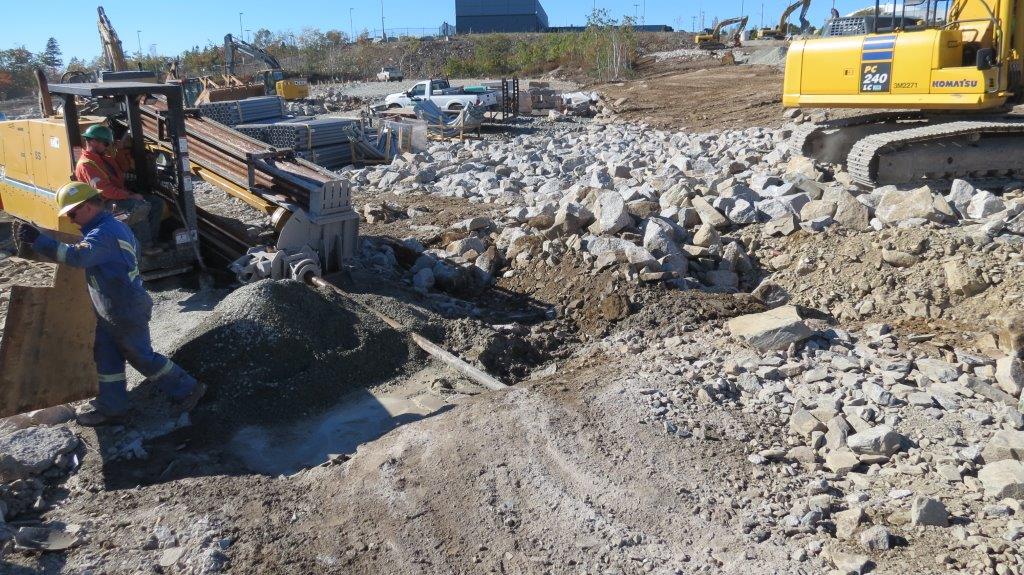
HDD Tooling Product Profile: Mincon HDD Air Hammer System
February 7, 2017
Having the appropriate tooling for the project goes a long way in determining whether the project will be successful. Drilling in rock — no matter the hardness and extreme conditions — always presents a challenge to the contractor hired to perform the job. They are never easy or routine. Many factors go into determining the best and most cost-efficient bore track and at the top of the list is having the proper tooling to get through the terrain.
Mincon Group Plc, a global manufacturer of hard rock drilling tooling, has been involved in many tough rock projects in which its equipment played a key role in the projects’ success, in particular its HDD Air Hammer system, which was introduced in 2002. The company’s current range of tooling consists of six Pilot Boring Hammer Systems, capable of drilling pilot hole sizes from 3 ½ in. to 9 ¼ in., as well as manufacturing the industry’s only patented Pull Reaming Range of Air Hammers. Utilizing this unique technology reamed hole sizes in rock of between 7 and 16 in., with before unseen production rates, are now attainable.
RELATED: Drilling in Hard Rock in Northern Virginia
The projects below focus on two different HDD bores that were completed with Mincon HDD Pilot Boring Hammer systems. In both cases, the performance of the Mincon products in extreme drilling conditions provided the correct drilling solution allowing for work to be completed in the most timely and cost-effective manner.
Mincon’s smallest pilot boring HDD Pilot Boring Hammer system, a Mincon HDD30, was designed for smaller air compressors and is used on compact class (10,000 lb and smaller) HDD machines. These machines are primarily used for short bores, spudding out small utilities, in residential or built up areas. These systems allow contractors to complete short bores that require a lot of steering in hard rock conditions, leaving a small footprint of a drill rig and compressor. In a lot of cases prior to this system, these bores could not be completed with conventional directional drilling methods.
Project No. 1
In November 2016, Mincon HDD product specialists were contacted by Eric Holby, sales manager, of Vermeer Sales & Service in Cranberry Township, Pa. Holby had a customer who was looking at some work for short bores utilizing their smaller HDD drill in hard rock conditions. After reviewing the project conditions, the size of the drill rig and the compressor that the contractor wanted to use, Mincon suggested its HDD30 Pilot Boring Air Hammer system. The contractor, Tru-Tek Drilling of Conneaut Lake, Pa., was looking for a system to complete shorter bores in hard rock to install fiber communication lines, as well as inner duct. The jobsite was located in southwestern Pennsylvania and required an 80-ft bore underneath an existing roadway. The exit location for the bore was elevated 12 ft above the entry location.
Describing the ground conditions that they were dealing with, Tru-Tek’s foreman said: “Short bores like these require excessive amounts of steering to get down under the road and then back up out of the ground. If you can’t steer the tooling back up, an exit pit is required, which entails breaking through multiple feet of solid rock with an excavator. This can be very time consuming and there is never any guarantee that you will be able to get back down to the tooling.”
The drill rig used for the bore was a Vermeer D9X13. The compressor was an Atlas Copco 400-cfm X 235-psi unit. The job required some aggressive steering and the contractor was able to achieve 4 percent per 6-ft rod, when needed. The tooling exited the ground at the required exit location, thus eliminating the need for digging an exit pit with the excavator. The bore was completed and the fiber and inner duct were installed in less than three hours.
RELATED: Tooling Provides Key to Rock Drilling in Missouri
Commenting on the job the Tru-Tek foreman stated, “We now have the ability to install these little services in a very cost-effective manner. Some of the bores we have attempted in the past would have been impossible before this tooling was available.”
Project No. 2
The second project took place in Canada and involved Mincon’s HDD60 Pilot Boring Hammer system. Designed for the 40,000- to 60,000-lb HDD drill rig class, this system is designed to be an extremely rugged high performance pilot boring tool. The Mincon HDD60 is fitted standard with a 6 ¼-in. drill bit and can safely handle up to 18,000 ft-lbs of rotational torque. The tool functions well on compressor sizes of 900 to 1,100 cfm at 350 to 500 psi.
Mincon’s partner in Canada, Vermeer Canada Inc., was asked to provide a solution to a particularly difficult on grade bore in the Halifax region of Nova Scotia. The project called for the installation of new sewer and water lines in a new subdivision in Bedford, Nova Scotia.
The contractor, Evangeline Excavators Ltd., had sought assistance from David Wood of Vermeer Canada. After discussions with Mincon HDD product specialists, it was clear that HDD hammers would be the only viable solution to complete the work. The geology at the bore site was solid granite, with a crushing strength of 30,000 psi or higher. The bore required the excavation of both an entry and exit pit down to a depth of 30 ft in order to get underneath an existing water main that had been installed approximately 50 years prior and was located 20 ft deep. The two pits took five weeks to excavate with crews working 12 hour days, six days a week.
RELATED: Time and Cost-Savings Achieved While Drilling in Hard Rock
The approach shot to the entry pit was 120 ft long down to a depth of 30 ft, exiting into the entry pit. Once drilling commenced, this bore took approximately six hours of drilling time utilizing the Mincon HDD60 Pilot Boring Hammer system on a Vermeer D50X100 drill rig. The compressor was rated at 1,100 cfm X 350 psi. Once the approach shot was completed, the drill rig was lowered into the entry pit. The bore from the entry to the exit pit was 60 feet long and was required to be maintained on grade. Drilling of this bore was completed in one and a half hours, with the tooling exiting at the required location into the exit pit.
Evangeline Excavators Ltd. and Vermeer Canada Inc. were pleased with the performance of the Mincon HDD60, allowing the work to be completed cost-effectively and in record time.
Article Provided by Mincon