
Total Trenchless Tackles Twin Casing Pipe Rams in Beautiful Banff
In North America there are few areas as beautiful and well-regarded as Banff National Park and Lake Louise in Canada. This majestic area of the Rocky Mountains is known for its amazing scenery, breath taking views, glacier-fed streams and lakes, as well as abundant wildlife.
Approximately 80 miles west of Calgary, Alberta, the park is accessible via the Trans-Canada Highway. The highway zigzags its way from the western edge of the Calgary prairie into the heart of the Canadian Rockies in Banff National Park. Preserving the beauty of the surrounding area, as well as the access to the park is a high priority for Parks Canada. It’s also not unusual that trenchless construction would be specified for a utility replacement project in the park.
The Lake Louise Water and Sewer Upgrades project included the replacement of existing water and sewer mains under the Trans-Canada Highway. Utility contractor Total Trenchless, Calgary, AB, was subcontracted to installation twin 30-in. casings, 280 ft, under the highway to house the water and sewer mains.
“The project owner was Parks Canada as the project fell within the limits of Banff National Park. The Trans-Canada Highway is pretty much the only passage through the Rocky Mountains. There’s a small development on the north side, Harry Hills, near Lake Louise that needed to have some utilities replaced, two 4-in. diameter carriers,” says Total Trenchless safety/field operations supervisor Jeff Corsie. “One was a force sanitary sewer main and one was for water supply. Parks Canada specified that the lines run through casings under the highway. We were brought in to install those twin casings.”
For the project, guided pipe ramming with pilot tube was specified for installing the casings under the highway.
For the installations, Total Trenchless used a 24-in. diameter Grundoram Taurus pipe rammer from trenchless equipment manufacturer TT Technologies, Aurora, Illinois, combined with a pilot tube system. According to TT Technologies pipe ramming specialist Rick Melvin, this combination of methods be really effective.
He said, “Pairing pipe ramming with guided boring or the pilot tube method can result in extremely accurate casing installations. The line and grade control system and a hydraulic jacking frame allows contractors to place pilot tubes through the ground very accurately. Once the pilot tubes are in place, an adapter is used to make a transition to the casing that’s being installed. The casing basically follows the pilot tube’s path, resulting in a very accurate, line and grade installation.”

Total Trenchless
Total Trenchless is an indigenous-owned company formed in July 2018, with just a few seasoned trenchless personnel. The owner and staff had previous experience working in the industry. The company offers horizontal auger boring, pipe ramming, guided horizontal auger boring, guided pipe ramming, pipe jacking and pipe bursting. The utility contractor performs trenchless services all over western Canada and has provided service to deep and shallow utility constructors, the oil and gas sector, irrigation contractors and railways for drainage improvements.
According to Corsie, the formation of the company proved to take place at a good time. He said, “The opportunities came fairly quickly. By the end of 2018, the company had grown to around 10 employees and the fleet of equipment had doubled. Since then the company has grown to 40 employees and the company owns an impressive fleet of trenchless equipment.”
Its trenchless fleet includes auger boring machines, several pilot tube units, a range of pneumatic pipe ramming tools including the 14-, 18-, and 24-in. rammers. Recently the company added the world’s most powerful hammer, a 32-in. Grundoram Apollo pneumatic rammer to its toolbox.
Pilot Tube Hits the Mark
According to Corsie, working inside of the national park required additional precautions such as spill kits and preparations for potential losses of control products, among other things. There was also an engineering group present to make sure that operations were meeting all of the regulatory requirements.
The pit construction and pad for the pilot tube and pipe ramming were completed by the prime contractor and consisted of mostly native materials. Corsie said, “We set up our auger bore machine and track. The auger bore machine just backs up the pilot system during the pilot tube boring. The unit is secured to the tracks and butts up behind the pilot tube machine to support it, so that nothing moves during the pilot tube drive. Once everything was set up, we sent the 4-in. diameter pilot tube through.”
Once the pilot tubes were in place, Total Trenchless crews moved to the next phase, pushing in another pipe. Corsie explained, “We pushed some heavy wall 4-in. pipe behind our pilot tubes. The reason is, if we connected the 30-in. casing to the pilot tubes and rammed that, all of the internal components of the pilot tubes can shake loose. That creates a lot of expense. So, after the pilot tubes are installed, we welded on an adapter to make the connection to the 4-in. pipe. We pushed that through the ground, in approximately 20-ft lengths, removing the pilot tubes on the other side as we went.
“Once the heavy wall 4-in. pipe was in place, another adapter was attached to the end of the pipe. The auger bore machine was used to push that configuration just into the ground to get it started. From there the pipe rammer takes over.”
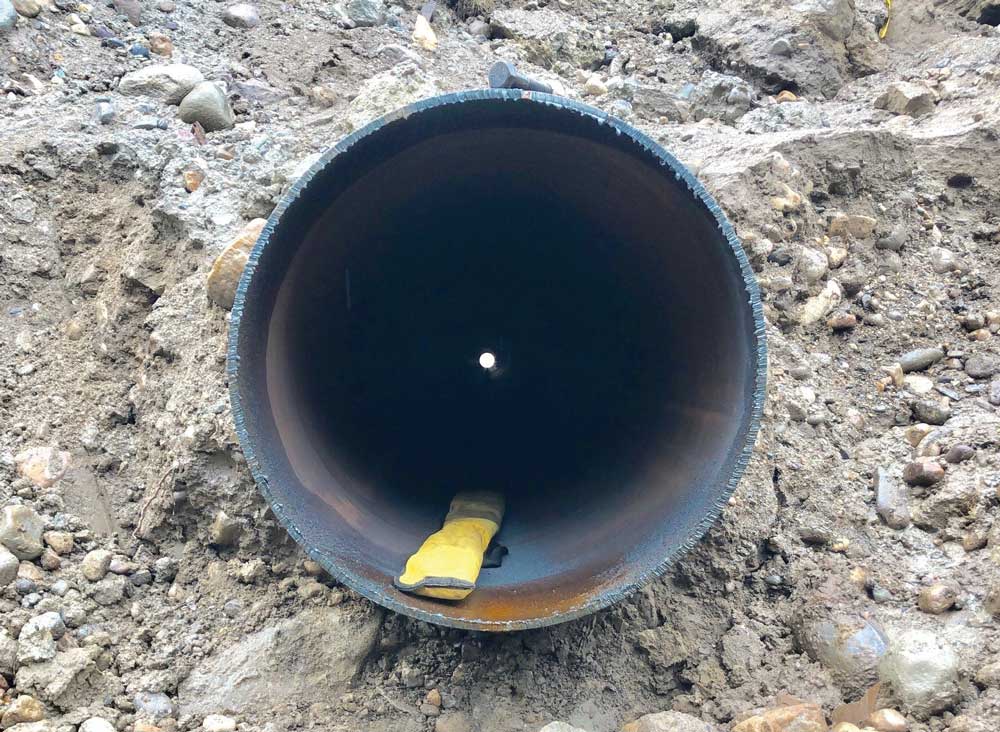
Rammer Time
Next, the auger bore machine was removed. Its rails, however, were used as a track for the 30-in. casing. The first section of casing was then moved into position and welded to the adapter at the end of the 4-in. pipe. Total Trenchless crews than proceed to make the connection between the ramming tool and the back of the casing.
Melvin said, “Properly and securely connecting ramming tool to the casing is done with pipe ramming gear, components that are manufactured specifically for certain pipe and tool diameters. Occasionally there is a need to fabricate connections and that is done on a project-by-project basis. But the standard ramming gear usually consists of a series on segmented and tapered ramming cones.”
In this particular case, 30-in. segmented ram cones were used to connect the 24-in. diameter Taurus to the casing. Melvin said, “These segments transfer percussive force to the casing. They are very important because they also help minimize wall flaring.”
Total Trenchless crews used an 1,800-CFM air compressor to power the pipe rammer, which was supported with slings and an excavator. Each 30-in. casing segment was 40 ft in length and ramming progressed at 90 to 120 minutes per segment. The installation traveled from the north side of the highway to the southside. As the casing advanced through the soil, lengths of 4-in. pipe were removed at the south end. Once a casing segment was installed, crews removed the rammer and moved the next one into position and welded it in place.
According to Melvin, this is a critical step. He said, “Welding is a key component to a successful pipe ramming project. You’re always going for 100 percent, full-penetration welds. But welding takes time. With the thicker casing requirements like the project in Banff, that means longer weld times.” Full penetration welds on the .750-in. wall, 30-in. pipe took 3.5 hours each with two welders working on it.
Corsie said, “About halfway through the ramming we cleaned out the spoil in the casing using the auger bore machine with a 30-in. auger. We were in gravel and cobbles. The biggest stones we saw in there were in the neighborhood of 12-in. The pit-run soil in this part of the world is typically very hard and dense. But everything went fairly smoothly. Often, the casing will swallow a rock that’s too big for the auger, but that wasn’t the case this time. Everything that came into the casings was removed by the auger.”
Once the first casing was installed and cleaned, crews reset the auger track and began the entire process again on the next casing installation. Corsie said, “It was about one day to set the equipment up. One day to punch the pilot tubes through. Probably half day to replace the pilot tubes with the 4-in. sacrificial pipe. And ramming took six days total for one installation. The entire project took about two and half to three weeks. We did supply the 4-in. by 29-in. casing spacers to the main contractor. They installed the carrier pipes and did the grout and backfill.”