ashie to the south or Glen Convinth to the west.
For the project, Scottish Water decided to use the Thermopipe system. “Rather than replacing the pipe, we were able to insert a new one inside it. Since taking the main out of service, we have still been able to supply the west side of Inverness, but it made sense to bring it back into use if it were technically and economically feasible,” explained project manager Jim Rafferty. “It will provide yet another option for the already robust supply network and could help improve water pressure to 286 properties at peak times when households draw large volumes from the system.”

The work took about four weeks to complete. Overall, the lining operation was completed without any problems other than some minor disruption on the west side of the river where some new ductile iron pipe had to be laid.
In terms of the actual liner pulled in, this operation took just 90 seconds to achieve over the 100-m lining run length, with the folded liner being provided off a pipe coil. Overall, the client was pleased with how the lining operation was achieved and its ultimate result.
Looking to the future, Scottish Water is considering a further water main to cross the river and the Caledonian Canal, which will depend on Highland Council’s chosen route to complete the Southern Distributor Road that could involve bridges or an aqueduct.
Over the next three years, Scottish Water expects to invest £154 million in the Highland Council area to maintain already high-quality drinking water and sewage treatment, lay new pipelines and increase capacities to enable the growth of communities.
Hildern Park
On another project, this time for client Southern Water, ITL completed another installation at Hildern Park School. This work was done through the water company’s main contractor, Holleran Mouchel Parkman Joint Venture and as part of the Southern Water K4 Rising Main Replacement Program.
The pipeline serving the school had experienced a number of burst incidents in previous years and was in need of renovation or replacement. However, the location of the existing pipe and its routing beneath the school building meant that an open-cut option was simply not viable, so a trenchless solution was needed. Also, because of the need to maintain flows through the renovated pipeline, any solution had to minimize any capacity losses. The solution also had to minimize the disruption to the location while offering a speedy installation.
The renovation work comprised two separate pipe lining operations. The pipes in question were of asbestos cement construction and at 225-mm diameter, over lengths of 310 m. To minimize disruption to the operations of the school, the work was completed during the summer break.
In the end, the lining works proceeded without incident. Again, the folded liner was pulled into the host pipe from a pipe coil trailer, which helped to minimize the working site footprint considerably.
The advantage of using the Thermopipe system in this case was that it achieved all the requirements of the project in terms of minimum capacity loss, time on site and ultimate longevity of the newly restored pipeline without any interruption to the running of the school.
Ian Clarke is president of NoDig Media Services, based in the United Kingdom.